The Material Used For Fuse Has Low Melting Point
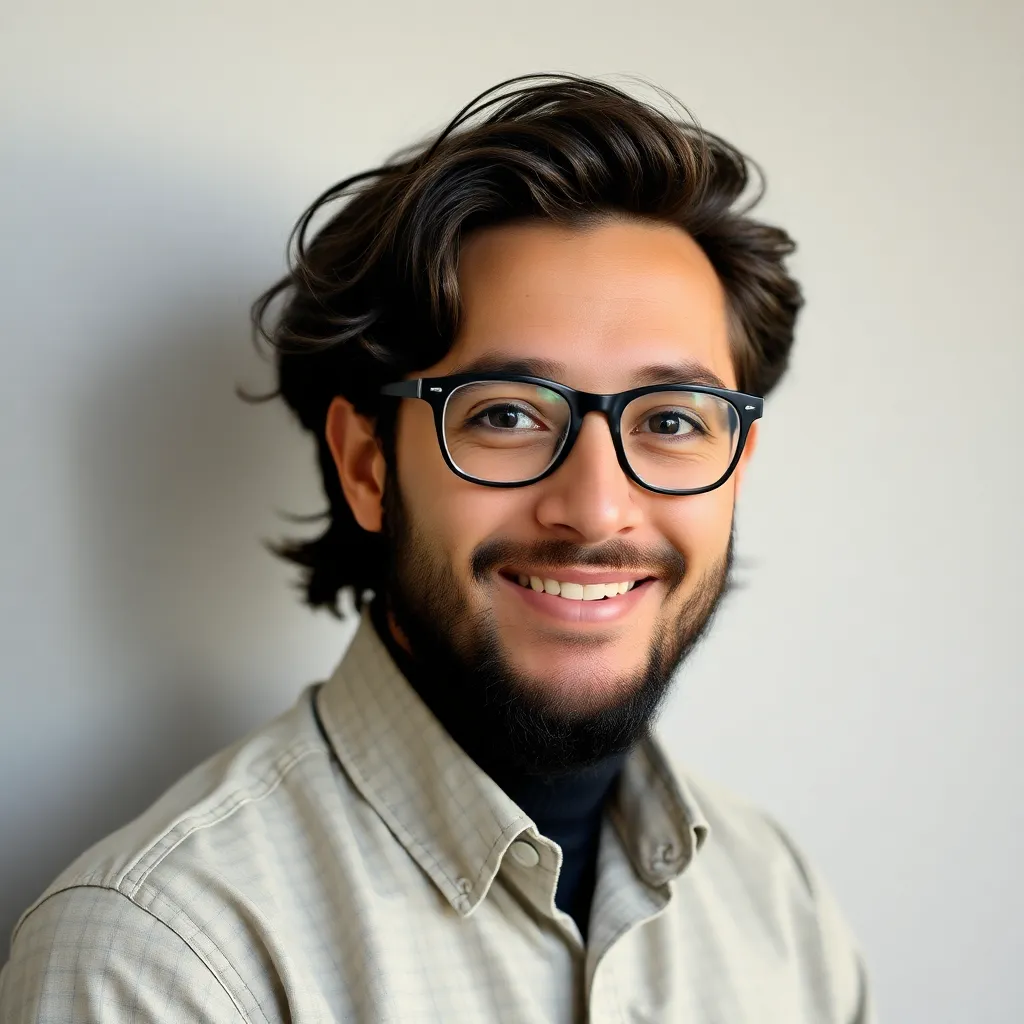
Juapaving
Apr 25, 2025 · 5 min read

Table of Contents
The Material Used for Fuses Has a Low Melting Point: Why This is Crucial for Electrical Safety
Fuses are unsung heroes of the electrical world. These seemingly simple devices play a vital role in protecting our homes, businesses, and electronic equipment from the devastating effects of overcurrent situations. Their effectiveness hinges on a critical characteristic: the use of materials with exceptionally low melting points. This article delves deep into the science behind fuse materials, exploring why a low melting point is essential for their function, the various materials employed, and the ongoing advancements in fuse technology.
Understanding the Function of a Fuse
Before diving into the specifics of low melting point materials, let's establish a fundamental understanding of how a fuse works. At its core, a fuse is a safety device designed to protect an electrical circuit from excessive current flow. This excessive current, often caused by short circuits, overloads, or equipment malfunctions, can generate excessive heat, potentially leading to fires, damage to equipment, and even electrocution.
A fuse consists of a thin wire or metal strip (the fuse element) encased in a protective housing. This fuse element is carefully chosen to have a specific melting point and current-carrying capacity. When the current flowing through the circuit exceeds the fuse's rated capacity, the excessive heat generated causes the fuse element to melt, breaking the circuit and preventing further current flow. This rapid response is crucial in minimizing damage and ensuring safety.
The Critical Role of Low Melting Point
The selection of materials for fuse elements is governed by the need for a low melting point. This is not merely a desirable characteristic; it's absolutely fundamental to the fuse's functionality. The reasons are threefold:
1. Rapid Response Time:
A low melting point ensures a swift response to overcurrent situations. When an excessive current flows, the heat generated rapidly raises the temperature of the fuse element. A material with a low melting point will melt quickly, interrupting the current flow before significant damage can occur. This rapid response is paramount in preventing fires and equipment damage. A slow-acting fuse could allow the overcurrent to persist, potentially leading to catastrophic consequences.
2. Precise Current Rating:
The melting point of the fuse element is directly related to its current rating. Fuse manufacturers carefully select materials with melting points that correspond to the desired current rating. A lower melting point allows for the creation of fuses with lower current ratings, catering to the diverse needs of various electrical circuits. This precision in current rating is crucial for selecting the appropriate fuse for a specific application, ensuring optimal protection without unnecessary interruptions.
3. Preventing Heat Buildup:
A low melting point helps to prevent excessive heat buildup within the fuse itself. While the fuse is designed to handle normal current flow, an overcurrent situation generates significantly more heat. A material with a low melting point melts before the heat can accumulate to dangerous levels, preventing the fuse from overheating and potentially causing a fire hazard even after the fuse has blown. This safety feature is crucial, especially in high-current applications.
Common Fuse Materials and Their Melting Points
Several materials are commonly used in fuse elements due to their low melting points and other desirable properties:
1. Lead Alloys:
Lead alloys, especially those containing tin and antimony, have been historically prevalent in fuse construction. These alloys offer a good balance between a low melting point (typically around 200-300°C), good conductivity, and relatively low cost. However, due to environmental concerns regarding lead toxicity, the use of lead-based alloys is gradually decreasing.
2. Zinc:
Zinc is another popular choice, boasting a melting point of 419.5°C. It offers a higher melting point compared to lead alloys, resulting in a slightly slower response time, but it's more environmentally friendly and exhibits good conductivity. Zinc fuses are commonly found in various electrical applications.
3. Copper:
While copper has a significantly higher melting point (1084.62°C), it's often used in high-current fuses where the thicker wire can still melt relatively quickly under excessive current. The higher melting point necessitates a larger cross-sectional area of the wire to achieve the desired current rating.
4. Aluminum:
Aluminum, with its melting point of 660.32°C, is another option occasionally used in high-current fuse applications. Its lightweight nature and relatively low cost make it attractive, although its lower conductivity compared to copper often limits its use.
5. Silver:
Silver, despite its exceptionally high melting point (961.8°C), is employed in specialized high-speed fuses. Its high conductivity allows for thinner wires, which can still melt quickly enough under severe overcurrent conditions. The higher cost of silver usually restricts its use to specialized, high-performance applications.
Advancements in Fuse Technology and Materials
The field of fuse technology is constantly evolving, driven by the need for improved safety, efficiency, and environmental friendliness. Several advancements are noteworthy:
1. Development of Lead-Free Alloys:
The environmental concerns surrounding lead have led to extensive research into developing lead-free alloys for fuse elements. These new alloys aim to replicate the desirable properties of lead-based alloys while eliminating the toxicity.
2. Improved Fuse Designs:
New fuse designs incorporate features such as improved arc quenching mechanisms and faster response times. These design improvements enhance safety and minimize the potential for damage during overcurrent events.
3. Smart Fuses:
The integration of electronics into fuses ("smart fuses") allows for monitoring current flow, detecting faults, and even communicating with other devices in a network. This technology enhances circuit protection and enables predictive maintenance.
4. Use of Nanotechnology:
Research is exploring the use of nanomaterials to improve the performance of fuse elements. Nanomaterials offer the potential to create fuses with enhanced properties, such as higher sensitivity, faster response times, and improved thermal management.
Conclusion
The use of materials with low melting points is not merely a design choice in fuse technology; it's a fundamental requirement for ensuring their effectiveness and safety. The rapid response time, precise current rating, and prevention of heat buildup provided by these materials are crucial in protecting electrical circuits and preventing damage. Ongoing research and development continue to refine fuse materials and designs, leading to enhanced safety and performance in the ever-evolving landscape of electrical systems. Understanding the crucial role of low melting point materials underscores the essential contribution of fuses to our electrical safety and reliability. The seemingly simple fuse is a testament to the powerful impact of material science on protecting our lives and infrastructure.
Latest Posts
Latest Posts
-
How Many Atoms Does Na Have
Apr 26, 2025
-
First 10 Elements Of Periodic Table
Apr 26, 2025
-
What Is The Conjugate Base Of Oh
Apr 26, 2025
-
98 6 Fahrenheit Is What In Celsius
Apr 26, 2025
-
5 Letter Words Beginning With Tho
Apr 26, 2025
Related Post
Thank you for visiting our website which covers about The Material Used For Fuse Has Low Melting Point . We hope the information provided has been useful to you. Feel free to contact us if you have any questions or need further assistance. See you next time and don't miss to bookmark.