The Most Common Type Of Pressure Gauge Is The
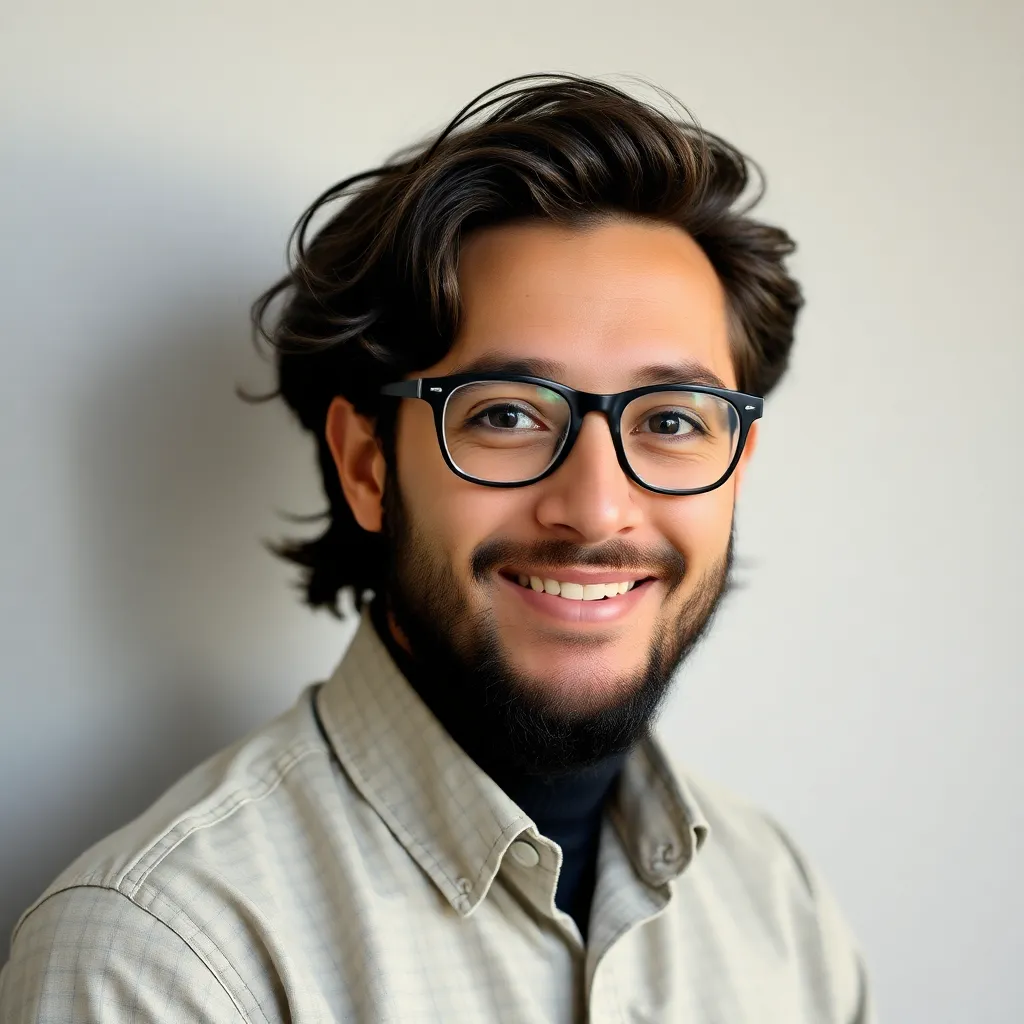
Juapaving
Apr 08, 2025 · 7 min read

Table of Contents
The Most Common Type of Pressure Gauge Is the Bourdon Tube Gauge: A Deep Dive into its Design, Applications, and Maintenance
The ubiquitous pressure gauge, a seemingly simple device, plays a crucial role in countless industrial processes, ensuring safety, efficiency, and optimal performance. While various types exist, the Bourdon tube gauge reigns supreme as the most common, thanks to its robust design, accuracy, and cost-effectiveness. This comprehensive guide delves into the intricacies of the Bourdon tube pressure gauge, exploring its working principle, diverse applications, potential limitations, and essential maintenance practices.
Understanding the Bourdon Tube: The Heart of the Gauge
At the core of the Bourdon tube pressure gauge lies its namesake component: the Bourdon tube. This is a C-shaped, or sometimes helical or spiral, metallic tube with an elliptical cross-section. When pressure is applied to the inside of the tube, its elliptical cross-section tends to straighten, a phenomenon driven by the internal pressure overcoming the tube's elastic resistance. This straightening motion, though subtle, is precisely what drives the gauge's indication.
How the Bourdon Tube Translates Pressure into Readable Data:
-
Pressure Application: Pressure enters the Bourdon tube through a connection point.
-
Tube Straightening: The internal pressure causes the elliptical cross-section to attempt to become circular, resulting in a slight straightening of the tube.
-
Mechanical Linkage: This straightening motion is mechanically amplified through a series of linkages, including a sector gear and pinion.
-
Pointer Movement: The amplified motion rotates the pinion, which in turn moves a pointer across a calibrated dial.
-
Pressure Indication: The pointer's position on the dial directly indicates the applied pressure.
The sensitivity of the Bourdon tube gauge is directly related to the tube's material properties, dimensions (including its length, diameter, and wall thickness), and the degree of its ellipticity. Different materials are selected based on the application's pressure range and the corrosive nature of the measured media.
Common Materials Used in Bourdon Tube Construction:
The choice of material for the Bourdon tube significantly impacts the gauge's durability, accuracy, and suitability for specific applications. Some of the most frequently used materials include:
-
Phosphor Bronze: A popular choice due to its excellent corrosion resistance and high elasticity, making it suitable for a wide range of applications.
-
Brass: Offers good corrosion resistance and machinability, although it may not be as durable as phosphor bronze under extreme pressure conditions.
-
Stainless Steel: Used when high temperatures, pressures, or corrosive media are involved, offering superior strength and resistance to chemical degradation. Different grades of stainless steel provide varying levels of performance.
-
Monel: A nickel-copper alloy, particularly suitable for highly corrosive environments where other materials may fail.
-
Inconel: A nickel-chromium-based superalloy, offering exceptional strength and resistance to high temperatures and corrosion, often used in demanding industrial settings.
Applications of Bourdon Tube Pressure Gauges:
The versatility and reliability of Bourdon tube gauges make them indispensable across numerous industries. Their applications are vast, encompassing:
-
Industrial Processes: Monitoring pressure in pipelines, reactors, compressors, and other critical equipment in chemical processing, oil and gas, power generation, and manufacturing plants.
-
HVAC Systems: Measuring air pressure in HVAC systems to ensure optimal airflow and efficiency.
-
Automotive Industry: Used in testing automotive components and systems.
-
Medical Applications: Certain specialized Bourdon tube gauges find application in medical equipment requiring precise pressure measurement.
-
Pneumatic Systems: Monitoring pressure in pneumatic control systems and equipment.
-
Hydraulic Systems: Measuring pressure in hydraulic systems, such as those used in heavy machinery and construction equipment.
Advantages of Bourdon Tube Pressure Gauges:
The enduring popularity of the Bourdon tube gauge stems from several key advantages:
-
Simplicity and Robustness: Its straightforward mechanical design leads to high reliability and ease of maintenance.
-
Cost-Effectiveness: Compared to other pressure measurement technologies, Bourdon tube gauges are generally more affordable.
-
Direct Reading: The analog dial provides a direct and easily interpretable pressure reading.
-
Wide Pressure Range: Bourdon tube gauges are available across an extensive range of pressure measurements, from low vacuum to extremely high pressures.
-
Compact Size: They typically have a compact size, making them suitable for applications with space constraints.
-
Ease of Installation: Installation is typically straightforward, requiring minimal specialized tools or expertise.
Limitations of Bourdon Tube Pressure Gauges:
Despite their widespread use, Bourdon tube gauges do have some limitations:
-
Accuracy: While generally accurate, their precision can be lower compared to more advanced digital or electronic pressure sensors.
-
Susceptibility to Vibration: Excessive vibration can affect the accuracy of the reading and potentially damage the gauge over time.
-
Limited Lifespan: The mechanical components are subject to wear and tear, resulting in a finite lifespan, especially under harsh conditions.
-
Analog Display: The analog display may not be suitable for applications requiring high-precision readings or data logging capabilities.
-
Difficult Remote Reading: Remote reading of the pressure requires a separate mechanism or additional instrumentation.
Maintenance and Calibration of Bourdon Tube Gauges:
Regular maintenance is crucial to ensure the longevity and accuracy of Bourdon tube pressure gauges. Essential maintenance practices include:
-
Regular Inspection: Visually inspect the gauge for any signs of damage, leaks, or unusual wear and tear.
-
Cleaning: Clean the gauge periodically to remove dust, debris, or corrosive materials that could affect accuracy or longevity.
-
Calibration: Regular calibration is vital to maintain accuracy. This typically involves comparing the gauge's reading to a known standard or a more accurate pressure measuring device. The frequency of calibration depends on the gauge's application and the required level of accuracy. Calibration should be performed by qualified personnel using appropriate equipment.
-
Storage: Proper storage in a clean, dry environment helps to extend the gauge's lifespan.
-
Avoid Overpressure: Never expose the gauge to pressures exceeding its maximum rated capacity.
Choosing the Right Bourdon Tube Gauge:
Selecting the appropriate Bourdon tube pressure gauge involves careful consideration of several factors:
-
Pressure Range: The gauge's pressure range must accommodate the expected pressure values within the application.
-
Accuracy: The required accuracy level dictates the choice of gauge and its calibration requirements.
-
Material Compatibility: The Bourdon tube material should be compatible with the measured medium to prevent corrosion or degradation.
-
Connection Type: The gauge must have the correct connection type to match the process equipment.
-
Environmental Conditions: The gauge's operating temperature range and resistance to vibration or other environmental factors must be suitable for the application.
-
Dial Size and Readability: Choose a dial size and marking that ensure easy readability in the specific application environment.
Bourdon Tube Gauges Compared to Other Pressure Measurement Technologies:
While Bourdon tube gauges dominate the market, alternative technologies offer different advantages and disadvantages. Comparison with other common pressure measurement technologies:
-
Digital Pressure Gauges: Digital gauges provide higher accuracy, data logging capabilities, and often remote reading options. However, they are typically more expensive and may require more complex installation and calibration procedures.
-
Diaphragm Gauges: Suitable for low-pressure applications, diaphragm gauges offer good accuracy and resistance to overpressure. They are generally less durable than Bourdon tube gauges.
-
Strain Gauge Pressure Transducers: These transducers offer high accuracy and rapid response times, often used in dynamic pressure measurements. They are more expensive than Bourdon tube gauges and require sophisticated signal conditioning circuitry.
-
Capacitive Pressure Sensors: These sensors utilize capacitance changes to measure pressure, offering high accuracy and stability. They are more expensive and generally used in demanding applications.
Future Trends in Bourdon Tube Gauge Technology:
While more advanced digital technologies are gaining popularity, the Bourdon tube gauge retains its significance. Future trends are likely to involve:
-
Improved Materials: The development of new materials with enhanced durability, corrosion resistance, and temperature tolerance will further extend the lifespan and capabilities of Bourdon tube gauges.
-
Miniaturization: Ongoing efforts to miniaturize Bourdon tube gauges will enhance their suitability for compact applications.
-
Integration with Smart Sensors: Integrating Bourdon tube gauges with smart sensors and data acquisition systems could provide advanced data logging and remote monitoring capabilities.
In conclusion, the Bourdon tube pressure gauge remains the most common type due to its robust design, wide applicability, and cost-effectiveness. Understanding its working principles, limitations, and maintenance requirements ensures its continued reliable operation and contributes to safe and efficient processes across various industries. Though new technologies present alternatives, the enduring simplicity and resilience of the Bourdon tube gauge solidify its place as an indispensable tool in pressure measurement.
Latest Posts
Latest Posts
-
Nouns That Start With A W
Apr 17, 2025
-
Which Of These Is An Example Of Acceleration
Apr 17, 2025
-
How Many Feet Are In 121 Inches
Apr 17, 2025
-
Can Light Travel Through A Vacuum
Apr 17, 2025
-
What Percent Of 30 Is 240
Apr 17, 2025
Related Post
Thank you for visiting our website which covers about The Most Common Type Of Pressure Gauge Is The . We hope the information provided has been useful to you. Feel free to contact us if you have any questions or need further assistance. See you next time and don't miss to bookmark.