Unloading Valves Are Used With Many Engine-driven Hydraulic Pumps To
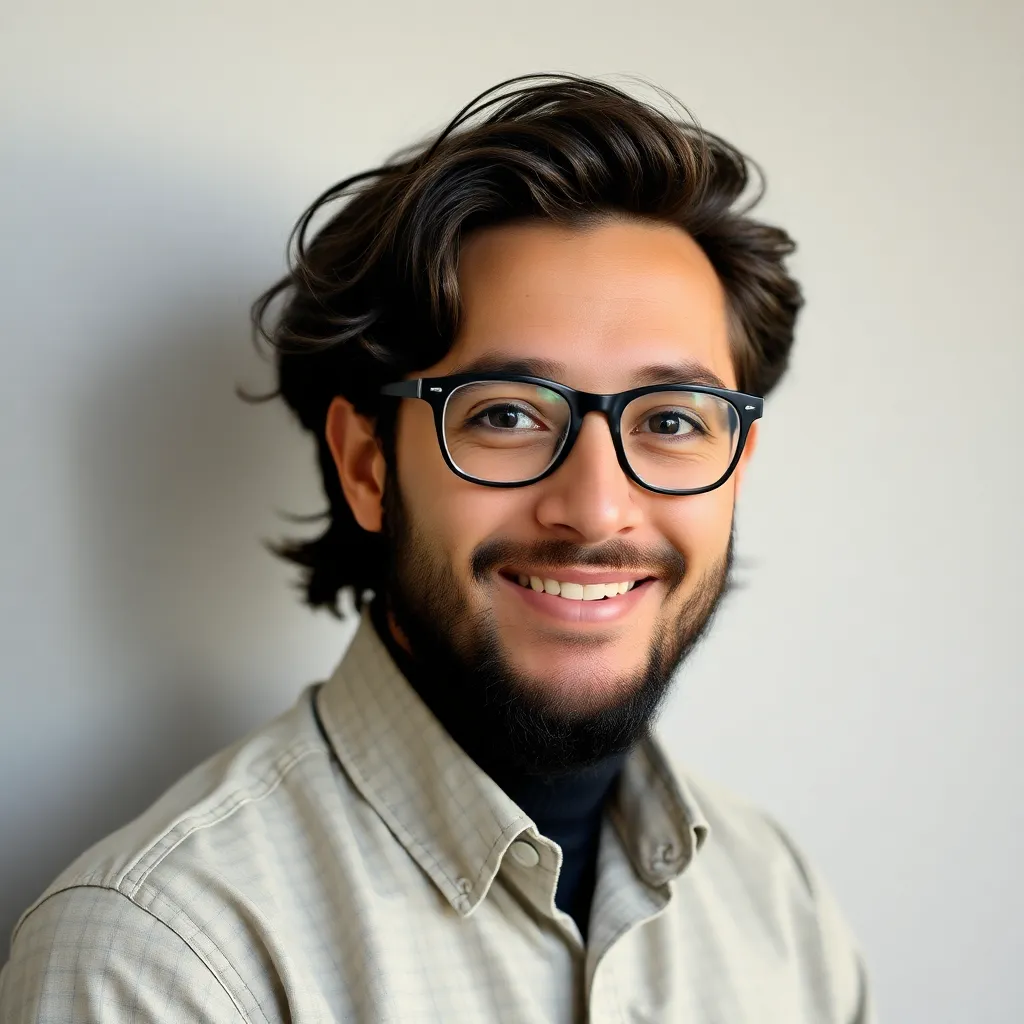
Juapaving
May 25, 2025 · 6 min read
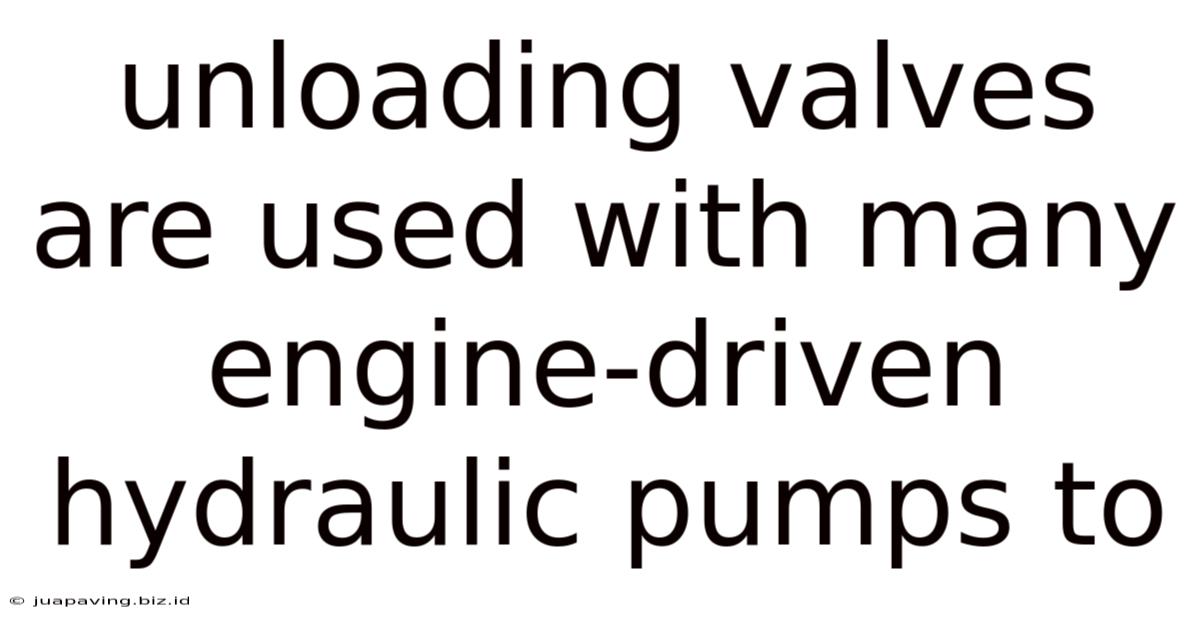
Table of Contents
Unloading Valves: Essential Components for Engine-Driven Hydraulic Pumps
Engine-driven hydraulic pumps are workhorses in numerous applications, from agricultural machinery and construction equipment to industrial processes and manufacturing. However, their efficient and safe operation relies heavily on a crucial component: the unloading valve. This article delves deep into the world of unloading valves, exploring their function, types, applications, benefits, and considerations for optimal performance.
Understanding the Role of Unloading Valves
Engine-driven hydraulic pumps, unlike electrically driven pumps, are constantly driven by the engine's power, even when the hydraulic system isn't actively demanding fluid. This continuous operation can lead to several problems:
- Increased wear and tear: Constant operation without a load generates excessive heat and friction within the pump, leading to premature wear and shortened lifespan.
- Wasted energy: The pump continuously consumes engine power, even when idle, resulting in inefficient fuel consumption and reduced overall system efficiency.
- High pressure build-up: If the hydraulic system is closed off, the pressure can build to dangerous levels, potentially causing damage to components or even system failure.
This is where the unloading valve steps in. It acts as a pressure relief mechanism, bypassing the hydraulic fluid directly back to the reservoir when the system isn't under load. This prevents the issues mentioned above by essentially "disengaging" the pump when it's not needed, saving energy, reducing wear, and maintaining safe operating pressures.
Types of Unloading Valves
Several types of unloading valves are used with engine-driven hydraulic pumps, each with its own design and operating characteristics:
1. Spring-Loaded Unloading Valves:
These are the simplest and most common type of unloading valve. A spring maintains the valve in a closed position until the system pressure reaches a predetermined level. Once this pressure is exceeded, the spring is overcome, allowing the fluid to bypass back to the reservoir. These valves are generally inexpensive and easy to maintain, making them suitable for many applications. However, their pressure setting is fixed, offering limited adjustability.
2. Pilot-Operated Unloading Valves:
These valves use a small pilot signal to control the main unloading valve. A low-pressure signal opens the valve, allowing the fluid to bypass, while the absence of a signal keeps it closed. Pilot-operated unloading valves offer better control and adjustability than spring-loaded valves. They can be precisely tuned to meet specific system requirements and respond more quickly to changes in pressure demand. They are more complex but provide superior performance.
3. Pressure-Compensated Unloading Valves:
These valves automatically adjust the unloading pressure based on the system's demand. As the pressure in the system increases, the valve opens proportionally, maintaining a relatively constant pressure. Pressure-compensated unloading valves are ideal for applications requiring precise pressure control. They offer superior efficiency and minimize pressure fluctuations, but are generally more expensive and complex than other types.
4. Flow-Controlled Unloading Valves:
These valves regulate the flow of hydraulic fluid bypassing back to the reservoir. They don't necessarily rely on pressure as the primary control mechanism. Flow-controlled unloading valves are suitable for applications where the flow rate needs to be precisely controlled, regardless of the system pressure. These are more specialized and found in more sophisticated hydraulic systems.
Applications of Unloading Valves
The versatility of unloading valves makes them essential components in a vast range of applications:
-
Agricultural Machinery: Tractors, harvesters, and other agricultural equipment heavily rely on engine-driven hydraulic pumps, and unloading valves are crucial for efficient operation, conserving fuel and reducing wear on the hydraulic system. They enable smooth operation of implements like plows, planters, and sprayers.
-
Construction Equipment: Excavators, loaders, bulldozers, and other construction machinery use powerful hydraulic systems for lifting, digging, and maneuvering. Unloading valves help prevent damage and optimize energy usage in these demanding applications.
-
Industrial Machinery: Numerous industrial processes rely on hydraulic power, including presses, conveyors, and robots. Unloading valves enhance the efficiency and lifespan of the hydraulic pumps within these systems.
-
Mobile Hydraulic Equipment: Forklifts, cranes, and other mobile hydraulic equipment benefit from unloading valves, contributing to longer pump life and reduced operational costs.
-
Manufacturing Processes: Unloading valves play a vital role in various manufacturing operations, enhancing the performance and reliability of hydraulically powered machinery.
-
Material Handling: Hydraulic systems are extensively used in material handling equipment, where unloading valves are essential for efficient and safe operations.
Benefits of Using Unloading Valves
Implementing unloading valves in engine-driven hydraulic pump systems offers several compelling advantages:
-
Extended Pump Lifespan: By reducing the constant wear and tear from continuous operation, unloading valves significantly extend the operational life of the hydraulic pump.
-
Improved Energy Efficiency: By bypassing fluid when the system isn't under load, unloading valves conserve energy, leading to reduced fuel consumption and lower operational costs.
-
Reduced Heat Generation: The continuous operation of a hydraulic pump generates significant heat. Unloading valves mitigate this by reducing the pump's workload, resulting in lower operating temperatures and improved system reliability.
-
Protection Against Pressure Surges: Unloading valves prevent dangerous pressure build-ups in the hydraulic system by quickly directing excess fluid back to the reservoir.
-
Enhanced System Efficiency: Unloading valves optimize the hydraulic system's overall performance by ensuring the pump operates only when needed, leading to improved productivity and reduced downtime.
-
Simplified System Design: In some cases, unloading valves can simplify the overall hydraulic system design by eliminating the need for more complex pressure-regulating components.
Selecting the Right Unloading Valve
Choosing the appropriate unloading valve depends on several factors:
-
System Pressure: The maximum operating pressure of the hydraulic system will determine the valve's pressure rating.
-
Flow Rate: The expected flow rate of the hydraulic fluid needs to be considered to ensure adequate valve capacity.
-
Response Time: The speed at which the valve needs to respond to changes in system demand will influence the selection.
-
Adjustability: The need for adjustable pressure or flow control will determine if a simple spring-loaded valve or a more sophisticated type is required.
-
Mounting Requirements: The physical dimensions and mounting configuration of the valve should be compatible with the system.
Maintenance and Troubleshooting
Proper maintenance is vital to ensure the longevity and reliability of unloading valves:
-
Regular Inspection: Visually inspect the valve for leaks, damage, or signs of wear and tear.
-
Pressure Testing: Periodically test the valve's pressure setting to ensure it's within the specified range.
-
Cleaning: Keep the valve and its surrounding area clean and free from debris.
-
Lubrication: If required, lubricate moving parts according to the manufacturer's recommendations.
Common troubleshooting issues with unloading valves include leaks, incorrect pressure settings, and sluggish operation. Identifying and addressing these issues promptly is crucial for maintaining optimal system performance.
Conclusion
Unloading valves are indispensable components in engine-driven hydraulic pump systems. They are essential for efficient operation, system protection, and extended equipment lifespan. Understanding the different types of unloading valves, their applications, and their maintenance requirements is crucial for maximizing the performance and reliability of any hydraulic system that relies on an engine-driven pump. By selecting the right valve and providing proper maintenance, users can ensure the smooth and efficient operation of their equipment, leading to cost savings, increased productivity, and improved overall system reliability. Choosing the correct unloading valve is a critical step in optimizing any engine-driven hydraulic system, ensuring both efficient operation and the longevity of vital components. Careful consideration of the factors mentioned above will lead to a more robust and productive hydraulic setup.
Latest Posts
Latest Posts
-
The Canterbury Tales The Reeves Tale
May 25, 2025
-
What Is The Setting In The Scarlet Letter
May 25, 2025
-
Ending Of The Death Of A Salesman
May 25, 2025
-
The Following Is Parking Regulation In California
May 25, 2025
-
Analysis Of Ode To The West Wind
May 25, 2025
Related Post
Thank you for visiting our website which covers about Unloading Valves Are Used With Many Engine-driven Hydraulic Pumps To . We hope the information provided has been useful to you. Feel free to contact us if you have any questions or need further assistance. See you next time and don't miss to bookmark.