How To Turn Gas Into Liquid
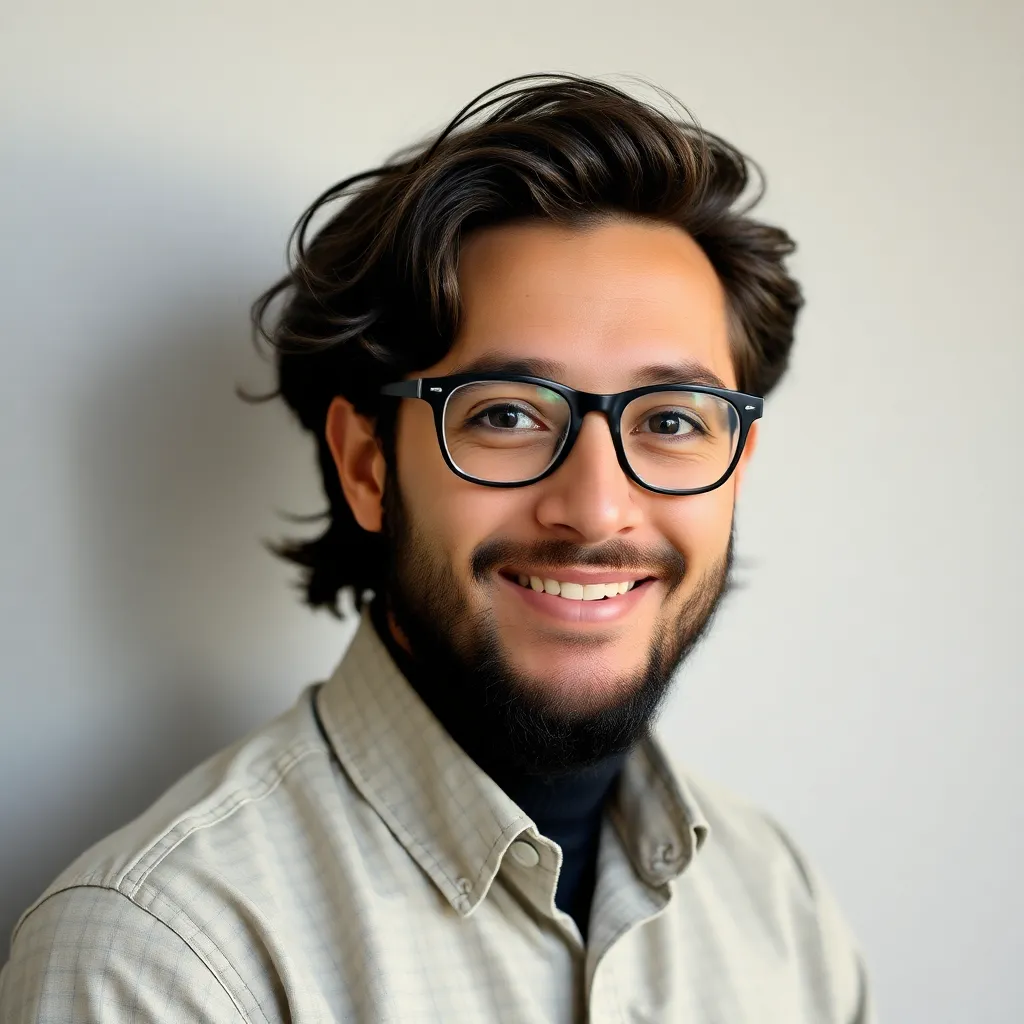
Juapaving
Apr 01, 2025 · 6 min read
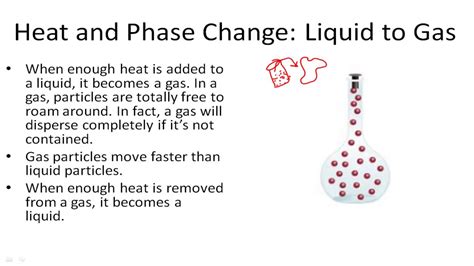
Table of Contents
How to Turn Gas into Liquid: A Comprehensive Guide to Liquefaction
Turning gas into liquid, a process known as liquefaction, is a crucial aspect of numerous industries, from the transportation of natural gas to the storage of cryogenic gases used in medical applications. This process is complex, involving significant changes in temperature and pressure, and depends heavily on the specific gas being liquefied. This comprehensive guide will delve into the intricacies of gas liquefaction, covering different methods, the underlying principles, and practical applications.
Understanding the Fundamentals: Gas Laws and Phase Transitions
Before exploring the methods of liquefaction, it's essential to understand the fundamental principles governing the phase transitions of matter. The behavior of gases is largely explained by the ideal gas law (PV = nRT), where:
- P represents pressure
- V represents volume
- n represents the number of moles of gas
- R is the ideal gas constant
- T represents temperature
This equation reveals the inverse relationship between volume and pressure at a constant temperature, and the direct relationship between volume and temperature at a constant pressure. Deviation from this ideal behavior becomes significant at high pressures and low temperatures, leading to the complexities involved in liquefying gases.
Furthermore, understanding the concept of critical point is crucial. Every gas has a critical temperature and pressure. Above the critical temperature, no amount of pressure can liquefy the gas. Therefore, cooling the gas below its critical temperature is a fundamental prerequisite for liquefaction.
Methods of Gas Liquefaction
Several methods exist for turning gas into liquid, each tailored to specific gases and industrial requirements. These primarily involve reducing the temperature and/or increasing the pressure of the gas.
1. Simple Compression and Cooling
This is the most straightforward method, suitable for gases with relatively high critical temperatures, such as propane or butane. The process involves:
- Compression: The gas is compressed using a compressor, increasing its pressure significantly. This compression process also increases the temperature of the gas.
- Cooling: The compressed, hot gas is then cooled using a heat exchanger or other cooling methods. This lowers the temperature to a point where, at the increased pressure, the gas begins to condense into liquid form.
- Further Cooling and Storage: The partially liquefied gas is further cooled to ensure complete liquefaction and stored in a pressure vessel.
This method is relatively simple but less efficient for gases with low critical temperatures, requiring significant energy for cooling.
2. Cascade Liquefaction
This method utilizes a series of interconnected refrigeration cycles, each cooling the gas closer to its liquefaction point. It's particularly effective for liquefying gases with lower critical temperatures. The process typically involves:
- Multiple Refrigeration Stages: Different refrigerants are used in different stages, each operating at a lower temperature than the previous stage. This stepwise cooling significantly reduces the energy required for liquefaction.
- Sequential Cooling: The gas is progressively cooled as it passes through the various refrigeration stages, eventually reaching its liquefaction point.
- Efficiency Advantages: Cascade liquefaction offers significantly higher efficiency than simple compression and cooling, especially for gases requiring extremely low temperatures.
3. Claude Liquefaction Process
This method employs the Joule-Thomson effect, also known as the Joule-Kelvin effect. This effect describes the change in temperature of a real gas or liquid when it is forced through a valve or porous plug while kept insulated from its surroundings. The Claude process involves:
- Initial Cooling: The gas is initially cooled using a pre-cooling stage, often employing other methods like compression and cooling.
- Joule-Thomson Expansion: The cooled, compressed gas is then expanded through a Joule-Thomson valve. This expansion causes the gas to cool further, due to the internal energy decrease during expansion.
- Recirculation: A portion of the liquefied gas is recycled to pre-cool incoming gas, enhancing the efficiency of the process.
- Liquefaction and Separation: The cooled gas then undergoes further cooling and separation, leading to the extraction of liquefied gas.
The Claude process is highly efficient for gases with low critical temperatures.
4. Linde-Hampson Liquefaction Process
Similar to the Claude process, the Linde-Hampson process also utilizes the Joule-Thomson effect but without the pre-cooling stage used in Claude.
- High-Pressure Compression: Gas is initially compressed to a high pressure.
- Joule-Thomson Expansion: The compressed gas then undergoes expansion through a Joule-Thomson valve, leading to cooling.
- Heat Exchange: The cooled gas is used to pre-cool the incoming compressed gas, increasing efficiency.
- Liquefaction: This iterative cooling process eventually leads to liquefaction.
While simpler than the Claude process, it is less efficient for gases requiring very low temperatures.
5. Helium Liquefaction
Liquefying helium poses unique challenges due to its extremely low critical temperature (5.2 K). Specialized techniques are needed, often involving several stages of pre-cooling and expansion using other refrigerants before employing the Joule-Thomson effect or other cryogenic processes.
Practical Applications of Gas Liquefaction
The liquefaction of gases finds widespread applications across various sectors:
1. Natural Gas Transportation
Liquefied natural gas (LNG) is essential for the efficient transportation of natural gas over long distances. The liquefaction process significantly reduces the volume of gas, making transportation more cost-effective.
2. Cryogenic Applications
Many gases are liquefied for use in cryogenic applications, such as in medical equipment (e.g., MRI machines), scientific research, and industrial processes. Liquid nitrogen, liquid helium, and liquid oxygen are common examples.
3. Chemical Industry
Liquefied gases are widely used as raw materials and intermediates in various chemical processes. The storage and handling of these gases in liquid form are often safer and more efficient.
4. Food Industry
Liquid nitrogen is used in the food industry for quick freezing of food products, preserving their quality and texture.
5. Aerospace Industry
Liquid oxygen and liquid hydrogen are critical for rocket propulsion systems, powering space launches and other aerospace applications.
Challenges and Considerations in Gas Liquefaction
While gas liquefaction is a crucial industrial process, it presents several challenges:
- Energy Consumption: The process is energy-intensive, especially for gases with low critical temperatures. Optimizing energy efficiency is a continuous area of research and development.
- Safety Hazards: Working with high-pressure gases and cryogenic liquids requires stringent safety protocols to prevent accidents.
- Equipment Costs: The specialized equipment required for gas liquefaction can be expensive, representing a significant capital investment.
- Environmental Impact: The energy consumption of liquefaction can contribute to greenhouse gas emissions. Developing more sustainable liquefaction technologies is crucial.
Future Trends in Gas Liquefaction
The field of gas liquefaction is constantly evolving, with ongoing research focusing on:
- Improved Efficiency: Developing more efficient liquefaction techniques to reduce energy consumption and operational costs.
- Sustainable Technologies: Exploring environmentally friendly methods to minimize the environmental footprint of the process.
- Miniaturization: Developing compact and portable liquefaction systems for various applications.
- New Materials: Utilizing advanced materials to improve the performance and durability of liquefaction equipment.
In conclusion, turning gas into liquid is a complex yet indispensable process with far-reaching applications. Understanding the underlying principles, various methods, and associated challenges is crucial for those involved in this field. The continuous advancements in liquefaction technology will undoubtedly lead to even more efficient and sustainable solutions in the future, further expanding its applications across diverse industries.
Latest Posts
Latest Posts
-
Flip A Coin Roll A Die
Apr 02, 2025
-
Calculating Ka From A Titration Curve
Apr 02, 2025
-
5 Letter Words Starting With T H I
Apr 02, 2025
-
If 2 Matrix Multiplication Is 0
Apr 02, 2025
-
Find The Square Root Of 121
Apr 02, 2025
Related Post
Thank you for visiting our website which covers about How To Turn Gas Into Liquid . We hope the information provided has been useful to you. Feel free to contact us if you have any questions or need further assistance. See you next time and don't miss to bookmark.