What Is The Purpose Of A Commutator
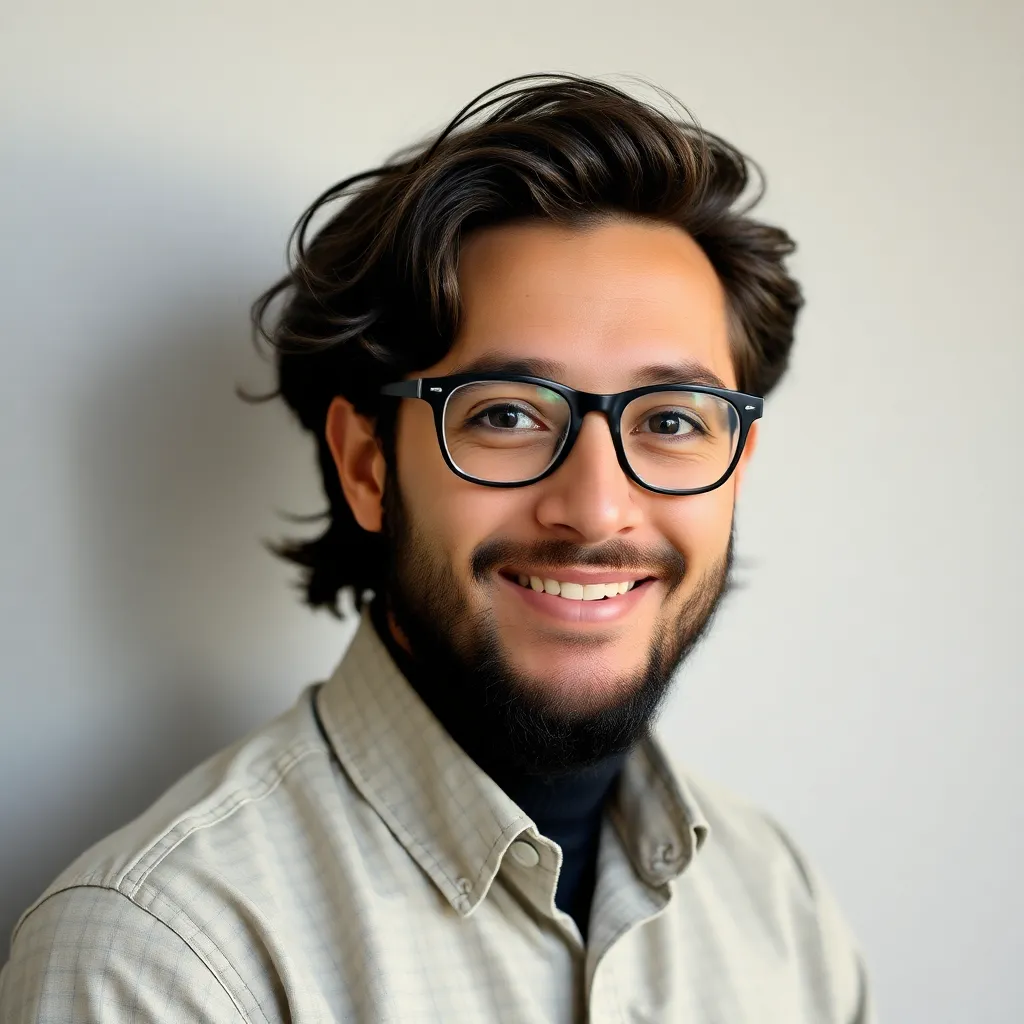
Juapaving
May 11, 2025 · 5 min read
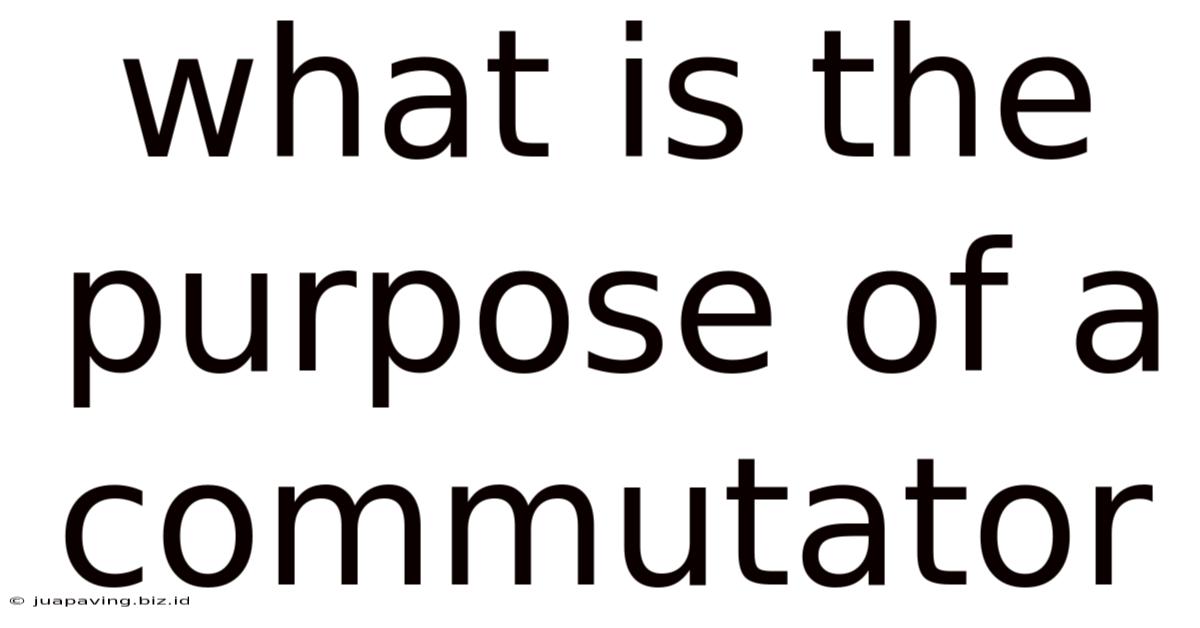
Table of Contents
What is the Purpose of a Commutator? A Deep Dive into DC Motor Functionality
The commutator, a seemingly simple component within DC motors, plays a crucial role in their operation. Understanding its purpose is key to grasping the fundamental principles behind these ubiquitous machines. This article delves deep into the intricacies of the commutator, explaining its function, construction, and significance in the broader context of DC motor technology. We'll explore its role in converting AC to DC, discuss common types, address troubleshooting, and even touch upon future trends in commutator design.
The Fundamental Role of the Commutator: Rectifying AC to DC
At the heart of a DC motor's operation lies the fundamental need to produce a unidirectional (DC) torque. However, the interaction between the magnetic field and the armature windings inherently generates an alternating current (AC). This is where the commutator steps in. Its primary purpose is to rectify this internally generated AC into a usable DC current, ensuring continuous rotation in one direction. This rectification process is crucial for maintaining consistent torque and preventing the motor from stalling or vibrating uncontrollably. Without a commutator, a DC motor would simply vibrate and fail to produce any significant rotational force.
The Commutator's Mechanism: Split Rings and Brushes
A commutator is essentially a segmented cylindrical ring made of copper segments insulated from each other. These segments are precisely attached to the ends of the armature windings. Carbon brushes, typically made of graphite or a carbon-graphite composite, press against the rotating commutator. These brushes maintain electrical contact with the rotating segments, forming a sliding electrical connection.
As the armature rotates, different commutator segments make contact with the brushes. This switching action effectively reverses the direction of current flow in the armature windings at precisely the right moments. This timed reversal ensures that the torque remains unidirectional, driving the motor in a single direction. This ingenious mechanism cleverly transforms the inherently alternating nature of the magnetic field interaction into a steady, unidirectional torque.
Understanding the Commutation Process: Timing is Everything
The precise timing of the commutation process is critical. If the commutation occurs too early or too late, the motor will experience arcing, sparking between the brushes and commutator segments. This arcing not only reduces the efficiency of the motor but also causes premature wear and tear on the commutator and brushes. Furthermore, excessive arcing can generate radio frequency interference (RFI), potentially causing problems with nearby electronic equipment.
Effective commutation relies on several factors including:
- Brush positioning: The brushes must be precisely positioned to ensure smooth transitions between commutator segments.
- Brush material: The brush material significantly impacts the contact resistance and wear characteristics. The choice of material is a careful balance between conductivity and wear resistance.
- Commutator surface condition: A smooth, clean commutator surface is essential for reliable commutation. Any imperfections or contamination can lead to arcing and poor motor performance.
Types of Commutators and their Applications
While the basic principle remains consistent, variations exist in commutator design based on specific motor applications and performance requirements.
Standard Commutators: The Workhorse
The most common type is the standard commutator, typically found in numerous small and medium-sized DC motors. This design prioritizes simplicity and cost-effectiveness. Its reliability makes it the go-to choice for a wide range of applications from toys and appliances to industrial machinery.
Lap Winding Commutators: High Current Applications
For high-current applications, lap wound commutators are often preferred. These designs utilize multiple parallel paths through the armature, effectively reducing the current flowing through each individual commutator segment. This arrangement enhances current carrying capacity and reduces the likelihood of overheating. This makes them suitable for heavy-duty applications where high power output is needed.
Wave Winding Commutators: High Speed Applications
Wave wound commutators, characterized by a more complex winding arrangement, are better suited for high-speed applications. They typically have fewer commutator segments than lap wound commutators, but maintain the required current capacity. Their design contributes to smoother operation at higher speeds.
Troubleshooting Commutator Issues: Identifying and Solving Problems
Various problems can arise with commutators, resulting in reduced motor performance or complete failure. Some common issues include:
- Arcing: Excessive sparking between brushes and commutator segments indicates poor commutation, potentially caused by misaligned brushes, worn brushes, dirty commutator surface, or a faulty winding.
- Wear: Wear on the commutator segments or brushes will eventually necessitate replacement. Uneven wear often points to issues like misalignment, poor brush quality, or a damaged commutator.
- Short circuits: A short circuit within the commutator segments will severely impair motor operation and might even damage other motor components.
- Open circuits: An open circuit within the commutator segments or the connections to the armature windings will prevent current flow and stop the motor.
Troubleshooting usually involves visual inspection, checking for continuity using a multimeter, and cleaning the commutator surface. Advanced troubleshooting may require more specialized tools and expertise.
Future Trends in Commutator Technology
While brushless DC motors are becoming increasingly popular, the commutator remains an essential part of many DC motor designs. Ongoing research and development focus on:
- Improved brush materials: Research into new materials with enhanced wear resistance, conductivity, and lower friction is constantly underway. This contributes to longer lifespan and improved efficiency.
- Advanced commutator machining techniques: Precision machining techniques are vital for achieving smoother commutator surfaces and reducing arcing.
- Improved brush-commutator interface: Better understanding of the tribological aspects of the brush-commutator interface can lead to minimized wear and enhanced reliability.
Conclusion: The Commutator's Enduring Importance
The commutator, despite its relatively simple design, plays a crucial and irreplaceable role in DC motor operation. Its ability to rectify the internally generated AC into usable DC power underpins the functionality of these essential machines. While advancements in brushless motor technology are changing the landscape of electrical drives, the commutator continues to serve as a vital component in many applications, proving its enduring importance. Its intricate design, coupled with the ongoing efforts to improve its performance and reliability, ensures that the commutator will remain a significant element in electrical engineering for the foreseeable future. A thorough understanding of its function, construction, and potential problems is critical for anyone working with DC motors.
Latest Posts
Latest Posts
-
What Is The Unit For Temperature In The Metric System
May 13, 2025
-
Lines Of Symmetry In A Regular Hexagon
May 13, 2025
-
How Many Atp Produced In Fermentation
May 13, 2025
-
Can A Triangle Have Two Right Angles
May 13, 2025
-
What Is The Lowest Common Multiple Of 8 And 24
May 13, 2025
Related Post
Thank you for visiting our website which covers about What Is The Purpose Of A Commutator . We hope the information provided has been useful to you. Feel free to contact us if you have any questions or need further assistance. See you next time and don't miss to bookmark.