Production Costs Of A Firm Quick Check
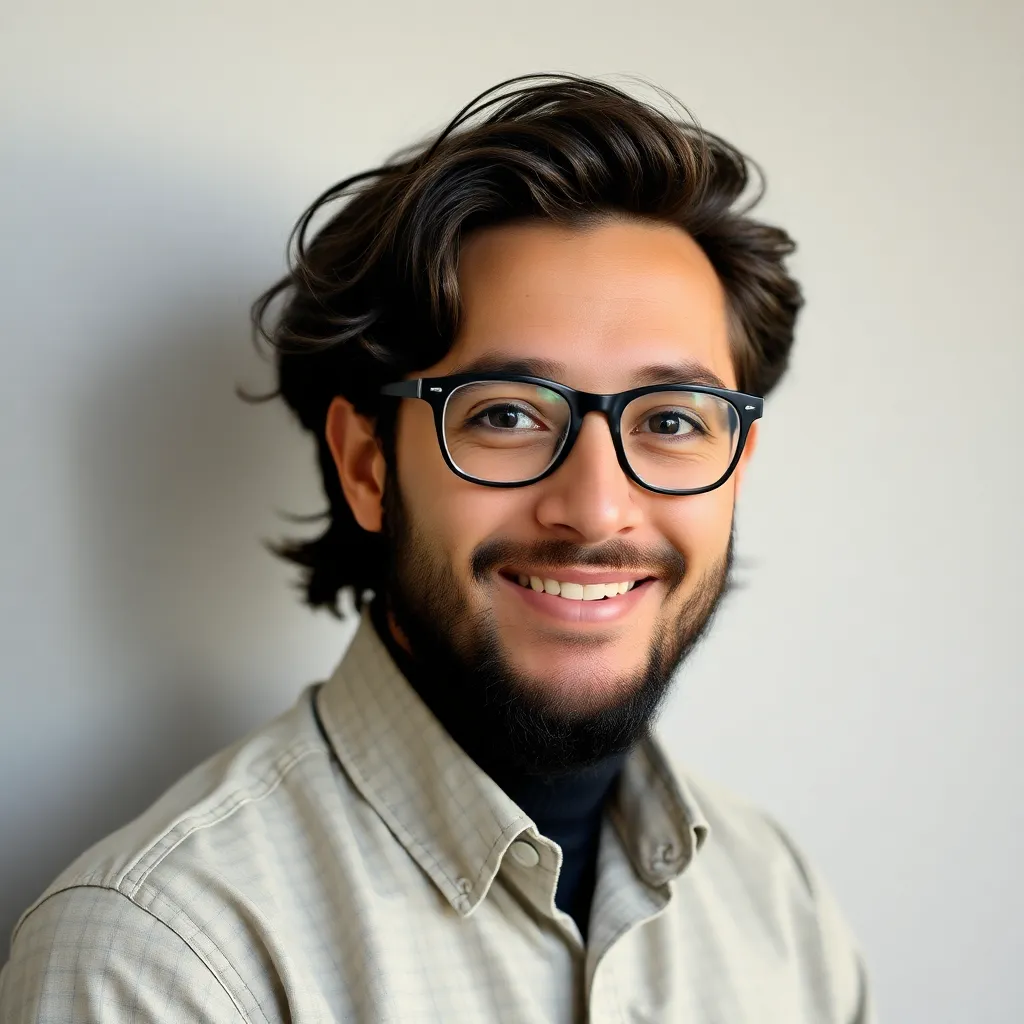
Juapaving
May 24, 2025 · 6 min read
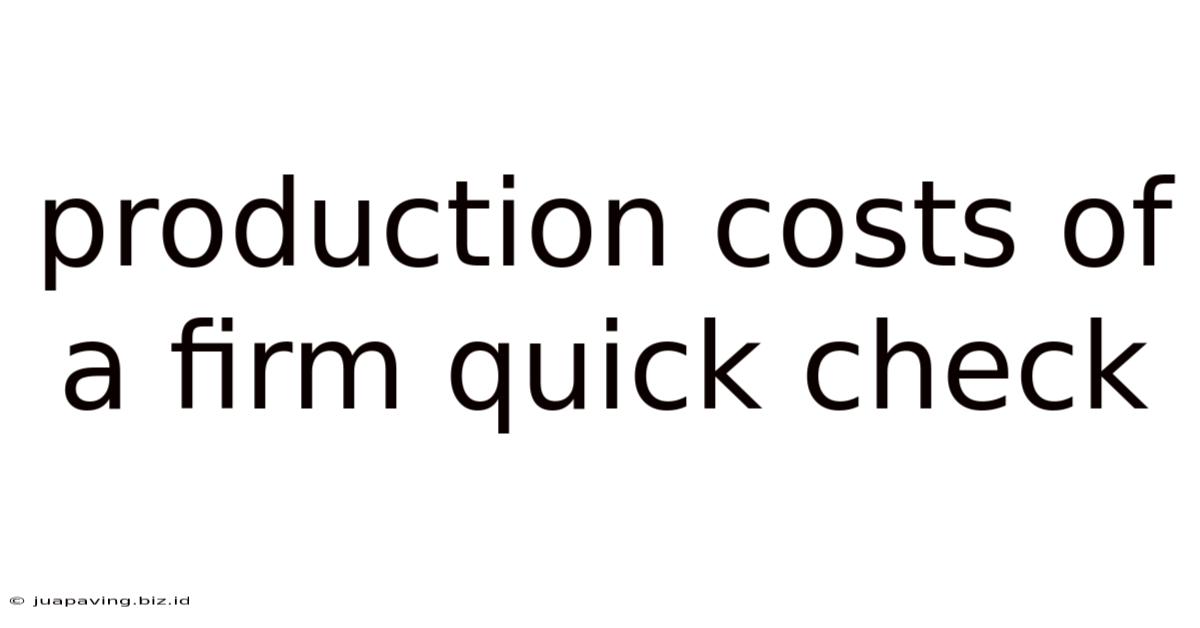
Table of Contents
Production Costs of a Firm: A Quick Check
Understanding production costs is crucial for any firm's success. Profitability hinges on effectively managing these costs, ensuring prices are competitive while maintaining healthy margins. This comprehensive guide provides a quick check of the key components of production costs, helping you analyze your firm's efficiency and identify areas for potential improvement. We'll delve into various cost classifications, their calculations, and their impact on decision-making.
Defining Production Costs
Production costs represent the total expenses incurred in producing goods or services. These costs are directly tied to the volume of output, meaning higher production generally leads to higher costs (although economies of scale can sometimes mitigate this). Understanding these costs is fundamental for pricing strategies, profit projections, and overall business planning.
Key Categories of Production Costs
Production costs are broadly categorized into several key areas:
-
Direct Costs: These costs are directly attributable to the production of goods or services. They are easily traceable to specific products or units.
-
Direct Materials: The raw materials and components directly used in the production process. This includes everything from raw cotton for a textile manufacturer to microchips for a computer company. Accurate tracking of direct materials is essential for inventory control and cost accounting.
-
Direct Labor: The wages and salaries paid to employees directly involved in the production process. This includes assembly line workers, machine operators, and other personnel whose time can be directly linked to specific products. Calculating direct labor costs often involves tracking hours worked and paying appropriate wages, including overtime.
-
-
Indirect Costs (Overhead Costs): These costs are not directly traceable to a specific product but are essential for the overall production process. They are often allocated to products based on a predetermined method.
-
Manufacturing Overhead: This encompasses various costs related to the production facility and its operation. It typically includes:
- Rent or mortgage payments for the factory: A significant fixed cost.
- Utilities (electricity, gas, water): These can vary depending on production levels.
- Depreciation of equipment: The allocation of the cost of equipment over its useful life.
- Factory maintenance and repairs: Keeping the facility operational.
- Factory supplies: Consumables used in production but not directly incorporated into the product.
- Indirect labor: Salaries of supervisors, quality control personnel, and other support staff.
-
Administrative Overhead: Costs associated with managing the overall business, including salaries of administrative staff, office rent, and general administrative expenses. While not directly related to production, these are still crucial for the smooth functioning of the firm.
-
Selling and Distribution Overhead: Costs related to marketing, sales, and distribution of the finished products. This includes advertising, sales commissions, shipping, and warehousing.
-
Calculating Production Costs
Accurately calculating production costs is vital for informed decision-making. Different methods exist depending on the complexity of the production process and the level of detail required.
1. Job Order Costing:
This method is suitable for businesses producing unique or customized products, where costs are tracked for each individual job or project. For example, a construction company might use job order costing to track the costs of building a specific house. It provides a detailed breakdown of costs associated with each job, facilitating accurate pricing and performance evaluation.
2. Process Costing:
Process costing is employed when producing large volumes of homogeneous products. The total production cost is divided by the number of units produced to determine the cost per unit. This method is commonly used in industries like food processing and chemical manufacturing where products are largely identical. It provides a simpler cost calculation than job order costing.
3. Activity-Based Costing (ABC):
ABC is a more sophisticated approach that assigns costs based on activities involved in production. It recognizes that overhead costs are not always directly proportional to production volume. ABC identifies cost drivers, which are activities that cause costs to be incurred. It then allocates overhead costs based on the consumption of these cost drivers. This provides a more accurate picture of the cost of each product, particularly in industries with diverse product lines.
Analyzing Production Costs: Key Metrics
Several key metrics help analyze production costs and identify areas for improvement:
-
Cost of Goods Sold (COGS): This represents the direct costs associated with producing goods sold during a specific period. It includes direct materials, direct labor, and manufacturing overhead. COGS is crucial for calculating gross profit and assessing the profitability of sales.
-
Unit Cost: The total cost of producing one unit of a product. This is calculated by dividing the total production cost by the number of units produced. Analyzing unit costs over time can reveal trends and help identify cost-saving opportunities.
-
Break-Even Point: The level of production where total revenue equals total costs (both fixed and variable). This metric helps determine the minimum sales volume needed to avoid losses.
-
Contribution Margin: The difference between revenue and variable costs. It represents the amount of revenue available to cover fixed costs and contribute to profit. A high contribution margin indicates better profitability.
-
Marginal Cost: The cost of producing one additional unit of a product. Understanding marginal cost is critical for making short-term production decisions, such as deciding whether to accept a special order.
Factors Affecting Production Costs
Various factors influence a firm's production costs:
-
Input Prices: Fluctuations in the prices of raw materials, labor, and energy significantly impact production costs. Hedging strategies or long-term contracts can mitigate these risks.
-
Technology and Automation: Investing in advanced technology and automation can improve efficiency, reduce labor costs, and improve product quality, ultimately lowering production costs.
-
Production Volume: Economies of scale can reduce unit costs at higher production volumes, but beyond a certain point, diseconomies of scale might set in due to inefficiencies.
-
Production Process Efficiency: Streamlining production processes, minimizing waste, and improving workflow can significantly reduce costs. Lean manufacturing principles can be implemented to optimize efficiency.
-
Location: The geographic location of the production facility impacts costs, considering factors like rent, labor costs, and transportation expenses.
-
Government Regulations and Taxes: Compliance with environmental regulations and paying various taxes can influence production costs.
Reducing Production Costs: Strategies and Best Practices
Lowering production costs without compromising quality is essential for maintaining competitiveness. Here are some strategies:
-
Negotiate with Suppliers: Secure better pricing for raw materials by negotiating with suppliers and exploring alternative sources.
-
Improve Inventory Management: Optimize inventory levels to avoid holding costs while ensuring sufficient materials for production. Just-in-time (JIT) inventory systems can help minimize inventory.
-
Enhance Production Processes: Implement lean manufacturing principles to eliminate waste and improve efficiency in the production process.
-
Invest in Technology: Utilize technology for automation and improved efficiency, reducing labor costs and improving quality.
-
Employee Training and Development: Invest in training and development programs to enhance employee skills, productivity, and reduce errors.
-
Regular Cost Analysis: Conduct regular cost analysis to monitor expenses, identify cost drivers, and take corrective actions.
Conclusion: Continuous Monitoring and Improvement
Successfully managing production costs requires continuous monitoring and improvement. By understanding the various cost categories, calculating costs accurately, and utilizing appropriate cost analysis metrics, firms can make informed decisions to optimize their operations, enhance profitability, and maintain a competitive edge. Regular review, adaptation to market conditions, and a commitment to efficiency are essential for long-term success. This quick check serves as a foundational understanding; further in-depth analysis specific to your industry and business model is always recommended. Consider consulting with financial professionals for tailored advice and strategy development.
Latest Posts
Latest Posts
-
How Does Odysseus Change Throughout The Odyssey
May 24, 2025
-
Nadeen Runs A Website On Vegan Lifestyle
May 24, 2025
-
Mrs Allen Has A Rare Condition
May 24, 2025
-
In The Fifth Paragraph The Author Mentions That She
May 24, 2025
-
Consider Your Knowledge About The Cell Membrane
May 24, 2025
Related Post
Thank you for visiting our website which covers about Production Costs Of A Firm Quick Check . We hope the information provided has been useful to you. Feel free to contact us if you have any questions or need further assistance. See you next time and don't miss to bookmark.