Polar Moment Of Inertia Of Hollow Cylinder
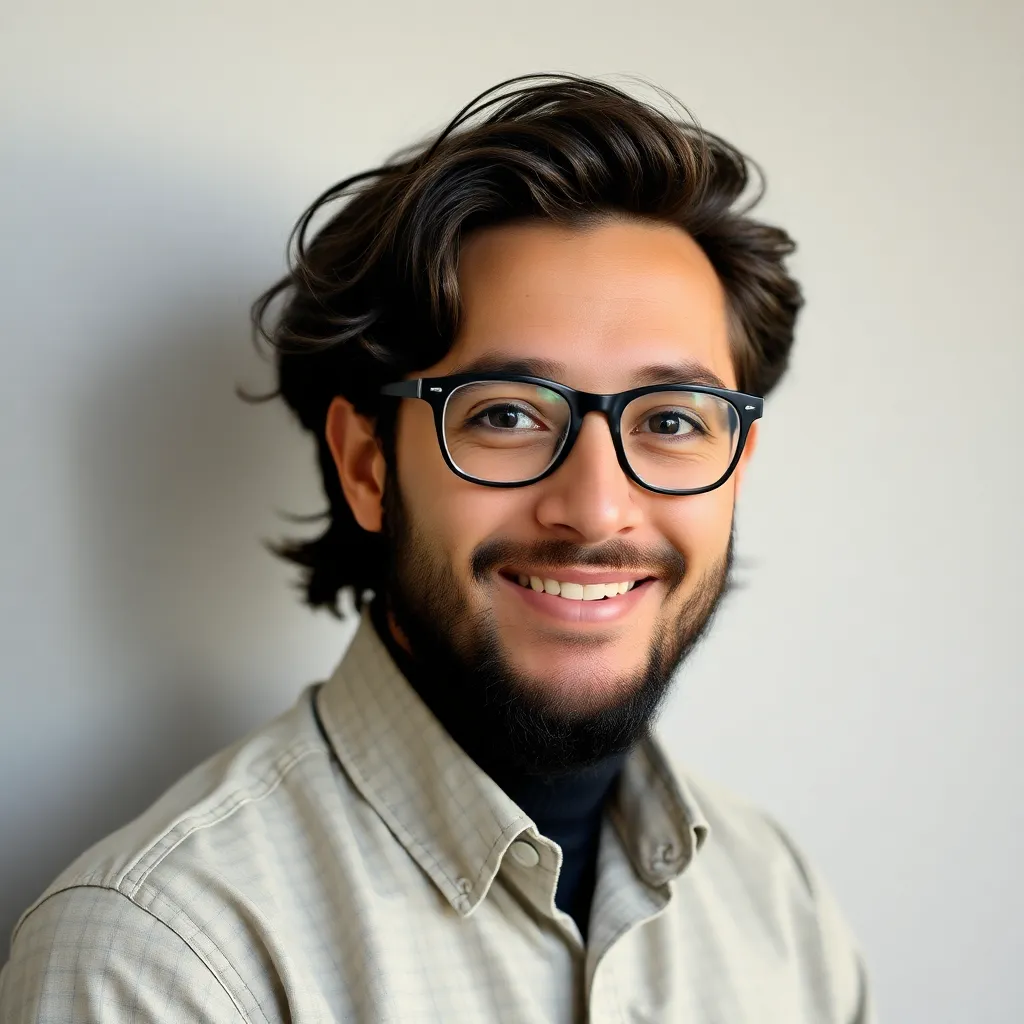
Juapaving
Apr 10, 2025 · 7 min read

Table of Contents
Polar Moment of Inertia of a Hollow Cylinder: A Comprehensive Guide
The polar moment of inertia, often denoted as J or Ip, is a crucial concept in engineering mechanics, particularly when analyzing torsional stress and deflection in rotating components. Understanding this property is essential for designing safe and efficient machinery, especially those involving cylindrical structures like shafts, pipes, and pressure vessels. This comprehensive guide delves into the polar moment of inertia of a hollow cylinder, exploring its calculation, applications, and significance.
What is the Polar Moment of Inertia?
The polar moment of inertia quantifies a body's resistance to torsional deformation. Unlike the area moment of inertia, which considers resistance to bending, the polar moment of inertia specifically addresses resistance to twisting. Imagine applying a torque to a cylindrical shaft; the higher its polar moment of inertia, the less it will twist for a given torque. This property is pivotal in ensuring structural integrity and preventing catastrophic failures in rotating components.
For a hollow cylinder, the polar moment of inertia represents the distribution of mass around its central axis. The farther the mass is distributed from this axis, the greater the resistance to torsion. This is analogous to how a larger radius in a solid cylinder increases its resistance to twisting.
Calculating the Polar Moment of Inertia of a Hollow Cylinder
The formula for calculating the polar moment of inertia of a hollow cylinder is derived from the fundamental definition of the moment of inertia and through integration across the cross-sectional area. It's given by:
J = (π/2) * (Ro⁴ - Ri⁴)
Where:
- J represents the polar moment of inertia.
- Ro represents the outer radius of the hollow cylinder.
- Ri represents the inner radius of the hollow cylinder.
This formula indicates that the polar moment of inertia is directly proportional to the fourth power of the outer and inner radii. This highlights the significant influence of the cylinder's dimensions on its torsional stiffness. A small increase in the outer radius has a much greater impact on J compared to a similar increase in the inner radius.
Derivation of the Formula
The formula isn't simply stated; it stems from integrating the infinitesimal moments of inertia of annular elements comprising the cylinder's cross-section. Consider a thin annular element with radius 'r' and thickness 'dr'. Its area is dA = 2πrdr. The moment of inertia of this element about the central axis is dA * r². Integrating this over the entire cross-section (from Ri to Ro) yields the total polar moment of inertia:
∫(Ri to Ro) 2πr³ dr = (π/2) * (Ro⁴ - Ri⁴)
This integration clearly demonstrates the relationship between the radii and the resulting polar moment of inertia.
Practical Applications of the Polar Moment of Inertia of a Hollow Cylinder
The polar moment of inertia of a hollow cylinder is a critical parameter in numerous engineering applications:
1. Shaft Design in Rotating Machinery
Shafts are fundamental components in countless machines, from automobiles to power generators. Determining the appropriate shaft diameter is crucial to prevent torsional failure under operational loads. The polar moment of inertia directly influences the shaft's torsional stiffness, allowing engineers to select a shaft diameter that adequately resists twisting under anticipated torque. A hollow shaft, with its higher polar moment of inertia compared to a solid shaft of the same weight, is often preferred due to its weight-saving properties without compromising torsional strength.
2. Pipe Stress Analysis
Pipelines carrying fluids under pressure experience significant stresses, particularly under thermal expansion or external loads. Analyzing these stresses requires understanding the pipe's polar moment of inertia. The polar moment of inertia helps engineers assess the pipe's resistance to twisting, ensuring its structural integrity and preventing leaks or ruptures. This is particularly critical for pipelines operating under high pressures or in challenging environments.
3. Pressure Vessel Design
Pressure vessels store fluids at high pressures. The polar moment of inertia plays a critical role in designing pressure vessels that can withstand these internal pressures without deformation or failure. The vessel's wall thickness and overall geometry are optimized to achieve a sufficient polar moment of inertia to resist twisting and maintain structural integrity.
4. Aerospace Engineering
Lightweight yet strong components are paramount in aerospace applications. Hollow cylinders are often employed in aircraft and spacecraft structures. Precise calculation of the polar moment of inertia helps engineers optimize the design for maximum strength-to-weight ratio, crucial for efficient flight and fuel consumption. The torsional resistance of these hollow cylindrical components needs careful consideration to avoid failures under flight loads and maneuvers.
5. Automotive Engineering
Similar to aerospace, automotive engineering also benefits from lightweight yet strong components. Drive shafts, axles, and other rotating parts are often designed using hollow cylinders to maximize strength while minimizing weight. Accurate computation of the polar moment of inertia is crucial for ensuring the durability and safety of these components under operational conditions.
Comparison with Solid Cylinder's Polar Moment of Inertia
It's instructive to compare the polar moment of inertia of a hollow cylinder to that of a solid cylinder. The polar moment of inertia of a solid cylinder is given by:
J = (π/2) * R⁴
Where R is the radius of the solid cylinder. Notice that the hollow cylinder's formula incorporates the inner radius (Ri), reflecting the material removed from the center. If Ri = 0 (a solid cylinder), the hollow cylinder's formula reduces to the solid cylinder's formula.
The key difference lies in the material distribution. A hollow cylinder, for the same mass, will generally have a significantly larger polar moment of inertia than a solid cylinder due to the increased distance of the material from the central axis. This increased moment of inertia translates to enhanced resistance to torsional stress.
Factors Affecting the Polar Moment of Inertia
Several factors influence a hollow cylinder's polar moment of inertia:
- Outer Radius (Ro): The most dominant factor; a larger outer radius drastically increases the polar moment of inertia.
- Inner Radius (Ri): A larger inner radius reduces the polar moment of inertia, as it decreases the amount of material contributing to the resistance to torsion.
- Material Density: While not directly in the formula, the density affects the overall mass and therefore the resistance to rotation. Higher density material leads to a greater resistance to twisting for the same dimensions.
- Wall Thickness (Ro - Ri): The wall thickness plays a crucial role. A thicker wall, keeping the outer radius constant, increases the polar moment of inertia.
Advanced Considerations and Applications
The analysis presented so far focuses on a perfectly homogeneous and isotropic hollow cylinder. In reality, factors such as material imperfections, stress concentrations, and dynamic loads can significantly impact the cylinder's behaviour.
Advanced analysis techniques, such as finite element analysis (FEA), are often employed for more realistic simulations, accounting for these complexities. FEA can provide a detailed stress distribution within the cylinder under various loading scenarios, enabling engineers to refine designs and enhance safety margins.
Furthermore, the concept extends beyond simple cylindrical shapes. For complex hollow sections, numerical methods or specialized software are necessary to determine the polar moment of inertia. These methods can handle arbitrary geometries and material properties, offering accurate predictions of torsional behaviour.
Conclusion
The polar moment of inertia of a hollow cylinder is a fundamental parameter in engineering design and analysis. Understanding its calculation, applications, and influence on structural integrity is crucial for ensuring the safety and efficiency of various engineering systems. From rotating machinery to pressure vessels, mastering this concept is essential for creating robust and reliable designs. The significant advantage of a hollow cylinder's higher polar moment of inertia for a given mass makes it a preferred choice in many applications where lightweight yet torsionally stiff components are required. By considering the factors influencing the polar moment of inertia and leveraging advanced analysis techniques when necessary, engineers can optimize designs and minimize the risk of failure.
Latest Posts
Latest Posts
-
What Is The Value Of X 6 8 10 12
Apr 18, 2025
-
All Of These Are Parts Of A Flower Except For
Apr 18, 2025
-
Which Of The Following Illustrates Conservation
Apr 18, 2025
-
3 5 Gallons Is How Many Liters
Apr 18, 2025
-
What Is The Function Of The Membrane On A Frog
Apr 18, 2025
Related Post
Thank you for visiting our website which covers about Polar Moment Of Inertia Of Hollow Cylinder . We hope the information provided has been useful to you. Feel free to contact us if you have any questions or need further assistance. See you next time and don't miss to bookmark.