Explain The Process Of Making Yarn From Fibre Answer
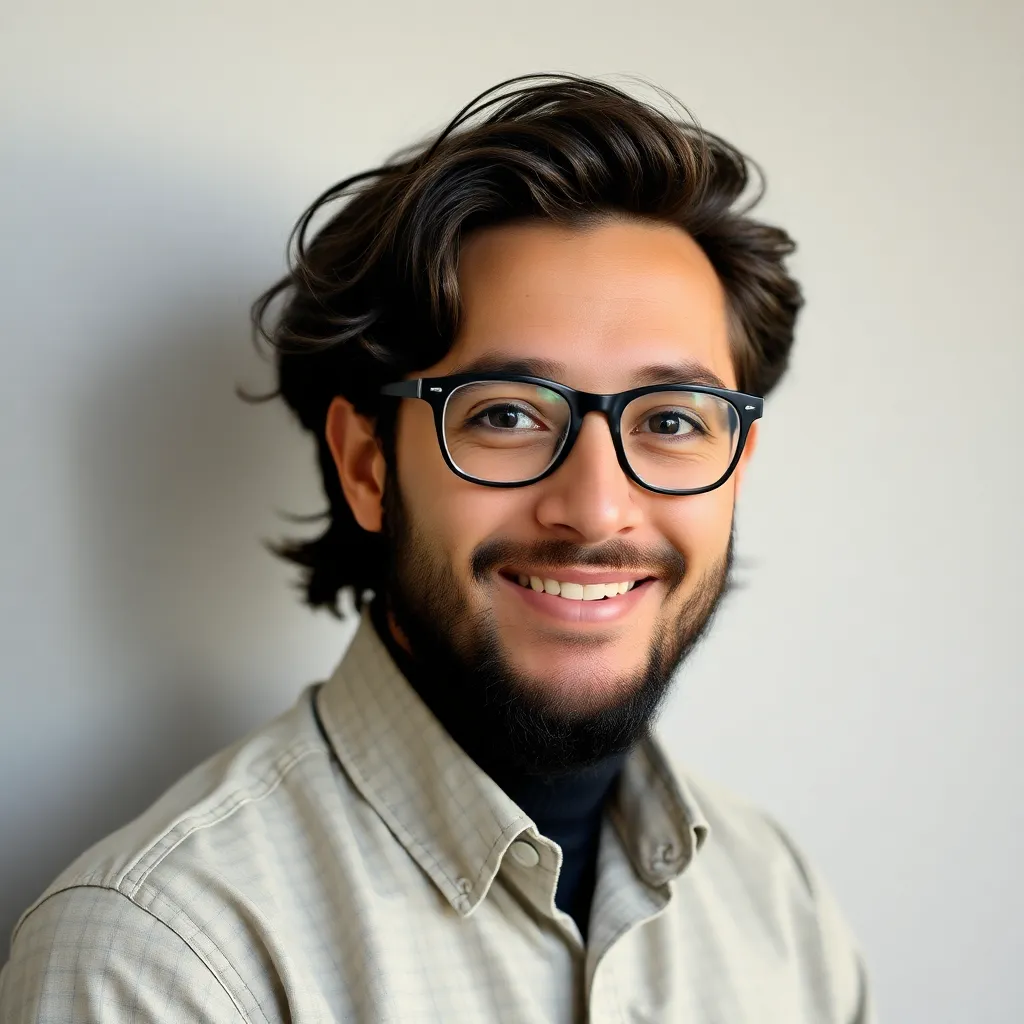
Juapaving
Apr 03, 2025 · 5 min read
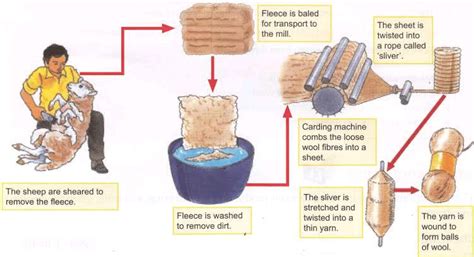
Table of Contents
From Fiber to Yarn: A Comprehensive Guide to Yarn Making
Yarn, the fundamental building block of countless textiles, isn't simply a fluffy thread. It's the result of a fascinating process that transforms raw fibers into a usable material for knitting, crocheting, weaving, and more. Understanding this process, from the initial fiber source to the final yarn, provides a deeper appreciation for the craftsmanship and technology behind the textiles we use daily. This comprehensive guide will explore the journey of fiber to yarn, detailing each step with precision and clarity.
Types of Fibers: The Starting Point
Before we delve into the yarn-making process, it's crucial to understand the diverse origins of fibers. Fibers are broadly classified into two categories:
1. Natural Fibers: Gifts from Nature
Natural fibers, sourced directly from plants and animals, boast unique properties and textures. Some of the most common include:
-
Cotton: A plant-based fiber, known for its softness, breathability, and absorbency. Its versatility makes it a staple in clothing and home textiles.
-
Wool: Derived from sheep (and other animals like alpacas, llamas, and goats), wool is renowned for its warmth, resilience, and moisture-wicking capabilities. Different breeds of sheep yield wool with varying characteristics.
-
Silk: Produced by silkworms, silk is a luxurious fiber celebrated for its lustrous sheen, smoothness, and drape. It's a delicate yet strong fiber, often used in high-end apparel.
-
Linen: Extracted from the flax plant, linen is a durable, strong fiber valued for its coolness, drape, and resistance to wrinkles. It’s often used in clothing and home furnishings.
-
Hemp: A strong, sustainable fiber derived from the hemp plant. Its durability and environmental friendliness make it increasingly popular.
2. Synthetic Fibers: Human Innovation
Synthetic fibers, crafted from chemical processes, offer a wide array of properties that can be tailored to specific needs. Examples include:
-
Polyester: A durable, wrinkle-resistant fiber that's widely used in clothing, upholstery, and other applications.
-
Nylon: Known for its strength and elasticity, nylon is used in hosiery, carpets, and other products requiring resilience.
-
Acrylic: A versatile fiber that mimics the feel of wool but is more affordable and easier to care for. It’s often used in sweaters and blankets.
-
Rayon: A semi-synthetic fiber made from cellulose, often blended with other fibers to enhance softness or drape.
The Yarn-Making Process: A Step-by-Step Guide
The transformation of raw fibers into yarn involves several key steps, varying slightly depending on the fiber type and desired yarn characteristics. However, the fundamental stages remain consistent:
1. Fiber Preparation: Cleaning and Sorting
This initial stage is vital for ensuring the quality of the final yarn. It involves:
-
Cleaning: Removing impurities like dirt, seeds, and plant matter from natural fibers. This can involve processes like scouring (washing with detergents) or degumming (removing sericin from silk). Synthetic fibers often require less cleaning.
-
Sorting: Separating fibers by length, color, and quality. This step is crucial for creating even and consistent yarn. Shorter fibers are often used for specific yarn types.
-
Carding: This process aligns fibers, removing short fibers and further improving evenness. For wool and other shorter-staple fibers, carding is crucial. It uses specialized machines with rotating wire brushes to untangle and align the fibers.
2. Spinning: The Heart of Yarn Making
Spinning is the core process where individual fibers are twisted together to form a continuous thread. This process can be achieved through various methods:
-
Hand Spinning: A traditional method involving a spindle or spinning wheel. This allows for greater control over the yarn's twist and texture, producing unique and often handcrafted yarns.
-
Machine Spinning: Modern yarn production relies heavily on automated spinning machines. These machines efficiently process large quantities of fibers, creating consistent yarns at scale. Different spinning techniques (e.g., ring spinning, open-end spinning) result in distinct yarn structures.
-
Ring Spinning: This widely used technique uses a rotating spindle and traveler to twist the fibers, creating a strong and even yarn.
-
Open-end Spinning: A faster and more efficient method that avoids the use of a traveler, producing a slightly hairier yarn compared to ring-spun yarn.
3. Winding and Coning: Preparing for Weaving or Knitting
Once the yarn is spun, it needs further processing before it's ready for use:
-
Winding: The spun yarn is wound onto bobbins or spools for easier handling and storage.
-
Coning: Large packages of yarn are created by winding the yarn from bobbins onto cones, a format suitable for knitting and weaving machines.
4. Yarn Treatment: Enhancing Properties
Depending on the desired final product, yarns may undergo additional treatments:
-
Dyeing: Adding color to the yarn, using various dyeing techniques like solution dyeing (dyeing the fibers before spinning), yarn dyeing (dyeing the spun yarn), or piece dyeing (dyeing the finished fabric).
-
Finishing: This includes processes like softening, setting the twist, and applying finishes to enhance the yarn's texture, drape, or resistance to shrinkage or wrinkles.
Yarn Types and Their Characteristics
The final characteristics of the yarn depend on several factors:
-
Fiber Type: Different fibers contribute unique properties—strength, softness, drape, and more.
-
Spinning Method: The spinning technique significantly influences the yarn's structure, strength, and evenness.
-
Twist: The amount of twist affects the yarn's strength, texture, and elasticity. A higher twist typically results in a stronger, less hairy yarn.
-
Ply: The number of strands twisted together. Single-ply yarns are made from a single strand, while multi-ply yarns are created by twisting two or more strands together. Multi-ply yarns are generally stronger and more durable.
Common Yarn Types
-
Woolen Yarn: Made from carded wool fibers, creating a soft, fuzzy yarn.
-
Worsted Yarn: Made from combed wool fibers, resulting in a smoother, more even yarn.
-
Cotton Yarn: Soft, breathable, and widely used in various applications.
-
Linen Yarn: Durable, strong, with a characteristic slightly rough texture.
Conclusion: The Journey of a Thread
The path from fiber to yarn is a journey of transformation, blending natural resources or human innovation with sophisticated techniques. Understanding this process reveals the meticulous work and advanced technology behind the humble thread that forms the basis of so many textiles. Whether appreciating the handcrafted beauty of hand-spun yarn or marveling at the efficiency of modern machine spinning, we gain a deeper appreciation for the rich history and ongoing innovation in the world of yarn production. This knowledge allows consumers to make informed choices about the yarns they use, valuing the craftsmanship and considering the sustainability of the fibers and production methods.
Latest Posts
Latest Posts
-
How Many Liters Has In Half Gallon
Apr 03, 2025
-
What Is 20 Percent Of 150
Apr 03, 2025
-
Electrical Current Will Pass Easily Through
Apr 03, 2025
-
Which Of The Following Are Rational Numbers
Apr 03, 2025
-
Five Letter Words With Ie In Them
Apr 03, 2025
Related Post
Thank you for visiting our website which covers about Explain The Process Of Making Yarn From Fibre Answer . We hope the information provided has been useful to you. Feel free to contact us if you have any questions or need further assistance. See you next time and don't miss to bookmark.