What Is The Difference Between Ac And Dc Motors
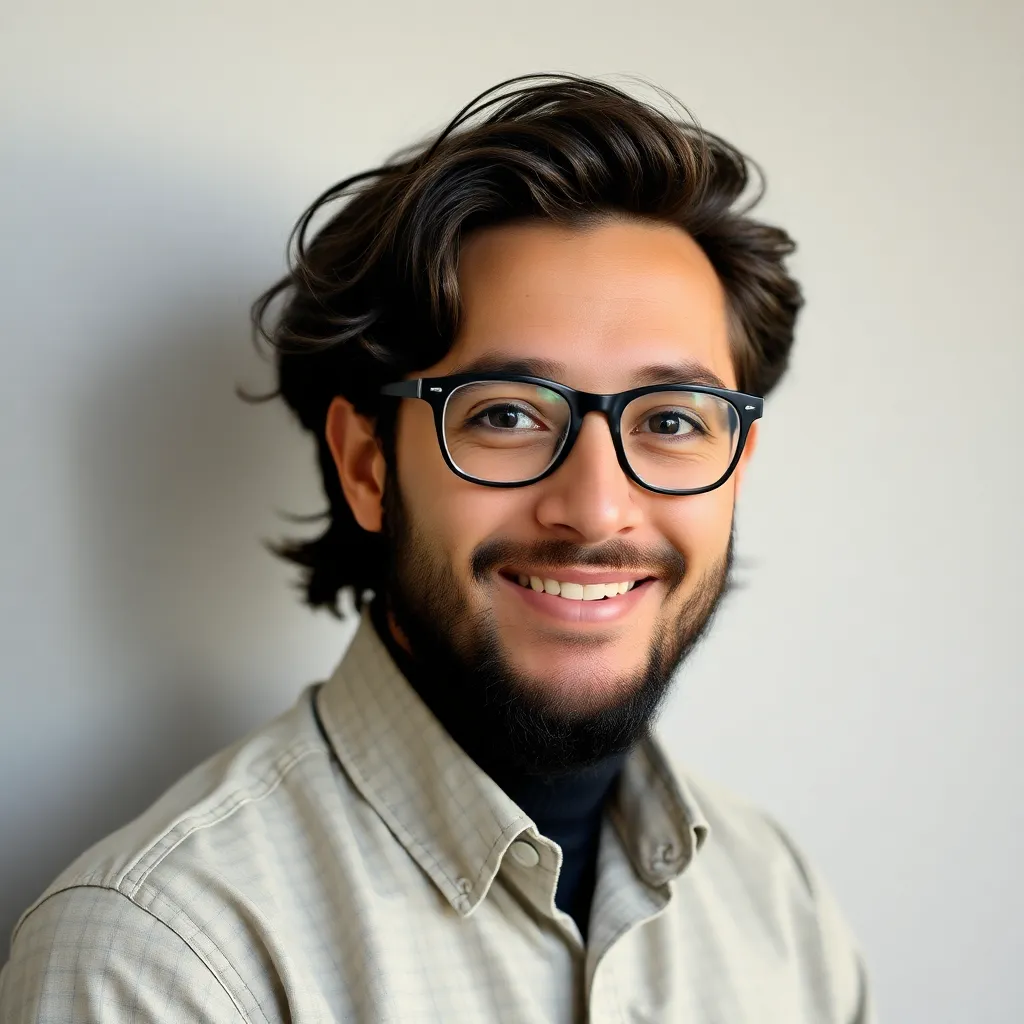
Juapaving
Apr 02, 2025 · 6 min read
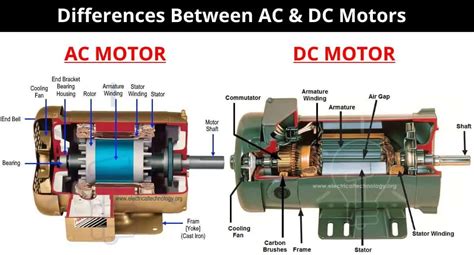
Table of Contents
AC vs. DC Motors: A Deep Dive into the Differences
Choosing the right motor for your application can be crucial for its success. Understanding the fundamental differences between AC and DC motors is paramount to making informed decisions. This comprehensive guide delves into the core distinctions, exploring their operating principles, advantages, disadvantages, and typical applications. We'll equip you with the knowledge to confidently navigate the world of electric motors.
Understanding Alternating Current (AC) and Direct Current (DC)
Before diving into the motor types, let's quickly refresh our understanding of AC and DC power.
-
Direct Current (DC): DC electricity flows in one direction, consistently from a negative terminal to a positive terminal. Batteries, solar cells, and DC power supplies are common sources of DC power. The voltage remains relatively constant over time.
-
Alternating Current (AC): AC electricity, conversely, periodically reverses its direction of flow. The voltage and current also change periodically, typically following a sinusoidal waveform. This cyclical change is characterized by frequency, usually measured in Hertz (Hz), representing the number of cycles per second. Household power outlets typically provide AC power.
AC Motor Types and Their Characteristics
AC motors are broadly categorized into several types, each with unique operating principles and applications. The most prevalent types are:
1. Induction Motors (Asynchronous Motors):
These are the workhorses of the industrial world, known for their robustness, simplicity, and cost-effectiveness. They operate on the principle of electromagnetic induction, where a rotating magnetic field in the stator (stationary part) induces current in the rotor (rotating part), causing it to spin.
- Advantages: Simple construction, low maintenance, high reliability, robust design, relatively low cost.
- Disadvantages: Speed regulation can be challenging, lower starting torque compared to some DC motors, efficiency can be lower at part loads.
- Applications: Fans, pumps, compressors, conveyors, industrial machinery. They're ideal for applications where speed control isn't paramount.
Types of Induction Motors:
- Squirrel Cage Motors: The most common type, featuring a rotor with conductive bars embedded in a steel core, resembling a squirrel cage.
- Wound Rotor Motors: These motors have a wound rotor with slip rings, allowing for better speed control and higher starting torque.
2. Synchronous Motors:
Synchronous motors operate at a constant speed directly proportional to the frequency of the AC power supply. They require a separate excitation source to create the magnetic field in the rotor.
- Advantages: Constant speed operation, high efficiency at full load, power factor correction capability.
- Disadvantages: More complex design, higher cost, requires an excitation source.
- Applications: Clocks, timers, precision instruments, applications requiring precise speed control, high-power applications where constant speed is crucial.
3. Stepper Motors:
Stepper motors are unique in that they rotate in discrete steps rather than continuously. They are controlled by digital signals and offer precise positioning capabilities.
- Advantages: Precise positioning, open-loop control, high torque at low speeds, simple control.
- Disadvantages: Limited speed range, potential for resonance issues at higher speeds, relatively lower torque compared to other AC motors at higher speeds.
- Applications: Printers, CNC machines, robotics, positioning systems, automation systems.
DC Motor Types and Their Characteristics
DC motors are characterized by their simple construction and precise speed control. Their operation relies on the interaction between a magnetic field and a current-carrying conductor.
1. Brushed DC Motors:
These motors are the most common type of DC motor. They utilize brushes and a commutator to switch the direction of current flow in the rotor, maintaining a unidirectional torque.
- Advantages: Simple construction, high starting torque, good speed control, relatively low cost.
- Disadvantages: Limited lifespan due to brush wear, higher maintenance, susceptible to sparking and electrical noise, not suitable for high-speed applications.
- Applications: Toys, appliances, tools, small robotics, low-power applications.
2. Brushless DC Motors (BLDC Motors):
BLDC motors eliminate the need for brushes, using electronic commutation to switch the current flow. This leads to significantly longer lifespan and higher efficiency.
- Advantages: Longer lifespan, higher efficiency, quieter operation, higher speed capability, less maintenance.
- Disadvantages: Higher cost, more complex control circuitry required.
- Applications: Electric vehicles, drones, high-performance appliances, servo systems, industrial automation.
3. Permanent Magnet DC Motors:
These motors use permanent magnets to create the magnetic field in the stator.
- Advantages: Simple construction, high torque-to-weight ratio, relatively good speed control.
- Disadvantages: Magnetic field strength can degrade over time, less efficient at high speeds.
- Applications: Small appliances, toys, robotics, various industrial applications.
4. Series Wound DC Motors:
In these motors, the field winding is connected in series with the armature winding.
- Advantages: High starting torque, high speed at light loads.
- Disadvantages: Speed can vary significantly with load changes, risk of runaway if the load is suddenly removed.
- Applications: Electric vehicles, electric trains, traction applications.
5. Shunt Wound DC Motors:
The field winding in these motors is connected in parallel with the armature winding.
- Advantages: Relatively constant speed under varying loads, good speed regulation.
- Disadvantages: Lower starting torque compared to series wound motors.
- Applications: Constant speed applications, machine tools, industrial machinery.
Key Differences Summarized:
Feature | AC Motor | DC Motor |
---|---|---|
Power Supply | Alternating Current | Direct Current |
Construction | Generally more robust and simpler | Can range from simple to complex |
Speed Control | Can be challenging, depends on type | Generally easier and more precise |
Starting Torque | Varies greatly depending on type | Generally higher, especially in DC brushed |
Maintenance | Typically lower maintenance | Higher for brushed motors, lower for brushless |
Efficiency | Varies depending on type and load | Can be high, particularly brushless |
Cost | Generally lower cost | Can be higher, especially for brushless |
Noise | Can be noisy, depending on type | Brushless are quieter than brushed |
Lifespan | Generally long lifespan | Brushless motors have a much longer lifespan |
Choosing the Right Motor: Application Considerations
The selection of an AC or DC motor hinges heavily on the specific application requirements. Here's a breakdown to guide your decision-making process:
-
Speed Control: If precise speed control is critical, DC motors, especially brushless DC motors, are generally preferred. AC motors, while offering some speed control options, often lack the precision of DC motors.
-
Starting Torque: Applications demanding high starting torque are well-suited for DC motors or certain types of AC motors like wound-rotor induction motors.
-
Cost: AC induction motors are often the most cost-effective option. However, the higher upfront cost of brushless DC motors can be justified by their longer lifespan and higher efficiency over their operational lifetime.
-
Maintenance: The lower maintenance requirements of AC induction motors are a significant advantage in many industrial settings. Brushless DC motors offer similar low-maintenance benefits.
-
Environmental Factors: The operating environment must also be considered. Harsh environments might necessitate motors with robust enclosures and protection against dust, moisture, or extreme temperatures.
-
Power Supply Availability: The availability of AC or DC power sources dictates the motor type. Most industrial settings have readily available AC power, while DC power might be more common in specialized applications like electric vehicles.
Conclusion: A Balanced Perspective
The "best" motor type – AC or DC – isn't a universally applicable answer. The ideal choice depends entirely on the specific application's needs. This in-depth comparison should empower you to analyze the requirements of your project and select the motor that optimally balances performance, cost, efficiency, and maintenance considerations. Remember to always consider factors like speed control precision, starting torque requirements, cost constraints, and the overall operating environment to ensure optimal performance and longevity. Careful planning and consideration will lead to a successful and efficient motor integration in your project.
Latest Posts
Latest Posts
-
Predict The Major Product For The Following Reaction
Apr 03, 2025
-
Differentiate The Major Characteristics Of Each Group Of Microorganisms
Apr 03, 2025
-
Are Data And Information Interchangeable Terms
Apr 03, 2025
-
How Is Photosynthesis And Cellular Respiration Different
Apr 03, 2025
-
Which Of The Following Is Strongest Acid
Apr 03, 2025
Related Post
Thank you for visiting our website which covers about What Is The Difference Between Ac And Dc Motors . We hope the information provided has been useful to you. Feel free to contact us if you have any questions or need further assistance. See you next time and don't miss to bookmark.