What Is The Function Of Commutator
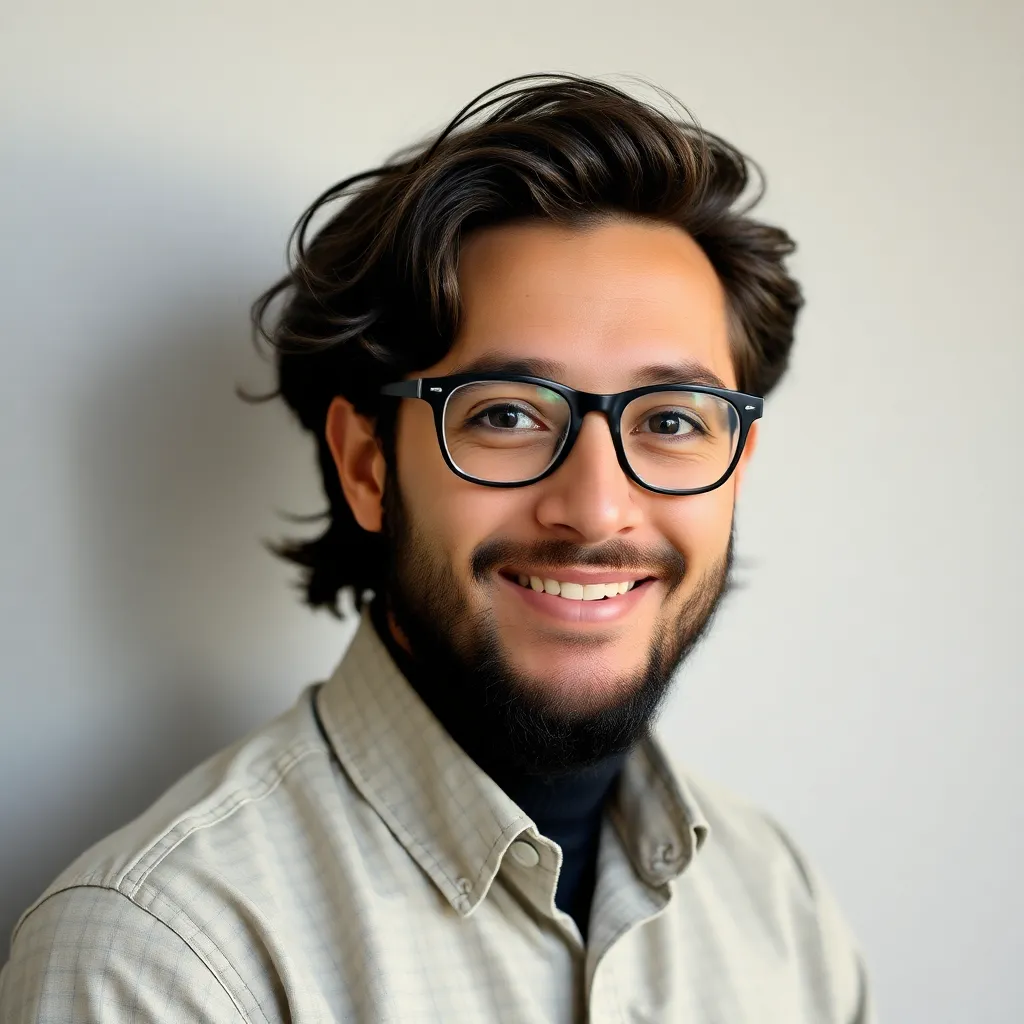
Juapaving
May 12, 2025 · 6 min read
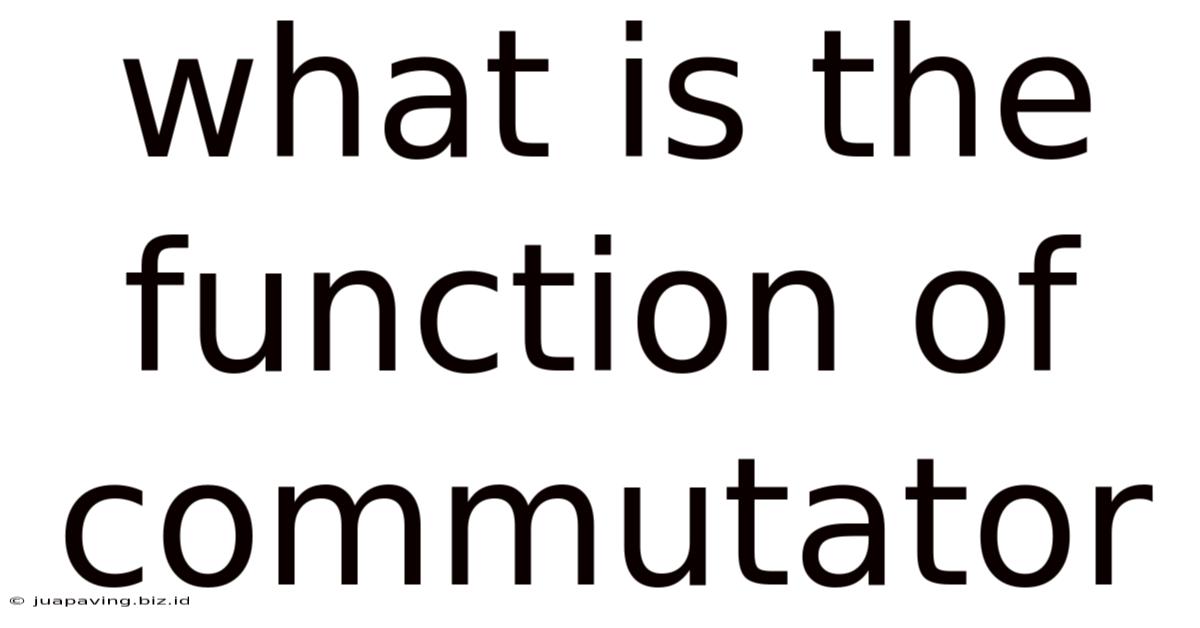
Table of Contents
What is the Function of a Commutator? A Deep Dive into DC Motor Operation
The commutator, a seemingly simple component, plays a critical role in the operation of direct current (DC) motors. Without it, these motors wouldn't function. Understanding its function requires exploring the underlying principles of DC motor operation and the ingenious way the commutator facilitates the continuous rotation of the armature. This article will delve into the intricacies of the commutator, explaining its function, construction, and importance in the broader context of electrical engineering.
Understanding the Basics: DC Motor Principles
Before diving into the commutator's function, it's essential to grasp the fundamental principles governing DC motor operation. A DC motor converts electrical energy into mechanical energy through the interaction of magnetic fields. The core components include:
- Stator: The stationary part of the motor, containing the field magnets that produce a constant magnetic field. In some designs, electromagnets are used instead of permanent magnets.
- Rotor (Armature): The rotating part of the motor, consisting of a coil of wire wound around a soft iron core. This coil, when energized, becomes an electromagnet.
- Commutator: The crucial component that facilitates the continuous rotation of the rotor. We'll examine this in detail later.
- Brushes: Conducting elements that make electrical contact with the commutator, supplying current to the rotor windings.
The principle of operation relies on the interaction between the magnetic fields of the stator and rotor. When current flows through the rotor coil, it creates a magnetic field. The interaction of this magnetic field with the stator's field produces a torque, causing the rotor to rotate.
The Commutator: The Heart of DC Motor Rotation
The commutator is a cylindrical assembly of segmented copper conductors, insulated from each other. These segments are arranged around the rotor shaft and are connected to the ends of the rotor windings. The brushes, typically made of carbon, press against the commutator's surface, providing the electrical connection between the external power source and the rotor windings.
The primary function of the commutator is to reverse the direction of current flow in the rotor windings at precisely the right moment. This is essential for maintaining continuous rotation. Without this switching action, the rotor would simply oscillate back and forth instead of rotating smoothly.
Let's examine this process step-by-step:
-
Initial Current Flow: When current flows from the power source through the brushes and into a segment of the commutator, it energizes a specific coil within the rotor. This creates a magnetic field in the rotor that interacts with the stator's magnetic field, producing torque and causing the rotor to begin rotating.
-
Commutation: As the rotor turns, the commutator segments rotate as well. At a specific point, the brushes transition from one commutator segment to the next. This transition is the commutation event.
-
Current Reversal: The commutation event effectively reverses the direction of current flow in the rotor windings. This is crucial because without the reversal, the torque would change direction, halting the rotation.
-
Continuous Rotation: By reversing the current at the precise moment, the commutator ensures that the torque always acts in the same direction, thus enabling continuous rotation of the rotor. This precise timing is crucial; even a slight misalignment can lead to inefficient operation or motor failure.
The Role of Brushes in the Commutation Process
The brushes play a vital supporting role in the commutation process. Their primary functions are:
-
Electrical Connection: They provide the electrical connection between the external power source and the rotating commutator. This connection must be reliable and maintain good contact to avoid arcing or sparking.
-
Current Transfer: They transfer the current from the power source to the rotor windings via the commutator segments. The smooth transfer of current is essential for efficient operation and to prevent excessive wear on the brushes and commutator.
-
Commutation Control: The position of the brushes is crucial. Their placement determines the timing of the current reversal in the rotor windings. Precise brush placement is vital for optimal motor performance and minimizing sparking.
Commutator Construction and Materials
The commutator is typically constructed from high-conductivity copper segments, insulated from each other by mica insulation. The mica provides the necessary insulation between the segments, preventing short circuits. The choice of materials is critical:
- Copper: Offers high electrical conductivity, ensuring minimal resistance and efficient current flow.
- Mica: Provides excellent insulation, preventing short circuits between the commutator segments. Its high thermal resistance is important because heat is generated during commutation.
Common Issues and Maintenance
Over time, commutators can experience wear and tear, leading to various issues:
- Sparking: Excessive sparking indicates poor brush contact or commutator wear, leading to reduced efficiency and potential damage.
- Pitting: Small pits or grooves can develop on the commutator surface, disrupting the smooth current transfer and causing increased sparking.
- Short Circuits: Damage to the mica insulation can lead to short circuits between the commutator segments, resulting in motor failure.
Regular maintenance, including brush replacement and commutator cleaning or resurfacing, is crucial to extend the life of the motor and maintain its performance.
Comparing Commutator Motors with Brushless Motors
While commutator motors are widely used, they are not without limitations. The presence of brushes introduces several drawbacks, including:
- Mechanical Wear: The continuous rubbing of the brushes against the commutator leads to mechanical wear and requires periodic maintenance.
- Sparking: The commutation process can produce sparking, which can be a source of noise, radio frequency interference (RFI), and potential fire hazards.
- Limited Speed: Commutator motors generally have lower speed capabilities compared to brushless motors.
Brushless DC motors, on the other hand, eliminate the brushes and commutator, resulting in increased efficiency, longer lifespan, and quieter operation. However, they are generally more complex and expensive.
Commutator's Importance in Specific Applications
The commutator's specific function makes it essential in various applications where reliable DC motor operation is crucial:
- Automotive Applications: In older vehicles, DC motors with commutators were frequently used for starters, window motors, and other applications.
- Industrial Machinery: DC motors with commutators are utilized in various industrial machinery applications requiring precise speed control and torque.
- Robotics: While less common now than brushless motors, commutator DC motors still find applications in some robotic systems.
- Hand Tools: Many hand-held power tools rely on DC motors with commutators.
Conclusion: The Enduring Relevance of the Commutator
Despite the rise of brushless DC motors, the commutator remains a relevant and important component in many electrical machines. Its ingenious design and ability to effectively switch current direction in the rotor windings continue to make it an essential part of various DC motor applications. Understanding the function, construction, and maintenance of the commutator is fundamental for anyone working with DC motors. This knowledge allows for efficient operation, troubleshooting, and maintaining these vital components within electrical systems. While technology advances, the underlying principles of the commutator and its role in converting electrical energy into mechanical energy remain a testament to fundamental electrical engineering principles.
Latest Posts
Latest Posts
-
Number In Words From 1 To 100
May 14, 2025
-
What Is 96 Inches In Feet
May 14, 2025
-
What Percentage Is 35 Out Of 40
May 14, 2025
-
Electricity Is Measured In What Unit
May 14, 2025
-
Is A Pencil A Conductor Or Insulator
May 14, 2025
Related Post
Thank you for visiting our website which covers about What Is The Function Of Commutator . We hope the information provided has been useful to you. Feel free to contact us if you have any questions or need further assistance. See you next time and don't miss to bookmark.