Which Of The Following Would Tend To Reduce Effective Capacity
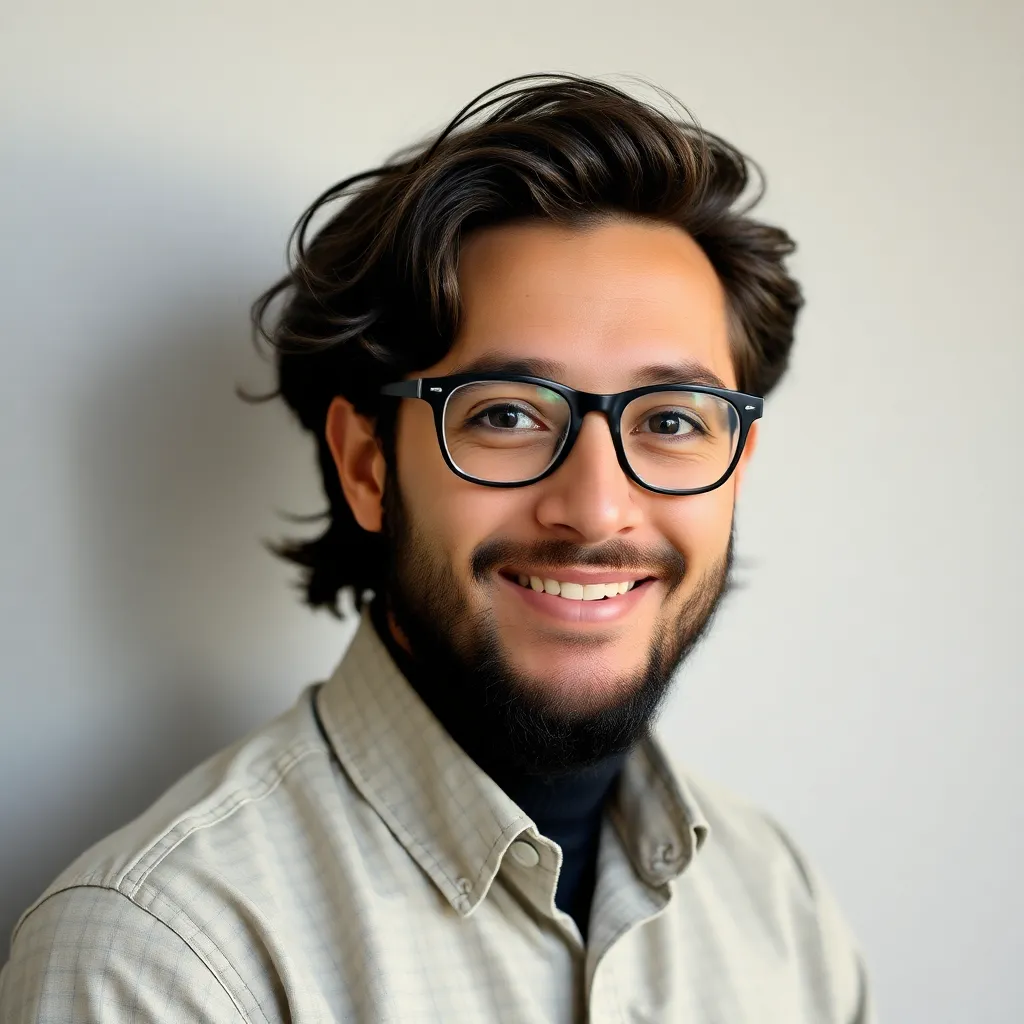
Juapaving
May 25, 2025 · 5 min read
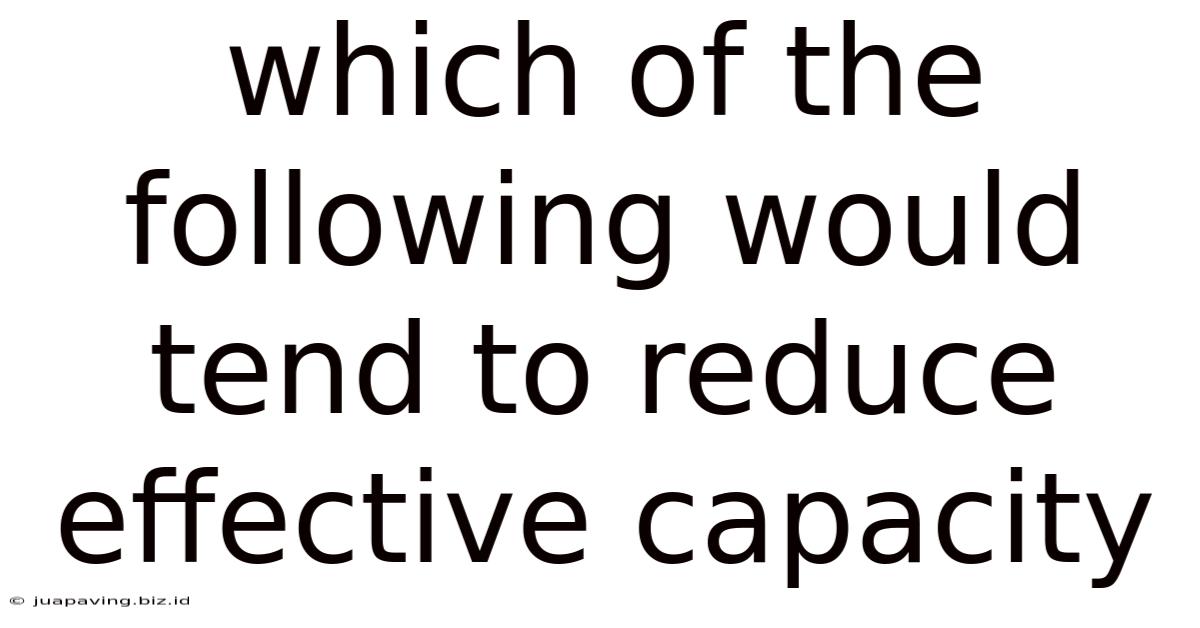
Table of Contents
Which of the following would tend to reduce effective capacity?
Effective capacity, the actual output a system can achieve given its design and operational realities, is often less than its theoretical maximum. Many factors can contribute to this reduction. Understanding these factors is crucial for businesses striving for optimal efficiency and profitability. This article delves into various elements that significantly impact effective capacity, exploring their causes and suggesting mitigation strategies.
Key Factors Reducing Effective Capacity
Several factors conspire to reduce effective capacity. These can be broadly categorized into:
1. Equipment and Technology Limitations
-
Equipment Breakdowns and Malfunctions: Unexpected equipment failures are a major culprit. This downtime translates directly into lost production, reducing effective capacity. Preventive maintenance, thorough quality control during procurement, and redundancy in critical equipment can mitigate this.
-
Inadequate Equipment: Using equipment that's underpowered, outdated, or simply unsuitable for the task at hand will inherently limit output. Investing in modern, efficient equipment and ensuring it's correctly sized for the workload are crucial.
-
Technological Bottlenecks: In complex systems, a single slow or inefficient piece of technology can create a bottleneck, holding back the entire process. Identifying and addressing these bottlenecks through process optimization, technology upgrades, or parallel processing is essential.
-
Software Glitches and System Errors: Software malfunctions, data entry errors, or system failures can cripple production. Robust software development practices, regular updates and patching, and data validation procedures are crucial.
2. Process Inefficiencies
-
Poor Workflow Design: Inefficient workflows, characterized by unnecessary steps, excessive handoffs, or lack of clear responsibilities, significantly reduce capacity. Lean manufacturing principles, process mapping, and value stream analysis can help identify and eliminate waste.
-
Lack of Standardization: Inconsistent processes lead to variability and errors, lowering predictability and output. Establishing standard operating procedures (SOPs) and ensuring consistent adherence can improve efficiency.
-
Inadequate Training: Untrained or poorly trained employees may not operate equipment efficiently or follow procedures correctly, leading to reduced output and increased errors. Investing in comprehensive training programs and providing ongoing support is vital.
-
Suboptimal Scheduling: Poorly planned schedules, including insufficient buffer time, can lead to delays and reduced throughput. Implementing effective scheduling techniques such as Kanban or MRP (Materials Requirements Planning) can improve capacity utilization.
3. Human Factors
-
Absenteeism and Turnover: Employee absence due to illness, vacation, or turnover leads to lost productivity. Implementing employee retention strategies, offering competitive benefits, and creating a positive work environment are crucial.
-
Employee Skill Gaps: A lack of skills or expertise in specific areas can limit output. Providing training and development opportunities, promoting skill diversification, and hiring skilled personnel can address this.
-
Motivation and Morale: Demotivated or disengaged employees are less productive. Creating a positive work environment, fostering teamwork, and offering incentive programs can boost morale and productivity.
-
Workplace Ergonomics: Poorly designed workspaces can lead to fatigue, discomfort, and injuries, reducing productivity. Investing in ergonomic furniture and equipment, promoting regular breaks, and implementing safety protocols are essential.
4. External Factors
-
Supply Chain Disruptions: Delays or disruptions in the supply of raw materials or components directly impact output. Diversifying suppliers, implementing just-in-time inventory management, and building strong supplier relationships can mitigate this risk.
-
Demand Fluctuations: Inconsistent demand makes it difficult to optimize capacity utilization. Implementing demand forecasting techniques and employing flexible manufacturing strategies can help smooth out production.
-
Economic Downturns: Economic recessions or industry-specific downturns can lead to reduced demand and underutilized capacity. Developing flexible business strategies, exploring new markets, and diversifying product offerings can help mitigate the impact.
-
Regulatory Changes: New regulations or changes in environmental standards can impact production processes and reduce capacity. Staying informed about regulatory changes, proactively adapting to new requirements, and investing in compliance can minimize disruptions.
5. Quality Control Issues
-
High Defect Rates: A high rate of defective products reduces effective capacity as time is spent on rework, scrap, and inspection. Implementing robust quality control measures, employing statistical process control (SPC), and focusing on continuous improvement are crucial.
-
Rework and Scrap: Time spent on fixing defects or disposing of faulty products reduces available capacity. Focusing on preventative quality control, implementing root cause analysis to identify the sources of defects, and improving processes are essential.
-
Inspection Bottlenecks: Inefficient inspection processes can create bottlenecks, delaying production. Optimizing inspection procedures, utilizing automation, and employing statistical sampling techniques can improve efficiency.
Mitigation Strategies for Increased Effective Capacity
Addressing the factors that reduce effective capacity requires a multifaceted approach. Here are some key strategies:
-
Invest in Preventive Maintenance: Regular maintenance prevents equipment breakdowns and minimizes downtime.
-
Optimize Workflows: Streamline processes to eliminate bottlenecks and reduce waste.
-
Improve Employee Training: Provide comprehensive training to enhance employee skills and efficiency.
-
Implement Effective Scheduling: Utilize scheduling techniques to optimize resource allocation and minimize idle time.
-
Enhance Supply Chain Management: Strengthen relationships with suppliers and diversify supply sources to ensure timely delivery.
-
Improve Quality Control: Implement rigorous quality control measures to reduce defects and minimize rework.
-
Utilize Technology: Leverage technology to automate tasks, improve efficiency, and enhance decision-making.
-
Foster a Positive Work Environment: Create a motivating work environment to boost employee morale and productivity.
-
Monitor and Measure Key Performance Indicators (KPIs): Track relevant metrics to identify areas for improvement and measure the effectiveness of implemented strategies. Examples include Overall Equipment Effectiveness (OEE), production lead times, and defect rates.
-
Embrace Continuous Improvement: Regularly evaluate processes and identify opportunities for improvement using methodologies like Six Sigma or Kaizen.
Conclusion: A Holistic Approach to Capacity Optimization
Maximizing effective capacity is a continuous process that requires a holistic approach. By systematically addressing equipment limitations, process inefficiencies, human factors, external influences, and quality control issues, businesses can significantly enhance their operational efficiency, increase productivity, and ultimately, achieve greater profitability. The key is to proactively identify potential bottlenecks, implement appropriate mitigation strategies, and continuously monitor performance to drive improvement. Remember that a focus on prevention is always more cost-effective than dealing with the consequences of reduced capacity.
Latest Posts
Latest Posts
-
2 09 Unit Test Radicals And Complex Numbers
May 25, 2025
-
The Absolutely True Diary Of A Part Time Indian Characters
May 25, 2025
-
Lymphatic Nodules Are Encapsulated Lymphatic Organs
May 25, 2025
-
Verbs With Etre In Passe Compose
May 25, 2025
-
How Many Chapters Is In The Fault In Our Stars
May 25, 2025
Related Post
Thank you for visiting our website which covers about Which Of The Following Would Tend To Reduce Effective Capacity . We hope the information provided has been useful to you. Feel free to contact us if you have any questions or need further assistance. See you next time and don't miss to bookmark.