Schedule For Cost Of Goods Manufactured
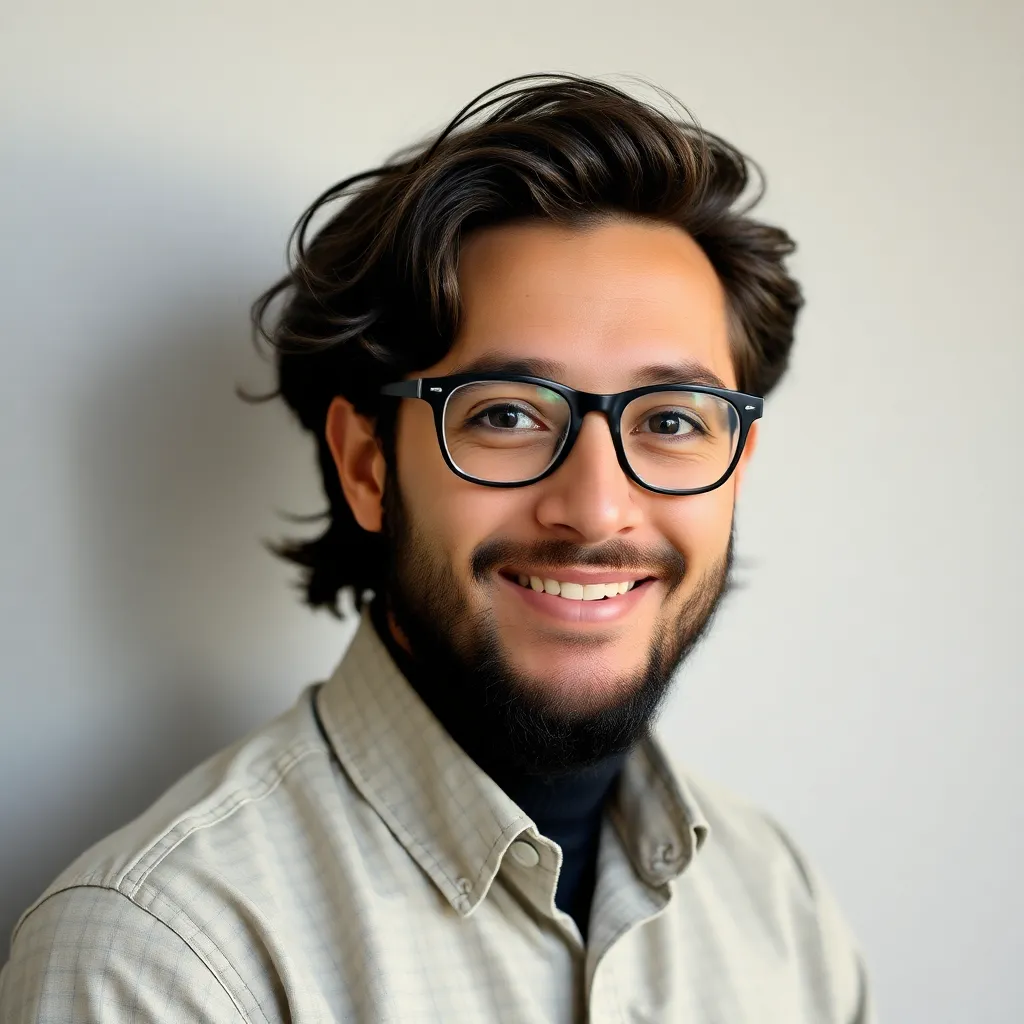
Juapaving
May 23, 2025 · 6 min read
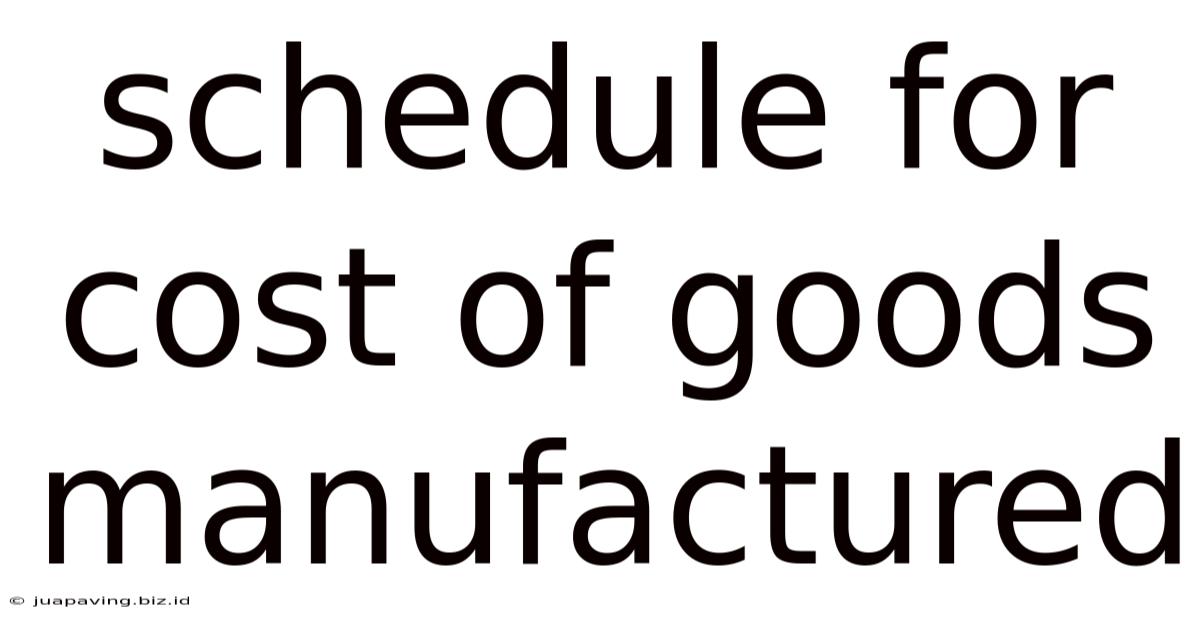
Table of Contents
A Comprehensive Schedule for Cost of Goods Manufactured (COGM)
The Cost of Goods Manufactured (COGM) schedule is a crucial financial statement for manufacturing businesses. It details the total cost of producing finished goods during a specific period. Understanding and accurately preparing this schedule is essential for accurate financial reporting, effective cost management, and informed decision-making. This comprehensive guide will delve into the intricacies of creating a COGM schedule, exploring its components, variations, and its importance in financial analysis.
Understanding the Components of a COGM Schedule
The COGM schedule meticulously tracks the flow of costs throughout the manufacturing process. It aggregates direct and indirect costs to arrive at the total cost of goods manufactured. Key components include:
1. Beginning Work-in-Process (WIP) Inventory:
This represents the cost of partially completed goods at the beginning of the accounting period. It includes direct materials, direct labor, and manufacturing overhead already applied to these unfinished goods. Accurately valuing beginning WIP inventory is paramount for an accurate COGM calculation. Any discrepancies here will propagate through the entire schedule.
2. Direct Materials Used:
This encompasses the raw materials directly consumed in the production process. The calculation typically involves:
- Beginning Raw Materials Inventory: The value of raw materials on hand at the start of the period.
- Purchases of Raw Materials: The cost of all raw materials acquired during the period.
- Ending Raw Materials Inventory: The value of raw materials remaining at the period's end.
The formula is: Beginning Raw Materials Inventory + Purchases – Ending Raw Materials Inventory = Direct Materials Used. Proper inventory management and accurate costing methods are crucial for determining direct materials used.
3. Direct Labor:
Direct labor represents the wages and benefits paid to workers directly involved in the manufacturing process. This includes the salaries and wages of assembly line workers, machine operators, and other personnel directly contributing to production. Accurate tracking of labor hours and associated costs is essential.
4. Manufacturing Overhead:
Manufacturing overhead comprises all indirect costs associated with production. These costs are not easily traceable to specific products but are necessary for the manufacturing process. Examples include:
- Indirect Labor: Salaries of factory supervisors, maintenance personnel, and quality control inspectors.
- Factory Rent and Utilities: Costs associated with the factory building and its utilities.
- Depreciation of Factory Equipment: The allocation of the cost of factory equipment over its useful life.
- Factory Supplies: The cost of consumables used in the factory, such as lubricants and cleaning supplies.
- Insurance and Property Taxes: Costs associated with factory insurance and property taxes.
Careful allocation of overhead costs is critical for accurate COGM calculation. Common methods include the predetermined overhead rate, which uses a predetermined percentage to allocate overhead based on a chosen allocation base (such as direct labor hours or machine hours).
Calculating the Cost of Goods Manufactured
Once the above components are determined, the COGM is calculated as follows:
Beginning Work-in-Process Inventory + Direct Materials Used + Direct Labor + Manufacturing Overhead – Ending Work-in-Process Inventory = Cost of Goods Manufactured
This equation demonstrates the flow of costs through the manufacturing process. The beginning WIP inventory is added to the current period's costs, and the ending WIP inventory is subtracted to arrive at the cost of goods that were completed during the period.
The COGM Schedule: A Detailed Example
Let's illustrate with a numerical example:
Company X – COGM Schedule for the Year Ended December 31, 2024
Item | Amount |
---|---|
Beginning Work-in-Process Inventory | $10,000 |
Direct Materials: | |
Beginning Raw Materials Inventory | $5,000 |
Purchases of Raw Materials | $25,000 |
Ending Raw Materials Inventory | $7,000 |
Direct Materials Used | $23,000 |
Direct Labor | $30,000 |
Manufacturing Overhead: | |
Indirect Labor | $8,000 |
Factory Rent | $5,000 |
Depreciation of Factory Equipment | $3,000 |
Factory Supplies | $2,000 |
Total Manufacturing Overhead | $18,000 |
Total Manufacturing Costs | $71,000 |
Ending Work-in-Process Inventory | $12,000 |
Cost of Goods Manufactured (COGM) | $69,000 |
This example demonstrates a clear and organized presentation of the COGM calculation. Each component is clearly identified, and the calculations are straightforward.
Variations in COGM Schedules
The structure of the COGM schedule might vary slightly depending on the complexity of the manufacturing process and the accounting methods used. Some variations include:
- Job Order Costing: This method tracks costs for individual jobs or projects. The COGM schedule will reflect the costs associated with each completed job.
- Process Costing: This method averages costs across a large volume of identical products. The COGM schedule will show the total cost of production for a specific period.
- Activity-Based Costing (ABC): This more sophisticated method allocates overhead costs based on activities that consume resources. This often leads to a more accurate cost allocation, particularly in complex manufacturing environments.
Regardless of the specific costing method employed, the fundamental principles underlying the COGM schedule remain consistent.
Importance of the COGM Schedule in Financial Analysis
The COGM schedule is not merely a bookkeeping exercise; it serves several crucial purposes in financial analysis:
- Cost Control and Efficiency: By analyzing the components of the COGM, management can identify areas for cost reduction and process improvement. Understanding the cost drivers helps in optimizing production efficiency.
- Inventory Valuation: The COGM schedule contributes to the accurate valuation of finished goods inventory. This accurate valuation is essential for accurate financial reporting and compliance with accounting standards.
- Profitability Analysis: The COGM is a crucial component in calculating the cost of goods sold (COGS), which is then used to determine gross profit and ultimately net income. Accurate COGM figures are therefore essential for meaningful profitability analysis.
- Pricing Decisions: Understanding the cost structure of production helps in making informed pricing decisions. Analyzing COGM data can guide strategies for competitive pricing and maximizing profit margins.
- Performance Evaluation: The COGM schedule provides valuable data for evaluating the performance of the manufacturing process and identifying areas needing improvement.
Advanced Considerations and Best Practices
- Accurate Cost Allocation: The accuracy of the COGM schedule heavily depends on the accuracy of cost allocation. A robust cost accounting system is crucial for accurate tracking and allocation of costs.
- Regular Reconciliation: Regular reconciliation of the COGM schedule with physical inventory counts helps in identifying discrepancies and ensuring accuracy.
- Technological Advancements: Utilizing ERP (Enterprise Resource Planning) systems and other technological tools can significantly improve the efficiency and accuracy of COGM calculations.
- Internal Controls: Establishing strong internal controls helps in preventing errors and fraud, ensuring the reliability of the COGM data.
- Compliance with Accounting Standards: The COGM schedule must comply with relevant accounting standards (e.g., Generally Accepted Accounting Principles (GAAP) or International Financial Reporting Standards (IFRS)).
Conclusion
The Cost of Goods Manufactured schedule is a cornerstone of manufacturing financial reporting. It provides crucial insights into production costs, enabling effective cost management, informed decision-making, and accurate financial reporting. By understanding its components, variations, and importance in financial analysis, manufacturing businesses can leverage this powerful tool to enhance their profitability and operational efficiency. Implementing best practices and utilizing technological advancements will further strengthen the accuracy and reliability of the COGM schedule, leading to better financial reporting and overall business success. Remember that continuous monitoring and improvement of the process are key to maximizing the benefits of this crucial financial statement.
Latest Posts
Latest Posts
-
Which Of The Following Exemplifies The Hawthorne Effect
May 23, 2025
-
Assume Gadgets Are Sold In A Competitive Market
May 23, 2025
-
How Many Wives Does Okonkwo Have
May 23, 2025
-
7 2 10 Packet Tracer Configure Dhcpv4
May 23, 2025
-
Hands On Large Language Models Pdf Free
May 23, 2025
Related Post
Thank you for visiting our website which covers about Schedule For Cost Of Goods Manufactured . We hope the information provided has been useful to you. Feel free to contact us if you have any questions or need further assistance. See you next time and don't miss to bookmark.