Polar Moment Of Inertia For Hollow Shaft
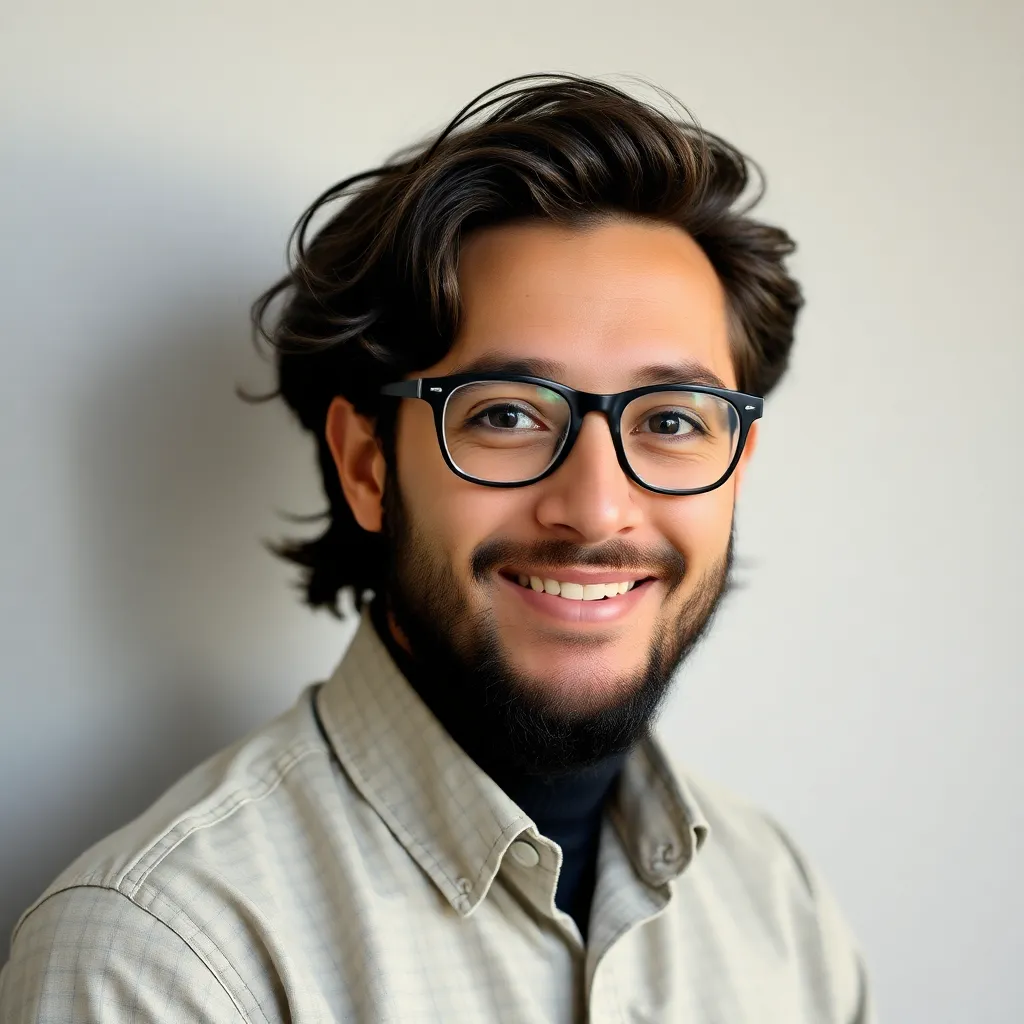
Juapaving
May 14, 2025 · 7 min read
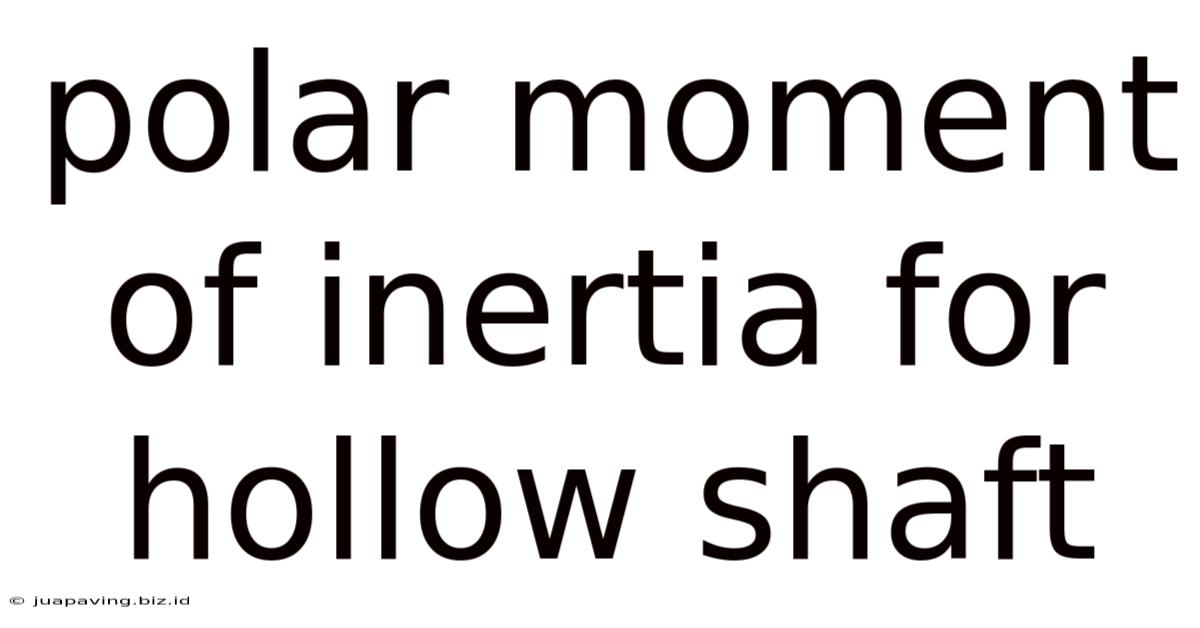
Table of Contents
Polar Moment of Inertia for Hollow Shafts: A Comprehensive Guide
The polar moment of inertia, often denoted as J or Ip, is a crucial concept in mechanical engineering, particularly when analyzing torsional stress and deflection in rotating shafts. Understanding this property is essential for designing safe and efficient machinery, from automotive components to large industrial turbines. This comprehensive guide delves into the polar moment of inertia, focusing specifically on hollow shafts, explaining its calculation, significance, and practical applications.
What is the Polar Moment of Inertia?
The polar moment of inertia quantifies a shaft's resistance to torsion. It represents the distribution of mass around the shaft's longitudinal axis. A higher polar moment of inertia indicates a greater resistance to twisting under an applied torque. Imagine trying to twist a thick metal rod versus a thin one – the thicker rod, with its larger polar moment of inertia, will resist twisting more effectively.
For a solid circular shaft, the calculation is relatively straightforward. However, hollow shafts, frequently used in engineering due to their higher strength-to-weight ratio, require a different approach.
Calculating the Polar Moment of Inertia for a Hollow Shaft
The polar moment of inertia for a hollow circular shaft is calculated using the following formula:
J = (π/32) * (D⁴ - d⁴)
Where:
- J represents the polar moment of inertia.
- D is the outer diameter of the hollow shaft.
- d is the inner diameter of the hollow shaft.
This formula highlights a key difference between solid and hollow shafts: the subtraction of the inner diameter's fourth power. This subtraction accounts for the material removed from the center, reducing the overall resistance to torsion compared to a solid shaft of the same outer diameter.
Understanding the Formula's Components:
- (π/32): This is a constant derived from the geometry of a circle.
- D⁴: Represents the contribution to the polar moment of inertia from the outer diameter. The fourth power emphasizes the significant effect of the outer diameter on torsional resistance.
- d⁴: Represents the contribution subtracted due to the hollow core. The fourth power similarly highlights the considerable impact of the inner diameter.
The formula's structure clearly shows that increasing the outer diameter (D) significantly increases the polar moment of inertia, while increasing the inner diameter (d) decreases it. This underscores the importance of carefully selecting the shaft's dimensions based on the anticipated torsional loads.
Why Use Hollow Shafts?
Hollow shafts, despite having a lower polar moment of inertia than a solid shaft of the same outer diameter, offer several advantages that often outweigh this difference:
-
Weight Reduction: Hollow shafts are significantly lighter than solid shafts of comparable strength, reducing inertia and improving overall system efficiency, especially in high-speed applications. This lighter weight also contributes to reduced energy consumption and lower operating costs.
-
Increased Strength-to-Weight Ratio: The material is distributed further from the neutral axis, improving its ability to resist bending and torsional stresses. This allows for the use of smaller diameter shafts while maintaining adequate strength.
-
Improved Fatigue Resistance: The absence of material at the center reduces stress concentrations, improving fatigue life and durability.
-
Enhanced Stiffness: For a given weight, hollow shafts can exhibit higher stiffness, leading to improved accuracy and reduced vibration in applications requiring precision.
-
Internal Passage for Fluids or Cables: The hollow core can accommodate the passage of fluids (e.g., hydraulic fluids, lubricating oils) or electrical cables, simplifying system design and reducing the number of components.
Practical Applications of Hollow Shafts
The advantages of hollow shafts make them ideal for various applications across diverse industries:
-
Automotive Engineering: Driveshafts, axles, and steering columns frequently utilize hollow shafts to minimize weight and maximize strength. The reduced weight improves fuel efficiency and handling.
-
Aerospace Engineering: In aircraft and spacecraft, lightweight yet strong components are paramount. Hollow shafts are used extensively in rotor systems, landing gear, and control systems. The reduced weight translates to improved fuel efficiency and payload capacity.
-
Robotics: The strength and lightweight nature of hollow shafts are advantageous in robotic arms and manipulators, enabling faster movement and increased precision.
-
Power Generation: Turbines and generators often incorporate hollow shafts to transmit high torques while minimizing weight and vibration. This is crucial for efficient and reliable power generation.
-
Industrial Machinery: Heavy-duty machinery, including cranes, excavators, and other construction equipment, often uses hollow shafts in their drive systems to withstand high torsional loads while minimizing weight.
-
Bicycle Manufacturing: Lightweight and high-strength hollow shafts are common in bicycles to minimize weight and maximize the rider's efficiency.
Factors Affecting the Polar Moment of Inertia
Several factors beyond the inner and outer diameters influence the effective polar moment of inertia of a hollow shaft:
-
Material Properties: The material's Young's modulus (E) and shear modulus (G) directly influence the shaft's resistance to torsion. A higher modulus indicates greater stiffness and resistance to twisting.
-
Shaft Length: While the formula above calculates the section polar moment of inertia, the overall torsional stiffness is also affected by the shaft's length. Longer shafts are more prone to twisting under the same torque.
-
Temperature: Temperature changes can alter the material properties and thus impact the effective polar moment of inertia.
-
Manufacturing Tolerances: Imperfections in the manufacturing process can introduce variations in the shaft's dimensions and material properties, affecting the actual polar moment of inertia. Precise manufacturing is crucial for ensuring the shaft meets design specifications.
-
Surface Finish: The surface roughness of the shaft can influence its resistance to fatigue and wear, indirectly impacting its effective torsional resistance.
Calculating Stress and Deflection in Hollow Shafts
The polar moment of inertia is central to calculating the shear stress and angle of twist (deflection) in a hollow shaft subjected to torsion. The following equations are commonly used:
- Shear Stress (τ): τ = (T * r) / J
Where:
- τ is the shear stress.
- T is the applied torque.
- r is the radial distance from the center of the shaft.
- J is the polar moment of inertia.
This equation shows that the shear stress is highest at the outer surface of the shaft (r = D/2) and zero at the center.
- Angle of Twist (θ): θ = (T * L) / (G * J)
Where:
- θ is the angle of twist in radians.
- L is the length of the shaft.
- G is the shear modulus of the material.
- J is the polar moment of inertia.
This equation shows that a higher polar moment of inertia (J) leads to a smaller angle of twist for a given torque (T).
Designing with Hollow Shafts: Considerations and Best Practices
Designing with hollow shafts requires careful consideration of several factors:
-
Load Capacity: Accurately determining the maximum torsional load the shaft will experience is critical. This load determines the necessary polar moment of inertia and, consequently, the shaft's dimensions.
-
Safety Factors: Always incorporate appropriate safety factors to account for uncertainties and potential overloads. This helps ensure the shaft's reliability and longevity.
-
Material Selection: Selecting a suitable material with appropriate strength, stiffness, and fatigue resistance is crucial for optimal performance.
-
Manufacturing Methods: The chosen manufacturing process (e.g., forging, machining) significantly impacts the shaft's dimensional accuracy and surface finish, influencing its strength and durability.
-
Fatigue Analysis: For applications involving cyclic loading, performing a fatigue analysis is essential to assess the shaft's lifespan and prevent premature failure.
-
Finite Element Analysis (FEA): For complex geometries or loading conditions, using FEA can provide a more accurate prediction of stress distribution and deflection.
Conclusion
The polar moment of inertia is a fundamental property for understanding and designing hollow shafts. Its calculation and significance in determining torsional stress and deflection are crucial for engineers working across various disciplines. By carefully considering the factors discussed in this guide and employing appropriate design practices, engineers can leverage the advantages of hollow shafts to create efficient, lightweight, and reliable components for a wide range of applications. Understanding the relationship between the inner and outer diameter and the resulting polar moment of inertia is key to optimizing shaft design for specific performance requirements. Remember that proper consideration of material properties, manufacturing tolerances, and potential loading conditions are vital for ensuring the safety and longevity of the components.
Latest Posts
Latest Posts
-
5 Letter Words Ending In As
May 14, 2025
-
How Many Feet Is 60 Cm
May 14, 2025
-
Is A Cake Baking A Chemical Change
May 14, 2025
-
How Long To Walk 1 5 Km
May 14, 2025
-
Objects That Start With The Letter V
May 14, 2025
Related Post
Thank you for visiting our website which covers about Polar Moment Of Inertia For Hollow Shaft . We hope the information provided has been useful to you. Feel free to contact us if you have any questions or need further assistance. See you next time and don't miss to bookmark.