How Many Diodes Are Used In A Bridge Rectifier
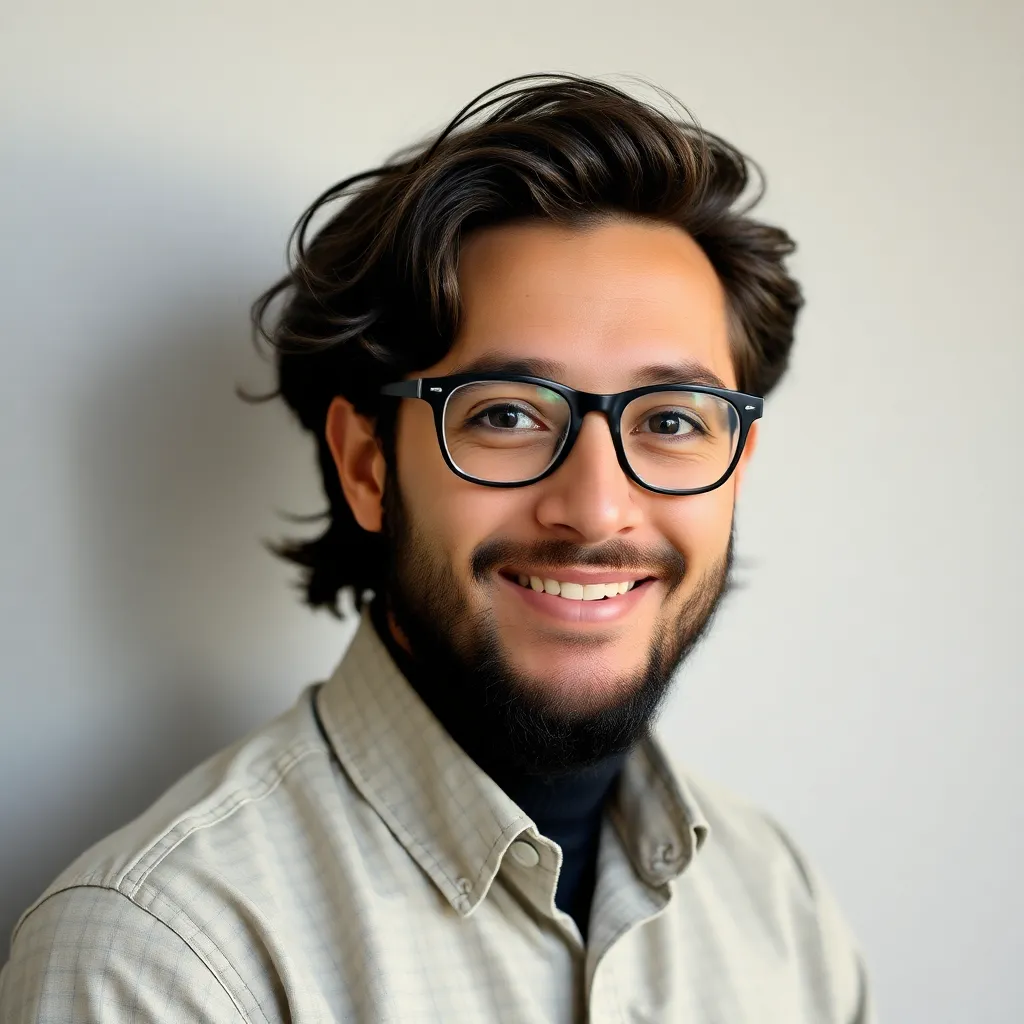
Juapaving
Apr 04, 2025 · 6 min read

Table of Contents
How Many Diodes are Used in a Bridge Rectifier? A Deep Dive into Bridge Rectifier Circuits
The humble bridge rectifier. A seemingly simple circuit, yet its widespread use in power supplies and countless electronic devices speaks volumes about its importance. But a fundamental question often arises, especially for those new to electronics: how many diodes are used in a bridge rectifier? The answer is straightforward: four. This article will delve deeper into this seemingly simple answer, exploring the configuration, functionality, and various applications of this essential circuit component. We'll also examine different types of bridge rectifiers and considerations for choosing the right one for your application.
Understanding the Bridge Rectifier Configuration
The core of a bridge rectifier lies in its arrangement of four diodes. These diodes are strategically positioned to allow current to flow in only one direction, effectively converting alternating current (AC) into pulsating direct current (DC). This conversion is crucial in many electronic devices that require a stable DC power source.
The Four Diodes: A Crucial Arrangement
The four diodes are arranged in a bridge-like configuration, hence the name "bridge rectifier." This arrangement ensures that regardless of the AC input polarity, current always flows in the same direction through the load. This unidirectional flow is the key to rectification.
How the Diodes Work Together
Let's examine the operation during a single AC cycle:
-
Positive Half-Cycle: During the positive half-cycle of the AC input, diodes D1 and D2 are forward-biased, allowing current to flow through them and the load. Diodes D3 and D4 are reverse-biased and thus block current flow.
-
Negative Half-Cycle: During the negative half-cycle, diodes D3 and D4 are forward-biased, allowing current to flow through them and the load. Diodes D1 and D2 are reverse-biased and block current flow.
This process repeats for each AC cycle, resulting in a pulsating DC output. The pulsating nature is due to the abrupt switching of the diodes; the output voltage is not a smooth DC voltage but rather a series of pulses.
Types of Bridge Rectifiers
While the basic principle remains the same – four diodes arranged in a bridge – there are variations in bridge rectifier designs based on their intended application and the required performance characteristics.
1. Single-Phase Bridge Rectifier
This is the most common type, suitable for lower power applications. It utilizes four diodes to rectify a single-phase AC input, as described above. This configuration is cost-effective and simple to implement.
2. Three-Phase Bridge Rectifier
Used in higher-power applications, the three-phase bridge rectifier utilizes six diodes to rectify a three-phase AC input. This configuration produces a smoother DC output with less ripple compared to a single-phase bridge rectifier. This smoother output is highly desirable in applications requiring stable DC power, such as industrial power supplies and motor control systems.
3. Full-Wave Bridge Rectifier vs. Half-Wave Rectifier
It's important to distinguish between full-wave and half-wave rectification. A full-wave bridge rectifier, as described above, utilizes all four diodes to rectify both the positive and negative half-cycles of the AC input, resulting in a higher average DC output voltage. A half-wave rectifier, in contrast, uses only one diode and rectifies only half of the AC cycle, resulting in a lower average DC output voltage and significant ripple. The full-wave bridge rectifier is generally preferred for its superior performance.
Beyond the Basic Four Diodes: Additional Components
While the core of a bridge rectifier consists of four diodes, many practical applications incorporate additional components to improve performance and safety.
1. Filter Capacitors: Smoothing the DC Output
The pulsating DC output of a bridge rectifier is often unsuitable for many electronic devices. To smooth the output and provide a more stable DC voltage, filter capacitors are added to the circuit. These capacitors store charge during the peaks of the rectified waveform and release it during the valleys, effectively reducing the ripple voltage. The capacitance value significantly impacts the smoothing effectiveness; higher capacitance values lead to better smoothing but also increased cost and size.
2. Input Filters: Suppressing Noise and Harmonics
AC input lines often contain noise and harmonic frequencies that can interfere with the rectifier's operation. Input filters, often comprising inductors and capacitors, can help suppress these unwanted frequencies before they reach the rectifier. This enhances the rectifier's efficiency and protects sensitive electronic components.
3. Output Filters: Further Ripple Reduction
In addition to the main filter capacitor, additional filtering components might be used to further reduce the ripple voltage and provide an even smoother DC output. These could include additional capacitors, inductors, or even more sophisticated filtering circuits, like LC filters or active filters.
4. Surge Protection Devices: Protecting Against Voltage Spikes
Voltage spikes and surges can damage the diodes in a bridge rectifier. Surge protection devices, such as metal-oxide varistors (MOVs), are often incorporated to absorb transient voltage spikes and protect the rectifier from damage.
Choosing the Right Bridge Rectifier: Key Considerations
Selecting the appropriate bridge rectifier depends on several factors:
1. Voltage Rating: Handling the Input Voltage
The diodes in the bridge rectifier must have a reverse breakdown voltage higher than the peak AC input voltage. Selecting diodes with insufficient voltage ratings can lead to diode failure.
2. Current Rating: Supporting the Load Current
The diodes should have a current rating sufficient to handle the maximum load current. A diode with insufficient current rating will overheat and fail.
3. Package Type: Physical Size and Mounting
Bridge rectifiers are available in various package types, such as through-hole, surface-mount, and power packages. The choice depends on the physical constraints of the application and the power dissipation requirements.
4. Temperature Considerations: Managing Heat Dissipation
Higher current applications generate more heat, necessitating proper heat dissipation. Heat sinks might be required to maintain the diodes within their operating temperature range.
Applications of Bridge Rectifiers: A Wide Range of Uses
The versatility of bridge rectifiers makes them essential components in a vast array of electronic systems.
-
Power Supplies: A core component in virtually all power supplies, converting AC mains voltage to the DC voltage required by electronic devices.
-
Battery Chargers: Used in battery chargers to convert AC input to DC to charge batteries.
-
Audio Amplifiers: Present in many audio amplifiers to provide the DC power needed to amplify audio signals.
-
Motor Control Systems: Used in motor control systems to provide the DC voltage required to drive motors.
-
Inverters: A crucial part of inverters, converting DC to AC. While they don't directly rectify, they use diodes for various switching operations within the inverter circuit.
-
Welding Machines: Used in some welding machines to provide the required DC current for welding.
-
DC-DC Converters: Though not directly rectifying AC, some DC-DC converter designs incorporate bridge rectifiers for intermediate voltage rectification steps.
Conclusion: The Unsung Hero of Electronics
The seemingly simple bridge rectifier, with its four diodes, is an essential component in countless electronic applications. Understanding its functionality, various types, and considerations for selection is crucial for anyone working with electronics. While the number of diodes remains consistently four for the basic configuration, the supporting components and design choices can significantly impact the performance and suitability of the bridge rectifier for a specific application. From simple power supplies to sophisticated industrial control systems, the bridge rectifier remains an unsung hero, quietly enabling the functionality of countless devices we use every day.
Latest Posts
Latest Posts
-
What Is Bond Order Of No
Apr 11, 2025
-
Is 11 A Prime Or Composite
Apr 11, 2025
-
How Tall Is 81 Inches In Feet
Apr 11, 2025
-
How Many Feet Are 40 Inches
Apr 11, 2025
-
What Is 5 9 As A Percentage
Apr 11, 2025
Related Post
Thank you for visiting our website which covers about How Many Diodes Are Used In A Bridge Rectifier . We hope the information provided has been useful to you. Feel free to contact us if you have any questions or need further assistance. See you next time and don't miss to bookmark.