Polar Moment Of Inertia Hollow Cylinder
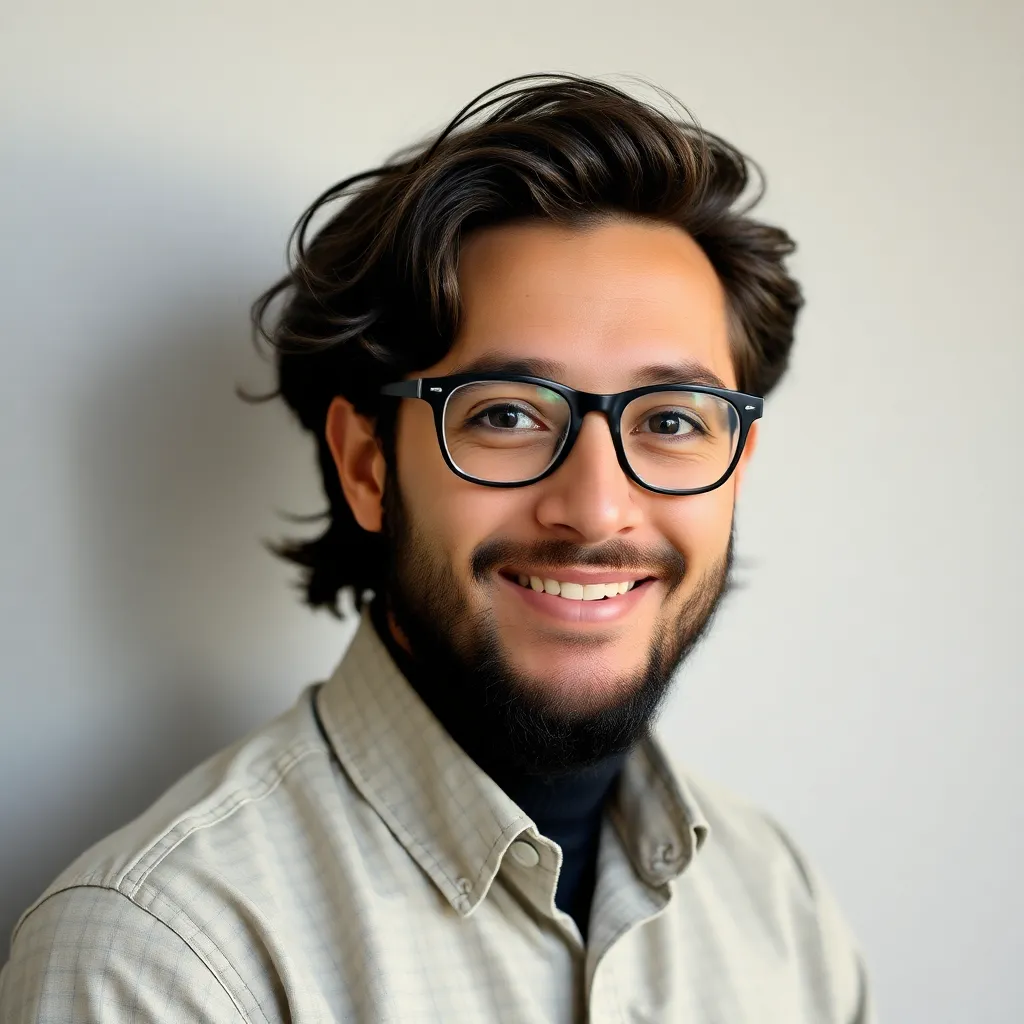
Juapaving
Apr 05, 2025 · 6 min read
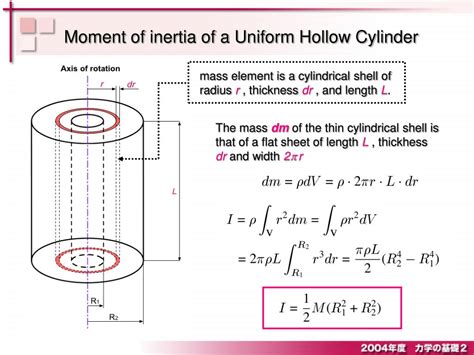
Table of Contents
Polar Moment of Inertia of a Hollow Cylinder: A Comprehensive Guide
The polar moment of inertia, often denoted as J or Ip, is a crucial concept in engineering mechanics, particularly when dealing with torsional stresses and rotational dynamics. Understanding this property is vital for designing shafts, axles, and other rotating components to withstand twisting forces without failure. This article delves into the polar moment of inertia of a hollow cylinder, exploring its calculation, applications, and significance in various engineering disciplines.
What is the Polar Moment of Inertia?
The polar moment of inertia quantifies a body's resistance to torsional deformation. Imagine twisting a cylindrical shaft; a shaft with a larger polar moment of inertia will resist twisting more effectively than one with a smaller value. It represents the sum of the moments of inertia about the x and y axes, which are perpendicular to each other and lie in the plane of the cross-section. In essence, it measures the distribution of mass around the central axis of rotation. Unlike the area moment of inertia, which is used for bending calculations, the polar moment of inertia focuses specifically on torsional behavior.
Calculating the Polar Moment of Inertia for a Hollow Cylinder
A hollow cylinder, also known as a tube or pipe, is a common structural element in many engineering applications. Calculating its polar moment of inertia requires understanding its geometry and applying the appropriate formula. The derivation of the formula hinges on integrating the infinitesimal area elements over the entire cross-sectional area.
The formula for the polar moment of inertia of a hollow cylinder is:
J = (π/2)(Ro⁴ - Ri⁴)
Where:
- J represents the polar moment of inertia.
- Ro represents the outer radius of the hollow cylinder.
- Ri represents the inner radius of the hollow cylinder.
This formula assumes a solid, homogeneous material with uniform density across the cylinder's cross-section. For complex materials or non-uniform density, more advanced techniques may be necessary.
Step-by-Step Calculation:
Let's illustrate this with a numerical example. Consider a hollow cylinder with an outer radius of 10 cm (0.1 m) and an inner radius of 5 cm (0.05 m).
-
Input Values: We have Ro = 0.1 m and Ri = 0.05 m.
-
Apply the Formula: Substitute the values into the formula:
J = (π/2) * ( (0.1 m)⁴ - (0.05 m)⁴ )
-
Calculation: Perform the calculation using a calculator:
J ≈ 7.36 x 10⁻⁵ m⁴
Therefore, the polar moment of inertia of this hollow cylinder is approximately 7.36 x 10⁻⁵ m⁴. This value indicates the cylinder's resistance to torsional stress. A larger value signifies greater resistance.
Relationship with Torsional Stress and Shear Stress
The polar moment of inertia is directly related to torsional stress and shear stress within the cylinder. When a torque (T) is applied to the hollow cylinder, it experiences torsional shear stress (τ). The relationship is defined by the following equation:
τ = (T * r) / J
Where:
- τ is the shear stress.
- T is the applied torque.
- r is the radial distance from the center of the cylinder.
- J is the polar moment of inertia.
This equation demonstrates that the shear stress is inversely proportional to the polar moment of inertia. A larger J implies a lower shear stress for the same applied torque, reducing the risk of failure due to shear. This highlights the importance of selecting materials and dimensions that yield a sufficiently large polar moment of inertia to withstand anticipated torsional loads.
Applications of Polar Moment of Inertia in Engineering
The concept of polar moment of inertia finds extensive use in various engineering fields:
1. Mechanical Engineering:
-
Shaft Design: In designing rotating shafts for machinery (e.g., in motors, turbines, or gearboxes), engineers use the polar moment of inertia to determine the shaft's ability to withstand torsional loads without exceeding allowable shear stress limits. The appropriate diameter is selected to ensure the shaft won't twist excessively or fail under operational conditions.
-
Axle Design: Similarly, axles in vehicles and other applications are designed with consideration for the polar moment of inertia to handle torsional forces from the wheels and other connected components.
-
Power Transmission: In power transmission systems involving rotating components, the polar moment of inertia is crucial for analyzing torsional vibrations and preventing resonance, which can lead to catastrophic failures.
2. Civil Engineering:
-
Column Design: Though less directly applied than in mechanical engineering, the polar moment of inertia can be relevant in certain column designs that experience torsional loads alongside axial compression.
-
Bridge Design: In some bridge designs, particularly those incorporating rotating components or subjected to torsional forces from wind or seismic activity, understanding the polar moment of inertia of relevant structural elements becomes critical.
3. Aerospace Engineering:
- Aircraft Design: In designing aircraft components such as propellers and turbine shafts, the polar moment of inertia is vital in ensuring sufficient strength and rigidity against torsional loads during flight operations.
Factors Affecting Polar Moment of Inertia
Several factors influence a hollow cylinder's polar moment of inertia:
-
Outer Radius (Ro): Increasing the outer radius significantly increases the polar moment of inertia. This is because a larger radius moves more mass farther from the axis of rotation, increasing its contribution to the resistance against twisting.
-
Inner Radius (Ri): Increasing the inner radius reduces the polar moment of inertia. Removing material from the center weakens the cylinder's torsional resistance.
-
Material Density: While not directly included in the formula, material density affects the mass distribution and consequently influences the polar moment of inertia. A denser material will have a higher moment of inertia for the same dimensions.
-
Material Properties: Material properties such as shear modulus (G) and yield strength impact the cylinder's ability to withstand torsional loads, although they're not directly part of the polar moment of inertia calculation. A material with a higher shear modulus will resist twisting more effectively.
Advanced Considerations and Non-Circular Cross-Sections
The formula presented earlier applies specifically to hollow cylinders with perfectly circular cross-sections. For non-circular cross-sections (e.g., rectangular tubes, elliptical tubes), the calculation becomes more complex and may require the use of integral calculus or specialized software for accurate determination of the polar moment of inertia. The complexity arises due to the variation in the distance of the mass elements from the central axis of rotation.
For complex geometries, numerical methods such as Finite Element Analysis (FEA) are frequently employed. FEA is particularly useful for modeling intricate shapes and analyzing stress distributions under various load conditions.
Conclusion
The polar moment of inertia of a hollow cylinder is a fundamental concept in engineering mechanics. Its understanding is paramount for the design and analysis of rotating components subjected to torsional loads. The formula provided offers a straightforward method for calculation in the case of circular hollow cylinders, while more advanced techniques are needed for complex geometries. By correctly applying this concept and understanding the factors influencing it, engineers ensure the structural integrity and operational reliability of various engineering systems. Accurate calculation of the polar moment of inertia is essential for preventing catastrophic failures and optimizing designs for maximum performance and safety. The relationship between the polar moment of inertia, torsional stress, and shear stress serves as a crucial link in structural analysis and ensures the safe and efficient operation of countless engineered systems.
Latest Posts
Latest Posts
-
A Pectoral Girdle Consists Of Two Bones The And The
Apr 05, 2025
-
How Many Feet Is 26 Inches
Apr 05, 2025
-
Actin And Myosin Are What Type Of Biological Molecule
Apr 05, 2025
-
Fluid Part Of Blood After Removal Of Corpuscles Is
Apr 05, 2025
-
Is A Substance In Which Another Substance Is Dissolved
Apr 05, 2025
Related Post
Thank you for visiting our website which covers about Polar Moment Of Inertia Hollow Cylinder . We hope the information provided has been useful to you. Feel free to contact us if you have any questions or need further assistance. See you next time and don't miss to bookmark.