What Is The Difference Between Ac And Dc Electric Motors
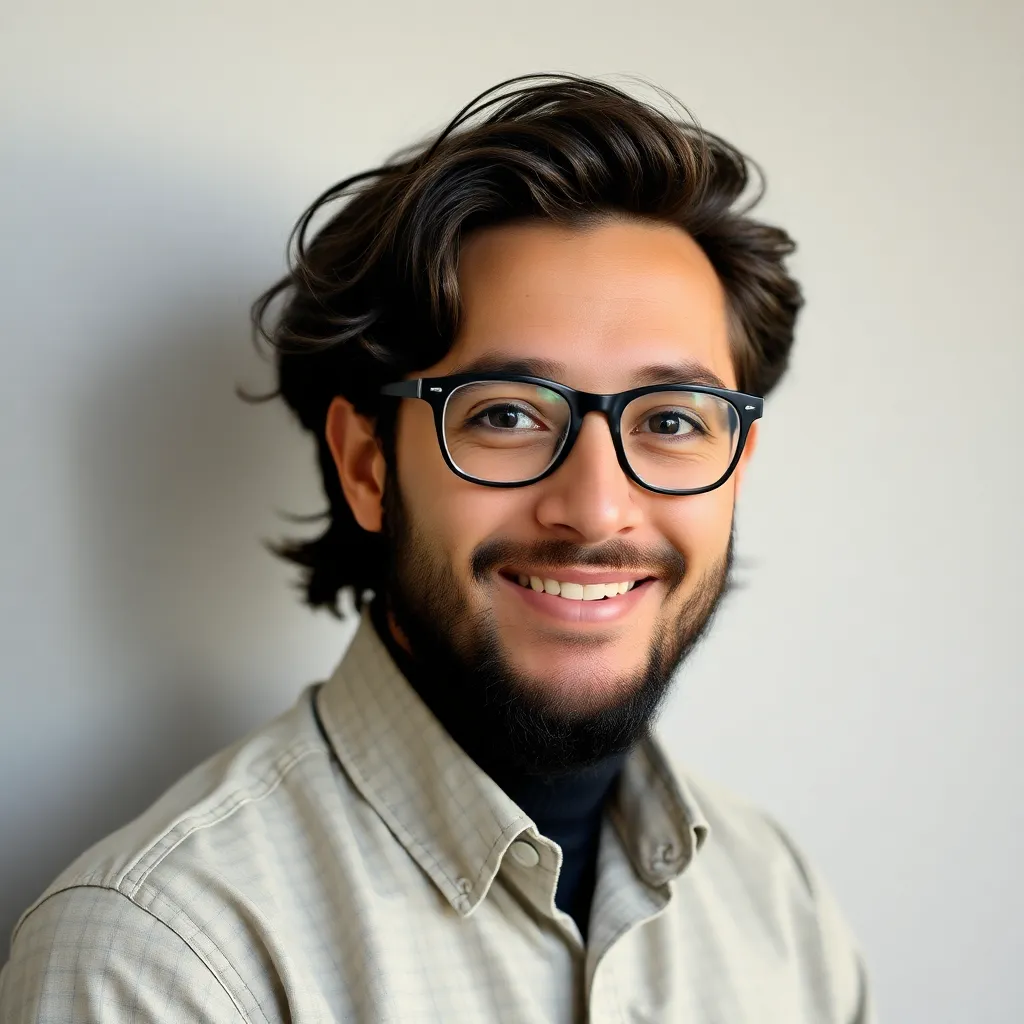
Juapaving
May 10, 2025 · 7 min read
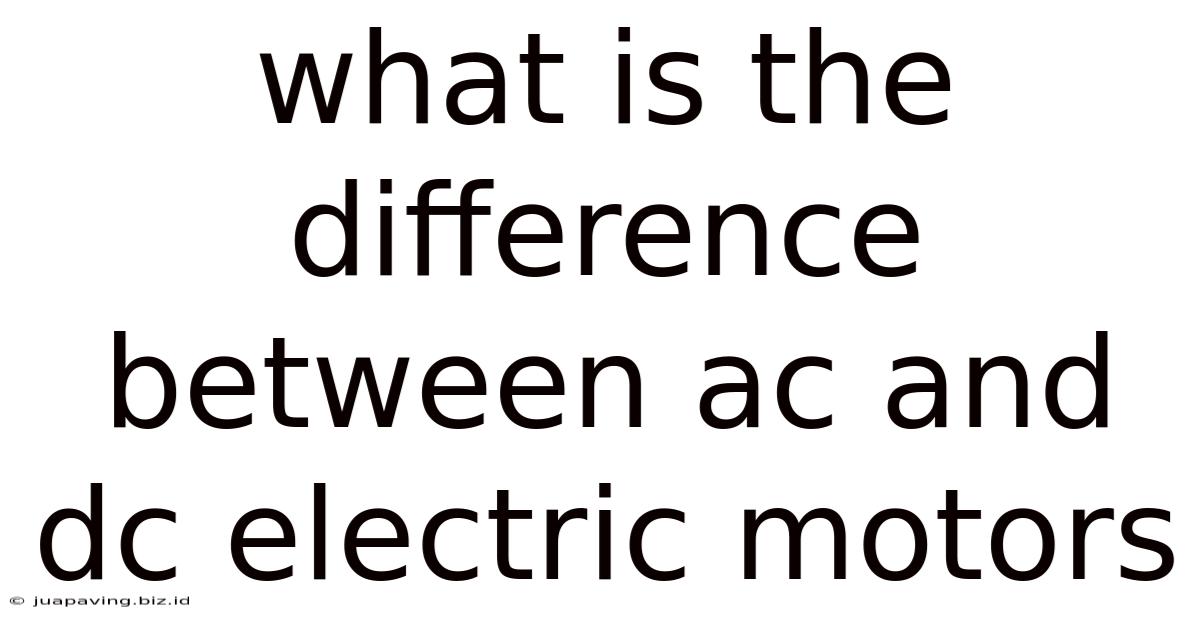
Table of Contents
AC vs. DC Electric Motors: A Comprehensive Comparison
Electric motors are the workhorses of modern industry and everyday life, powering everything from industrial machinery to household appliances. Understanding the fundamental differences between alternating current (AC) and direct current (DC) motors is crucial for selecting the right motor for a specific application. This comprehensive guide delves deep into the distinctions between AC and DC motors, covering their operating principles, advantages, disadvantages, and typical applications.
Understanding AC and DC Power
Before diving into the motors themselves, let's clarify the difference between AC and DC electricity.
AC (Alternating Current)
AC electricity is characterized by its periodic reversal of current direction. The voltage and current fluctuate sinusoidally, meaning they rise to a peak, fall to zero, reverse polarity, rise to a negative peak, and return to zero, repeatedly. This cyclical pattern is defined by its frequency, typically 50 Hz or 60 Hz depending on geographical location. The advantage of AC is its ease of transmission over long distances with minimal energy loss.
DC (Direct Current)
DC electricity, on the other hand, flows in one consistent direction. The voltage and current maintain a constant polarity, although the magnitude may vary. DC is often generated by batteries or rectified from AC power using devices like rectifiers. While easier to control and manage speed, DC power transmission over long distances is less efficient than AC due to higher energy losses.
AC Motor Types and Operating Principles
Several types of AC motors exist, each with its own characteristics. The most common are:
1. Induction Motors (Asynchronous Motors)
-
Operating Principle: Induction motors operate on the principle of electromagnetic induction. A rotating magnetic field is created in the stator (stationary part) by supplying AC power to its windings. This rotating field induces currents in the rotor (rotating part), creating its own magnetic field. The interaction between these two magnetic fields produces torque, causing the rotor to rotate. Induction motors are further categorized into squirrel-cage and wound-rotor motors, based on the rotor construction.
-
Advantages: Simple, robust construction, low maintenance, high efficiency, and relatively low cost.
-
Disadvantages: Speed control is more complex, and starting torque can be lower compared to some DC motors.
-
Applications: Fans, pumps, compressors, conveyors, and many other industrial applications.
2. Synchronous Motors
-
Operating Principle: Synchronous motors are characterized by their synchronous speed, meaning the rotor rotates at the same speed as the rotating magnetic field in the stator. This requires an external source to initially bring the rotor up to speed, often through a separate starting mechanism. They often use permanent magnets or DC excitation to the rotor.
-
Advantages: High efficiency, precise speed control at constant loads, and high power factor.
-
Disadvantages: More complex construction, and higher cost compared to induction motors. They are not self-starting and require special starting mechanisms.
-
Applications: Clocks, high-precision machinery, and applications requiring constant speed.
3. Stepper Motors
-
Operating Principle: Stepper motors move in discrete steps rather than continuous rotation. They are controlled by a series of pulses, with each pulse causing the rotor to rotate a specific angle.
-
Advantages: Precise positioning and control, high torque at low speeds, and simple control circuitry.
-
Disadvantages: Limited speed range, and potential for resonance vibrations at higher speeds.
-
Applications: Printers, CNC machines, robotics, and other applications requiring precise positioning.
4. Servomotors
-
Operating Principle: Servomotors are closed-loop control systems that use feedback to maintain precise speed and position. They often integrate a position sensor to continually adjust their output. They are typically AC motors, but DC servomotors also exist.
-
Advantages: High precision, accurate speed and position control, high responsiveness.
-
Disadvantages: Complex control systems, higher cost, and increased complexity compared to simpler AC motors.
-
Applications: Robotics, automation, precise positioning systems, and other high-precision control applications.
DC Motor Types and Operating Principles
Several types of DC motors are also commonly used, each with unique characteristics:
1. Permanent Magnet DC Motors (PMDC)
-
Operating Principle: PMDC motors use permanent magnets in the stator to create the magnetic field. The current flowing through the rotor windings interacts with this magnetic field to generate torque. Commutators and brushes reverse the current direction in the rotor windings to ensure continuous rotation.
-
Advantages: Simple construction, high starting torque, and good speed control.
-
Disadvantages: Relatively low efficiency compared to some AC motors, brush wear, and maintenance requirements.
-
Applications: Toys, small appliances, hand tools, and low-power applications.
2. Series Wound DC Motors
-
Operating Principle: The field winding is connected in series with the armature winding. This configuration produces high starting torque and speed that changes drastically depending on the load.
-
Advantages: High starting torque, and varying speed.
-
Disadvantages: Can be difficult to control speed, and significant speed variation with load.
-
Applications: Electric vehicles, electric trains, and other high-torque applications where speed control isn’t as critical.
3. Shunt Wound DC Motors
-
Operating Principle: The field winding is connected in parallel (shunt) with the armature winding. This allows for better speed control and constant speed despite variations in load.
-
Advantages: Better speed regulation, and improved speed control compared to series wound motors.
-
Disadvantages: Lower starting torque than series wound motors, and higher cost.
-
Applications: Constant speed applications where load variations are expected (fans, pumps).
4. Compound Wound DC Motors
-
Operating Principle: Combines features of both series and shunt wound motors by having both series and shunt field windings.
-
Advantages: High starting torque with good speed regulation, balance between the advantages of series and shunt wound motors.
-
Disadvantages: More complex design, and higher cost.
-
Applications: Elevators, cranes, hoists, and applications requiring high starting torque and good speed regulation.
AC vs. DC Motor: A Comparative Table
Feature | AC Motor | DC Motor |
---|---|---|
Power Source | AC Power Supply | DC Power Supply |
Construction | Generally simpler, more robust | Can be more complex, depending on type |
Starting Torque | Generally lower for induction motors | Generally higher, especially PMDC |
Speed Control | More complex, often requires VFDs | Simpler, often achieved directly |
Efficiency | Generally higher at rated speed | Can be lower, depending on type |
Maintenance | Generally lower | Can be higher due to brush wear |
Cost | Generally lower for induction motors | Can be higher, depending on type |
Applications | Industrial applications, pumps, fans | Robotics, automotive, appliances, etc. |
Choosing the Right Motor: Key Considerations
Selecting the appropriate motor type depends heavily on the specific application requirements. Several factors need to be considered:
- Power Requirements: Determine the required power output to drive the load.
- Speed Requirements: Specify the needed operating speed and whether speed control is necessary.
- Torque Requirements: Determine the torque needed to overcome the load inertia and friction.
- Duty Cycle: Define the motor's operating time and rest periods.
- Environmental Conditions: Consider factors like temperature, humidity, and dust.
- Cost and Maintenance: Balance initial cost with maintenance needs and lifespan.
- Efficiency: Optimize energy consumption, especially in continuous operation.
- Size and Weight: Choose a motor of appropriate dimensions and weight for the application.
Conclusion: AC and DC Motors in the Modern World
Both AC and DC motors play crucial roles in powering countless applications across various industries. AC motors, particularly induction motors, dominate industrial settings due to their robust design, high efficiency, and low cost. DC motors, especially PMDC motors, find widespread use in applications requiring precise speed control and high starting torque. Understanding the nuances of each type, their operating principles, and their respective advantages and disadvantages is paramount for selecting the optimal motor for a given application, ensuring efficiency, reliability, and optimal performance. By carefully weighing these factors, engineers and designers can harness the power of electric motors to drive innovation and progress in various technological sectors.
Latest Posts
Latest Posts
-
What Is The Difference Between An Antibiotic And An Antiseptic
May 10, 2025
-
What Is 2 3 4 5
May 10, 2025
-
Does A Catalyst Lower Activation Energy
May 10, 2025
-
Words That End With The E Sound
May 10, 2025
-
What Are The Common Multiples Of 9 And 10
May 10, 2025
Related Post
Thank you for visiting our website which covers about What Is The Difference Between Ac And Dc Electric Motors . We hope the information provided has been useful to you. Feel free to contact us if you have any questions or need further assistance. See you next time and don't miss to bookmark.