Why Can't Aluminum Be Reduced With Carbon
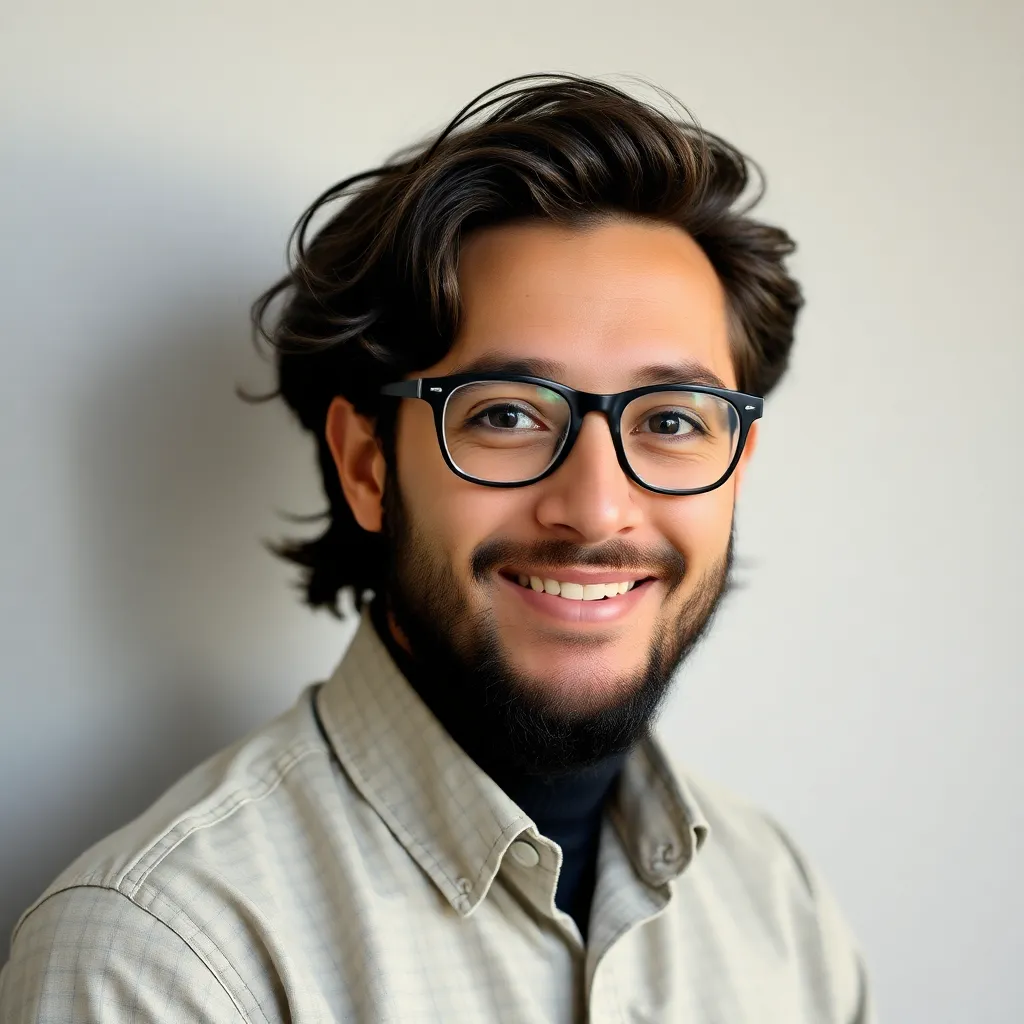
Juapaving
Mar 04, 2025 · 5 min read
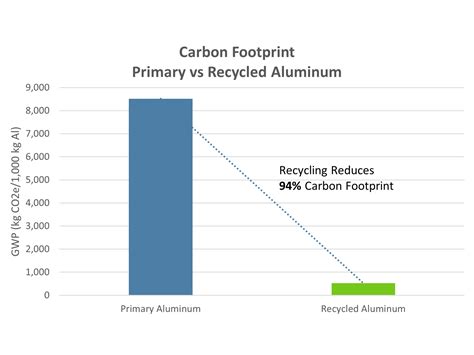
Table of Contents
Why Can't Aluminum Be Reduced with Carbon? A Deep Dive into Alumina Reduction
Aluminum is a ubiquitous metal, vital to modern life. Its lightweight yet strong nature makes it ideal for countless applications, from aircraft construction to beverage cans. But the journey from bauxite ore to the shiny aluminum we use daily is surprisingly complex, and hinges on a key chemical challenge: why can't aluminum be reduced with carbon? This seemingly simple question unlocks a fascinating exploration of thermodynamics, kinetics, and the industrial processes that shape our world.
The Thermodynamics of Aluminum Reduction
The heart of the matter lies in the Gibbs Free Energy (ΔG) of a chemical reaction. ΔG essentially tells us whether a reaction is spontaneous (favorable) or not at a given temperature and pressure. A negative ΔG indicates a spontaneous reaction, while a positive ΔG means the reaction won't proceed without external energy input.
To understand why carbon reduction fails for aluminum, let's examine the relevant reactions. Aluminum oxide (Al₂O₃), the primary source of aluminum, needs to be reduced to metallic aluminum (Al). Theoretically, carbon could act as the reducing agent, with carbon monoxide (CO) or carbon dioxide (CO₂) as byproducts:
- 2Al₂O₃ + 3C → 4Al + 3CO₂
- 2Al₂O₃ + 3C → 4Al + 3CO
These reactions seem straightforward, but the crucial element is the Gibbs Free Energy change for these reactions at various temperatures. While the reactions are thermodynamically favorable at extremely high temperatures (above 2000°C), the practicality of achieving and maintaining such temperatures in a cost-effective manner is prohibitive.
Comparing Aluminum and Carbon's Affinity for Oxygen
The core reason for the difficulty lies in the relative electronegativity of aluminum and carbon. Oxygen has a much stronger affinity for aluminum than for carbon. This means that aluminum-oxygen bonds are significantly stronger than carbon-oxygen bonds. Consequently, the energy required to break the aluminum-oxygen bonds and form carbon-oxygen bonds is exceptionally high, requiring temperatures far beyond practical industrial application. Essentially, carbon simply isn't a strong enough reducing agent to overcome the stability of aluminum oxide at industrially feasible temperatures.
The Kinetics of Aluminum Reduction: Reaction Rate Challenges
Even if the thermodynamics were slightly more favorable, the kinetics of the reaction present significant hurdles. The reaction between aluminum oxide and carbon is incredibly slow at temperatures below 2000°C. This slow reaction rate is primarily due to the formation of a protective layer on the alumina particles. This layer, often composed of aluminum carbide (Al₄C₃) or other intermediate compounds, hinders further reaction by preventing direct contact between the carbon and aluminum oxide. This passive layer effectively insulates the aluminum oxide, making it difficult for carbon to reach and react with the unreacted alumina.
The Role of High Temperatures and Reaction Intermediates
At extremely high temperatures, the reaction rate increases, but this brings its own set of challenges. Maintaining and controlling such high temperatures is expensive and energy-intensive, making it commercially unsustainable. Furthermore, the formation of reaction intermediates, like aluminum carbide, complicates the process and can lead to undesirable byproducts that reduce the yield of pure aluminum.
The Hall-Héroult Process: The Industrial Solution
The industrial production of aluminum relies on the Hall-Héroult process, a method that cleverly circumvents the thermodynamic and kinetic limitations of direct carbon reduction. Instead of using carbon directly to reduce alumina, the Hall-Héroult process employs electrolysis.
Electrolysis: A Powerful Alternative
Electrolysis involves using an electric current to drive a non-spontaneous chemical reaction. In the Hall-Héroult process, molten cryolite (Na₃AlF₆) acts as a solvent for alumina, significantly lowering its melting point and enhancing its ionic conductivity. When a direct current is passed through this molten electrolyte, aluminum ions (Al³⁺) are reduced at the cathode (negative electrode), forming molten aluminum. Simultaneously, oxygen ions (O²⁻) are oxidized at the anode (positive electrode), producing carbon dioxide (CO₂) or carbon monoxide (CO) depending on the anode material used.
Advantages of Electrolysis over Direct Carbon Reduction
The electrolysis approach offers several significant advantages over direct carbon reduction:
- Lower Operating Temperatures: The Hall-Héroult process operates at around 950-980°C, a substantially lower temperature compared to the extremely high temperatures required for direct carbon reduction.
- Higher Efficiency: Electrolysis provides a more efficient way to reduce aluminum oxide, resulting in better yields and reduced energy consumption (relatively speaking).
- Controllability: The process offers greater control over the reaction parameters, improving product quality and minimizing the formation of undesirable byproducts.
- Feasibility: The Hall-Héroult process has been industrialized, providing a cost-effective and scalable method for aluminum production.
Other Potential Reducing Agents
While carbon is unsuitable for direct aluminum reduction, research continues to explore alternative reducing agents. These investigations aim to find more efficient and environmentally friendly methods for aluminum production. However, these methods still face their own significant challenges in terms of thermodynamics, kinetics, or cost-effectiveness.
Exploring Alternative Routes: Challenges and Opportunities
Researchers are exploring several alternative routes, including:
- Electrolysis with alternative electrolytes: Investigations are underway to find electrolytes that could lower the energy requirements of the Hall-Héroult process, or potentially enable aluminum production at even lower temperatures.
- Direct reduction using other reducing agents: Researchers are exploring alternative reducing agents such as silicon, magnesium, or calcium. However, the thermodynamic and kinetic challenges remain substantial.
- Plasma-based reduction: Plasma technology offers the potential to achieve extremely high temperatures, which might make direct carbon reduction more feasible. However, the energy requirements and scalability issues need further investigation.
Conclusion: The Ongoing Search for Efficient Aluminum Production
The question of why aluminum can't be reduced with carbon is not a simple one. It delves into the intricate interplay between thermodynamics, kinetics, and the practical considerations of industrial-scale production. The Hall-Héroult process remains the dominant industrial method, successfully navigating the challenges inherent in aluminum oxide reduction. However, continuous research and development strive to improve efficiency and explore alternative approaches, ultimately driving efforts toward more sustainable and cost-effective aluminum production in the future. The inherent thermodynamic limitations imposed by the strong aluminum-oxygen bond and the kinetic difficulties presented by passive layers remain significant obstacles to overcome. But the relentless pursuit of innovation in materials science and chemical engineering continues to push the boundaries of what's possible.
Latest Posts
Latest Posts
-
The Structural And Functional Units Of All Living Organisms
Mar 04, 2025
-
What Are The Common Factors Of 4 And 6
Mar 04, 2025
-
What Kingdom Is A Human In
Mar 04, 2025
-
Lowest Common Multiple Of 3 4 5
Mar 04, 2025
-
Natural Boundry Between France And Italy
Mar 04, 2025
Related Post
Thank you for visiting our website which covers about Why Can't Aluminum Be Reduced With Carbon . We hope the information provided has been useful to you. Feel free to contact us if you have any questions or need further assistance. See you next time and don't miss to bookmark.