What Are The 4 Types Of Motors
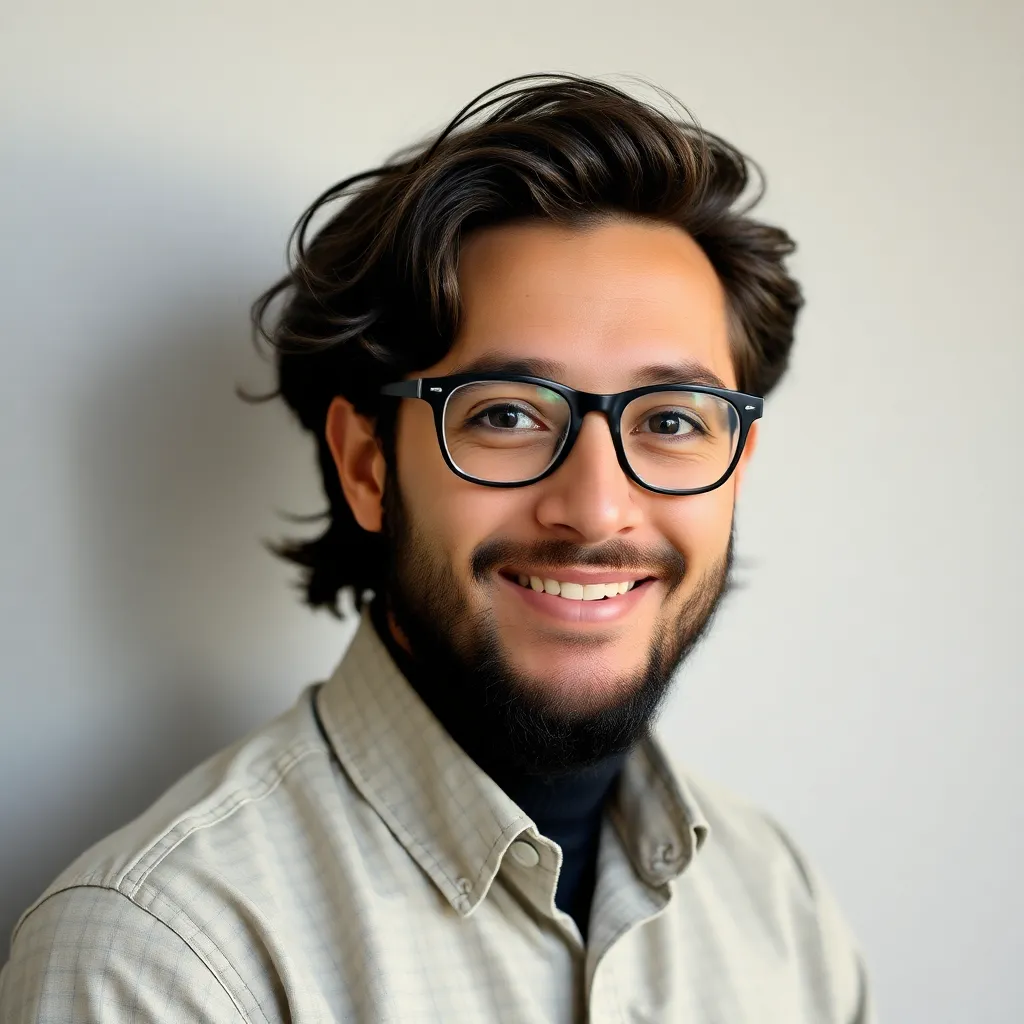
Juapaving
May 14, 2025 · 7 min read
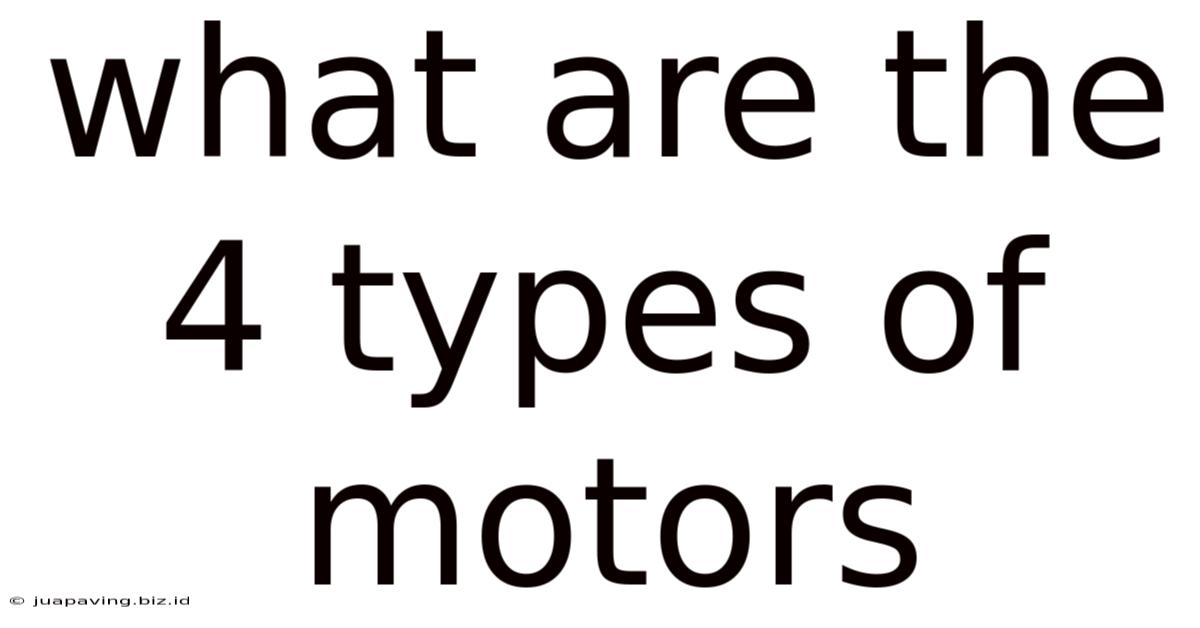
Table of Contents
What are the 4 Main Types of Motors? A Comprehensive Guide
Choosing the right motor for your application can be daunting, given the sheer variety available. While countless variations exist, most electric motors fall under four main categories: AC induction motors, DC brushed motors, DC brushless motors, and stepper motors. Each possesses unique characteristics, strengths, and weaknesses, making them suitable for specific tasks. This comprehensive guide will delve into the intricacies of each type, helping you understand their functionalities and ideal applications.
1. AC Induction Motors: The Workhorses of Industry
AC induction motors are the undisputed champions of industrial applications, accounting for a significant portion of all electric motors produced globally. Their prevalence stems from their robust design, relatively low cost, and ease of maintenance. These motors operate on the principle of electromagnetic induction, harnessing alternating current (AC) to generate a rotating magnetic field that induces current in the rotor, causing it to turn.
How AC Induction Motors Work:
The motor comprises two main components: the stator and the rotor. The stator houses windings supplied with AC power, creating a rotating magnetic field. This rotating field interacts with the rotor's conductive bars (squirrel cage rotor) or windings (wound rotor), inducing currents that generate a magnetic field in the rotor. The interaction between the stator's and rotor's magnetic fields produces torque, causing the rotor to rotate and deliver mechanical power.
Types of AC Induction Motors:
-
Squirrel Cage Induction Motors: The most common type, characterized by a simple, robust rotor consisting of conductive bars embedded in a steel core. They offer high efficiency, low maintenance, and simple construction, making them ideal for many industrial applications. However, they have limited starting torque and speed control capabilities.
-
Wound Rotor Induction Motors: These motors utilize a rotor with windings connected to slip rings and brushes. This design allows for external control of the rotor current, providing improved starting torque and speed control compared to squirrel cage motors. However, they are more complex, costly, and require more maintenance due to the presence of brushes and slip rings.
Advantages of AC Induction Motors:
- High efficiency: They generally offer high efficiency across a wide range of loads.
- Low cost: Their simple design and mass production contribute to a lower cost compared to other motor types.
- Robust and reliable: Known for their durability and ability to withstand harsh operating conditions.
- Low maintenance: They require minimal maintenance, especially squirrel cage types.
Disadvantages of AC Induction Motors:
- Limited starting torque: Squirrel cage motors, in particular, have relatively low starting torque.
- Difficult speed control: Precise speed control can be challenging, requiring specialized techniques like variable frequency drives (VFDs).
- Reactive power consumption: They consume reactive power, which can impact power factor and increase energy costs.
Applications of AC Induction Motors:
AC induction motors are ubiquitous in various applications, including:
- Industrial machinery: Fans, pumps, conveyors, compressors, and other industrial equipment.
- Home appliances: Refrigerators, washing machines, and other household appliances (often smaller single-phase versions).
- Power generation: Used in wind turbines and other power generation systems.
2. DC Brushed Motors: Simple and Versatile
DC brushed motors are known for their simple construction and ease of speed control. They operate by using a commutator and brushes to switch the direction of current flow in the rotor windings, creating a rotating magnetic field that interacts with the stator's magnetic field to produce torque.
How DC Brushed Motors Work:
These motors consist of a stator with permanent magnets or electromagnets and a rotor with windings. The commutator, a segmented cylinder attached to the rotor shaft, reverses the current flow in the rotor windings at specific intervals, ensuring continuous rotation. The brushes make contact with the commutator, providing the electrical connection.
Advantages of DC Brushed Motors:
- Simple construction and low cost: Their straightforward design makes them relatively inexpensive to manufacture.
- Easy speed control: Speed can be easily controlled by adjusting the voltage applied to the motor.
- High starting torque: They can produce significant torque at low speeds.
Disadvantages of DC Brushed Motors:
- Maintenance requirements: The brushes wear out over time and require periodic replacement.
- Limited lifespan: The brushes and commutator are prone to wear, limiting the motor's lifespan.
- Noise and sparking: The brushes can generate noise and sparks, particularly at higher speeds.
- Inefficient at high speeds: Efficiency decreases at higher speeds due to brush wear and commutation losses.
Applications of DC Brushed Motors:
DC brushed motors are suitable for various applications, including:
- Toys and hobby applications: Remote-controlled cars, model airplanes, and other hobbyist projects.
- Small appliances: Hand drills, electric screwdrivers, and other small power tools.
- Automotive applications: Older vehicle windshield wipers and other low-power applications.
3. DC Brushless Motors: High-Performance and Efficient
DC brushless motors represent a significant advancement over their brushed counterparts. They eliminate the brushes and commutator, replacing them with electronic commutation controlled by a dedicated controller. This leads to increased efficiency, longer lifespan, and reduced noise and maintenance.
How DC Brushless Motors Work:
Similar to DC brushed motors, brushless motors use a stator with magnets and a rotor with windings. However, instead of brushes, an electronic controller senses the rotor's position and switches the current flow in the stator windings to create a rotating magnetic field. This precise control eliminates the need for mechanical commutation.
Advantages of DC Brushless Motors:
- High efficiency: They achieve significantly higher efficiency compared to brushed motors, particularly at high speeds.
- Long lifespan: The absence of brushes eliminates wear-related issues, greatly extending the motor's lifespan.
- Reduced noise and vibration: Their smooth operation results in lower noise and vibration levels.
- Precise speed and torque control: The electronic controller allows for accurate control of speed and torque.
- High power-to-weight ratio: They offer a high power output for their size and weight.
Disadvantages of DC Brushless Motors:
- Higher cost: They are generally more expensive than brushed motors due to the added complexity of the electronic controller.
- Requires a controller: They necessitate a dedicated controller to manage electronic commutation.
- More complex design: Their design is more intricate compared to brushed motors.
Applications of DC Brushless Motors:
DC brushless motors are found in a wide range of high-performance applications:
- Electric vehicles: Used in electric cars, bicycles, and other electric vehicles.
- Robotics: Essential components in industrial robots, drones, and other robotic systems.
- Computer peripherals: Found in high-performance computer fans, hard drives, and optical drives.
- Industrial automation: Used in various automated systems requiring precise control and high efficiency.
4. Stepper Motors: Precise Position Control
Stepper motors are unique in their ability to provide precise, incremental rotational movements. Unlike the other motor types discussed, stepper motors do not rotate continuously but move in discrete steps, making them ideal for applications requiring accurate positioning.
How Stepper Motors Work:
These motors typically use a permanent magnet rotor and an electromagnet stator. The stator windings are energized sequentially, creating a magnetic field that pulls the rotor to specific positions. Each energizing sequence corresponds to a step, resulting in incremental rotation.
Types of Stepper Motors:
- Permanent Magnet Stepper Motors: These are the most common type, characterized by their simple design and relatively low cost.
- Variable Reluctance Stepper Motors: These motors utilize a salient-pole rotor and stator, offering higher torque but potentially less precise stepping.
- Hybrid Stepper Motors: These combine features of both permanent magnet and variable reluctance motors, offering a good balance of torque, precision, and cost.
Advantages of Stepper Motors:
- Precise positioning: They allow for accurate and repeatable positioning in incremental steps.
- Open-loop control: They can operate in open-loop control, simplifying the control system.
- High holding torque: They can hold their position without the need for external brakes.
Disadvantages of Stepper Motors:
- Lower speed capabilities: They are typically limited in their maximum speed compared to other motor types.
- Resonance issues: At higher speeds, resonance can occur, leading to vibrations and inaccurate positioning.
- Complex control systems for high speeds: Achieving smooth high speed operations may require more advanced control techniques.
Applications of Stepper Motors:
Stepper motors are commonly used in applications requiring precise control and positioning:
- 3D printers: Essential for precise movement of the print head.
- CNC machines: Used for accurate positioning of cutting tools.
- Robotics: Used in applications requiring precise movements.
- Medical devices: Found in various medical instruments requiring accurate positioning.
Conclusion: Choosing the Right Motor for Your Needs
The choice of motor depends heavily on the specific application's requirements. Consider factors such as required torque, speed, efficiency, cost, size, maintenance requirements, and control complexity when making your selection. AC induction motors reign supreme in industrial settings for their robustness and efficiency. DC brushed motors provide a simple, low-cost solution for many smaller applications. DC brushless motors offer superior performance and longevity for high-performance applications. Finally, stepper motors are indispensable for applications demanding precise positioning and control. By understanding the strengths and weaknesses of each type, you can make an informed decision and choose the optimal motor for your project.
Latest Posts
Latest Posts
-
Number In Words From 1 To 100
May 14, 2025
-
What Is 96 Inches In Feet
May 14, 2025
-
What Percentage Is 35 Out Of 40
May 14, 2025
-
Electricity Is Measured In What Unit
May 14, 2025
-
Is A Pencil A Conductor Or Insulator
May 14, 2025
Related Post
Thank you for visiting our website which covers about What Are The 4 Types Of Motors . We hope the information provided has been useful to you. Feel free to contact us if you have any questions or need further assistance. See you next time and don't miss to bookmark.