In Managing Production Worker Compensation And Expenditures
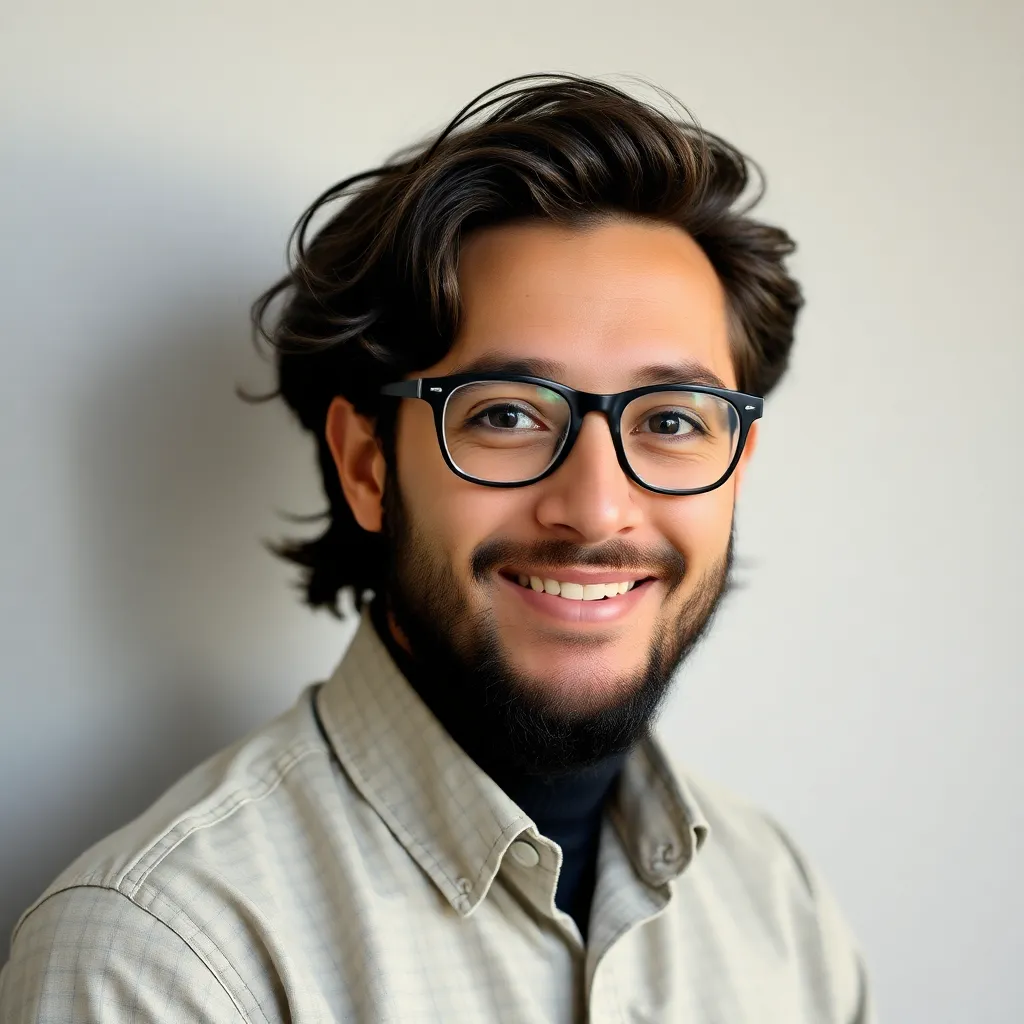
Juapaving
May 23, 2025 · 7 min read
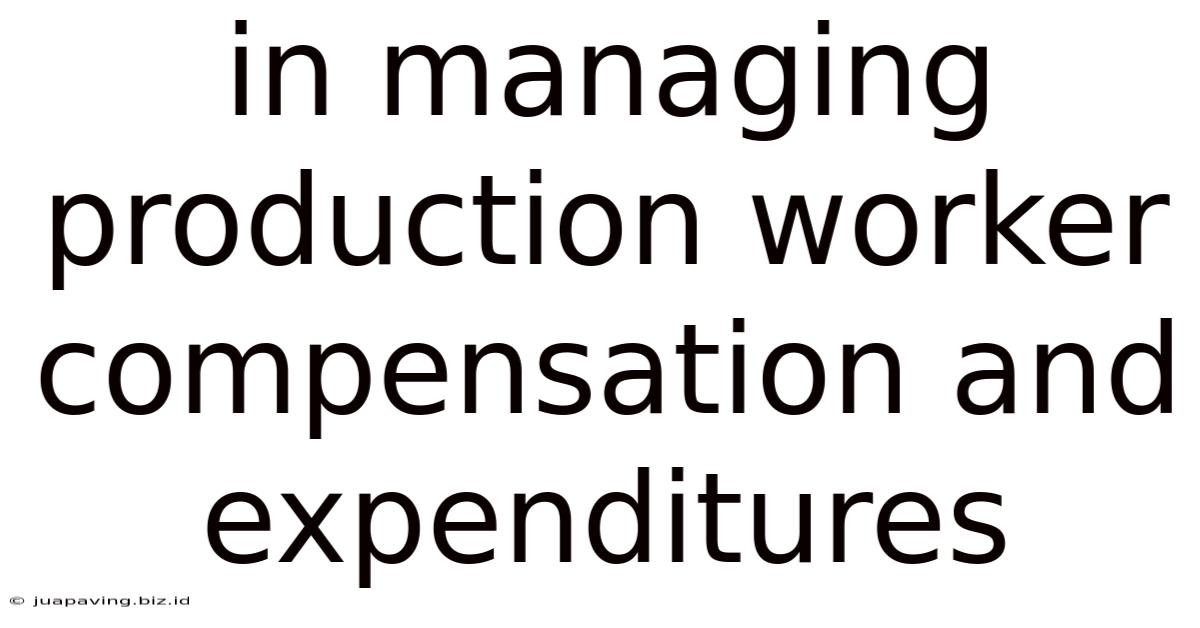
Table of Contents
Mastering Production Worker Compensation and Expenditures: A Comprehensive Guide
Managing production worker compensation and expenditures is a critical aspect of maintaining a profitable and efficient manufacturing operation. It requires a multifaceted approach that balances attracting and retaining skilled labor with controlling costs and ensuring compliance with all relevant regulations. This comprehensive guide delves into the key strategies and considerations for effectively managing this complex area.
Understanding the Landscape of Production Worker Compensation
Production worker compensation encompasses a broad spectrum of elements, extending beyond just the base hourly wage. A thorough understanding of these components is crucial for effective management.
1. Base Wages and Salaries:
This forms the foundation of compensation. Determining competitive base wages involves market research, analyzing competitor compensation packages, and considering the local cost of living. A poorly structured wage system can lead to high turnover and difficulties attracting qualified workers. Key considerations:
- Geographic location: Wages vary significantly across regions due to differences in the cost of living and the local labor market.
- Industry benchmarks: Researching industry-standard wages for similar roles helps establish competitive compensation.
- Experience and skills: Experienced workers with specialized skills typically command higher wages.
- Internal equity: Maintaining fair compensation across different roles within the company prevents internal dissatisfaction.
2. Incentive Programs and Bonuses:
Implementing effective incentive programs is crucial for boosting productivity and motivating employees. These programs can be tied to individual performance, team achievements, or overall company performance. Examples include:
- Piece-rate systems: Workers are paid based on the number of units produced. This incentivizes higher output but can also lead to quality issues if not carefully managed.
- Performance-based bonuses: Bonuses are awarded based on meeting or exceeding pre-determined performance goals. This can be tied to metrics like efficiency, quality, or safety.
- Profit-sharing plans: Employees receive a share of the company's profits. This fosters a sense of ownership and encourages teamwork.
- Gainsharing programs: Incentivize teams or departments to improve efficiency and reduce costs by sharing the resulting savings.
Careful design is crucial; poorly designed incentive programs may have unintended consequences such as compromising quality or creating unhealthy competition.
3. Benefits Packages:
Attracting and retaining skilled production workers often requires offering a comprehensive benefits package. This goes beyond mandatory requirements and includes:
- Health insurance: Medical, dental, and vision coverage are increasingly important employee benefits.
- Retirement plans: 401(k) plans or pension plans provide employees with long-term financial security.
- Paid time off: Vacation time, sick leave, and paid holidays are standard benefits that improve employee well-being and retention.
- Life insurance and disability insurance: These benefits protect employees and their families in the event of unforeseen circumstances.
- Employee assistance programs (EAPs): EAPs provide confidential support for employees dealing with personal or work-related issues.
- Tuition reimbursement: Supporting employee development through tuition reimbursement can improve skills and loyalty.
A robust benefits package improves employee morale and reduces turnover. However, the cost of benefits must be carefully budgeted and managed.
4. Overtime Compensation:
Overtime pay is a significant cost factor, particularly during peak production periods or unexpected surges in demand. Effective planning and workforce management are key to minimizing unnecessary overtime costs. Strategies include:
- Accurate demand forecasting: Predicting production needs helps avoid last-minute overtime requests.
- Flexible scheduling: Implementing flexible work schedules can accommodate fluctuations in production demands and reduce overtime.
- Cross-training: Training employees in multiple roles increases workforce flexibility and reduces reliance on overtime.
- Efficient production processes: Streamlining workflows and improving efficiency reduces the need for extra hours.
Controlling Production Worker Expenditures: Strategies and Best Practices
Controlling expenditures related to production workers requires a strategic and proactive approach. The goal is to optimize costs without sacrificing employee morale or productivity.
1. Strategic Workforce Planning:
Effective workforce planning ensures that the right number of workers with the necessary skills are available at the right time. This reduces the need for costly overtime and temporary staffing. Key elements include:
- Demand forecasting: Accurately predicting production needs is vital for determining staffing requirements.
- Skill gap analysis: Identifying skill shortages allows for proactive training and recruitment efforts.
- Succession planning: Developing internal talent ensures a smooth transition when employees leave.
- Recruitment strategies: Employing effective recruitment methods attracts qualified candidates at competitive costs.
2. Performance Management:
Robust performance management systems identify and address performance issues proactively. This can prevent productivity losses and reduce the need for corrective actions, which often incur extra costs. Effective performance management includes:
- Clear performance expectations: Setting clear goals and expectations prevents misunderstandings and ensures accountability.
- Regular performance reviews: Regular feedback sessions provide opportunities for improvement and address performance gaps early on.
- Training and development: Investing in employee training improves skills and productivity.
- Performance-based incentives: Rewarding high-performing employees motivates them and improves overall productivity.
3. Technology and Automation:
Investing in technology and automation can significantly reduce labor costs in the long run. While the initial investment can be substantial, automation can improve efficiency, reduce errors, and increase output. Examples include:
- Robotics: Robots can automate repetitive tasks, freeing up human workers for more complex roles.
- Automated guided vehicles (AGVs): AGVs automate material handling, reducing labor costs and improving efficiency.
- Computer-aided manufacturing (CAM): CAM software optimizes production processes and reduces waste.
- Enterprise resource planning (ERP) systems: ERP systems integrate various business functions, improving efficiency and reducing administrative costs.
The return on investment (ROI) for automation should be carefully analyzed before implementation.
4. Health and Safety Programs:
Investing in comprehensive health and safety programs reduces worker's compensation costs and lost productivity due to injuries. Key elements include:
- Safe work practices: Implementing and enforcing safe work practices minimizes workplace accidents.
- Regular safety training: Providing regular safety training ensures that employees are aware of and understand safety procedures.
- Ergonomic assessments: Ergonomic assessments identify and address potential hazards related to workplace design and equipment.
- Personal protective equipment (PPE): Providing appropriate PPE protects employees from workplace hazards.
Reducing workplace injuries significantly reduces costs associated with workers' compensation claims, medical expenses, and lost productivity.
5. Compliance and Legal Considerations:
Adherence to all relevant labor laws and regulations is paramount. Non-compliance can result in significant fines and legal repercussions. Key areas to consider include:
- Wage and hour laws: Ensuring compliance with minimum wage laws, overtime pay regulations, and other wage-related requirements.
- Workers' compensation insurance: Maintaining adequate workers' compensation insurance coverage protects the company from liability in case of workplace accidents.
- Equal employment opportunity (EEO) laws: Avoiding discrimination in hiring, promotion, and compensation practices.
- Occupational Safety and Health Administration (OSHA) regulations: Complying with OSHA regulations to ensure a safe and healthy work environment.
Analyzing and Optimizing Compensation and Expenditure Data
Regularly analyzing compensation and expenditure data is crucial for identifying areas for improvement and optimizing costs.
1. Key Performance Indicators (KPIs):
Tracking relevant KPIs provides insights into the effectiveness of compensation and expenditure strategies. Examples include:
- Labor cost per unit: Measures the cost of labor relative to the output produced.
- Employee turnover rate: Indicates the rate at which employees leave the company.
- Overtime hours as a percentage of total hours: Measures the extent of overtime work.
- Workers' compensation costs per employee: Reflects the cost of workplace accidents and injuries.
- Employee satisfaction scores: Indicates employee morale and engagement.
Monitoring these KPIs allows for proactive adjustments to compensation and expenditure strategies.
2. Data Analysis and Reporting:
Regularly analyze compensation and expenditure data to identify trends and areas for improvement. This analysis should include:
- Comparative analysis: Comparing compensation and expenditure data with industry benchmarks and competitors.
- Trend analysis: Identifying trends in labor costs, overtime hours, and other key metrics.
- Cost-benefit analysis: Evaluating the cost-effectiveness of different compensation and expenditure strategies.
Data-driven decision-making allows for informed adjustments and optimization.
3. Continuous Improvement:
Managing production worker compensation and expenditures is an ongoing process that requires continuous improvement. Regularly review and update compensation and benefits packages, keeping in mind the local labor market, and industry trends. This ensures the company remains competitive while controlling costs effectively. Strategies include:
- Regularly review compensation data: Conduct periodic market research to ensure that wages remain competitive.
- Solicit employee feedback: Gather employee feedback on compensation and benefits to identify areas for improvement.
- Implement process improvements: Continuously look for ways to improve efficiency and reduce labor costs.
- Stay up-to-date on labor laws and regulations: Regularly review relevant laws and regulations to ensure compliance.
By effectively managing production worker compensation and expenditures, manufacturers can achieve a balance between attracting and retaining skilled employees, optimizing costs, and maintaining a sustainable and profitable operation. A well-structured compensation plan, coupled with effective expenditure control measures, is essential for long-term success.
Latest Posts
Latest Posts
-
How Many Irregular Verbs Are In The Imperfect Tense
May 23, 2025
-
Crime Scene Photography Webquest Answer Key
May 23, 2025
-
Chapter 3 All Quiet On The Western Front
May 23, 2025
-
Summary Of Act 1 In Julius Caesar
May 23, 2025
-
Hhmi Biointeractive The Eukaryotic Cell Cycle And Cancer Answers
May 23, 2025
Related Post
Thank you for visiting our website which covers about In Managing Production Worker Compensation And Expenditures . We hope the information provided has been useful to you. Feel free to contact us if you have any questions or need further assistance. See you next time and don't miss to bookmark.