Which Is A Limitation Of Scientific Management
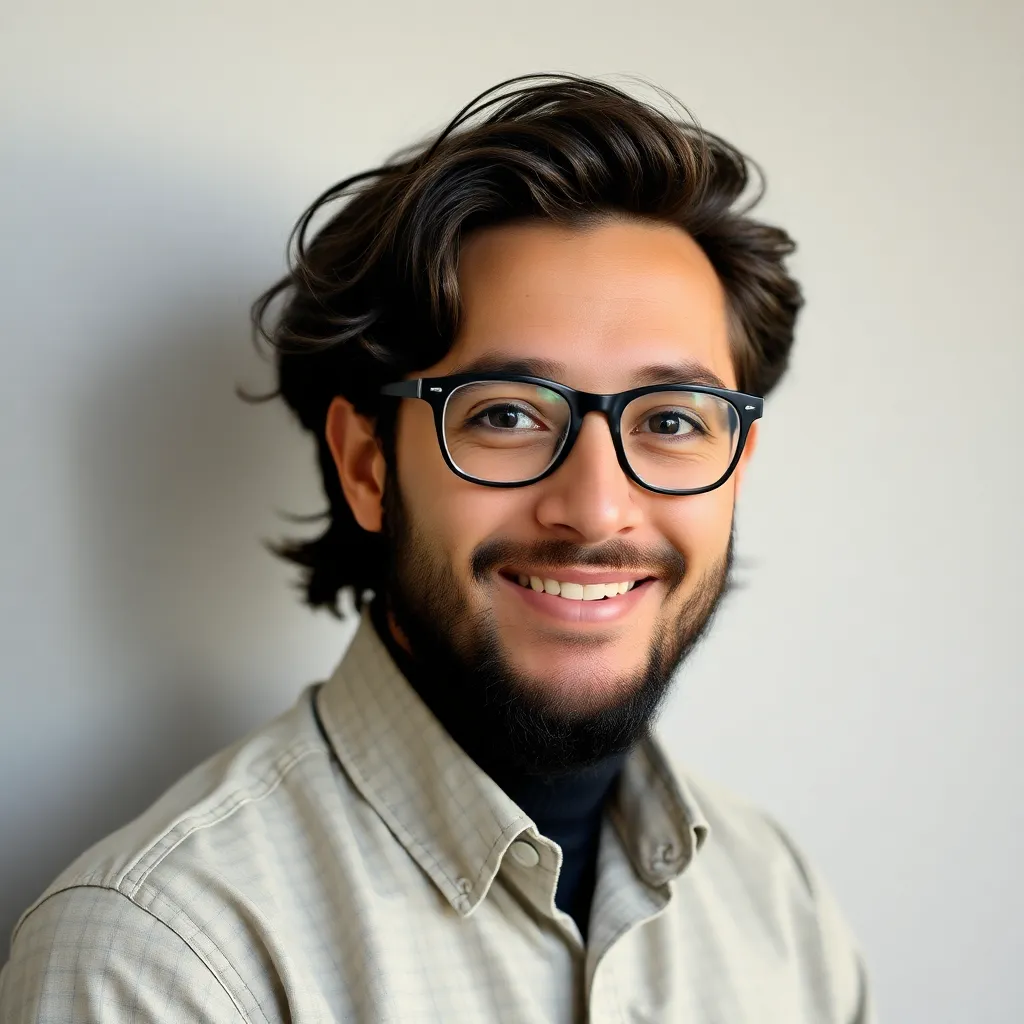
Juapaving
May 11, 2025 · 5 min read
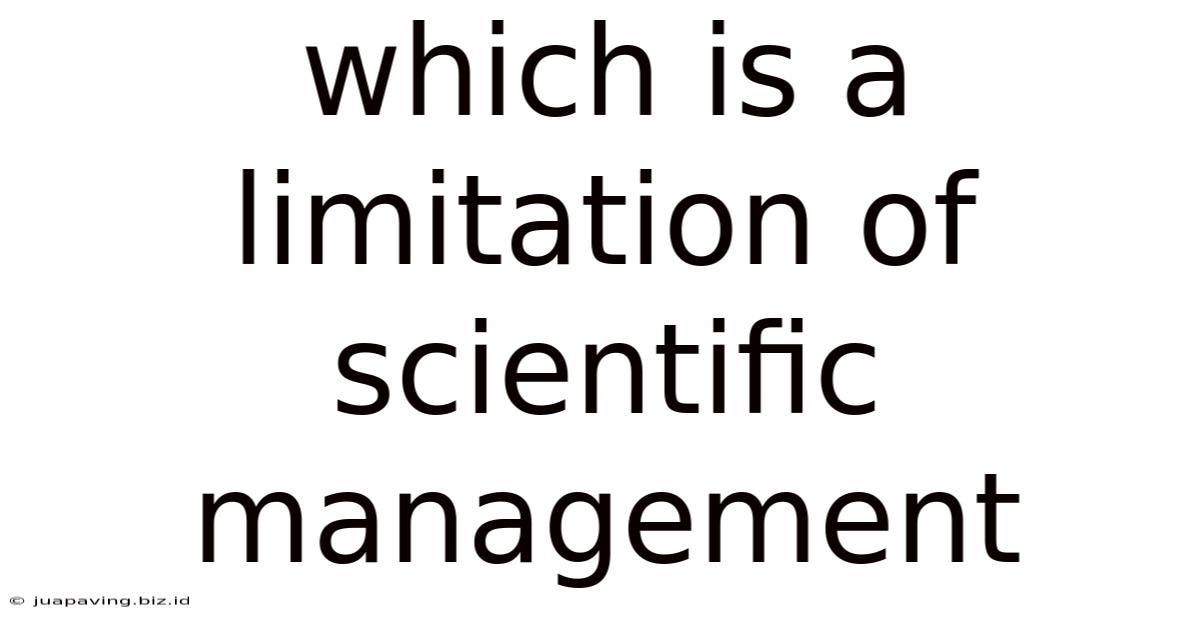
Table of Contents
The Limitations of Scientific Management: A Critical Analysis
Scientific management, also known as Taylorism, revolutionized industrial processes in the early 20th century. By emphasizing efficiency, standardization, and scientific methods, it dramatically increased productivity in many sectors. However, its inherent limitations have become increasingly apparent over time, leading to critiques and the development of more holistic management approaches. This article delves into the significant shortcomings of scientific management, examining its impact on workers, organizations, and the broader societal context.
Neglecting the Human Element: The Dehumanization of Work
One of the most significant criticisms of scientific management lies in its dehumanizing approach to labor. By focusing solely on maximizing output and efficiency, it often disregarded the psychological and social needs of workers. Taylor's methods, which involved breaking down complex tasks into smaller, repetitive components, led to:
1. Monotony and Boredom:
The repetitive nature of work under scientific management fostered monotony and boredom, leading to decreased job satisfaction and increased worker alienation. The lack of variety and challenge in tasks often resulted in reduced motivation and productivity in the long run, counteracting the initial gains in efficiency. Workers felt like cogs in a machine, their individual contributions and skills rendered insignificant.
2. Deskilling and Reduced Autonomy:
Scientific management often led to deskilling of the workforce. By standardizing tasks and meticulously defining procedures, the need for skilled workers diminished. This reduced workers' autonomy and control over their work, leading to feelings of powerlessness and resentment. The emphasis on following prescribed methods stifled creativity and initiative, hindering the potential for innovation and improvement.
3. Increased Worker Stress and Health Issues:
The pressure to meet stringent production quotas and adhere to rigid procedures often resulted in increased worker stress and health issues. Repetitive strain injuries, mental fatigue, and burnout became common problems associated with the highly structured and demanding work environment. The neglect of human well-being ultimately undermined the long-term sustainability of the system.
Overemphasis on Efficiency: Ignoring Broader Organizational Needs
While efficiency is undoubtedly crucial for organizational success, scientific management's overemphasis on it often came at the expense of other important factors:
1. Lack of Flexibility and Adaptability:
The rigid standardization and control inherent in scientific management made it difficult to adapt to changing circumstances. Unexpected events or shifts in market demand could disrupt the finely tuned system, leading to inefficiencies and decreased productivity. The lack of flexibility limited the organization's capacity to innovate and respond to dynamic environments.
2. Stifling Innovation and Creativity:
By prescribing precise methods and procedures, scientific management inadvertently stifled innovation and creativity. Workers were discouraged from suggesting improvements or experimenting with new approaches. This rigid adherence to established methods hindered the organization's ability to develop and implement new technologies or strategies, eventually leading to a competitive disadvantage.
3. Neglect of Communication and Collaboration:
Scientific management's focus on individual task specialization often led to poor communication and collaboration among workers. The lack of interaction and shared understanding between different departments or work teams hampered efficient workflows and created silos within the organization. This isolation undermined teamwork and prevented the synergistic benefits of collective problem-solving.
4. Limited Consideration of Quality:
The intense focus on quantity and speed often came at the expense of quality. The pressure to meet production targets might incentivize workers to cut corners or compromise on quality, leading to defective products or services. This resulted in customer dissatisfaction, increased costs associated with rework or repairs, and ultimately damaged the organization's reputation.
Social and Ethical Concerns: The Broader Impact of Taylorism
Beyond the organizational level, scientific management raised significant social and ethical concerns:
1. Increased Inequality:
Scientific management's emphasis on efficiency and specialization contributed to increased inequality between management and workers. Managers held greater power and control, while workers were reduced to performing repetitive, low-skill tasks with limited opportunities for advancement. This power imbalance led to social stratification and potentially exacerbated existing societal inequalities.
2. Alienation and Loss of Meaning:
The repetitive and dehumanizing nature of work under scientific management often resulted in worker alienation and a loss of meaning. Workers felt disconnected from the overall production process and lacked a sense of purpose or accomplishment in their work. This lack of engagement could lead to decreased morale, increased absenteeism, and higher employee turnover.
3. Ignoring External Factors:
Scientific management frequently failed to consider the broader societal context in which organizations operated. Factors like economic fluctuations, technological advancements, and social changes were often overlooked in the pursuit of maximizing efficiency within the factory walls. This narrow perspective limited the organization's ability to adapt and thrive in a dynamic and evolving environment.
Alternatives and Contemporary Approaches: Moving Beyond Taylorism
The limitations of scientific management have led to the development of more holistic and human-centered management approaches. These include:
- Human Relations Movement: This emphasizes the importance of social factors, employee motivation, and communication in improving productivity.
- Total Quality Management (TQM): This focuses on continuous improvement, customer satisfaction, and employee empowerment.
- Lean Manufacturing: This emphasizes efficiency, waste reduction, and continuous flow of work, but with a greater focus on employee involvement and respect.
- Agile methodologies: These promote flexibility, collaboration, and iterative development, particularly valuable in dynamic and uncertain environments.
These newer approaches acknowledge the importance of balancing efficiency with worker well-being, creativity, and organizational adaptability. They incorporate principles of empowerment, collaboration, and continuous improvement, thereby addressing many of the limitations of scientific management.
Conclusion: Learning from the Past, Shaping the Future
Scientific management, despite its historical significance and initial successes, suffers from inherent limitations related to its dehumanizing approach, overemphasis on efficiency, and neglect of broader organizational and societal factors. Its legacy serves as a valuable lesson, highlighting the importance of integrating human considerations and flexibility into management practices. Contemporary approaches to management strive to learn from the mistakes of the past, creating work environments that are both efficient and supportive of worker well-being, creativity, and overall organizational success. By understanding the limitations of scientific management, organizations can cultivate a more productive, fulfilling, and sustainable working environment for all. The future of management lies in embracing a holistic and human-centered perspective, one that recognizes the crucial interdependence of efficiency, innovation, and human flourishing.
Latest Posts
Latest Posts
-
The Lines On A Solubility Graph Indicate Where A Solution
May 12, 2025
-
What Is The Reciprocal Of 4 5
May 12, 2025
-
2 177 Rounded To The Nearest Hundredth
May 12, 2025
-
Is A Train Faster Than A Car
May 12, 2025
-
Name Of Polygon With 9 Sides
May 12, 2025
Related Post
Thank you for visiting our website which covers about Which Is A Limitation Of Scientific Management . We hope the information provided has been useful to you. Feel free to contact us if you have any questions or need further assistance. See you next time and don't miss to bookmark.