What Energy Transformation Happens In A Motor
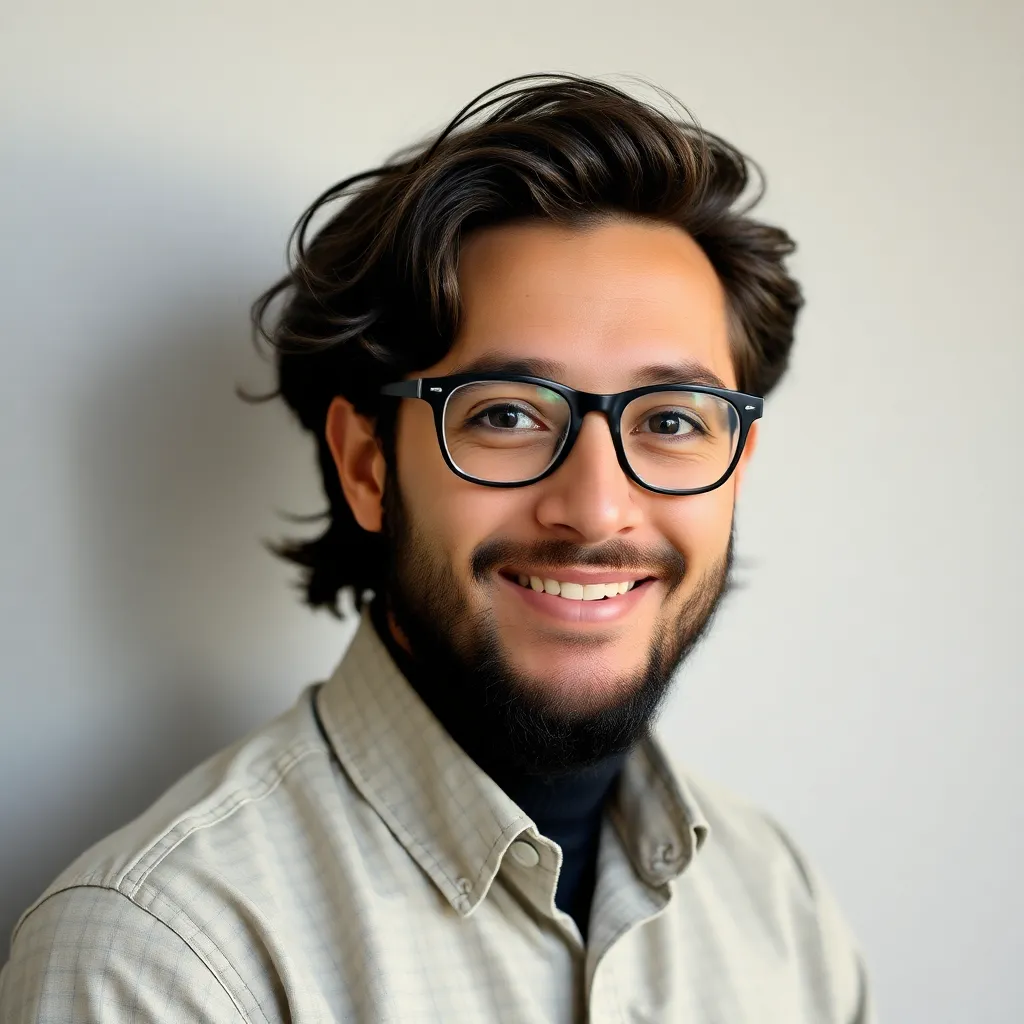
Juapaving
May 09, 2025 · 6 min read
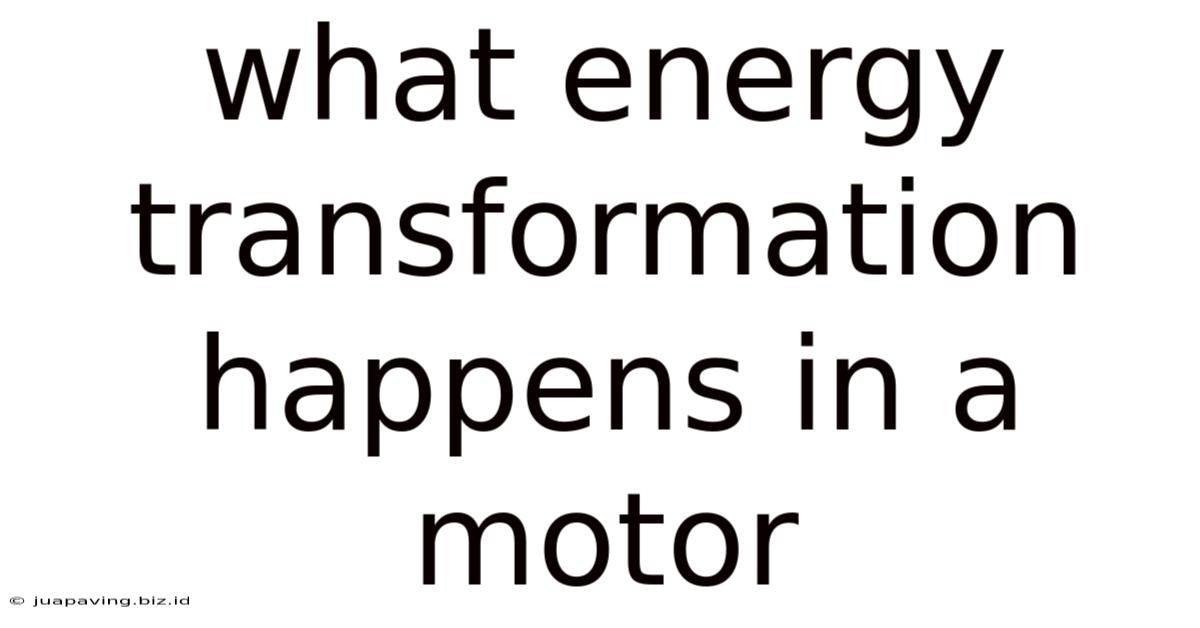
Table of Contents
What Energy Transformations Happen in a Motor? A Deep Dive into Electromechanical Conversion
Electric motors are ubiquitous in modern life, powering everything from our smartphones to industrial machinery. Understanding the energy transformations within these devices is crucial for appreciating their efficiency, limitations, and the ongoing advancements in their design. This article delves deep into the fascinating world of electromechanical energy conversion, exploring the intricate processes that allow motors to transform electrical energy into mechanical work.
From Electrical Energy to Mechanical Motion: The Core Principle
At its heart, an electric motor is an electromechanical energy converter. It takes electrical energy as input and transforms it into rotational mechanical energy – motion – as its output. This transformation isn't a single step but a complex interplay of electromagnetic forces and principles. The specific processes vary depending on the motor type (DC, AC induction, AC synchronous, etc.), but the fundamental principle remains the same: harnessing the interaction between magnetic fields and current-carrying conductors to generate torque and rotation.
The Role of Magnetic Fields
The creation and manipulation of magnetic fields are pivotal to motor operation. These fields are generated in two primary ways:
- Permanent Magnets: Some motors utilize permanent magnets, which possess a persistent magnetic field without the need for external power. This simplifies the motor's design but limits its controllability and power output.
- Electromagnets: More commonly, electromagnets are employed. These are created by passing an electric current through coils of wire, generating a magnetic field whose strength is directly proportional to the current. This allows for precise control over the motor's speed and torque.
The Interaction of Magnetic Fields and Current: The Force Behind Motion
The core energy transformation relies on the interaction between the magnetic fields (either from permanent magnets or electromagnets) and the current flowing through conductors within the motor. This interaction gives rise to a fundamental principle of electromagnetism: a current-carrying conductor placed within a magnetic field experiences a force. This force is perpendicular to both the direction of the current and the direction of the magnetic field.
This force, known as the Lorentz force, is the driving force behind the motor's rotation. By carefully arranging the conductors and magnets, engineers can direct this force to produce a continuous rotational torque.
Different Motor Types: A Spectrum of Energy Transformations
While the underlying principle of electromagnetic interaction remains constant, the specific implementation and energy transformation pathways vary considerably across different motor types.
1. Direct Current (DC) Motors
DC motors are relatively simple in construction and operation. They typically consist of a rotor (the rotating part) with windings, a stator (the stationary part) containing magnets, and a commutator (a device that switches the direction of current in the rotor windings).
The energy transformation in a DC motor can be summarized as follows:
- Electrical Energy Input: DC current is supplied to the motor windings.
- Magnetic Field Generation: This current generates a magnetic field in the rotor windings.
- Interaction of Magnetic Fields: The rotor's magnetic field interacts with the stator's magnetic field, resulting in a torque that causes the rotor to rotate.
- Mechanical Energy Output: The rotational motion of the rotor performs mechanical work.
- Energy Losses: Inefficiencies in the system lead to energy losses as heat due to resistance in the windings and friction in bearings.
Types of DC Motors:
- Brushed DC Motors: These utilize a commutator and brushes to switch the current direction in the rotor windings, ensuring continuous rotation. They are simpler but have limited lifespan due to brush wear.
- Brushless DC Motors: These use electronic commutation, eliminating the need for brushes. This results in longer lifespan, higher efficiency, and better speed control.
2. Alternating Current (AC) Induction Motors
AC induction motors are the workhorses of industrial applications, renowned for their robustness, efficiency, and simplicity. These motors don't require any external electrical connections to the rotor, instead relying on electromagnetic induction to generate torque.
The energy transformation is more complex in AC induction motors:
- Electrical Energy Input: AC current is supplied to the stator windings.
- Rotating Magnetic Field Generation: The AC current creates a rotating magnetic field in the stator.
- Electromagnetic Induction: This rotating magnetic field induces currents in the rotor windings (even without direct electrical connection).
- Interaction of Magnetic Fields: The induced currents in the rotor generate their own magnetic field, which interacts with the stator's rotating field, producing torque.
- Mechanical Energy Output: The rotor rotates, performing mechanical work.
- Energy Losses: Energy losses stem from resistance in the windings, core losses (hysteresis and eddy currents), and mechanical friction.
Types of AC Induction Motors:
- Squirrel Cage Motors: These have a simple rotor construction, making them robust and inexpensive.
- Wound Rotor Motors: These have wound rotors, allowing for greater control over speed and torque.
3. Alternating Current (AC) Synchronous Motors
AC synchronous motors maintain a constant speed synchronized with the frequency of the AC power supply. They are typically used in applications requiring precise speed control, such as clocks and high-precision machinery.
The energy transformation involves:
- Electrical Energy Input: AC current is supplied to both the stator and rotor windings.
- Magnetic Field Generation: Both stator and rotor windings generate magnetic fields.
- Synchronization of Magnetic Fields: The rotor's magnetic field is synchronized with the rotating magnetic field of the stator.
- Torque Generation: The interaction of these synchronized magnetic fields produces torque, driving the rotor.
- Mechanical Energy Output: The rotor rotates at a constant speed, performing mechanical work.
- Energy Losses: Similar to other motor types, energy losses occur due to winding resistance, core losses, and mechanical friction.
Efficiency and Energy Losses: The Imperfect Transformation
No motor is perfectly efficient; some energy is always lost during the transformation process. These losses primarily manifest as heat and reduce the overall efficiency of the motor. Major sources of energy loss include:
- Copper Losses (I²R losses): These are caused by the resistance of the motor windings. Higher currents lead to greater heat generation and energy loss.
- Iron Losses (Core Losses): These include hysteresis losses (energy lost due to magnetization and demagnetization of the core material) and eddy current losses (induced currents in the core material that generate heat).
- Mechanical Losses: These encompass friction losses in bearings, windage losses (air resistance), and other mechanical inefficiencies.
- Stray Load Losses: These are miscellaneous losses that are difficult to quantify accurately.
Advances in Motor Technology: Towards Higher Efficiency
Continuous research and development are focused on improving motor efficiency and reducing energy losses. Some key advancements include:
- Improved Materials: Using materials with lower resistance and higher magnetic permeability can minimize copper and iron losses.
- Optimized Design: Advanced computational techniques allow for precise optimization of motor geometry and winding configurations to reduce losses and enhance efficiency.
- High-Efficiency Motors: New motor designs incorporate features such as improved cooling systems and advanced control strategies to maximize energy conversion.
- Power Electronics: Sophisticated power electronic converters play a crucial role in controlling the motor's speed and torque while minimizing losses.
Conclusion: A Marvel of Electromechanical Conversion
Electric motors represent a remarkable achievement in engineering, seamlessly converting electrical energy into mechanical work. While the underlying principle remains consistent across different motor types, the specific implementation and energy conversion pathways vary. Understanding these transformations is essential for optimizing motor performance, improving efficiency, and designing more sustainable and powerful electromechanical systems for the future. The ongoing advancements in motor technology promise even greater efficiency and performance, further solidifying the motor's indispensable role in our increasingly electrified world.
Latest Posts
Latest Posts
-
What Quadrilateral Has Diagonals That Bisect Each Other
May 10, 2025
-
How To Find Square Root Of 12
May 10, 2025
-
Five Letter Word Starting With R A
May 10, 2025
-
Which Of These Is A Function Of The Skeletal System
May 10, 2025
-
What Is The Cube Root Of 12
May 10, 2025
Related Post
Thank you for visiting our website which covers about What Energy Transformation Happens In A Motor . We hope the information provided has been useful to you. Feel free to contact us if you have any questions or need further assistance. See you next time and don't miss to bookmark.