What Are The 3 Types Of Wires
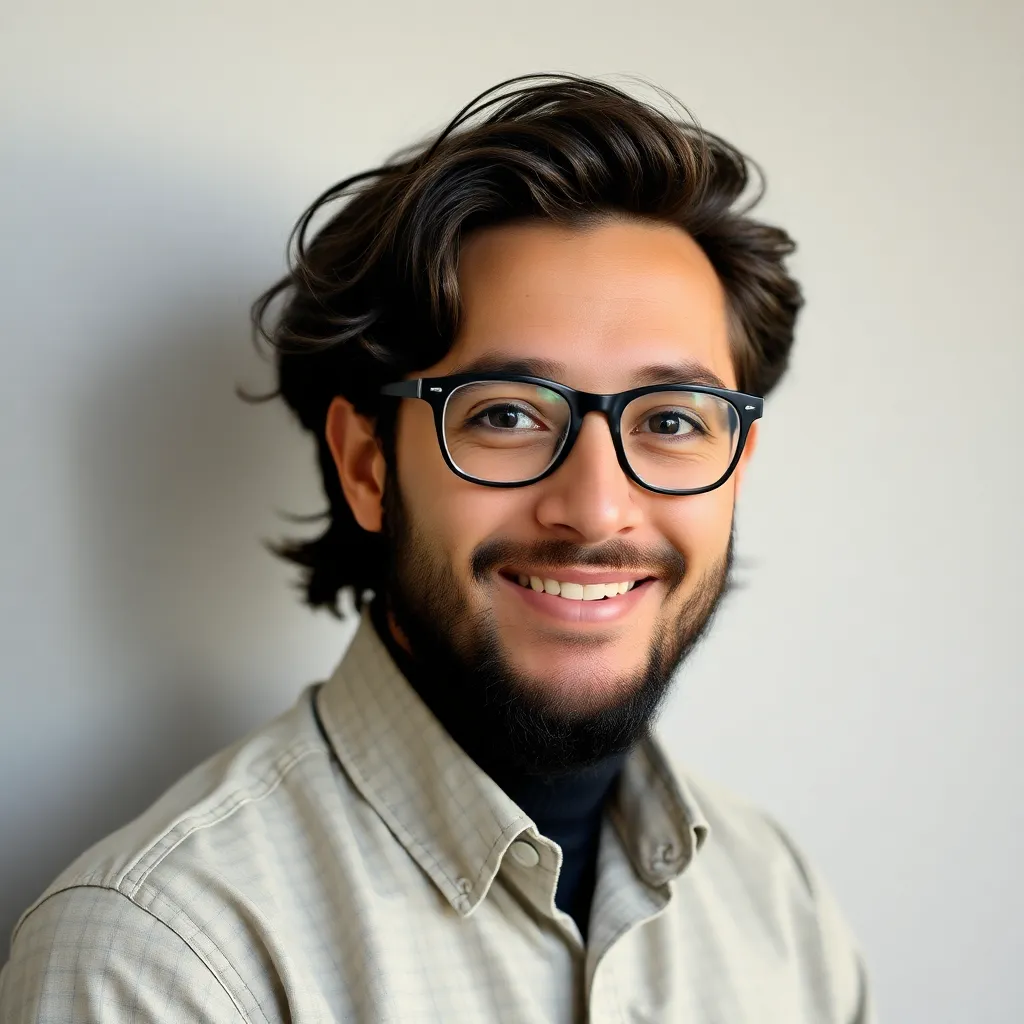
Juapaving
Mar 18, 2025 · 6 min read
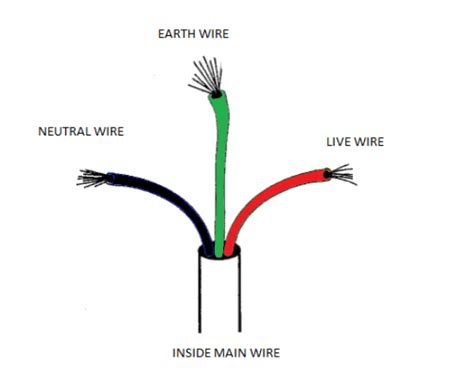
Table of Contents
What Are the 3 Types of Wires? A Deep Dive into Electrical Conductors
The seemingly simple question, "What are the 3 types of wires?" belies a complex world of electrical conductors. While a simplistic answer might point to solid core, stranded, and braided wires, a more accurate and comprehensive understanding requires a deeper dive into the materials, construction, applications, and properties of these conductors. This exploration will delve into the nuanced differences between various wire types, exploring far beyond a basic tripartite classification. We’ll examine not just the three main categories, but also sub-categories and specific applications within each, providing a robust understanding of wire selection for diverse projects.
Beyond the Basics: A More Comprehensive Classification
The initial categorization into three wire types – solid core, stranded, and braided – serves as a helpful starting point, but it lacks the granularity needed to address the wide spectrum of wire applications. A more detailed classification considers the following factors:
1. Conductor Material: The Heart of the Wire
The material forming the wire's core significantly impacts its properties, including conductivity, flexibility, durability, and resistance to corrosion. The most common conductor materials include:
-
Copper (Cu): Universally favored for its exceptional conductivity, relatively low cost, and ease of processing. Copper wires are used in a vast range of applications, from household wiring to high-voltage transmission lines. Different grades of copper exist, influencing cost and performance.
-
Aluminum (Al): Lighter than copper, aluminum is often used in high-voltage power transmission lines where weight is a critical factor. However, its conductivity is lower than copper, and it's more susceptible to corrosion and oxidation. Special alloys and coatings are often employed to mitigate these issues.
-
Steel: While not as conductive as copper or aluminum, steel wire finds applications where high tensile strength is paramount, such as supporting communication cables. Steel is frequently used as a reinforcing element within other wires for enhanced mechanical strength.
-
Other Alloys: Various copper alloys (such as copper-clad steel) and other metallic alloys are utilized for specialized applications. These combinations leverage the unique properties of each component material, optimizing the wire for specific performance requirements. Examples include improved corrosion resistance or enhanced strength.
2. Wire Construction: Solid Core vs. Stranded vs. Braided
This classification focuses on the physical structure of the wire:
-
Solid Core Wire: As the name suggests, solid core wire consists of a single, solid conductor. This design offers high current-carrying capacity and excellent conductivity for its cross-sectional area. However, it's relatively inflexible and prone to breakage under repeated bending or vibration. It's primarily used in applications where flexibility isn't critical, such as fixed wiring in buildings. Its simpler construction often leads to lower manufacturing costs.
-
Stranded Wire: Stranded wire comprises multiple smaller strands of wire twisted together. This construction enhances flexibility and resistance to fatigue, making it ideal for applications requiring frequent movement or vibration, such as appliance cords, automotive wiring, and extension cables. The number of strands and their individual diameters determine the overall wire gauge and current-carrying capacity. A higher strand count increases flexibility at the expense of slightly higher resistance.
-
Braided Wire: Braided wire employs many fine strands woven together in a braided configuration, much like a rope. This construction offers superior flexibility compared to stranded wire, excellent shielding properties (particularly when used with conductive materials like copper), and good resistance to abrasion. Commonly used in applications such as shielding in cables, flexible conductors in robotics, and grounding applications. The braid's density influences its shielding effectiveness and flexibility.
3. Insulation Type and Material: Protecting the Conductor
The insulating material surrounding the conductor plays a crucial role in electrical safety, environmental protection, and performance. Different insulating materials are chosen based on the wire's intended application and the operating conditions:
-
PVC (Polyvinyl Chloride): A common and inexpensive insulating material offering good dielectric strength and durability. It is widely used in household wiring and general-purpose applications. However, PVC has limitations in terms of its temperature resistance and flexibility at low temperatures.
-
XLPE (Cross-Linked Polyethylene): A superior insulating material offering higher temperature resistance, improved flexibility, and enhanced dielectric strength compared to PVC. Commonly used in high-voltage power cables and industrial applications where higher operating temperatures and greater flexibility are required.
-
Teflon (PTFE): Provides excellent chemical and heat resistance, making it suitable for high-temperature applications and environments where chemicals are present. Teflon-insulated wire is often more expensive than PVC- or XLPE-insulated wire.
-
Silicone Rubber: Another high-temperature option, silicone rubber offers good flexibility and chemical resistance.
4. Wire Gauge and Current Capacity: Matching the Application
The wire gauge, expressed in AWG (American Wire Gauge) or similar standards, determines the wire's diameter and its ability to carry current safely. A larger gauge number indicates a smaller diameter wire. Selecting the appropriate gauge is crucial to prevent overheating and potential fire hazards. Factors like the length of the wire, the ambient temperature, and the insulation type all influence the safe current carrying capacity.
5. Wire Sheathing and Jacketing: Providing Additional Protection
Beyond insulation, many wires incorporate sheathing or jacketing for additional protection. This outer layer can provide resistance to abrasion, moisture, chemicals, or UV radiation. Common materials include PVC, polyethylene, nylon, and other specialized polymers.
Specific Applications and Wire Type Selection
The choice of wire depends heavily on its intended application. Here are some examples:
-
Household Wiring: Typically uses solid core copper wire with PVC insulation for its cost-effectiveness and good conductivity.
-
Appliance Cords: Employs stranded copper wire with PVC or other flexible insulation to accommodate the movement of the appliance.
-
Automotive Wiring: Utilizes stranded copper wire with specialized insulation designed to withstand high temperatures and vibrations.
-
High-Voltage Transmission Lines: Often uses aluminum conductors reinforced with steel for superior tensile strength and reduced weight. The insulation may be XLPE or other specialized materials designed for high voltage.
-
Electronic Circuits: May employ fine gauge stranded or solid core wires with thin insulation for precision and flexibility.
Beyond the "Three Types": Specialised Wires
The initial three-category classification is a simplification. Many specialized wire types exist, tailored to niche applications:
-
Coaxial Cable: Designed for high-frequency signal transmission, utilizing a central conductor surrounded by insulation, a conductive shield, and an outer jacket.
-
Fiber Optic Cable: Transmits data using light pulses through optical fibers enclosed within a protective jacket.
-
Multi-Conductor Cable: Contains multiple insulated conductors bundled together within a common sheath.
-
Shielded Cable: Includes a metallic braid or foil shield to minimize electromagnetic interference.
-
Ribbon Cable: Features multiple parallel conductors in a flat, ribbon-like configuration, often used in computer systems.
Conclusion: Choosing the Right Wire
Selecting the correct wire for a specific application requires careful consideration of various factors. The "three types" of wires – solid core, stranded, and braided – provide a foundational understanding but are insufficient to encompass the breadth and diversity of wire types used across various industries and applications. Understanding conductor materials, insulation types, wire gauge, and additional protective layers enables informed decisions, ensuring both electrical safety and optimal performance. Remember to always consult relevant electrical codes and standards for specific requirements and best practices. The proper selection of wire is crucial for safety and the reliability of any electrical system.
Latest Posts
Latest Posts
-
Natural Boundary Between France And Itsly
Mar 18, 2025
-
How Many Side Does A Octagon Have
Mar 18, 2025
-
What Kingdom Does Euglena Belong To
Mar 18, 2025
-
Lcm Of 5 4 And 2
Mar 18, 2025
-
Which Action Is A Reflex Action
Mar 18, 2025
Related Post
Thank you for visiting our website which covers about What Are The 3 Types Of Wires . We hope the information provided has been useful to you. Feel free to contact us if you have any questions or need further assistance. See you next time and don't miss to bookmark.