How Do You Calculate The Efficiency Of A Machine
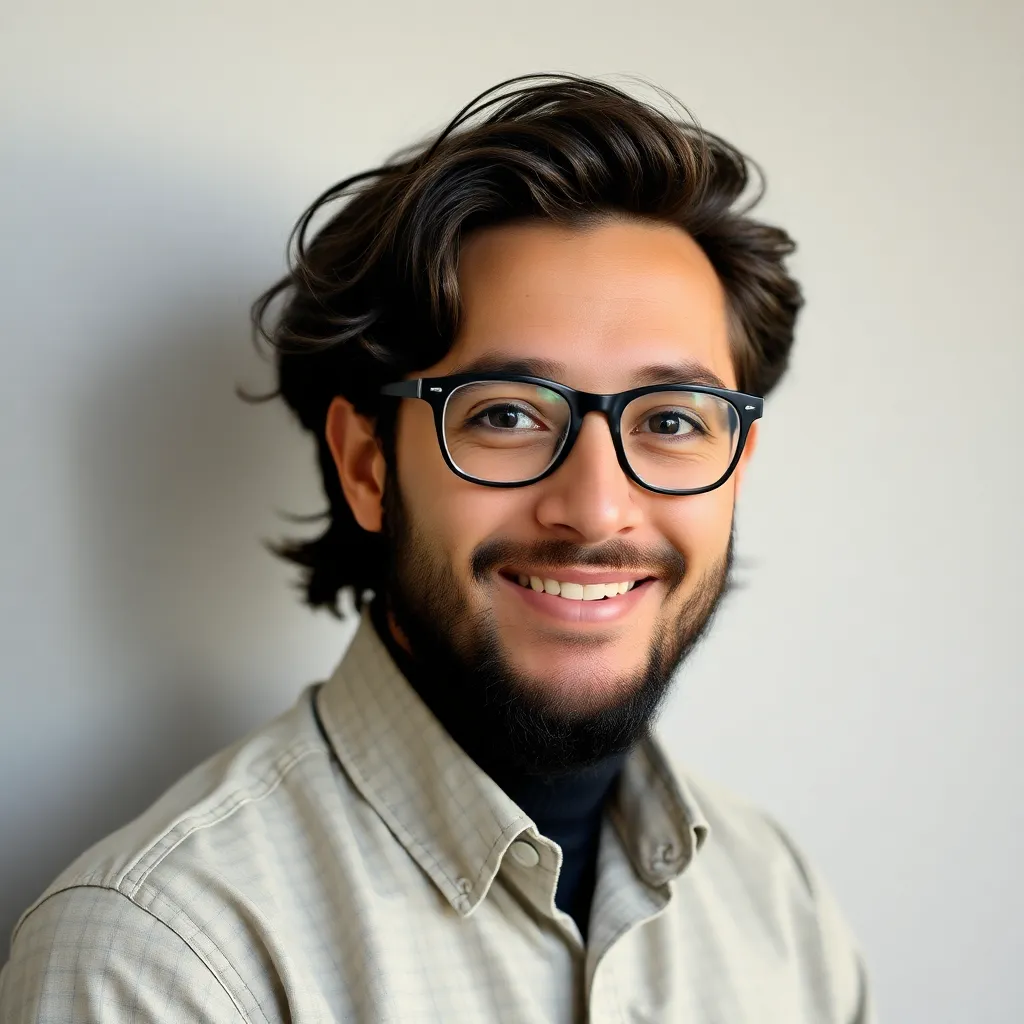
Juapaving
May 10, 2025 · 6 min read
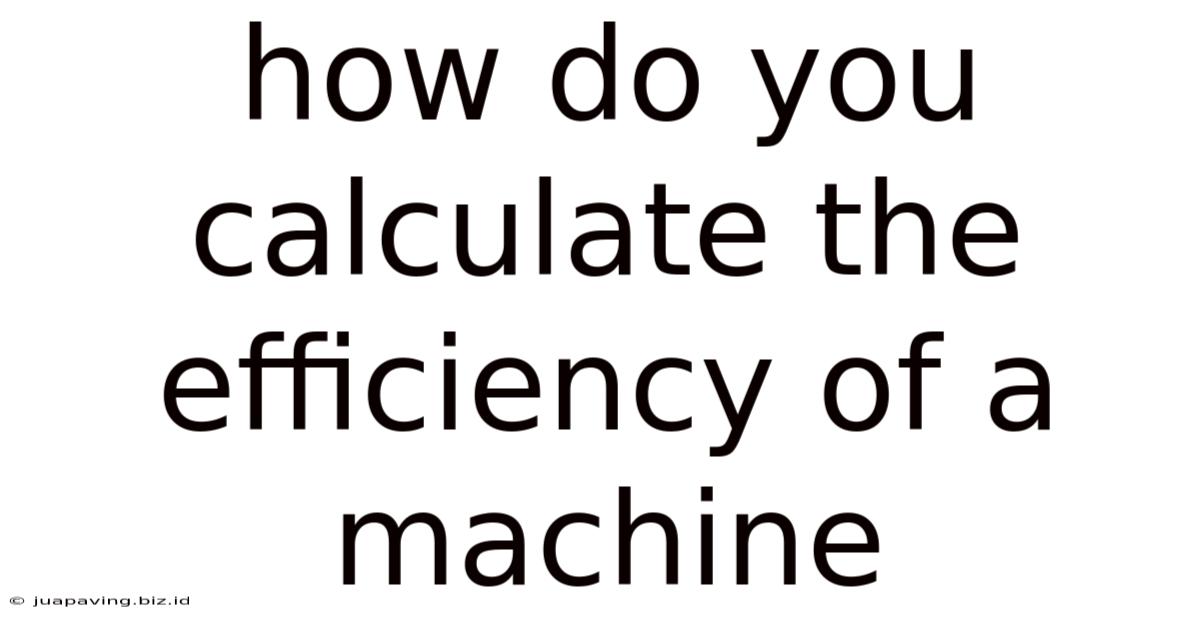
Table of Contents
How Do You Calculate the Efficiency of a Machine? A Comprehensive Guide
Understanding the efficiency of a machine is crucial in various fields, from engineering and manufacturing to energy conservation and environmental sustainability. A machine's efficiency represents how effectively it converts input energy into useful output work. This article delves deep into the methods and concepts involved in calculating machine efficiency, encompassing various types of machines and their specific considerations.
Defining Efficiency: The Ratio of Output to Input
At its core, machine efficiency is defined as the ratio of useful output work to the total input energy. This ratio is typically expressed as a percentage. The formula is straightforward:
Efficiency (%) = (Useful Output Work / Total Input Energy) x 100
However, the complexities lie in accurately determining both the useful output work and the total input energy. The methods for this vary significantly depending on the type of machine.
Identifying Useful Output Work: The Key to Accurate Calculations
Determining "useful output work" is often the most challenging aspect of calculating efficiency. It represents the actual work accomplished by the machine that aligns with its intended purpose. This requires careful consideration of losses and inefficiencies within the system.
Examples of Useful Output Work:
-
Motor: The rotational energy delivered to a load, measured in Joules (J) or kilowatt-hours (kWh). Losses due to friction in bearings or heat generation within the motor itself are not considered useful work.
-
Pump: The amount of fluid pumped to a specific height or pressure, often expressed in terms of energy transferred to the fluid. Leakage and frictional losses within the pump system are excluded from useful output work.
-
Internal Combustion Engine: The mechanical energy delivered to the crankshaft, after accounting for losses due to friction, exhaust heat, and incomplete combustion. This is often measured through brake horsepower (bhp).
-
Heat Engine: The amount of heat energy converted into mechanical work. Much of the input heat is lost as waste heat, which is not considered useful output.
-
Solar Panel: The amount of electrical energy produced, measured in kilowatt-hours (kWh). Losses due to reflection, internal resistance, and temperature effects are excluded.
Critical Note: Accurately quantifying useful output work demands a thorough understanding of the machine's operational principles and the specific factors contributing to energy losses.
Determining Total Input Energy: Accounting for All Energy Sources
The total input energy encompasses all forms of energy supplied to the machine to perform its intended function. This can include:
-
Electrical Energy: Measured in kilowatt-hours (kWh) or Joules (J), this is a common input for electric motors, pumps, and other electrically powered devices.
-
Chemical Energy: For internal combustion engines and other combustion-based systems, this is the energy released from the combustion of fuel, typically calculated from the fuel's heating value and the amount of fuel consumed.
-
Thermal Energy: In heat engines, this is the heat energy supplied from a source such as a boiler or a nuclear reactor.
-
Hydraulic Energy: For hydraulic systems, this is the energy contained in the pressurized fluid.
-
Mechanical Energy: For machines driven by mechanical means (e.g., a water wheel), this refers to the initial mechanical energy supplied.
Accurate measurement of input energy often relies on specialized instruments like power meters, flow meters, and calorimeters, depending on the energy type.
Types of Losses and Their Impact on Efficiency
Understanding the various sources of energy loss is vital for accurately assessing a machine's efficiency. These losses significantly reduce the ratio of output work to input energy. Common loss mechanisms include:
1. Frictional Losses:
Friction between moving parts consumes energy as heat, reducing the amount of energy available for useful work. This is prevalent in mechanical systems with rotating parts, such as gears, bearings, and shafts.
2. Heat Losses:
Many machines generate heat as a byproduct of their operation. This heat energy is typically dissipated to the environment and is not converted into useful work, thus reducing efficiency. Examples include heat generated by friction, electrical resistance, and incomplete combustion.
3. Leakage Losses:
In fluid systems like pumps and hydraulic systems, leakage of fluid represents a loss of energy. This reduces the amount of fluid effectively delivered, leading to a lower efficiency.
4. Windage Losses:
Rotating parts create air resistance, which consumes energy. This is particularly significant for high-speed rotating machinery such as turbines and fans.
5. Electrical Losses:
In electrically powered machines, losses can occur due to resistance in wires and other electrical components. This leads to energy being dissipated as heat rather than being converted into mechanical energy.
Calculating Efficiency for Specific Machine Types
The calculation method varies depending on the machine type. Let's explore a few examples:
1. Electric Motor Efficiency:
Efficiency (%) = (Output Power / Input Power) x 100
Output Power is typically measured using a dynamometer, while Input Power is measured using a power meter.
2. Internal Combustion Engine Efficiency:
Efficiency (%) = (Brake Power / Fuel Energy Input) x 100
Brake Power is the power delivered to the crankshaft, while Fuel Energy Input is determined from the fuel's heating value and consumption rate.
3. Pump Efficiency:
Efficiency (%) = (Hydraulic Power / Input Power) x 100
Hydraulic Power represents the energy transferred to the fluid, calculated from flow rate, pressure, and density. Input power is the power consumed by the pump's motor.
4. Heat Engine Efficiency (e.g., Steam Turbine):
Efficiency (%) = (Mechanical Work Output / Heat Input) x 100
This involves measuring the mechanical work done by the turbine and the heat energy supplied to the steam.
Improving Machine Efficiency: Strategies and Techniques
Improving machine efficiency is a continuous pursuit in engineering and manufacturing. Strategies include:
-
Reducing Friction: Using better lubricants, optimizing bearing designs, and employing low-friction materials.
-
Minimizing Heat Losses: Implementing insulation, using more efficient heat exchangers, and optimizing combustion processes.
-
Reducing Leakage: Employing better sealing techniques and improving design to minimize fluid leaks.
-
Optimizing Design: Computational fluid dynamics (CFD) and finite element analysis (FEA) can be used to optimize designs and minimize energy losses.
-
Using More Efficient Materials: Selecting materials with higher strength-to-weight ratios can reduce friction and improve performance.
-
Advanced Control Systems: Implementing advanced control systems can optimize the machine's operation for maximum efficiency.
Conclusion: A Continuous Pursuit of Optimization
Calculating the efficiency of a machine is a multifaceted process that requires a deep understanding of the machine's operational principles and energy conversion processes. Accurately determining both useful output work and total input energy, while accounting for various loss mechanisms, is crucial for obtaining meaningful results. By employing the methods outlined above and implementing strategies for improvement, engineers and manufacturers can continuously strive to optimize machine efficiency, leading to reduced energy consumption, improved productivity, and enhanced sustainability. The pursuit of higher efficiency is an ongoing process of refinement and innovation, constantly pushing the boundaries of what's possible in mechanical and electrical systems.
Latest Posts
Latest Posts
-
What Is The Name For Pcl5
May 10, 2025
-
The Third Law Of Thermodynamics States That
May 10, 2025
-
How Much Is 30 Of 1500
May 10, 2025
-
The Two Bases That Are Purines Are
May 10, 2025
-
How Long Is 32 Cm In Inches
May 10, 2025
Related Post
Thank you for visiting our website which covers about How Do You Calculate The Efficiency Of A Machine . We hope the information provided has been useful to you. Feel free to contact us if you have any questions or need further assistance. See you next time and don't miss to bookmark.