Difference Between Operation And Production Management
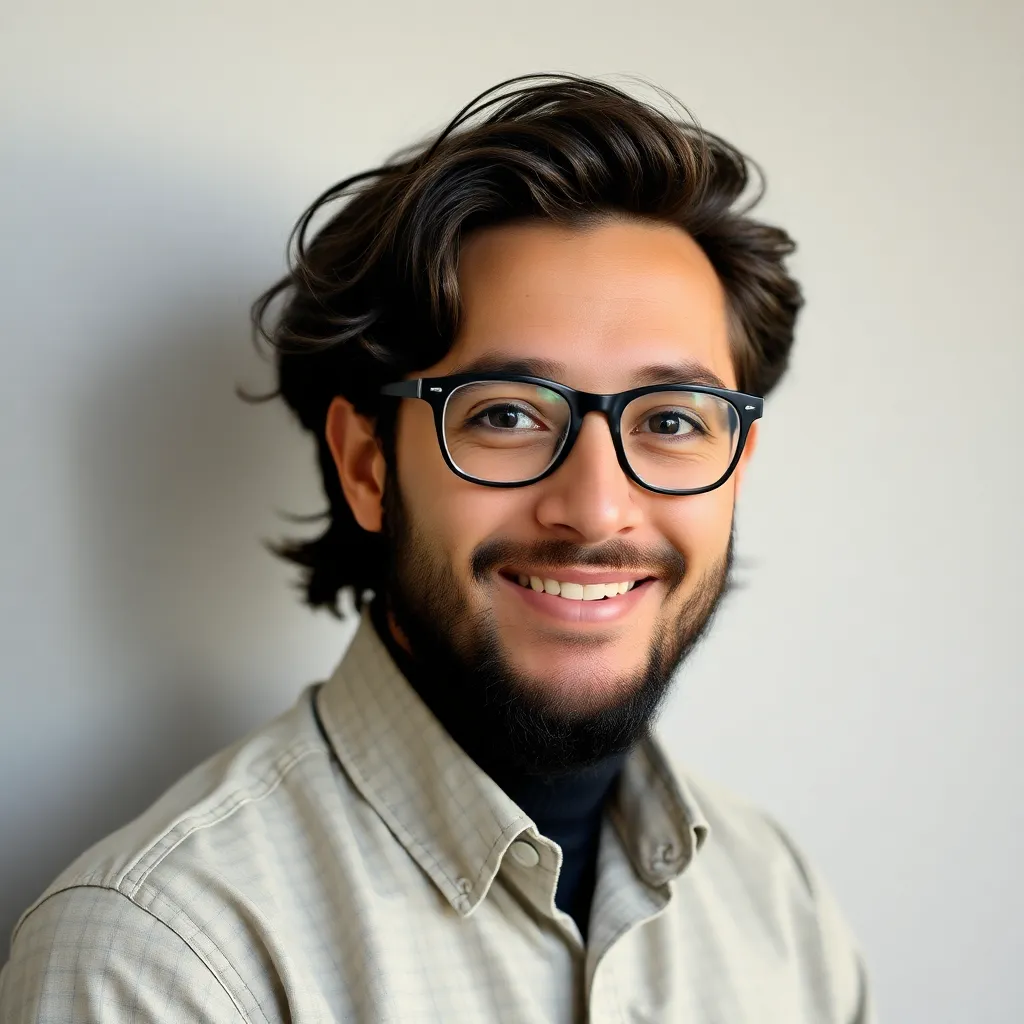
Juapaving
Apr 05, 2025 · 6 min read
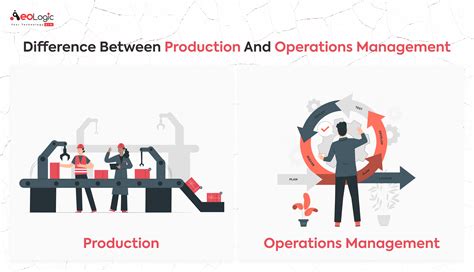
Table of Contents
Unveiling the Distinctions: Operation Management vs. Production Management
The terms "operations management" and "production management" are often used interchangeably, leading to confusion. While closely related, they represent distinct yet interconnected disciplines within the realm of business management. Understanding their nuances is crucial for effective organizational strategy and efficient resource allocation. This comprehensive guide delves into the core differences between operations management and production management, highlighting their respective roles, responsibilities, and scope within a modern business environment.
Operations Management: A Holistic Approach
Operations management (OM) encompasses the design, operation, and improvement of the entire system that creates and delivers the organization's primary products or services. It's a broad field that extends far beyond just the manufacturing floor. OM considers the entire value chain, from sourcing raw materials to delivering the final product or service to the end customer.
Key Responsibilities of Operations Management:
- Strategic Planning: OM professionals develop long-term strategies aligned with the organization's overall goals. This involves capacity planning, forecasting demand, and identifying potential risks and opportunities. This strategic layer is crucial in understanding market trends and adapting the operational structure accordingly.
- Process Design and Improvement: This is a central aspect of OM. It involves analyzing existing processes, identifying bottlenecks and inefficiencies, and implementing improvements using tools like Lean, Six Sigma, and Kaizen. This includes everything from streamlining workflows to optimizing technology utilization.
- Supply Chain Management: Effective management of the supply chain is paramount. OM professionals oversee the procurement of raw materials, inventory management, logistics, and distribution networks to ensure timely delivery and cost-effectiveness. This includes building strong relationships with suppliers and managing potential disruptions.
- Quality Control: Maintaining high quality standards is essential for customer satisfaction and brand reputation. OM professionals implement quality control systems, monitor performance metrics, and address quality issues proactively. This often involves implementing ISO standards or other industry-specific certifications.
- Technology Integration: OM leverages technology to enhance efficiency, productivity, and decision-making. This involves implementing ERP systems, automation technologies, and data analytics tools to optimize operational processes. The selection and integration of these technologies is a key part of OM's responsibility.
- Human Resource Management (within Operations): While HR typically operates independently, OM plays a role in managing the workforce involved in production and operations. This includes training, scheduling, and performance management of operational staff.
- Sustainability and Environmental Responsibility: Increasingly, organizations are incorporating sustainable practices into their operations. OM professionals play a crucial role in implementing environmentally friendly processes, reducing waste, and minimizing environmental impact.
Scope of Operations Management:
OM's scope is vast and encompasses all aspects of an organization's operations, irrespective of industry or sector. This includes:
- Manufacturing: Planning and controlling the production process, managing inventory, and ensuring quality control.
- Service Industries: Managing service delivery processes, optimizing customer service, and ensuring service quality.
- Healthcare: Optimizing patient flow, managing resources, and ensuring the quality of healthcare services.
- Government: Managing public services, infrastructure, and resource allocation.
Production Management: A Focused Approach
Production management, a subset of operations management, specifically focuses on the planning, control, and optimization of the production process. It's heavily concerned with the efficient transformation of inputs (raw materials, labor, equipment) into outputs (finished goods or services). While its scope is narrower than OM, it's crucial for manufacturing-based industries.
Key Responsibilities of Production Management:
- Production Planning and Scheduling: Developing detailed production plans, scheduling production runs, and managing production capacity to meet demand. This often involves utilizing specialized software for production scheduling and resource allocation.
- Materials Management: Managing the flow of materials from procurement to production, ensuring that sufficient raw materials are available when needed and minimizing inventory costs.
- Quality Control (within Production): Implementing quality control procedures to ensure that products meet specified standards and minimizing defects. This often involves statistical process control (SPC) techniques.
- Production Process Improvement: Continuously improving the production process to increase efficiency, reduce costs, and enhance quality. This might involve implementing lean manufacturing principles or other process improvement methodologies.
- Equipment Maintenance and Upkeep: Ensuring that production equipment is properly maintained and in good working order to minimize downtime and maximize productivity. This includes preventative maintenance schedules and efficient repair processes.
- Inventory Management (within Production): Optimizing inventory levels to minimize holding costs while ensuring that sufficient materials are available for production. This might involve implementing just-in-time (JIT) inventory systems.
- Performance Monitoring and Reporting: Tracking key performance indicators (KPIs) to monitor the efficiency and effectiveness of the production process. This data is then used to identify areas for improvement.
Scope of Production Management:
Production management's focus is primarily on the manufacturing process, encompassing:
- Production Planning: Determining what to produce, how much to produce, and when to produce it.
- Production Control: Monitoring the production process, ensuring that production is on schedule, and addressing any problems that arise.
- Production Improvement: Continuously improving the production process to increase efficiency and reduce costs.
The Interplay Between Operations and Production Management
While distinct, operations management and production management are deeply interconnected. Production management is a critical component of operations management, focusing specifically on the manufacturing or production aspects of the overall operational system. Consider this analogy: operations management is the orchestra, conducting the entire symphony, while production management is a crucial section – say, the string section – playing a vital but specific role.
Operations management provides the strategic framework, while production management implements the tactical execution within the production domain. Effective collaboration between these two areas is crucial for overall organizational success. For example, the strategic decisions made by OM regarding capacity planning will directly influence the production plans developed by production management. Similarly, the efficiency improvements implemented by production management will contribute to the overall operational effectiveness measured by OM.
Key Differences Summarized:
Feature | Operations Management | Production Management |
---|---|---|
Scope | Broad; encompasses the entire organization's operations | Narrow; focuses on the production process only |
Focus | Strategic planning, process design, supply chain | Planning, control, and optimization of production |
Output | Efficient and effective delivery of products/services | Efficient and effective production of goods/services |
Metrics | Customer satisfaction, efficiency, cost, quality | Production output, defect rates, cycle time, efficiency |
Tools & Techniques | Lean, Six Sigma, forecasting, ERP, supply chain management | JIT, SPC, MRP, production scheduling, quality control |
Conclusion: A Synergistic Relationship
Operations management and production management, while distinct, work in synergy to achieve an organization's operational goals. Understanding their differences and interdependencies is crucial for effective management. By strategically aligning these functions, organizations can optimize their processes, improve efficiency, enhance quality, and ultimately achieve a competitive advantage in today's dynamic business landscape. The future of both disciplines lies in continuous improvement, technological adaptation, and a focus on creating sustainable and resilient operational systems.
Latest Posts
Latest Posts
-
What Is The Tangent Of 30 Degrees
Apr 06, 2025
-
What Distinguishes An Element From A Compound
Apr 06, 2025
-
How Many Feet Is 27 Inches
Apr 06, 2025
-
What Are The Factors Of 117
Apr 06, 2025
-
The Energy Currency Used By Cells Is
Apr 06, 2025
Related Post
Thank you for visiting our website which covers about Difference Between Operation And Production Management . We hope the information provided has been useful to you. Feel free to contact us if you have any questions or need further assistance. See you next time and don't miss to bookmark.