How To Calculate Efficiency Of Machine
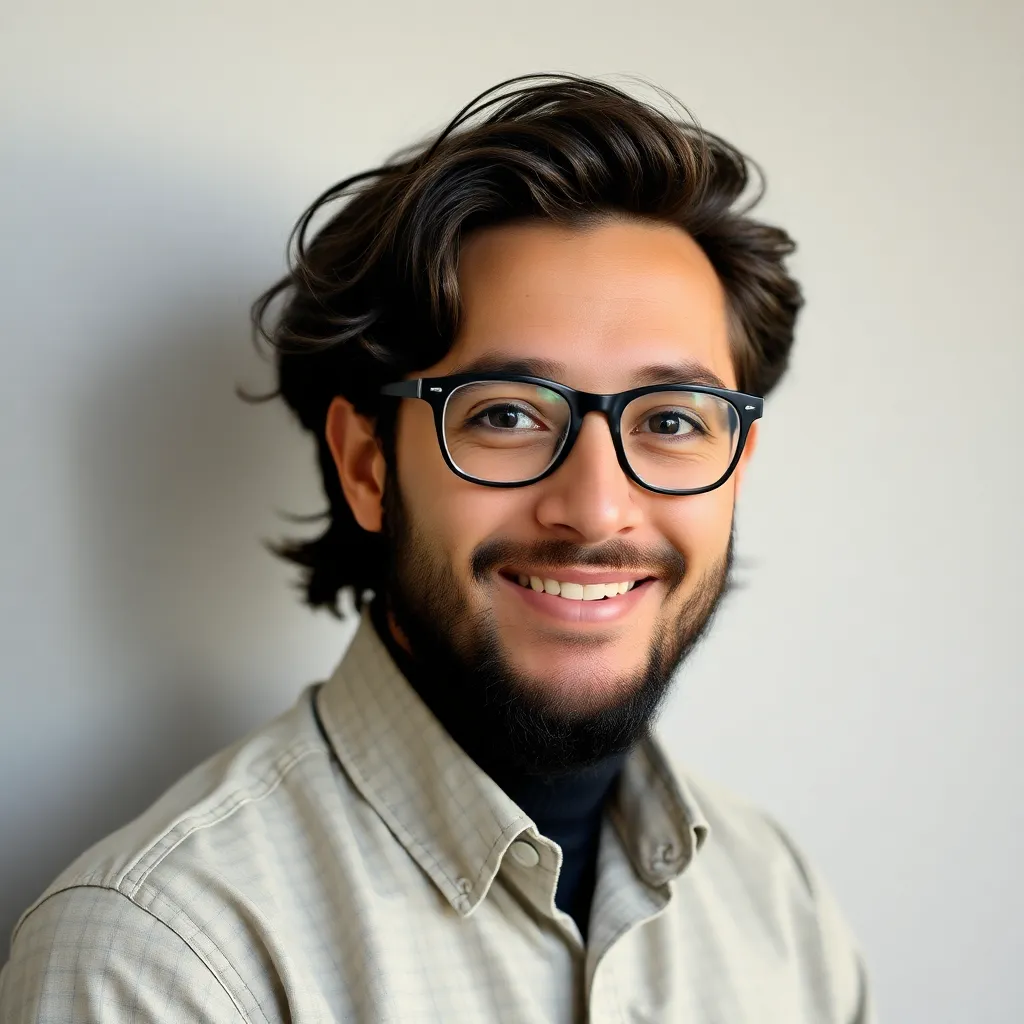
Juapaving
May 09, 2025 · 6 min read
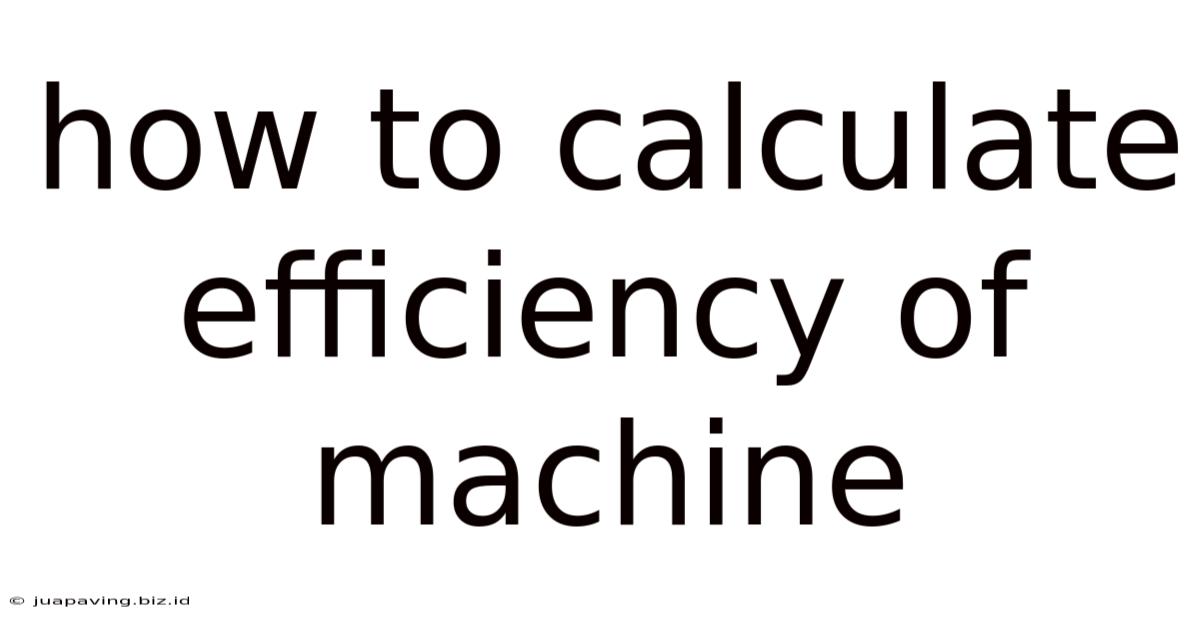
Table of Contents
How to Calculate the Efficiency of a Machine
Calculating the efficiency of a machine is crucial for optimizing performance, minimizing energy waste, and maximizing productivity. Understanding efficiency helps identify areas for improvement, whether through maintenance, upgrades, or process redesign. This comprehensive guide will walk you through various methods for calculating machine efficiency, considering different types of machines and applications.
Understanding Machine Efficiency
Machine efficiency is a measure of how effectively a machine converts input energy or resources into useful output. It's expressed as a percentage, representing the ratio of useful output to the total input. A higher percentage signifies a more efficient machine, meaning less energy or resources are wasted in the process. Inefficient machines consume more resources, leading to increased operational costs and environmental impact.
Key Concepts:
-
Input: This represents the energy, materials, or resources consumed by the machine during operation. This could be electrical power, fuel consumption, raw materials, or labor. It's critical to accurately measure the input to obtain a reliable efficiency calculation.
-
Output: This is the useful work or product generated by the machine. This can be mechanical work (e.g., lifting weight, cutting material), a finished product (e.g., manufactured parts, processed food), or energy produced (e.g., electrical power generation). Defining and quantifying the output is equally important as accurately measuring the input.
-
Losses: Inefficiencies arise from various losses within the machine, such as friction, heat, vibration, and material waste. Understanding these loss mechanisms is crucial for improving efficiency.
Methods for Calculating Machine Efficiency
The method used to calculate machine efficiency depends on the type of machine and the nature of its input and output. Here are some common methods:
1. Mechanical Efficiency
This method is typically used for mechanical machines where the input and output are measured in terms of work or power.
Formula:
Mechanical Efficiency = (Useful Work Output / Work Input) x 100%
Where:
-
Useful Work Output: This is the work done by the machine, often measured in Joules (J) or kilowatt-hours (kWh). This considers only the useful work performed, excluding losses. For example, in a lifting machine, this would be the potential energy gained by the lifted object.
-
Work Input: This is the total work supplied to the machine, also measured in Joules (J) or kilowatt-hours (kWh). This includes all energy input, regardless of whether it results in useful work. For a motor-driven machine, it's the electrical energy consumed.
Example: A motor lifts a 100kg weight 5 meters. The motor consumes 6000 Joules of energy. The useful work output is the potential energy gained by the weight (mgh = 100kg * 9.8m/s² * 5m = 4900J).
Mechanical Efficiency = (4900J / 6000J) x 100% = 81.67%
2. Thermal Efficiency
This is used for machines that convert heat energy into other forms of energy, such as engines or power plants.
Formula:
Thermal Efficiency = (Useful Work Output / Heat Input) x 100%
Where:
-
Useful Work Output: This is the work produced, typically measured in Joules (J) or kilowatt-hours (kWh).
-
Heat Input: This is the heat energy supplied to the machine, usually measured in Joules (J) or British Thermal Units (BTU).
Example: A heat engine produces 5000 Joules of work from 10000 Joules of heat input.
Thermal Efficiency = (5000J / 10000J) x 100% = 50%
3. Electrical Efficiency
This method is applicable to machines that convert electrical energy into other forms of energy, such as motors, transformers, or electronic devices.
Formula:
Electrical Efficiency = (Useful Electrical Power Output / Electrical Power Input) x 100%
Where:
-
Useful Electrical Power Output: This is the useful electrical power delivered by the machine, measured in Watts (W) or kilowatts (kW). For example, in a power supply, this would be the power delivered to the load.
-
Electrical Power Input: This is the total electrical power supplied to the machine, measured in Watts (W) or kilowatts (kW).
Example: A transformer receives 10 kW of power and delivers 9 kW to the load.
Electrical Efficiency = (9kW / 10kW) x 100% = 90%
4. Manufacturing Process Efficiency
This type of efficiency calculation focuses on the effectiveness of a manufacturing process, incorporating factors beyond just the machine itself.
Formula:
Manufacturing Process Efficiency = (Standard Output / Actual Output) x 100%
Where:
-
Standard Output: This is the expected output based on ideal conditions and process parameters.
-
Actual Output: This is the actual output achieved during the production process.
This calculation considers factors such as downtime, material waste, and defects, providing a broader picture of overall efficiency.
Factors Affecting Machine Efficiency
Several factors contribute to or detract from machine efficiency. Understanding these factors is crucial for improvement efforts.
-
Friction: Friction between moving parts is a major source of energy loss, leading to reduced efficiency. Lubrication, proper alignment, and using low-friction materials can minimize this loss.
-
Heat: Heat generated due to friction, electrical resistance, or other processes represents wasted energy. Effective cooling systems can help mitigate heat losses.
-
Wear and Tear: As machines age, wear and tear increase friction and other losses, reducing efficiency. Regular maintenance and timely repairs are critical for sustaining performance.
-
Material Properties: The properties of the materials used in the machine significantly impact its efficiency. Using stronger, lighter, and more durable materials can lead to better performance.
-
Design and Construction: The design and construction of a machine have a significant impact on its efficiency. Aerodynamic designs can reduce drag in fluid systems; optimized geometry can reduce friction.
-
Operating Conditions: Environmental conditions, such as temperature and humidity, can affect machine efficiency. Operating within the designed parameters is essential.
-
Operator Skill: Operator skill and proper operation of the machine are important factors affecting efficiency. Trained operators ensure optimal performance.
Improving Machine Efficiency
Improving machine efficiency involves a systematic approach focusing on addressing the identified inefficiencies.
-
Regular Maintenance: Regular maintenance is crucial for preventing breakdowns and maintaining optimal performance. This includes lubrication, cleaning, and inspections.
-
Process Optimization: Analyzing the entire process and identifying bottlenecks can reveal areas for improvement. Streamlining operations and eliminating unnecessary steps can increase efficiency.
-
Technology Upgrades: Upgrading to more efficient machines or components can significantly improve overall efficiency. This might involve implementing new technologies or replacing outdated parts.
-
Energy Management: Implementing energy-efficient practices, such as using energy-efficient motors or implementing energy recovery systems, can reduce energy consumption and improve efficiency.
-
Training and Development: Training operators on best practices and proper operating procedures ensures optimal utilization of the machine.
-
Data Analysis: Monitoring machine performance using sensors and data acquisition systems allows for identifying areas of inefficiency and implementing targeted improvements.
Conclusion
Calculating machine efficiency is a crucial task for any industry striving for optimal productivity and cost-effectiveness. By accurately measuring input and output, and understanding the various factors that affect efficiency, businesses can identify areas for improvement. Implementing strategies to reduce losses and optimize processes leads to significant improvements in performance, reducing operational costs, and enhancing environmental sustainability. Remember that continuous monitoring and improvement are essential for maintaining high levels of machine efficiency over time.
Latest Posts
Latest Posts
-
1 Atm Pressure Is Equivalent To
May 09, 2025
-
C2h6 O2 Co2 H2o
May 09, 2025
-
Is 33 A Prime Number Or Composite
May 09, 2025
-
Which Of The Following Hormones Does Not Influence Blood Pressure
May 09, 2025
-
What Is The Main Product Of Photosynthesis
May 09, 2025
Related Post
Thank you for visiting our website which covers about How To Calculate Efficiency Of Machine . We hope the information provided has been useful to you. Feel free to contact us if you have any questions or need further assistance. See you next time and don't miss to bookmark.