What Is The Function Of A Commutator
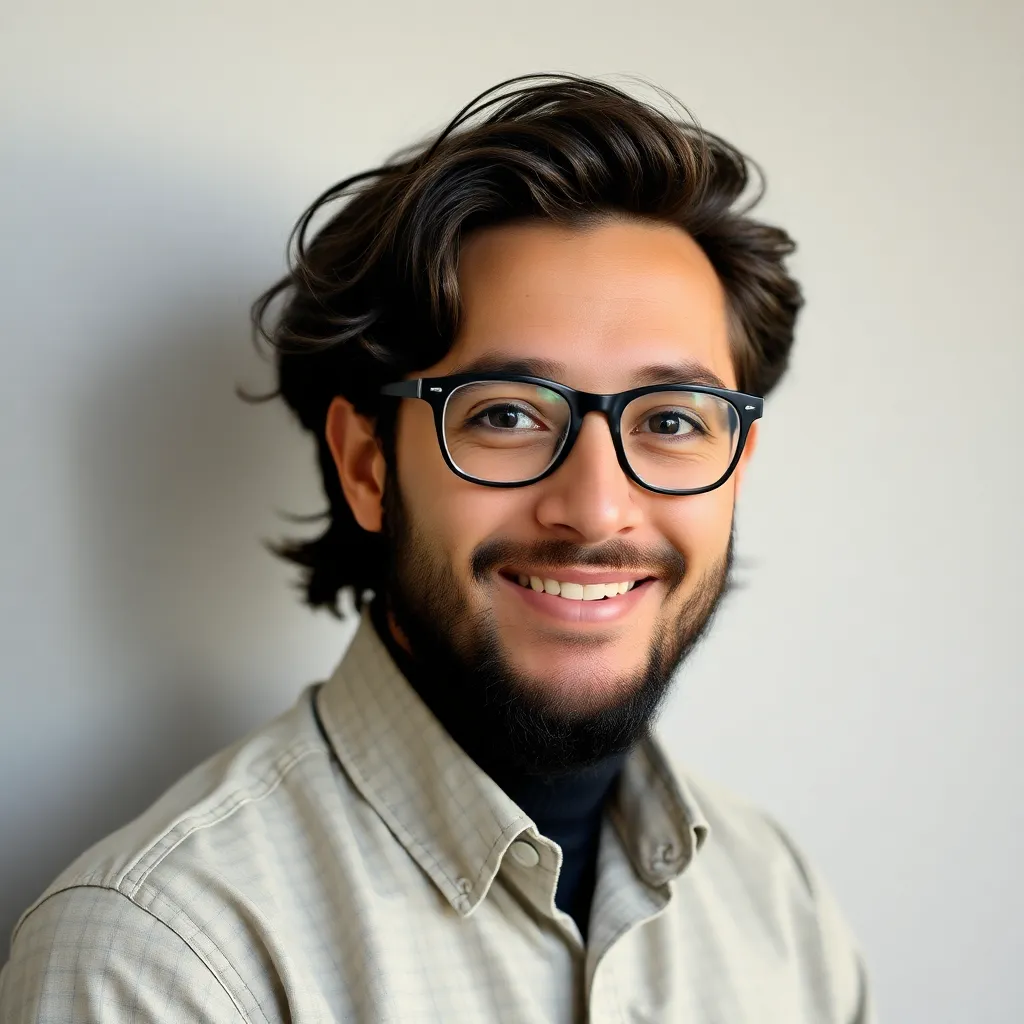
Juapaving
May 09, 2025 · 6 min read
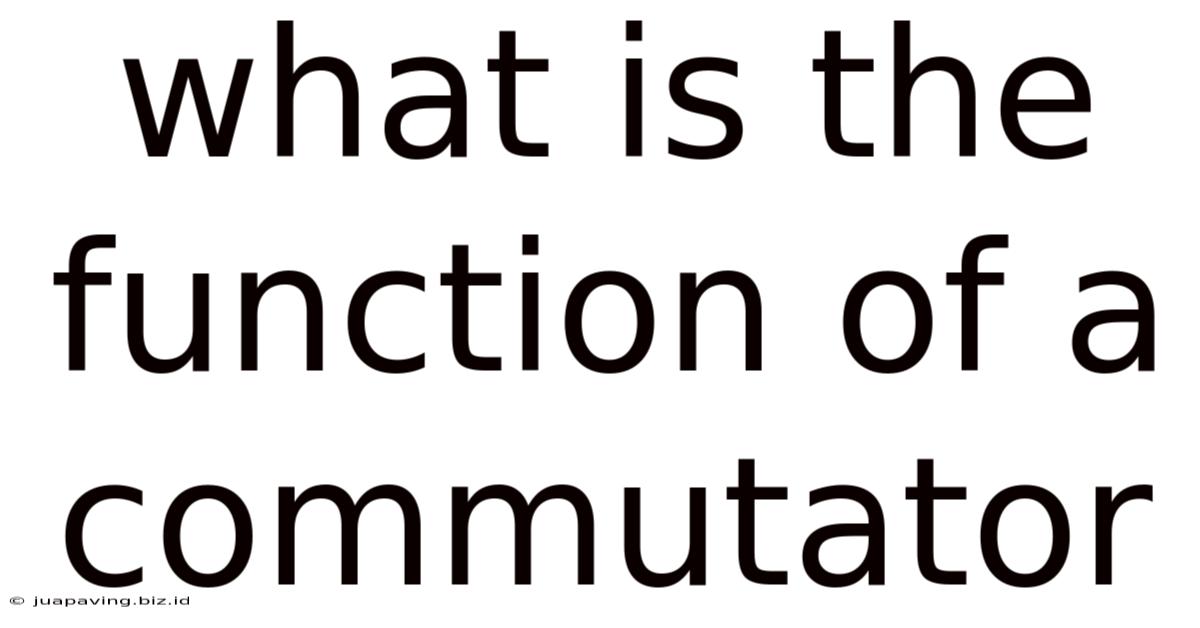
Table of Contents
What is the Function of a Commutator? A Deep Dive into DC Motor Operation
The humble commutator, a seemingly simple cylindrical component, plays a crucial role in the operation of direct current (DC) motors. Without it, these motors – ubiquitous in everything from power tools to electric vehicles – wouldn't function. This article will delve into the intricacies of the commutator, exploring its function, construction, and significance in the broader context of DC motor technology. We'll unravel its mechanism, discuss its importance in converting electrical energy into mechanical energy, and examine potential issues and maintenance considerations.
Understanding the Role of the Commutator in DC Motors
The fundamental function of a commutator in a DC motor is to mechanically rectify the alternating current (AC) generated within the motor's armature into a unidirectional, direct current (DC). This seemingly simple task is critical to the continuous rotation of the motor shaft.
Let's break this down:
-
AC Generation: When a current-carrying conductor moves within a magnetic field, a voltage is induced (Faraday's Law of Induction). In a DC motor, the armature windings (the rotating part) act as these conductors. As the armature rotates, the current flowing through the windings interacts with the magnetic field of the stator (the stationary part), generating an alternating current within the armature coils. This AC is inherently bidirectional, meaning the current direction reverses periodically.
-
Mechanical Rectification: This is where the commutator steps in. It's a cylindrical component segmented into multiple insulated copper segments, each connected to a coil in the armature winding. These segments are arranged in a precise manner to switch the direction of the current in the external circuit at the precise moment when the direction of the induced voltage changes in the armature coils. This switching ensures that the current always flows in the same direction through the external circuit, resulting in a unidirectional torque and continuous rotation.
-
Continuous Rotation: By cleverly switching the current direction in the armature windings, the commutator maintains the unidirectional torque required for sustained rotation. Without the commutator, the torque would fluctuate and reverse, causing the motor to vibrate violently and fail to rotate consistently.
Construction and Components of a Commutator
The commutator itself is a relatively simple, yet precisely engineered, device. It is typically constructed from several key components:
-
Copper Segments: These are the heart of the commutator. These segments, usually made of high-conductivity copper, are individually insulated from each other by mica insulation. The number of segments corresponds to the number of coils in the armature winding.
-
Mica Insulation: This is a crucial component. It provides the electrical insulation between adjacent copper segments, preventing short circuits. The quality and integrity of the mica insulation are critical to the commutator's reliability. Different types of mica are used depending on the application and required performance characteristics.
-
Commutator Shaft: The copper segments are rigidly mounted onto a cylindrical shaft, which is mechanically connected to the armature shaft. This ensures that the commutator rotates synchronously with the armature.
-
Commutator Riser: These are often used to help with the connection of the commutator to the wiring.
The Commutator's Interaction with Brushes
The commutator doesn't function in isolation. It interacts closely with carbon brushes, which are spring-loaded and maintain contact with the rotating commutator segments. These brushes provide the electrical connection between the commutator and the external circuit. As the commutator rotates, the brushes make and break contact with different segments, effectively switching the current direction in the armature windings.
The precise timing of this switching, determined by the commutator's segment arrangement and the brush placement, is essential for smooth, efficient motor operation. If the timing is off, the motor will likely experience sparking, reduced efficiency, and premature wear.
Advantages and Disadvantages of Commutators
While commutators are indispensable in many DC motors, they also present certain advantages and disadvantages:
Advantages:
- Simple and Relatively Inexpensive: Compared to other rectification methods, commutators are relatively simple and inexpensive to manufacture.
- Robust and Reliable: With proper maintenance, commutators can be highly reliable, providing long service lives.
- Efficient Energy Conversion: Commutators achieve high efficiency in converting electrical energy into mechanical energy.
Disadvantages:
- Mechanical Wear and Tear: The constant rubbing of the brushes against the commutator segments leads to mechanical wear. This requires periodic maintenance, including brush replacement and commutator resurfacing.
- Sparking: Sparking can occur due to various factors, including poor brush contact, worn commutator segments, or high currents. Sparking reduces efficiency, generates heat, and can cause radio-frequency interference (RFI).
- Limited Speed: The mechanical nature of the commutator limits the maximum rotational speed achievable. Higher speeds often lead to increased sparking and wear.
- Maintenance Requirements: Commutators require regular maintenance to ensure optimal performance and longevity.
Troubleshooting Commutator Issues
Common problems associated with commutators include:
- Excessive Sparking: This can indicate worn brushes, a rough commutator surface, or incorrect brush placement.
- Poor Motor Performance: Reduced power output or inconsistent rotation can result from damaged commutator segments or insulation breakdown.
- Noise and Vibration: These often point towards worn brushes or a rough commutator surface.
- Overheating: Excessive heat can be a sign of high current flow, poor brush contact, or damaged insulation.
Addressing these issues usually involves replacing worn brushes, resurfacing or replacing the commutator itself, and ensuring proper brush alignment and contact pressure.
Modern Alternatives and the Future of Commutators
While commutators remain prevalent in many applications, particularly those requiring high torque at low speeds, modern technologies offer alternatives:
-
Brushless DC motors (BLDC): These motors use electronic commutation instead of mechanical commutation, eliminating the need for brushes and commutators. BLDC motors offer superior efficiency, longer lifespan, and higher speeds. However, they generally come at a higher cost and may require more sophisticated control electronics.
-
Other motor types: AC motors, stepper motors, and servo motors also provide alternatives to traditional brushed DC motors and their inherent reliance on commutators.
The future of commutators depends on the specific application and the trade-offs between cost, performance, and maintenance requirements. While they may eventually be replaced in many high-performance applications, commutators will likely remain important components in low-cost, robust DC motors for the foreseeable future.
Conclusion: The Enduring Importance of the Commutator
The commutator, despite its seemingly simple design, remains a critical component in many DC motors. Its ability to mechanically rectify the alternating current generated within the armature into a unidirectional current is fundamental to the motor's operation. Understanding its function, construction, and potential issues is essential for anyone working with DC motors, whether for maintenance, repair, or design. While modern alternatives are emerging, the commutator's enduring importance in certain applications underscores its continuing role in the world of electrical engineering. Its reliability, simplicity, and cost-effectiveness ensure that the commutator will continue to serve as a workhorse component in countless devices for years to come.
Latest Posts
Latest Posts
-
Compare And Contrast A Food Chain And Food Web
May 09, 2025
-
What Are The Elements In Baking Soda
May 09, 2025
-
How Many Nm In One M
May 09, 2025
-
Figure With Two Lines Of Symmetry
May 09, 2025
-
Is Glass A Good Conductor Of Electricity
May 09, 2025
Related Post
Thank you for visiting our website which covers about What Is The Function Of A Commutator . We hope the information provided has been useful to you. Feel free to contact us if you have any questions or need further assistance. See you next time and don't miss to bookmark.