Prepare Schedule Of Cost Of Goods Manufactured
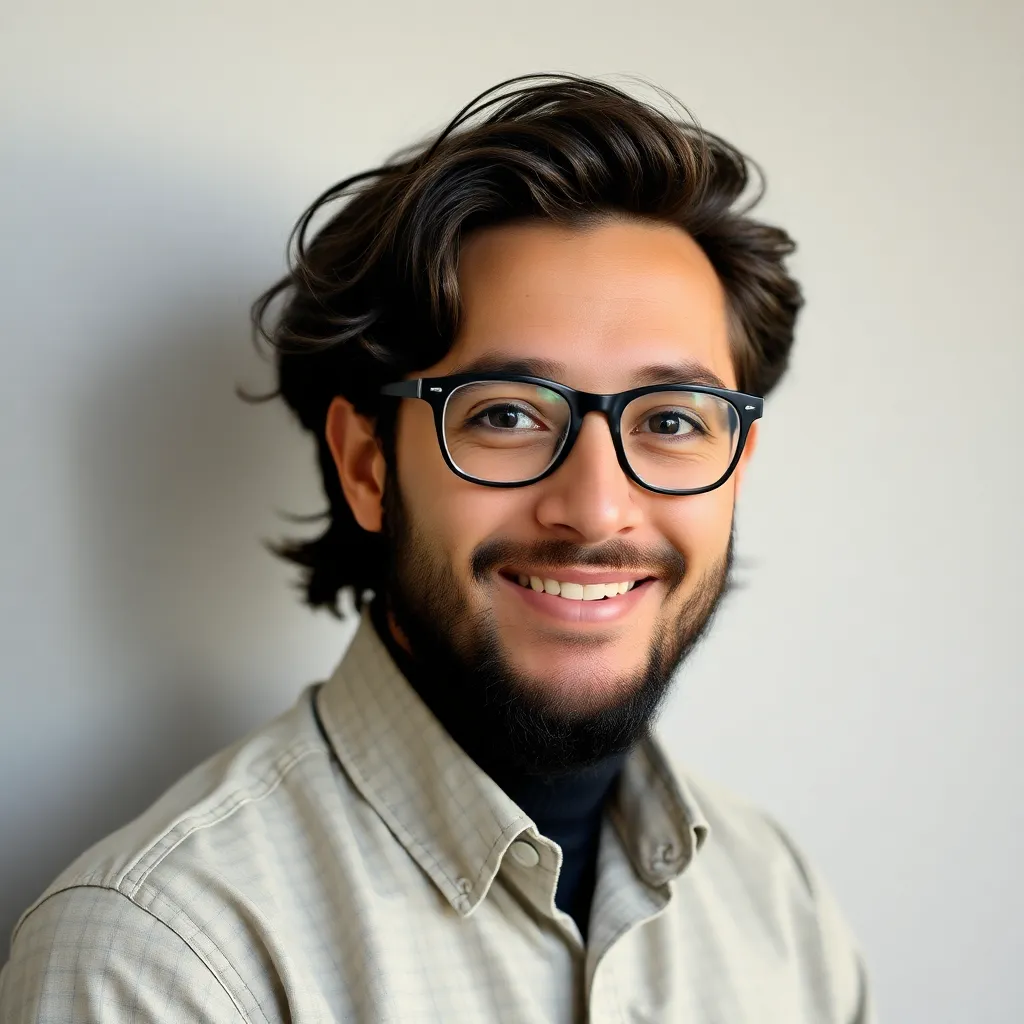
Juapaving
May 25, 2025 · 6 min read
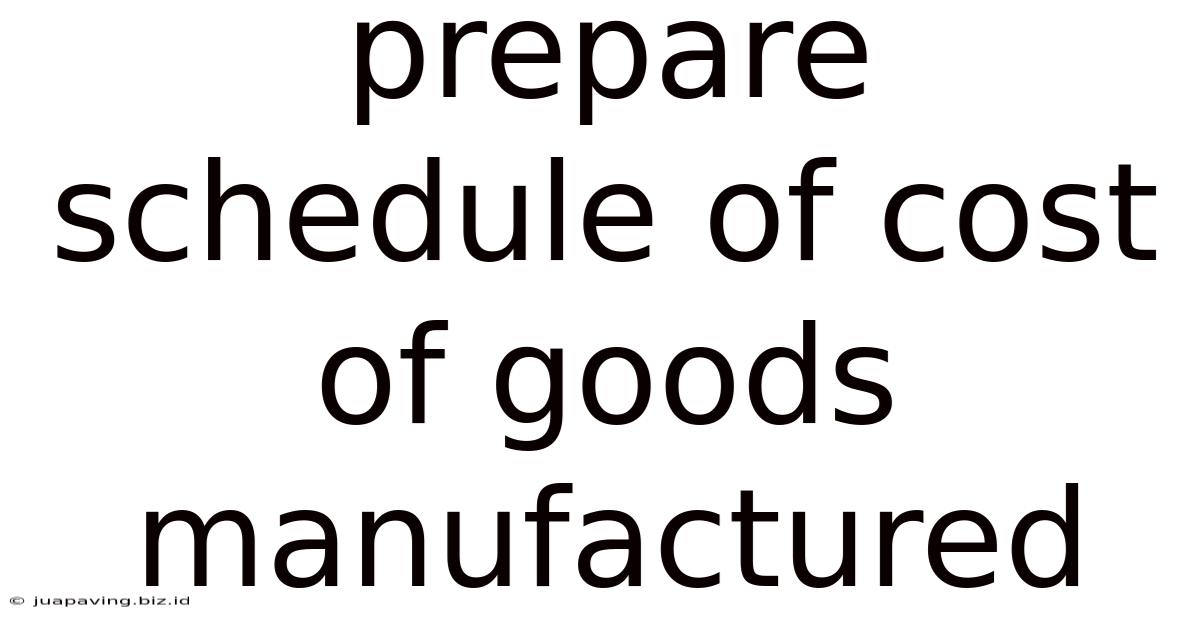
Table of Contents
Preparing a Schedule of Cost of Goods Manufactured (COGM)
The Schedule of Cost of Goods Manufactured (COGM) is a crucial financial statement that details the total cost of producing finished goods during a specific period. Understanding and accurately preparing this schedule is vital for businesses, particularly manufacturers, to determine profitability, manage inventory, and make informed business decisions. This comprehensive guide will walk you through the process of preparing a COGM schedule, explaining each component in detail and offering practical examples. We'll also delve into its importance in financial reporting and analysis.
Understanding the Components of COGM
Before diving into the preparation, let's understand the key components that constitute the cost of goods manufactured:
1. Direct Materials
These are raw materials directly used in the production process and can be easily traced to the finished product. Examples include:
- Raw materials: Wood for furniture, steel for automobiles, fabric for clothing.
- Directly attributable costs: Freight costs directly related to transporting raw materials to the production facility.
Calculating Direct Materials Used:
This involves determining the beginning inventory of raw materials, adding purchases during the period, and subtracting the ending inventory of raw materials. The formula is:
Beginning Raw Materials Inventory + Purchases - Ending Raw Materials Inventory = Direct Materials Used
2. Direct Labor
This represents the wages and benefits paid to workers directly involved in the manufacturing process. This includes the salaries and benefits of:
- Production line workers: Assembling products, operating machinery.
- Quality control inspectors: Ensuring product quality.
Calculating Direct Labor Costs:
Direct labor costs are relatively straightforward to calculate; they simply represent the total wages and benefits paid to production workers during the period.
3. Manufacturing Overhead
This encompasses all indirect costs associated with the production process that cannot be easily traced to a specific product. This includes:
- Indirect labor: Salaries of supervisors, maintenance personnel, and factory security.
- Factory rent and utilities: Costs associated with the factory space.
- Depreciation on factory equipment: Allocation of the cost of factory equipment over its useful life.
- Factory supplies: Lubricants, cleaning supplies, and other consumables used in the factory.
- Insurance on factory property: Premiums paid for insuring factory buildings and equipment.
Calculating Manufacturing Overhead:
This is often calculated using predetermined overhead rates, which allocate overhead costs based on a chosen allocation base (e.g., machine hours, direct labor hours). The formula is:
Predetermined Overhead Rate x Actual Allocation Base = Applied Manufacturing Overhead
Note that there will often be a difference between applied manufacturing overhead and actual manufacturing overhead. This difference is often reported as an over- or under-applied overhead and is adjusted at the end of the accounting period.
Preparing the Schedule of Cost of Goods Manufactured
Now let's move on to the actual preparation of the COGM schedule. A typical COGM schedule includes the following sections:
1. Direct Materials:
- Beginning Raw Materials Inventory: [Amount]
- Add: Purchases of Raw Materials: [Amount]
- Raw Materials Available for Use: [Sum of Beginning Inventory and Purchases]
- Less: Ending Raw Materials Inventory: [Amount]
- Direct Materials Used in Production: [Difference between Raw Materials Available for Use and Ending Inventory]
2. Direct Labor: [Amount]
3. Manufacturing Overhead:
- Indirect Labor: [Amount]
- Factory Rent: [Amount]
- Utilities: [Amount]
- Depreciation: [Amount]
- Factory Supplies: [Amount]
- Insurance: [Amount]
- Total Manufacturing Overhead: [Sum of all overhead costs]
4. Total Manufacturing Costs:
- Direct Materials Used: [Amount from Section 1]
- Direct Labor: [Amount from Section 2]
- Manufacturing Overhead: [Amount from Section 3]
- Total Manufacturing Costs: [Sum of Direct Materials Used, Direct Labor, and Manufacturing Overhead]
5. Cost of Goods Manufactured:
- Beginning Work in Process (WIP) Inventory: [Amount]
- Add: Total Manufacturing Costs: [Amount from Section 4]
- Total Cost of Work in Process: [Sum of Beginning WIP Inventory and Total Manufacturing Costs]
- Less: Ending Work in Process (WIP) Inventory: [Amount]
- Cost of Goods Manufactured: [Difference between Total Cost of Work in Process and Ending WIP Inventory]
Example: Preparing a COGM Schedule
Let's illustrate this with a hypothetical example:
Direct Materials:
- Beginning Raw Materials Inventory: $10,000
- Purchases of Raw Materials: $50,000
- Raw Materials Available for Use: $60,000
- Ending Raw Materials Inventory: $12,000
- Direct Materials Used in Production: $48,000
Direct Labor: $30,000
Manufacturing Overhead:
- Indirect Labor: $5,000
- Factory Rent: $10,000
- Utilities: $3,000
- Depreciation: $7,000
- Factory Supplies: $2,000
- Insurance: $3,000
- Total Manufacturing Overhead: $30,000
Total Manufacturing Costs:
- Direct Materials Used: $48,000
- Direct Labor: $30,000
- Manufacturing Overhead: $30,000
- Total Manufacturing Costs: $108,000
Cost of Goods Manufactured:
- Beginning Work in Process (WIP) Inventory: $8,000
- Add: Total Manufacturing Costs: $108,000
- Total Cost of Work in Process: $116,000
- Less: Ending Work in Process (WIP) Inventory: $6,000
- Cost of Goods Manufactured: $110,000
Importance of the COGM Schedule
The COGM schedule is essential for several reasons:
- Determining Cost of Goods Sold (COGS): The COGM is a key input in calculating the cost of goods sold, a crucial figure on the income statement. Knowing the COGS is vital for accurate profit determination.
- Inventory Valuation: The schedule helps in accurately valuing inventory, ensuring compliance with generally accepted accounting principles (GAAP). Accurate inventory valuation prevents misstatements in financial reports.
- Performance Evaluation: Analyzing the COGM allows businesses to assess the efficiency of their production processes and identify areas for improvement. This can help in cost reduction and increased profitability.
- Pricing Decisions: Understanding the cost of manufacturing each product is vital for setting competitive prices that ensure profitability.
- Budgeting and Forecasting: The COGM schedule provides valuable data for budgeting and forecasting future production costs. This supports sound financial planning and decision-making.
Potential Challenges and Considerations
While preparing a COGM schedule is straightforward in principle, certain challenges might arise:
- Accurate Cost Allocation: Accurately assigning costs to direct materials, direct labor, and manufacturing overhead can be challenging, especially in complex manufacturing environments. Careful cost accounting practices are crucial.
- Inventory Management: Maintaining accurate records of beginning and ending inventories of raw materials and work in process is essential for accurate calculations. Robust inventory tracking systems are necessary.
- Overhead Allocation: Choosing the appropriate allocation base for overhead costs and determining the overhead rate requires careful consideration. The selected method should accurately reflect the relationship between overhead costs and production volume.
- Variations in Production Processes: Businesses with diverse and complex production processes may face added complexities in cost allocation and tracking.
Conclusion
The Schedule of Cost of Goods Manufactured is a fundamental financial statement for manufacturers. Understanding its components, preparing it accurately, and analyzing the resulting data are essential for effective cost management, accurate financial reporting, and informed business decision-making. By implementing robust inventory tracking systems, employing careful cost allocation methods, and regularly reviewing the COGM schedule, businesses can leverage this valuable tool to optimize their operations and enhance their financial performance. This detailed guide provides a strong foundation for navigating the intricacies of COGM preparation and utilization. Remember to consult with accounting professionals for guidance tailored to your specific business needs and complexities.
Latest Posts
Latest Posts
-
Characters In Last Of The Mohicans
May 25, 2025
-
Summary Of Part 3 Of The Book Thief
May 25, 2025
-
All Of The Following Statements Concerning Dividends Are True Except
May 25, 2025
-
Review Sheet Exercise 6 Classification Of Tissues
May 25, 2025
-
Slim Description Of Mice And Men
May 25, 2025
Related Post
Thank you for visiting our website which covers about Prepare Schedule Of Cost Of Goods Manufactured . We hope the information provided has been useful to you. Feel free to contact us if you have any questions or need further assistance. See you next time and don't miss to bookmark.