The Costs Of Direct Materials Are Classified As
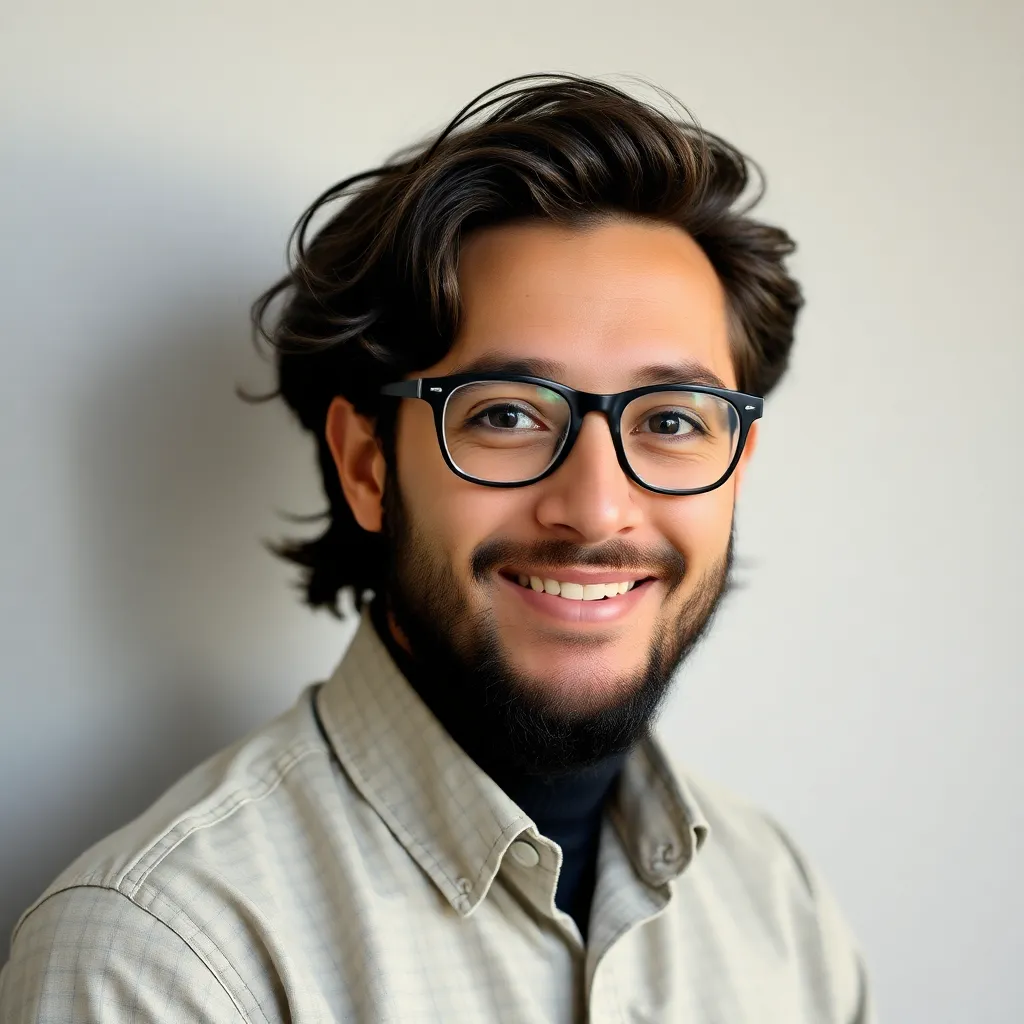
Juapaving
May 28, 2025 · 6 min read
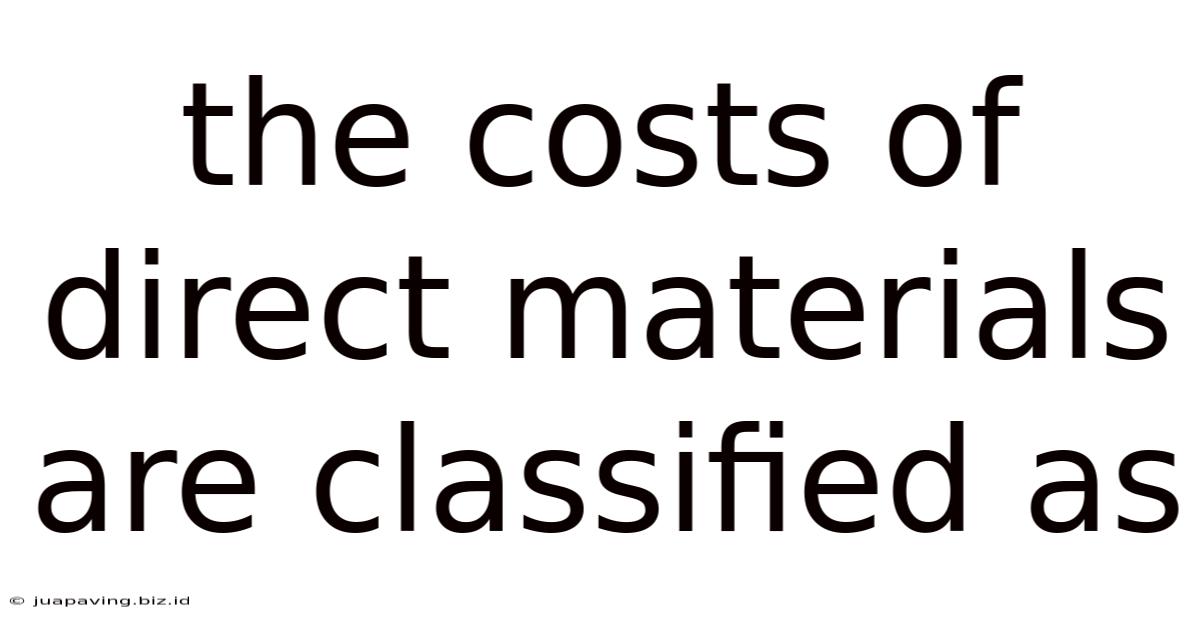
Table of Contents
The Costs of Direct Materials: A Comprehensive Guide to Classification and Management
Direct materials are the lifeblood of many manufacturing and production businesses. Understanding how to classify and manage their costs is crucial for profitability and efficient operations. This in-depth guide will explore the various classifications of direct material costs, providing practical insights and examples for businesses of all sizes.
What are Direct Materials?
Before diving into classifications, let's define what constitutes direct materials. Direct materials are those raw materials that are directly used in the production process and can be easily traced to the finished product. Think of the flour in a bakery, the wood in furniture making, or the steel in automobile manufacturing. These materials become an integral part of the final product and their costs are directly attributable to it. This contrasts with indirect materials, which are used in the production process but are not easily traceable to a specific product (e.g., cleaning supplies, lubricants).
Key Classifications of Direct Material Costs
The costs of direct materials can be classified in several ways, depending on the context and the level of detail required. Here are some of the most common classifications:
1. By Nature of Material:
-
Raw Materials: These are the basic, unprocessed materials that enter the production process. Examples include timber for furniture, cotton for textiles, or iron ore for steel production. The cost of raw materials is a significant component of the total direct material cost.
-
Purchased Parts: These are components or sub-assemblies that are purchased from external suppliers and directly incorporated into the finished product. For instance, a car manufacturer might purchase pre-fabricated engines or tires from specialized suppliers. The cost includes not only the price paid but also transportation and handling charges.
-
Packaging Materials: In some industries, packaging is an integral part of the product. For example, the cost of bottles for wine, boxes for cereal, or specialized containers for pharmaceuticals is a crucial direct material cost.
2. By Cost Behavior:
-
Variable Costs: These costs change directly in proportion to the volume of production. The more products produced, the higher the direct material costs. A great example is the cost of raw materials used in making bread; more loaves mean more flour, yeast, and other ingredients are needed.
-
Fixed Costs (Relatively): While generally, direct materials are variable costs, there can be elements of fixed cost in certain scenarios. For instance, a minimum order quantity from a supplier might mean paying a fixed amount irrespective of immediate production needs. This is a relatively fixed cost component within the broader variable direct materials category.
3. By Accounting Treatment:
-
Standard Costs: This method involves pre-determining the expected cost of direct materials per unit. These standard costs are then compared to actual costs to identify variances and improve efficiency. Standard costing provides a valuable benchmark for cost control.
-
Actual Costs: This approach uses the actual costs incurred for direct materials during the production process. While it's more accurate than standard costing, it's also less efficient for planning and control, as costs are only known after production.
4. By Cost Element:
-
Material Acquisition Cost: This includes the purchase price of the materials, freight charges, import duties (if applicable), and any other expenses related to acquiring the materials. This is a crucial factor in determining the overall cost of materials.
-
Handling and Storage Costs: These costs involve storing and handling materials before they are used in the production process. Costs might include rent for warehouse space, insurance, utilities, and labor related to material handling. These are often considered part of indirect costs but can be directly allocated to specific products in certain accounting systems.
-
Quality Control Costs: Costs associated with inspecting and testing materials to ensure they meet quality standards. Rejected materials or rework due to quality issues directly impact the cost of direct materials.
-
Waste and Spoilage: This represents the value of materials lost due to waste, spoilage, or defects. Minimizing waste is critical for controlling direct material costs.
Managing Direct Material Costs: Key Strategies
Effective management of direct material costs is essential for a company's bottom line. Here are some strategies that can help:
1. Supplier Relationship Management (SRM):
Developing strong relationships with reliable suppliers is crucial. This involves negotiating favorable pricing, securing reliable supply chains, and establishing clear communication channels. Negotiating bulk discounts, long-term contracts, and exploring alternative suppliers can significantly reduce costs.
2. Inventory Management:
Efficient inventory management is crucial to avoid stockouts and excessive holding costs. Implementing inventory control systems like Just-in-Time (JIT) inventory or Kanban can minimize storage costs and reduce waste due to spoilage or obsolescence.
3. Waste Reduction and Process Improvement:
Identifying and minimizing waste in the production process is essential. This includes implementing lean manufacturing techniques to streamline operations, optimize production processes, and reduce material waste. Regular process audits and employee training can help improve efficiency and reduce material costs.
4. Quality Control:
Maintaining strict quality control procedures at every stage of production can significantly reduce material waste and rework costs. Regular inspection and testing of raw materials and finished goods can help ensure that materials meet the required standards, reducing waste and enhancing efficiency.
5. Technological Advancements:
Adopting new technologies like automation, robotics, and advanced manufacturing systems can significantly improve efficiency and reduce material waste. These technologies can also improve precision and accuracy in production, minimizing errors and reducing the need for rework.
6. Value Engineering:
Value engineering involves examining all aspects of the product and its production process to identify areas where costs can be reduced without compromising quality or functionality. This might involve using alternative materials, redesigning components, or optimizing production processes.
Analyzing Direct Material Costs: Tools and Techniques
Several tools and techniques can help analyze and manage direct material costs effectively:
-
Cost Accounting Systems: Implementing robust cost accounting systems is vital for accurately tracking and analyzing direct material costs. This involves using standard cost accounting, activity-based costing, or other suitable methods to track costs throughout the production process.
-
Variance Analysis: Regularly comparing actual costs to standard costs allows for the identification of variances, pinpointing areas where costs are higher than expected. This analysis helps identify areas for improvement and cost reduction.
-
Benchmarking: Comparing your direct material costs to industry benchmarks can help identify areas where your costs are higher than average, providing insights into potential cost-saving opportunities.
-
Data Analytics: Using data analytics tools to analyze large datasets of cost information can reveal hidden patterns and insights, leading to improved decision-making and more effective cost management.
Conclusion: The Importance of Direct Material Cost Management
Direct material costs represent a significant portion of the total cost of goods sold for many businesses. Therefore, effective management of these costs is critical for profitability and competitiveness. By understanding the different classifications of direct material costs and implementing the strategies and techniques discussed above, businesses can significantly reduce costs, improve efficiency, and enhance their overall profitability. Continuous monitoring, analysis, and adaptation are essential for maintaining a competitive edge in today's dynamic business environment. The ongoing pursuit of cost optimization in direct materials remains a key factor in the success and sustainability of any manufacturing or production-based enterprise.
Latest Posts
Latest Posts
-
The Progressive Movement Drew Its Strength From
May 29, 2025
-
Which Of These Are Networking Devices Choose All That Apply
May 29, 2025
-
Which Statement Is True Regarding Cost Cutting Proposals
May 29, 2025
-
Damage To The Corpora Quadrigemina Would Interfere With
May 29, 2025
-
According To The Atkinson Shiffrin Model
May 29, 2025
Related Post
Thank you for visiting our website which covers about The Costs Of Direct Materials Are Classified As . We hope the information provided has been useful to you. Feel free to contact us if you have any questions or need further assistance. See you next time and don't miss to bookmark.