Name The Metal Which Is Used For Galvanising Iron
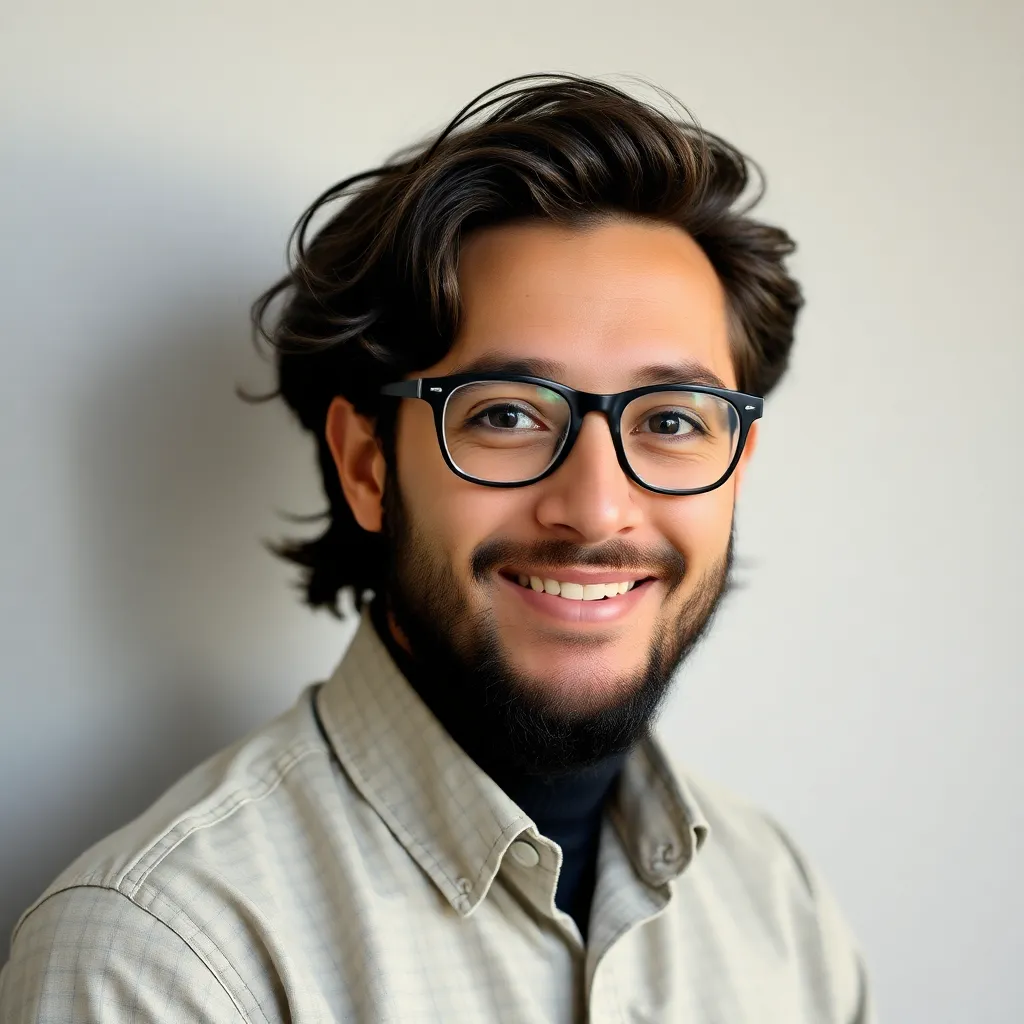
Juapaving
Apr 22, 2025 · 5 min read

Table of Contents
Name the Metal Which is Used for Galvanising Iron: A Deep Dive into Zinc's Protective Properties
Galvanizing iron is a crucial process in protecting iron and steel from corrosion, extending their lifespan significantly. But what exactly is galvanizing, and which metal plays the starring role in this protective shield? The answer, simply put, is zinc. This article will delve deep into the world of galvanizing, exploring why zinc is the metal of choice, the process itself, the various types of galvanizing, and the advantages and disadvantages of this widely-used technique.
Understanding the Process of Galvanizing
Galvanization is a metallurgical process that involves coating iron or steel with a layer of zinc to prevent rust and corrosion. This protective layer acts as a barrier, preventing oxygen and moisture from reaching the underlying metal. This is crucial because rust, the common form of iron corrosion, is essentially the oxidation of iron in the presence of oxygen and water. The zinc coating sacrifices itself to protect the iron, a concept central to its effectiveness.
The Chemistry of Corrosion Protection
The zinc coating doesn't simply act as a physical barrier. Zinc is more reactive than iron, meaning it readily oxidizes (rusts) itself before the iron. This is known as sacrificial protection or cathodic protection. When exposed to the elements, the zinc reacts with oxygen and water to form zinc oxide and zinc hydroxide, forming a passive layer that further inhibits corrosion. This means even if the zinc coating is scratched, the underlying iron remains protected by the remaining zinc and the passive layer formed on the surface of the zinc.
Types of Galvanizing
There are primarily two main types of galvanizing:
-
Hot-Dip Galvanizing: This is the most common method, involving immersing the cleaned iron or steel object in a molten bath of zinc at a temperature typically between 820°F (440°C) and 860°F (460°C). The zinc adheres to the iron surface, forming a strong metallurgical bond. This process results in a thick, durable coating that offers excellent corrosion resistance.
-
Electrogalvanizing: Also known as electroplating, this method involves using an electric current to deposit a layer of zinc onto the iron surface. This process is generally used for producing thinner coatings compared to hot-dip galvanizing, making it suitable for applications where a thinner, more uniform coating is preferred.
Why Zinc? The Unique Properties of Zinc in Galvanizing
Choosing the right metal for galvanizing isn't arbitrary; zinc possesses several crucial properties that make it ideal for this purpose:
-
Reactivity: Zinc's higher reactivity than iron is the cornerstone of its protective action. It preferentially oxidizes, preventing the iron from corroding.
-
Cost-Effectiveness: Zinc is a relatively inexpensive metal, making galvanizing a cost-effective corrosion protection method compared to other techniques like painting or coating with more expensive metals.
-
Durability: A properly applied zinc coating offers excellent durability and longevity, significantly extending the lifespan of the protected iron or steel. Hot-dip galvanizing, in particular, creates a very durable coating that can last for decades.
-
Ease of Application: Both hot-dip and electrogalvanizing methods are relatively straightforward to implement, making the process efficient and scalable for large-scale production.
-
Formability: Zinc's malleability allows for the coating to withstand bending and shaping without significant damage to the protective layer. This is particularly important for applications involving fabricated metal components.
-
Environmental Compatibility: Zinc is considered relatively environmentally friendly compared to some other metals. While zinc oxide can cause some environmental concerns in large quantities, the quantities used in galvanizing are generally not considered harmful.
Applications of Galvanized Iron
Galvanized iron finds widespread use in a multitude of applications across various industries, thanks to its exceptional corrosion resistance:
-
Construction: Galvanized steel is frequently used in roofing, siding, gutters, downspouts, and other exterior components of buildings, where its resistance to rust is vital.
-
Automotive: Many automotive parts, including body panels and chassis components, are galvanized to prevent rust and extend their lifespan.
-
Infrastructure: Galvanized steel is widely used in bridges, pipelines, fencing, and other infrastructure projects, where corrosion resistance is paramount for long-term durability and safety.
-
Agricultural: Galvanized steel is common in agricultural equipment, storage structures, and fencing, where exposure to the elements is significant.
-
Manufacturing: Various industrial components and machinery utilize galvanized steel for its durability and corrosion resistance in diverse manufacturing processes.
-
Household Items: Many everyday items, such as buckets, trash cans, and various hardware components, benefit from the corrosion protection afforded by galvanizing.
Advantages and Disadvantages of Galvanizing
Like any other process, galvanizing has its advantages and disadvantages:
Advantages:
- Cost-effective: Compared to other corrosion protection methods, galvanizing offers excellent value for money.
- Long-lasting: A properly applied zinc coating provides long-term corrosion protection.
- Easy to apply: Both hot-dip and electrogalvanizing are relatively straightforward processes.
- Versatile: Galvanizing can be applied to various shapes and sizes of iron and steel components.
- Environmentally friendly: Zinc is considered a relatively benign metal compared to some alternatives.
Disadvantages:
- Hydrogen embrittlement: Hot-dip galvanizing can lead to hydrogen embrittlement in high-strength steels, making them more susceptible to cracking.
- Zinc spalling: In certain harsh environments, the zinc coating can flake or spall, compromising its protective properties.
- Appearance: Some may find the appearance of galvanized iron less aesthetically pleasing compared to other finishes.
- Not suitable for all metals: Galvanizing is only suitable for iron and steel; it can't be applied to other base metals.
Maintaining Galvanized Iron
While galvanizing provides excellent corrosion resistance, proper maintenance can further extend its lifespan. Regular cleaning and inspection are advisable, especially in harsh environments. Repairing minor scratches or damaged areas might be necessary in some cases.
Conclusion: The Irreplaceable Role of Zinc in Galvanizing
Zinc’s unique properties, particularly its higher reactivity than iron and its cost-effectiveness, solidify its position as the go-to metal for galvanizing. This process remains a cornerstone of corrosion protection, enhancing the durability and longevity of iron and steel structures across various applications. Understanding the nuances of galvanizing, including its types, advantages, and disadvantages, is crucial for making informed decisions in engineering, construction, and manufacturing. The widespread use of galvanized iron and steel demonstrates its lasting impact on modern infrastructure and industrial processes, and its importance is only set to grow as the demand for durable, cost-effective corrosion protection continues to rise.
Latest Posts
Latest Posts
-
Does A Solid Have A Definite Shape
Apr 22, 2025
-
What Is The Purpose Of A Punnett Square
Apr 22, 2025
-
Objects In A Mirror Are Closer Than They Appear
Apr 22, 2025
-
Plasma Membranes Are Selectively Permeable This Means That
Apr 22, 2025
-
What Is The Density Of Ice
Apr 22, 2025
Related Post
Thank you for visiting our website which covers about Name The Metal Which Is Used For Galvanising Iron . We hope the information provided has been useful to you. Feel free to contact us if you have any questions or need further assistance. See you next time and don't miss to bookmark.