Stress And Strain Graph For Steel
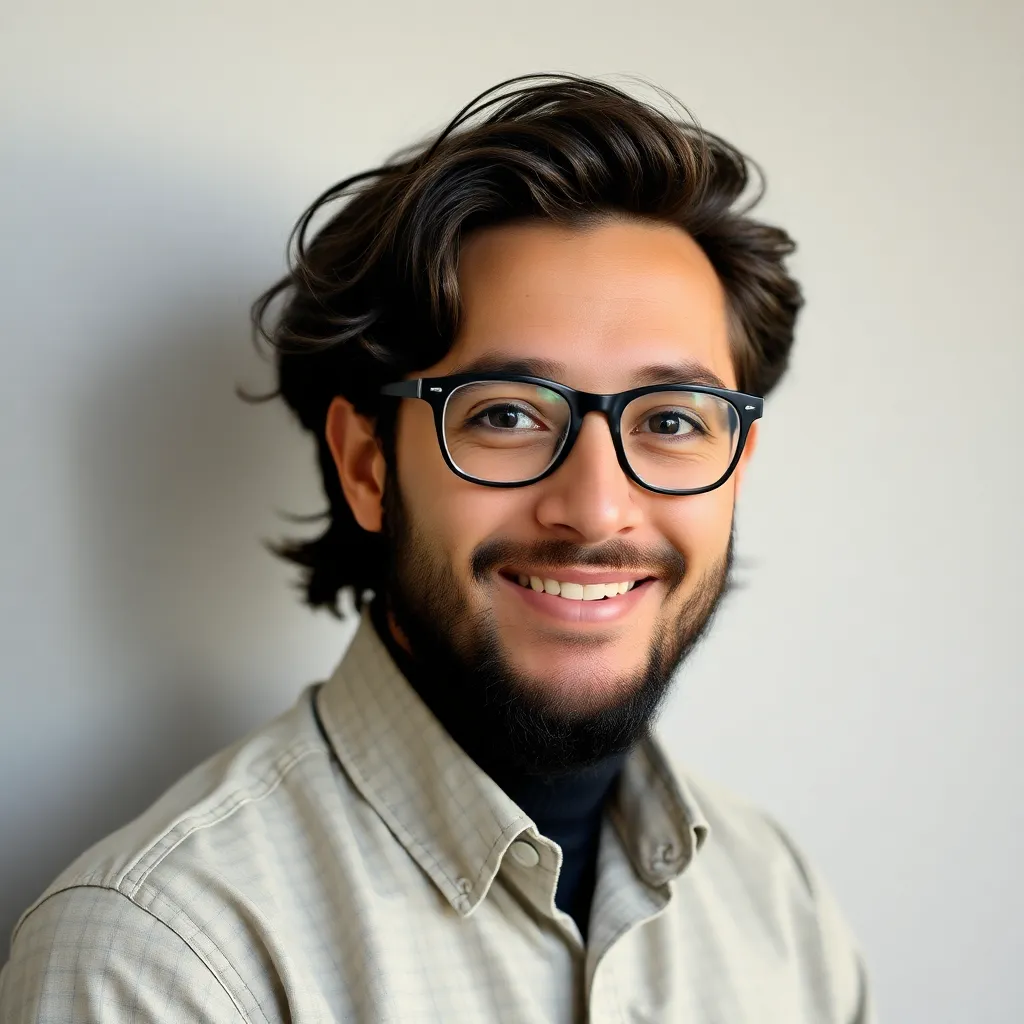
Juapaving
May 09, 2025 · 6 min read
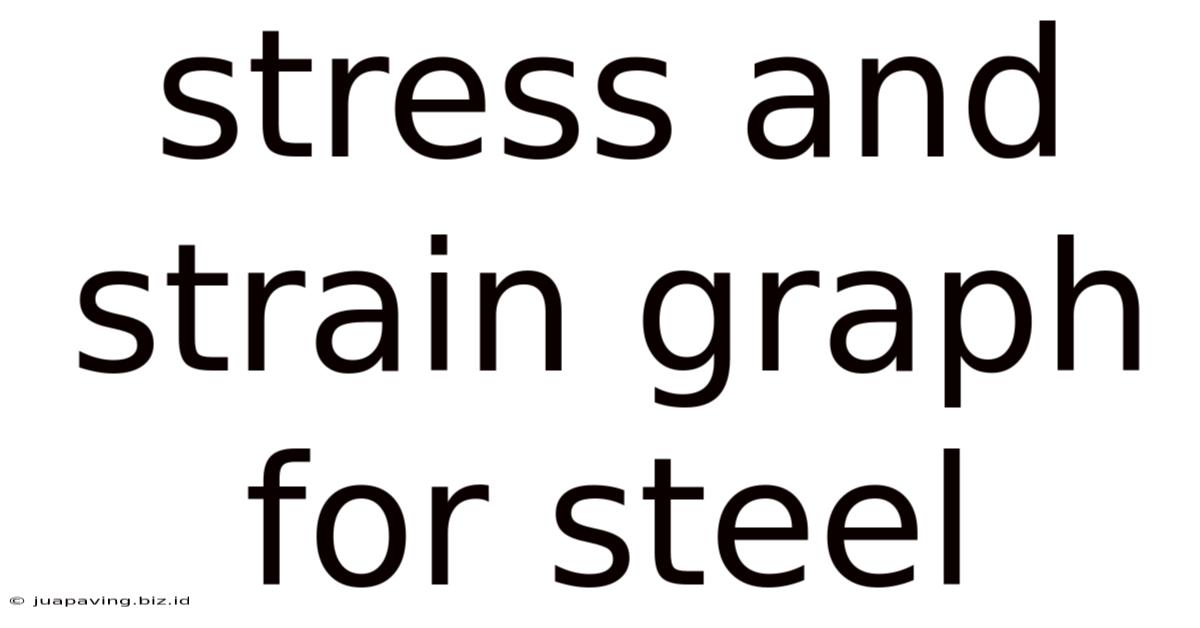
Table of Contents
Stress-Strain Graph for Steel: A Comprehensive Guide
Understanding the mechanical properties of steel is crucial in various engineering applications. One of the most effective ways to visualize these properties is through the stress-strain graph, also known as the tensile test curve. This comprehensive guide will delve into the intricacies of the stress-strain graph for steel, explaining its various regions, influencing factors, and practical implications.
Understanding Stress and Strain
Before diving into the graph itself, let's clarify the fundamental concepts of stress and strain.
Stress: The Force Applied
Stress is defined as the force applied per unit area of a material. It's a measure of the internal forces within the material resisting deformation. The formula for stress (σ) is:
σ = F/A
where:
- F represents the applied force (typically in Newtons)
- A represents the original cross-sectional area of the material (typically in square meters)
Stress is typically expressed in Pascals (Pa) or its multiples, such as megapascals (MPa).
Strain: The Resulting Deformation
Strain (ε) quantifies the deformation of a material under stress. It's a dimensionless quantity representing the change in length divided by the original length. The formula is:
ε = ΔL/L₀
where:
- ΔL represents the change in length
- L₀ represents the original length
Strain is a ratio and therefore has no units.
The Stress-Strain Curve for Mild Steel
The stress-strain curve for mild steel, a common type of steel, exhibits distinct regions reflecting its behavior under tensile loading. This curve is obtained experimentally through a tensile test, where a specimen is subjected to a gradually increasing tensile force until it fractures.
1. Elastic Region: Proportional Limit and Elastic Limit
The initial portion of the curve is the elastic region. In this region, the material behaves elastically, meaning it returns to its original shape once the load is removed. This region is characterized by a linear relationship between stress and strain, following Hooke's Law:
σ = Eε
where:
- E is Young's Modulus (or modulus of elasticity), a material constant representing the stiffness of the material.
Within the elastic region, we find two important points:
- Proportional Limit: The point up to which the stress-strain relationship is perfectly linear. Beyond this point, the relationship becomes non-linear, although the material still behaves elastically.
- Elastic Limit: The maximum stress a material can withstand without experiencing permanent deformation (plastic deformation). Beyond the elastic limit, some permanent deformation remains even after the load is removed.
2. Plastic Region: Yield Point, Yield Strength, and Strain Hardening
After the elastic limit, the material enters the plastic region. In this region, permanent deformation occurs. Key features of this region include:
- Yield Point: The point at which plastic deformation begins. Some materials exhibit a clear yield point, marked by a sudden drop in stress after the initial yield. Others show a gradual transition into the plastic region.
- Yield Strength: The stress at which a specified amount of permanent deformation (usually 0.2%) occurs. This is an important design parameter, as it represents the stress level beyond which permanent deformation is unacceptable.
- Strain Hardening (Work Hardening): As the material is deformed plastically, it becomes stronger and harder. This is reflected in the increasing slope of the curve in the plastic region. The increasing resistance to further deformation is known as strain hardening. This process involves dislocations in the material's crystal structure hindering their movement.
3. Ultimate Tensile Strength (UTS) and Necking
As the stress continues to increase, the material reaches its ultimate tensile strength (UTS), the maximum stress the material can withstand before it begins to neck.
- Necking: Necking refers to the localized reduction in cross-sectional area of the specimen. This phenomenon occurs due to the non-uniform distribution of stress within the material as it approaches failure. The reduction in cross-sectional area leads to an apparent decrease in stress, even though the load is still increasing.
4. Fracture Point
Finally, the material fractures at the fracture point. The stress at fracture is generally lower than the UTS.
Factors Influencing the Stress-Strain Curve
Several factors can significantly affect the stress-strain curve of steel:
- Carbon Content: Higher carbon content generally increases the strength and hardness but reduces the ductility of steel. This results in a steeper stress-strain curve with a higher UTS but lower elongation.
- Alloying Elements: Adding alloying elements like manganese, chromium, nickel, or molybdenum can alter the mechanical properties of steel, significantly influencing the shape of the stress-strain curve. These additions can increase strength, toughness, or corrosion resistance.
- Heat Treatment: Heat treatment processes, such as annealing, quenching, and tempering, can drastically change the microstructure and consequently the mechanical properties of steel. These processes affect the arrangement of carbon atoms within the steel's crystalline structure, altering the stress-strain response. Annealing will generally lead to a more ductile material, while quenching and tempering can significantly increase strength and hardness.
- Temperature: The temperature at which the tensile test is conducted has a profound influence on the material's behavior. Generally, higher temperatures lead to decreased strength and increased ductility.
- Strain Rate: The speed at which the load is applied also affects the stress-strain curve. Higher strain rates can lead to increased strength and reduced ductility.
Interpreting the Stress-Strain Curve: Practical Implications
The stress-strain curve provides critical information for engineers in designing and selecting materials for various applications. Key information derived from the curve includes:
- Young's Modulus (E): Represents the stiffness of the material. A higher Young's modulus indicates a stiffer material.
- Yield Strength: The maximum stress a material can withstand without permanent deformation. This is a crucial design parameter to prevent permanent deformation under operational loads.
- Ultimate Tensile Strength (UTS): Indicates the maximum stress a material can withstand before failure. This parameter is used to ensure the material can withstand the maximum anticipated loads during its service life.
- Ductility: Measured as elongation or reduction in area. Ductility indicates the material's ability to deform plastically before fracture. High ductility allows for greater deformation before failure.
- Toughness: A measure of the material's ability to absorb energy before fracture. It's related to the area under the stress-strain curve. High toughness indicates the ability to withstand impact loads.
Beyond Mild Steel: Stress-Strain Curves of Other Steels
While this guide focuses on mild steel, it’s essential to remember that different types of steel exhibit different stress-strain curves. High-strength low-alloy steels, stainless steels, and tool steels all possess unique characteristics reflected in their respective curves. These variations stem from differences in composition, microstructure, and processing techniques.
For example, high-strength low-alloy (HSLA) steels often demonstrate a higher yield strength and UTS compared to mild steel but may exhibit lower ductility. Stainless steels, known for their corrosion resistance, can display varying mechanical properties depending on their specific alloying composition. Tool steels, designed for high-temperature applications and machining, typically possess exceptional hardness and strength, resulting in unique stress-strain curves.
Conclusion
The stress-strain graph for steel is a powerful tool for understanding its mechanical behavior. By analyzing the different regions of the curve and considering the various factors influencing it, engineers can effectively select and utilize steel in a wide range of applications, ensuring structural integrity and optimal performance. This comprehensive understanding is crucial for designing safe and reliable structures and components across various industries. Further research into specific types of steel and their individual stress-strain characteristics is recommended for specialized applications. Understanding the interplay between material properties, processing techniques, and application requirements remains paramount in utilizing steel's potential effectively.
Latest Posts
Latest Posts
-
Compare Light Microscope And Electron Microscope
May 11, 2025
-
Which Graph Shows An Even Function
May 11, 2025
-
Which Of The Following Em Waves Has The Highest Frequency
May 11, 2025
-
Find The Area Of The Irregular Figure
May 11, 2025
-
Whats A 6 Out Of 8
May 11, 2025
Related Post
Thank you for visiting our website which covers about Stress And Strain Graph For Steel . We hope the information provided has been useful to you. Feel free to contact us if you have any questions or need further assistance. See you next time and don't miss to bookmark.