What Step Do You Take After The Decmat Is Complete
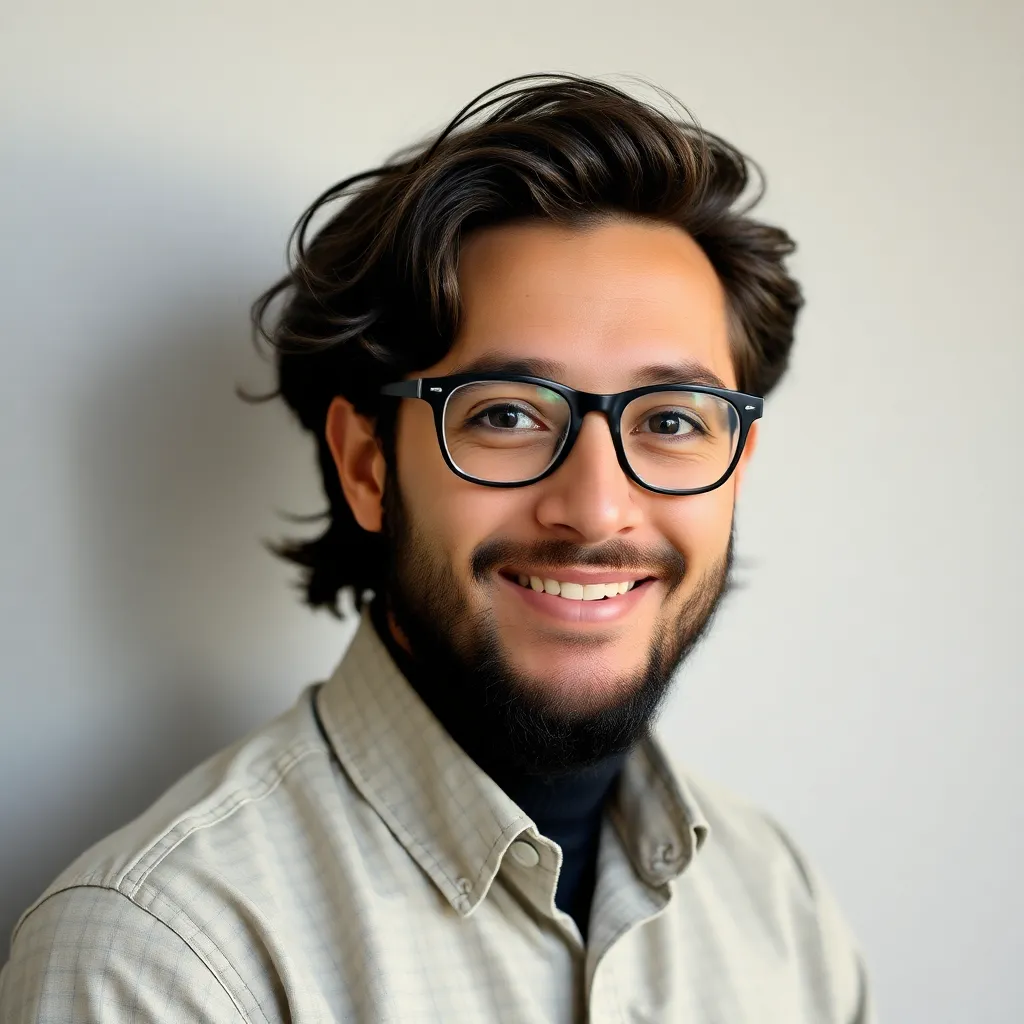
Juapaving
May 25, 2025 · 7 min read
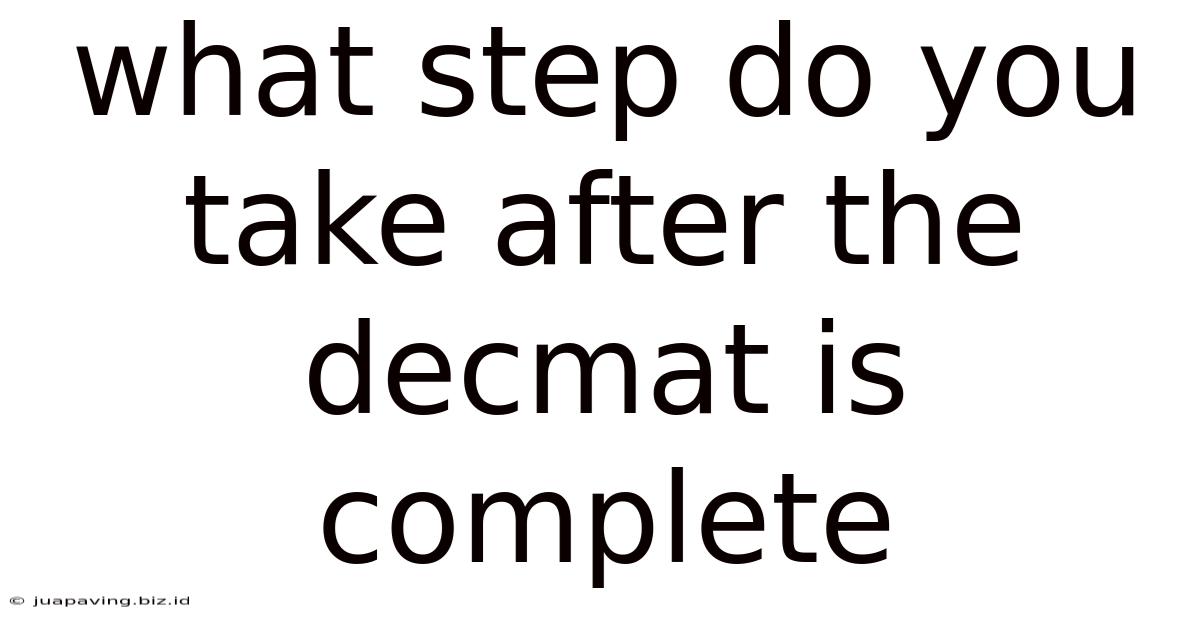
Table of Contents
What Steps Do You Take After the DECMAT is Complete?
The completion of a Design and Construction Management Attainment (DECMAT) marks a significant milestone in a construction project. It signifies the successful completion of the design phase and the transition into the construction phase. However, the work isn't over. Successfully navigating the post-DECMAT phase requires careful planning, meticulous execution, and proactive management. This comprehensive guide details the critical steps you must take after DECMAT completion to ensure a smooth and successful project delivery.
1. Formal Handover and Documentation Review
The first critical step is a formal handover of the approved design documents from the design team to the construction team. This handover shouldn't be a casual exchange; it necessitates a meticulous process:
1.1. Comprehensive Document Checklist:
- Complete Set of Drawings: Ensure all architectural, structural, MEP (Mechanical, Electrical, Plumbing), and other relevant drawings are complete, stamped, and approved. This includes all revisions and addenda.
- Specifications: Verify the completeness and accuracy of all specifications, ensuring they align perfectly with the approved drawings. Any ambiguities or discrepancies should be addressed before proceeding.
- Material Schedules: Review the material schedules to ensure all necessary materials are identified and readily available for procurement. This includes confirming lead times and potential supply chain risks.
- Cost Estimates: Re-examine the cost estimates, comparing them to the final approved budget. Identify any potential cost overruns and develop mitigation strategies.
- Contractor's Agreements: Ensure all relevant contracts with subcontractors and suppliers are finalized and legally sound. Clarify payment schedules and performance expectations.
- Permitting Documentation: Confirm that all necessary permits and approvals are obtained and ready for submission to the relevant authorities.
1.2. Design Review Meeting:
A formal design review meeting between the design team, construction team, and key stakeholders is crucial. This meeting serves to:
- Clarify Ambiguities: Address any outstanding questions or ambiguities within the design documents.
- Identify Potential Issues: Proactively identify potential constructability issues or design flaws that may arise during construction.
- Establish Communication Protocols: Establish clear communication channels and reporting procedures between all parties involved.
- Document Agreement: Prepare and sign a formal handover document acknowledging the completion of the design phase and the commencement of the construction phase.
2. Construction Planning and Sequencing
With the design finalized and handed over, the focus shifts to meticulous construction planning. This involves:
2.1. Detailed Construction Schedule:
Developing a detailed and realistic construction schedule is paramount. This schedule should include:
- Task Breakdown: Break down the entire construction process into smaller, manageable tasks.
- Sequencing: Determine the logical sequence of these tasks, identifying dependencies and critical paths.
- Resource Allocation: Assign resources (labor, equipment, materials) to each task, optimizing resource utilization.
- Timeline: Set realistic timelines for each task, considering potential delays and unforeseen circumstances.
- Milestone Tracking: Establish key milestones to track progress and identify potential deviations from the schedule.
2.2. Site Logistics and Management:
Effective site logistics are essential for a smooth construction process. This includes:
- Site Layout: Develop a detailed site layout plan, identifying the location of construction activities, material storage areas, and access points.
- Waste Management Plan: Establish a comprehensive waste management plan to comply with environmental regulations and minimize site impact.
- Safety Plan: Develop a thorough safety plan that addresses all potential hazards on the construction site. This should comply with all relevant safety regulations and standards.
- Communication Plan: Establish a robust communication plan to ensure effective communication among all stakeholders, including workers, subcontractors, and the client.
3. Procurement and Material Management
Efficient procurement and material management are critical for timely project completion. This phase involves:
3.1. Material Procurement:
- Supplier Selection: Select reliable suppliers based on price, quality, and delivery timelines.
- Order Placement: Place orders for all necessary materials, factoring in lead times and potential delays.
- Quality Control: Establish a quality control process to ensure that all materials meet the required specifications.
- Inventory Management: Implement an inventory management system to track the status of materials and prevent shortages.
3.2. Material Delivery and Handling:
- Scheduling Delivery: Coordinate material deliveries to minimize disruption on the construction site.
- Storage and Handling: Establish procedures for the safe storage and handling of materials to prevent damage or loss.
- Waste Minimization: Implement measures to minimize material waste during construction.
4. Construction Execution and Monitoring
The actual construction phase requires diligent oversight and management:
4.1. Daily Site Inspections:
Regular daily inspections are crucial for monitoring progress, identifying potential problems, and ensuring that the work is being done according to the plans and specifications. This includes:
- Quality Control Checks: Conduct regular quality control checks to ensure that the construction work meets the required standards.
- Safety Inspections: Conduct regular safety inspections to identify and mitigate potential safety hazards.
- Progress Monitoring: Track progress against the schedule and identify any potential delays.
- Documentation: Meticulously document all inspections, including photos and written reports.
4.2. Progress Reporting and Communication:
Regular progress reports should be prepared and distributed to all stakeholders. These reports should:
- Summarize Progress: Summarize the progress made on the project since the last report.
- Identify Issues: Highlight any issues or challenges that have arisen.
- Outline Solutions: Propose solutions for addressing the identified issues.
- Forecast Future Progress: Provide a forecast of the expected progress in the coming period.
5. Quality Control and Assurance
Maintaining rigorous quality control throughout the construction process is vital for delivering a high-quality finished product. This involves:
5.1. Regular Inspections and Testing:
Regular inspections and testing of materials and workmanship are essential to identify and rectify defects early on. This prevents costly rework later in the project.
5.2. Quality Assurance Procedures:
Establish robust quality assurance procedures to ensure that the entire construction process adheres to the highest quality standards. This might involve:
- Third-Party Inspections: Consider engaging third-party inspectors to provide an independent assessment of the construction quality.
- Documentation of Quality: Maintain comprehensive documentation of all quality control and assurance activities.
6. Risk Management and Mitigation
Proactive risk management is critical throughout the construction process. This involves:
6.1. Risk Identification and Assessment:
Identify potential risks that could impact the project's schedule, budget, or quality. This includes risks related to:
- Weather: Extreme weather conditions can cause significant delays and cost overruns.
- Materials: Supply chain disruptions or material defects can impact the schedule and budget.
- Labor: Labor shortages or strikes can cause delays.
- Regulatory Changes: Changes in building codes or regulations can require design modifications.
6.2. Risk Mitigation Strategies:
Develop mitigation strategies to address the identified risks. This might include:
- Contingency Planning: Develop contingency plans to address potential delays or cost overruns.
- Insurance: Secure appropriate insurance coverage to protect against unforeseen events.
- Early Warning Systems: Establish early warning systems to identify potential problems early on.
7. Change Management
Changes to the original design or scope of work are inevitable during a construction project. Effective change management is critical:
7.1. Change Order Process:
Establish a formal change order process to manage all changes to the original design or scope of work. This process should clearly define:
- Change Request Submission: How changes are requested and documented.
- Review and Approval: The process for reviewing and approving change requests.
- Cost and Schedule Impact: How the cost and schedule impact of changes are assessed.
- Documentation: How changes are documented and tracked.
7.2. Communication and Collaboration:
Maintain open communication and collaboration between all stakeholders to ensure that all parties are aware of and agree to any changes.
8. Project Closeout
The final phase involves the project closeout process:
8.1. Final Inspection and Handover:
Conduct a final inspection to ensure that the completed project meets the design specifications and all requirements. This includes a thorough walk-through with the client.
8.2. Documentation and As-Built Drawings:
Prepare and submit all necessary documentation, including as-built drawings, operation and maintenance manuals, and warranty information.
8.3. Financial Settlement:
Ensure that all outstanding payments are made and that all financial records are reconciled.
8.4. Project Lessons Learned:
Conduct a post-project review to identify lessons learned that can be applied to future projects. This is crucial for continuous improvement.
By meticulously following these steps after DECMAT completion, construction professionals can significantly enhance the likelihood of delivering successful, high-quality projects on time and within budget. Remember that proactive planning, effective communication, and rigorous monitoring are key to navigating the post-DECMAT phase successfully.
Latest Posts
Latest Posts
-
Main Themes Of The Great Gatsby
May 25, 2025
-
Fundamentals Of Anatomy And Physiology 11th Edition
May 25, 2025
-
Appendices Of The Lord Of The Rings
May 25, 2025
-
Acs Practice Exam Gen Chem 2 Pdf
May 25, 2025
-
Who Is Franz In The Count Of Monte Cristo
May 25, 2025
Related Post
Thank you for visiting our website which covers about What Step Do You Take After The Decmat Is Complete . We hope the information provided has been useful to you. Feel free to contact us if you have any questions or need further assistance. See you next time and don't miss to bookmark.