Difference Between Ac And Dc Electric Motors
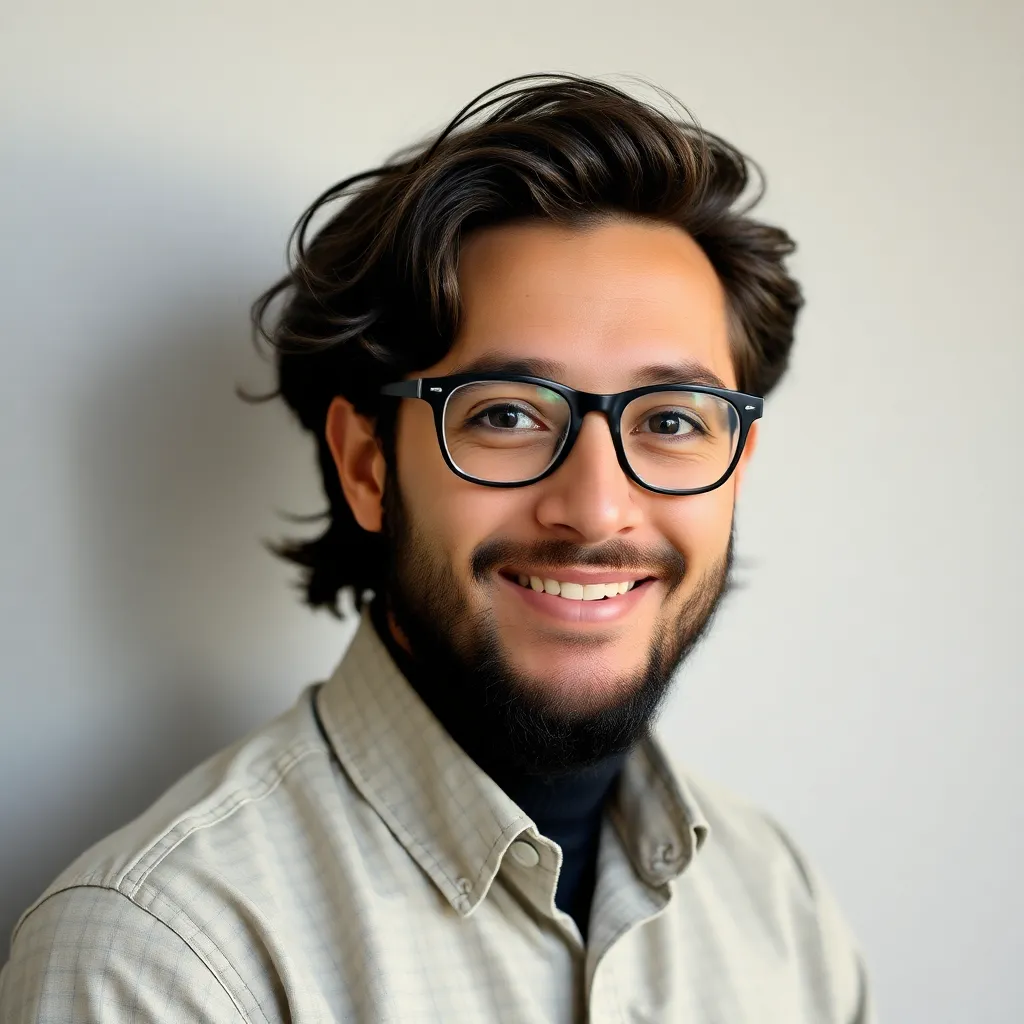
Juapaving
Mar 19, 2025 · 6 min read
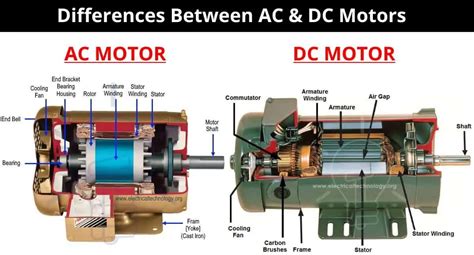
Table of Contents
AC vs. DC Electric Motors: A Comprehensive Comparison
Choosing the right electric motor for your application hinges on a deep understanding of its capabilities and limitations. While both AC and DC motors convert electrical energy into mechanical energy, their underlying principles, construction, and performance characteristics differ significantly. This comprehensive guide delves into the core distinctions between AC and DC electric motors, helping you make informed decisions based on your specific needs.
Fundamental Differences: AC vs. DC
The most basic difference lies in the nature of the electrical current they utilize:
-
AC (Alternating Current) Motors: These motors operate on alternating current, where the direction of current flow reverses periodically. This cyclical change in current direction is a defining feature of AC power systems found in most homes and industries.
-
DC (Direct Current) Motors: These motors run on direct current, where the current flows consistently in one direction. DC power is commonly used in battery-powered devices and specialized industrial applications.
This fundamental difference dictates many of the subsequent variations in their design, performance, and applications.
Types of AC Motors
The world of AC motors is diverse, encompassing several distinct types, each with its own strengths and weaknesses:
1. Induction Motors: The Workhorses of Industry
Induction motors, also known as asynchronous motors, are the most prevalent type of AC motor. Their popularity stems from their robust construction, relatively low cost, and ease of maintenance. They operate on the principle of electromagnetic induction:
-
Principle of Operation: A rotating magnetic field in the stator (stationary part) induces currents in the rotor (rotating part), creating a magnetic field that interacts with the stator's field, resulting in rotation.
-
Types: Induction motors are further classified into squirrel-cage and wound-rotor types, each differing in their rotor construction and starting characteristics. Squirrel-cage motors are simpler and more common, while wound-rotor motors offer better starting torque and speed control.
-
Advantages: High efficiency, robust construction, low maintenance, and relatively low cost.
-
Disadvantages: Lower starting torque compared to some DC motors, and speed control can be more complex.
2. Synchronous Motors: Precision and Control
Synchronous motors operate at a constant speed synchronized with the frequency of the AC power supply. This characteristic makes them ideal for applications requiring precise speed control:
-
Principle of Operation: These motors use a permanent magnet or electromagnet in the rotor that locks in sync with the rotating magnetic field of the stator.
-
Advantages: Constant speed operation, high efficiency at rated load, and good power factor.
-
Disadvantages: More complex and expensive than induction motors, and typically require a separate starting mechanism.
3. Single-Phase AC Motors: For Smaller Applications
Single-phase AC motors are smaller and simpler than their three-phase counterparts, frequently found in household appliances:
-
Principle of Operation: They utilize a single-phase AC power supply and often require a starting mechanism (capacitor-start, split-phase) to initiate rotation.
-
Advantages: Compact size, low cost, suitable for smaller applications.
-
Disadvantages: Lower efficiency and power output compared to three-phase motors.
Types of DC Motors
DC motors also come in various forms, each tailored to specific operational needs:
1. Brushed DC Motors: Simple and Widely Used
Brushed DC motors are the most basic type, featuring brushes that make electrical contact with the commutator to switch the current direction in the rotor:
-
Principle of Operation: The interaction between the magnetic fields of the stator and rotor causes rotation. The commutator ensures that the current in the rotor windings reverses at the appropriate time to maintain continuous rotation.
-
Advantages: Simple construction, low cost, ease of speed control through voltage adjustment.
-
Disadvantages: Limited lifespan due to brush wear, mechanical noise, and sparks from the brushes.
2. Brushless DC Motors (BLDC): High Efficiency and Durability
Brushless DC motors eliminate the brushes and commutator, leading to longer lifespan, higher efficiency, and quieter operation:
-
Principle of Operation: Electronic commutation replaces the mechanical commutation of brushed DC motors. Sensors or electronic control circuits determine the rotor position and switch the current in the stator windings accordingly.
-
Advantages: Longer lifespan, higher efficiency, lower noise, higher torque-to-size ratio.
-
Disadvantages: More complex electronic control circuitry is required, generally higher cost.
3. Servo Motors: Precision Position Control
Servo motors are specialized DC motors designed for precise position control, commonly used in robotics and automation:
-
Principle of Operation: They incorporate a feedback mechanism (encoder or potentiometer) that monitors the rotor position and allows for precise control of its angle and speed.
-
Advantages: High accuracy, precise position control, fast response times.
-
Disadvantages: Higher cost and complexity compared to standard DC motors.
Key Performance Characteristics: A Comparative Analysis
Comparing AC and DC motors requires analyzing several key performance parameters:
1. Speed Control:
-
AC Motors: Speed control in AC motors can be more challenging, often requiring specialized methods like variable frequency drives (VFDs) or wound-rotor motor designs.
-
DC Motors: DC motors generally offer easier speed control through voltage adjustment, making them well-suited for applications demanding variable speed operation.
2. Starting Torque:
-
AC Motors: Induction motors typically have lower starting torque compared to DC motors, particularly at higher loads.
-
DC Motors: DC motors, especially those with high starting torque capabilities, are preferred for applications requiring high initial torque, such as conveyor belts or hoists.
3. Efficiency:
-
AC Motors: Modern AC motors, especially high-efficiency induction motors, offer comparable or even superior efficiency to DC motors in many applications.
-
DC Motors: Brushless DC motors boast high efficiency, often exceeding that of brushed DC motors and some AC motors.
4. Maintenance:
-
AC Motors: Induction motors generally require less maintenance than DC motors due to their simple construction and lack of brushes.
-
DC Motors: Brushed DC motors require periodic brush replacement, whereas brushless DC motors require less maintenance.
5. Cost:
-
AC Motors: AC motors, especially induction motors, tend to have lower initial costs than comparable DC motors.
-
DC Motors: Brushless DC motors, due to their electronic control circuitry, generally command higher prices than brushed DC motors or standard AC motors.
Application Considerations: Choosing the Right Motor
The optimal choice between AC and DC motors depends heavily on the specific application requirements:
-
High-volume industrial applications requiring robust, low-maintenance operation: Induction motors are typically the preferred choice. Their simple design, high efficiency, and reliability make them suitable for demanding environments.
-
Applications needing precise speed control and high starting torque: DC motors, particularly brushless DC motors, are often ideal. Their ease of speed control and higher torque capabilities make them suitable for demanding applications.
-
Household appliances and smaller devices: Single-phase AC motors are commonly used due to their compact size and low cost.
-
Robotics and automation systems demanding precise position control: Servo motors offer the high accuracy and fast response times necessary for such tasks.
-
Applications needing constant speed operation: Synchronous motors are preferred for their constant speed characteristics.
Conclusion: Navigating the AC vs. DC Motor Landscape
The decision between AC and DC motors involves careful consideration of numerous factors. Understanding the fundamental differences in their operating principles, characteristics, and advantages and disadvantages is crucial for making informed decisions. This in-depth comparison empowers you to select the motor that best aligns with your specific application's requirements, ensuring optimal performance, efficiency, and longevity. Remember to consult motor specifications and datasheets to make an informed decision for your specific project.
Latest Posts
Latest Posts
-
How Does Nadp Turn Into Nadph
Mar 19, 2025
-
As You Move Down A Group Atomic Radius Increases Because
Mar 19, 2025
-
Determine Whether Each Characteristic Is Exhibited By Plants Or Fungi
Mar 19, 2025
-
The Temperature At Which A Liquid Changes To A Gas
Mar 19, 2025
-
A Rectangle Has How Many Sides
Mar 19, 2025
Related Post
Thank you for visiting our website which covers about Difference Between Ac And Dc Electric Motors . We hope the information provided has been useful to you. Feel free to contact us if you have any questions or need further assistance. See you next time and don't miss to bookmark.