Office Salaries Expense And Factory Maintenance Are Both Product Costs.
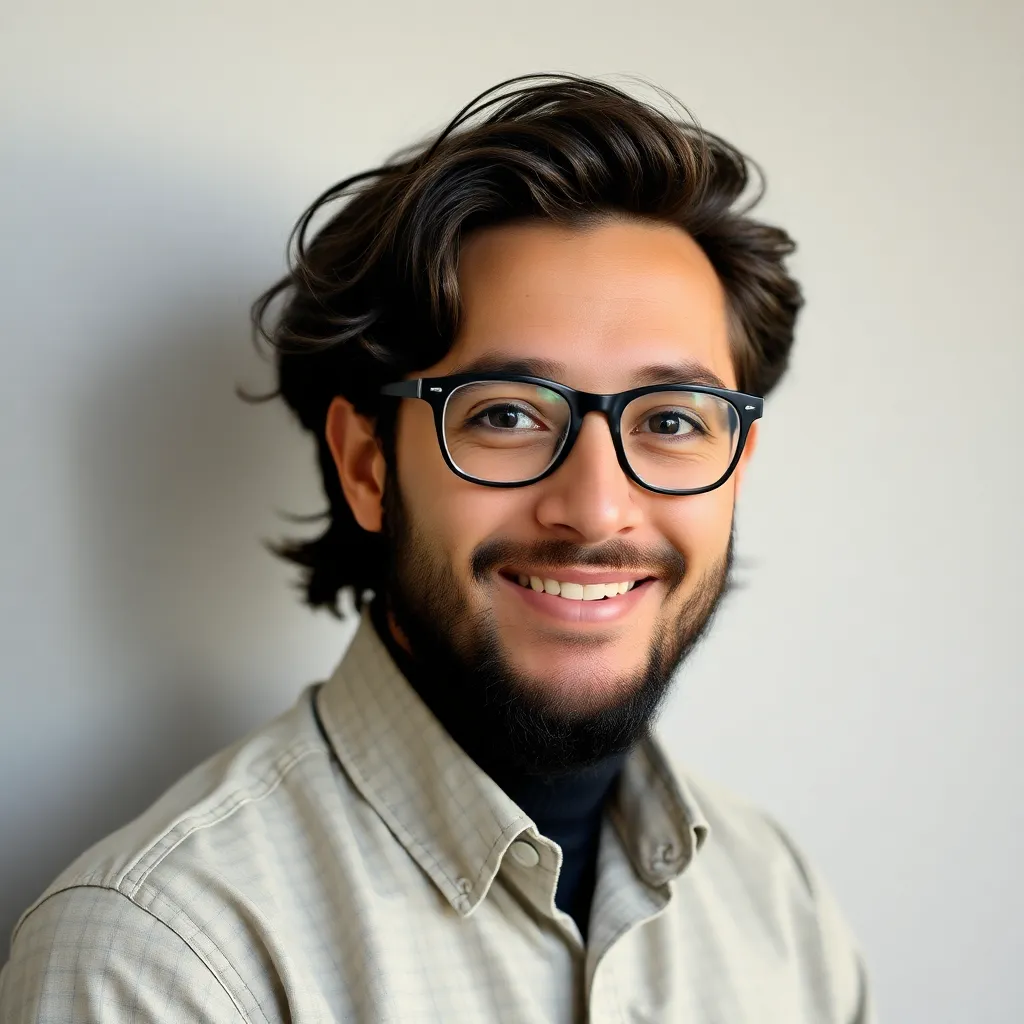
Juapaving
May 25, 2025 · 6 min read
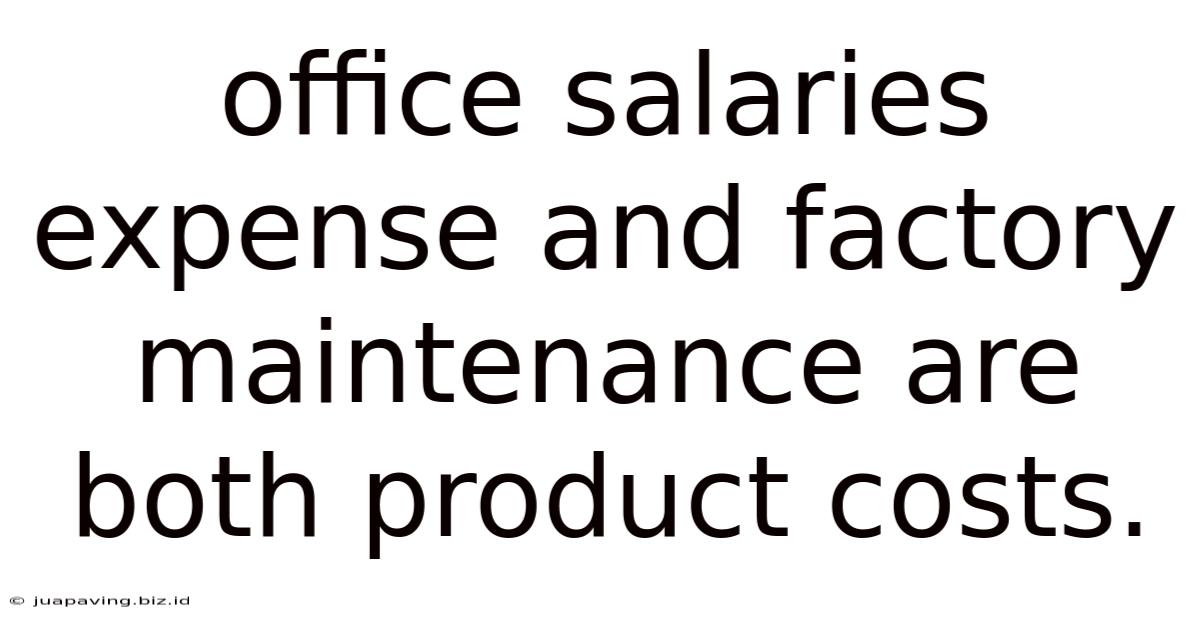
Table of Contents
Office Salaries Expense and Factory Maintenance: Both Product Costs? A Deep Dive
Understanding the true nature of product costs is crucial for accurate financial reporting and effective business decision-making. While seemingly straightforward, the categorization of certain expenses can be surprisingly complex. This article will delve into the often-debated topic of whether office salaries expense and factory maintenance are both considered product costs. We'll explore the nuances of cost accounting, examining different costing methods and their impact on the classification of these expenses.
What are Product Costs?
Product costs, also known as inventoriable costs, are all costs directly related to the production of goods. These costs are assigned to the inventory and are only expensed when the goods are sold. The primary components of product costs are:
- Direct Materials: These are raw materials directly traceable to the finished product. Think of the wood in a table, the fabric in a shirt, or the steel in a car.
- Direct Labor: This encompasses the wages and benefits paid to workers directly involved in the manufacturing process. This includes assembly line workers, machine operators, and other personnel directly contributing to the creation of the product.
- Manufacturing Overhead: This is a broader category encompassing all indirect costs associated with production. This includes things like factory rent, utilities, depreciation on factory equipment, factory supplies, and factory maintenance.
It’s this last category, manufacturing overhead, that often leads to confusion regarding the classification of certain expenses.
Are Office Salaries Product Costs?
The simple answer is: generally, no. Office salaries are typically considered period costs, meaning they are expensed in the period they are incurred, regardless of whether goods are sold.
This is because office salaries are related to administrative and selling activities, not directly to the production of goods. While the office staff might support the production process, their work isn't directly involved in transforming raw materials into finished products. Their contributions are essential for the overall functioning of the business, but they are not considered part of the cost of creating a specific product.
However, there are exceptions. If an office employee's primary role directly supports the manufacturing process, their salary could be considered a product cost. For example:
- Production scheduling staff: Employees responsible for planning and coordinating the production schedule directly impact manufacturing efficiency and output. A portion of their salaries could be allocated to the product cost.
- Quality control inspectors in the office: If inspectors review production data and reports directly related to product quality from the factory floor, a portion of their salary might be considered a product cost.
- Design engineers working on product specifications: Salaries for engineers directly involved in designing the product itself could be considered product costs.
The key is whether the employee's work directly contributes to the physical transformation of materials into finished goods. If not, the salary is a period cost.
Allocating Office Salaries: Challenges and Approaches
Allocating a portion of office salaries to product costs is complex and often requires careful judgment. Common methods include:
- Percentage of Sales: This method allocates a percentage of office salaries based on the sales revenue generated. While simple, it doesn't accurately reflect the actual contribution of office staff to production.
- Activity-Based Costing (ABC): ABC is a more sophisticated method that allocates costs based on the activities performed. It identifies specific activities, assigns costs to those activities, and then allocates the costs based on the consumption of those activities by various products. This can provide a more accurate allocation of office salaries if activities directly linked to production can be identified.
- Direct Allocation: This involves directly assigning office salary costs to specific products if there’s a clear and direct relationship.
The choice of method depends on the company's size, complexity, and the level of accuracy required.
Factory Maintenance: A Clear Product Cost
Unlike office salaries, factory maintenance is unequivocally a product cost, specifically classified under manufacturing overhead. This is because factory maintenance is essential for the continued operation of the factory and the production of goods. Without proper maintenance, equipment could malfunction, leading to production delays, defects, and increased costs.
The costs associated with factory maintenance include:
- Preventative maintenance: Regular inspections, cleaning, and lubrication of equipment to prevent breakdowns.
- Repair and maintenance: Fixing broken or malfunctioning equipment.
- Overhauls: Major overhauls of equipment to extend its lifespan.
- Depreciation of factory maintenance equipment: The depreciation on tools and equipment used for factory maintenance.
These costs are all directly tied to the production process and are necessary for the creation of goods. Therefore, they are appropriately categorized as product costs, specifically under manufacturing overhead.
The Impact on Costing Methods
The classification of these expenses significantly impacts the costing methods employed by a company. Understanding the difference between product and period costs is crucial for accurately calculating:
- Cost of Goods Sold (COGS): COGS is a crucial figure on the income statement and represents the direct costs associated with producing goods sold during a specific period. Product costs are included in COGS.
- Inventory Valuation: Product costs are directly included in the valuation of inventory on the balance sheet. This affects the company's financial position.
- Pricing Decisions: Accurate cost calculations allow for informed pricing decisions, ensuring profitability.
- Profitability Analysis: Properly categorizing costs is necessary for accurate analysis of profitability and identification of areas for cost reduction.
Ignoring the distinction between product and period costs can lead to inaccurate financial reporting, distorted profitability analysis, and flawed management decisions.
Absorption Costing vs. Variable Costing
The classification of these costs also influences the choice between absorption costing and variable costing.
- Absorption Costing: This method includes all manufacturing costs (direct materials, direct labor, and manufacturing overhead, including factory maintenance) in the product cost. This means factory maintenance increases the per-unit cost of the product.
- Variable Costing: This method includes only variable manufacturing costs in the product cost. Fixed manufacturing overhead, such as a portion of factory maintenance costs, is treated as a period cost and expensed in the period incurred. Therefore, factory maintenance is partially a product cost and partially a period cost under this method.
The choice between these methods depends on the company's specific needs and the information required for decision-making.
Conclusion: Clarity and Consistency are Key
While office salaries are generally period costs, specific circumstances might necessitate allocating a portion to product costs. Factory maintenance, on the other hand, is clearly a product cost, a crucial element of manufacturing overhead. Accurate classification of these expenses is essential for precise financial reporting, informed decision-making, and a thorough understanding of the company's cost structure. Consistency in the application of chosen accounting methods is crucial for reliable financial information. Consulting with a qualified accountant or financial professional is advisable to ensure appropriate cost allocation strategies aligned with the specific circumstances and accounting standards of your business. Remember, careful consideration and consistent application of the chosen methodology are key to ensuring accurate financial reporting and effective business management.
Latest Posts
Latest Posts
-
At The Output Level That Maximizes Economic Surplus
May 25, 2025
-
When To Use The Plus Que Parfait
May 25, 2025
-
Sociological Concepts Of Life Of Pi Book
May 25, 2025
-
Entrepreneurship And Small Business V 2 Project Workbook First Edition
May 25, 2025
-
The Things They Carried Chapter 9
May 25, 2025
Related Post
Thank you for visiting our website which covers about Office Salaries Expense And Factory Maintenance Are Both Product Costs. . We hope the information provided has been useful to you. Feel free to contact us if you have any questions or need further assistance. See you next time and don't miss to bookmark.