The Amount Of Inspection Needed Depends On __________ And __________.
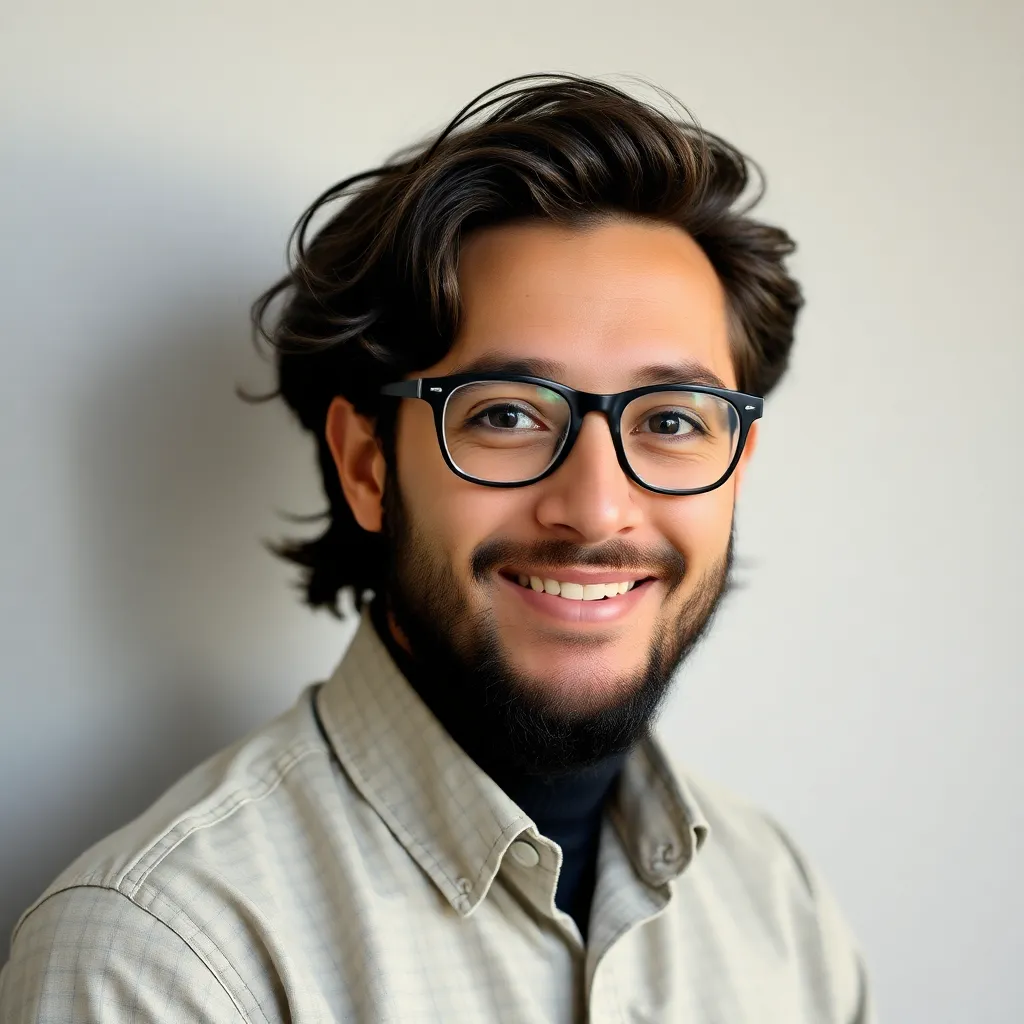
Juapaving
May 24, 2025 · 6 min read
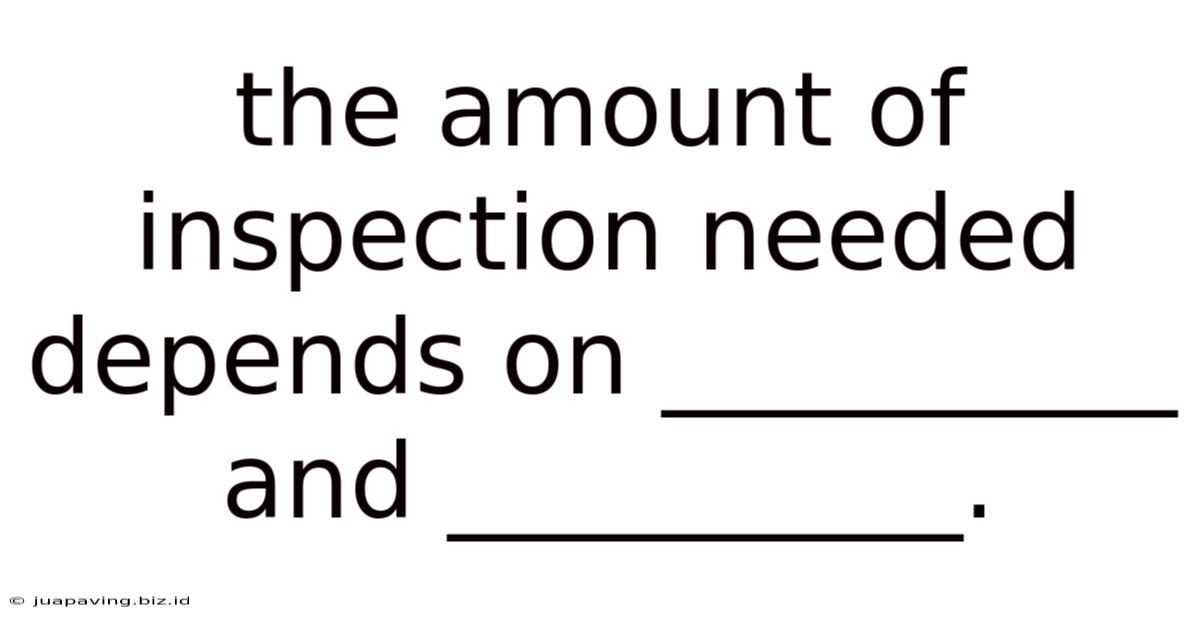
Table of Contents
The Amount of Inspection Needed Depends on Risk and Complexity
The amount of inspection required for any given project, process, or product isn't a fixed quantity. It's a dynamic variable directly influenced by two crucial factors: risk and complexity. Understanding and effectively managing these two elements is paramount to ensuring efficient, effective, and cost-effective inspection practices. This article delves into the intricate relationship between risk, complexity, and the level of inspection necessary, offering insights for various industries and scenarios.
Understanding the Risk Factor
Risk, in the context of inspection, refers to the potential for negative consequences if defects or non-conformances are not detected and rectified. These consequences can range widely, including:
Financial Losses:
- Product recalls: Faulty products reaching consumers can lead to significant financial losses from recall expenses, legal fees, and damage to brand reputation. Industries with high safety standards, such as pharmaceuticals and automotive, face particularly high financial risks.
- Warranty claims: Defects discovered after purchase can trigger warranty claims, impacting profitability and straining resources.
- Production downtime: Identifying problems late in the production process can necessitate expensive downtime for repairs and rework.
Safety and Health Risks:
- Injuries or fatalities: In industries dealing with hazardous materials or complex machinery, inadequate inspection can lead to serious injuries or fatalities, resulting in severe legal repercussions and ethical implications.
- Environmental damage: Failure to inspect properly can lead to environmental contamination, with associated cleanup costs and potential regulatory fines.
Reputational Damage:
- Loss of customer trust: Delivering substandard products or services severely damages a company's reputation, potentially leading to long-term market share loss.
- Negative publicity: Public exposure of safety breaches or quality issues can significantly harm brand image and public perception.
High-risk situations demand more rigorous inspection. This includes more frequent inspections, more thorough examination techniques, and potentially more stringent acceptance criteria. For instance, inspecting components used in aircraft manufacturing requires a much higher level of scrutiny than inspecting components for a simple toy. The potential consequences of failure are drastically different.
Decoding Complexity
Complexity, the second critical factor, encompasses various aspects influencing inspection needs:
Process Complexity:
- Number of steps: The more steps involved in a process, the greater the potential for errors to creep in. A highly automated process with numerous interconnected components might need more frequent monitoring than a simpler manual process.
- Interdependencies: Complex processes with tightly coupled steps mean that a failure in one area can cascade and impact other aspects. Thorough inspections are essential to identify these interdependencies and prevent cascading failures.
- Technological sophistication: Advanced technologies and automation increase process complexity, requiring specialized skills and techniques for effective inspection.
Product Complexity:
- Number of components: Products with numerous parts and intricate designs require a more detailed inspection process to ensure each component meets specifications.
- Material variety: Using diverse materials with varying properties adds to the complexity, demanding specific inspection methods for each material type.
- Design intricacy: Highly intricate designs with tight tolerances necessitate precise inspection tools and techniques to ensure adherence to specifications.
Complex processes and products mandate comprehensive inspection strategies. This may involve multiple inspection stages, utilizing advanced inspection technologies such as X-ray inspection, ultrasonic testing, or 3D scanning, alongside a highly skilled workforce. A simple, mass-produced item will demand less intricate inspection than a custom-designed piece of equipment.
The Interplay of Risk and Complexity
Risk and complexity are not independent variables; they interact and influence each other. A highly complex process with a high potential for safety risks (e.g., nuclear power plant operation) will necessitate an extremely rigorous and thorough inspection regime. Conversely, a simple process with low inherent risks (e.g., packaging consumer goods) may require less intensive inspection.
Here's a matrix illustrating the relationship:
Risk Level | Low Complexity | Medium Complexity | High Complexity |
---|---|---|---|
Low | Minimal inspection needed | Basic inspection sufficient | More frequent inspections |
Medium | Basic inspection sufficient | More thorough inspections | Comprehensive inspections |
High | More frequent inspections | Comprehensive inspections | Extremely rigorous inspections, potentially multiple stages |
This matrix is a guideline; the specific inspection strategy will always depend on the specifics of the situation. Factors such as regulatory requirements, historical data on defect rates, and the cost of inspection relative to the cost of failure all need to be considered.
Implementing Effective Inspection Strategies
The key to effective inspection is not simply increasing the amount of inspection indiscriminately but rather implementing a risk-based and targeted approach. Here are some crucial considerations:
- Risk Assessment: Conduct a thorough risk assessment to identify potential hazards and prioritize areas requiring the most attention.
- Inspection Planning: Develop a detailed inspection plan outlining the inspection methods, frequency, acceptance criteria, and personnel involved.
- Inspection Techniques: Choose appropriate inspection techniques based on the nature of the product or process and the identified risks. This might include visual inspection, dimensional measurements, non-destructive testing (NDT), or destructive testing.
- Data Analysis: Collect and analyze inspection data to identify trends, patterns, and potential root causes of defects. This data-driven approach allows for continuous improvement in the inspection process itself.
- Personnel Training: Ensure that inspection personnel are adequately trained and qualified to perform their tasks effectively.
- Documentation: Maintain detailed records of all inspections, including findings, corrective actions, and any deviations from the plan.
Case Studies: Illustrative Examples
Let's consider a few examples to illustrate how risk and complexity dictate the level of inspection:
Example 1: Food Processing Plant
A food processing plant faces moderate to high risk due to potential foodborne illnesses. The complexity can range from low (simple packaging) to high (complex automated production lines). A simple packaging line might require visual inspection and temperature checks, while a sophisticated automated line needs more frequent checks involving sensors, automated quality control systems, and microbiological testing.
Example 2: Aerospace Manufacturing
Aerospace manufacturing is characterized by extremely high risk, given the potential for catastrophic failure. The complexity is inherently high, with intricately designed components and stringent material specifications. This mandates rigorous inspections at every stage, utilizing advanced NDT techniques such as X-ray inspection, ultrasonic testing, and magnetic particle inspection. Detailed documentation and traceability are also crucial.
Example 3: Software Development
Software development poses unique challenges. Risk depends on the software's purpose (life-critical systems vs. simple applications) while complexity depends on the codebase size, architecture, and number of features. Simple applications might need basic testing, while critical systems require rigorous testing, code reviews, and security audits.
Conclusion
The amount of inspection needed is not arbitrary. It's a direct function of the inherent risks and the complexity of the process or product under consideration. A risk-based approach, incorporating thorough risk assessment, strategic planning, appropriate techniques, data analysis, and proper training, is essential for effective and efficient inspection. By understanding and managing these two critical factors—risk and complexity—organizations can optimize their inspection strategies, reducing costs, mitigating risks, and ensuring high quality and safety standards. The goal is not to inspect everything excessively, but to strategically focus inspection efforts where they matter most, thereby maximizing efficiency and effectiveness.
Latest Posts
Latest Posts
-
Which Of The Following Is True About Technology Certifications
May 24, 2025
-
Such As We Are Made Of Such We Be Meaning
May 24, 2025
-
Ap Classroom Unit 5 Progress Check Mcq
May 24, 2025
-
Ap World History Unit 3 Mcq
May 24, 2025
-
List Of Characters Midsummer Nights Dream
May 24, 2025
Related Post
Thank you for visiting our website which covers about The Amount Of Inspection Needed Depends On __________ And __________. . We hope the information provided has been useful to you. Feel free to contact us if you have any questions or need further assistance. See you next time and don't miss to bookmark.