Examples Of Questions That Focus On Process Include:
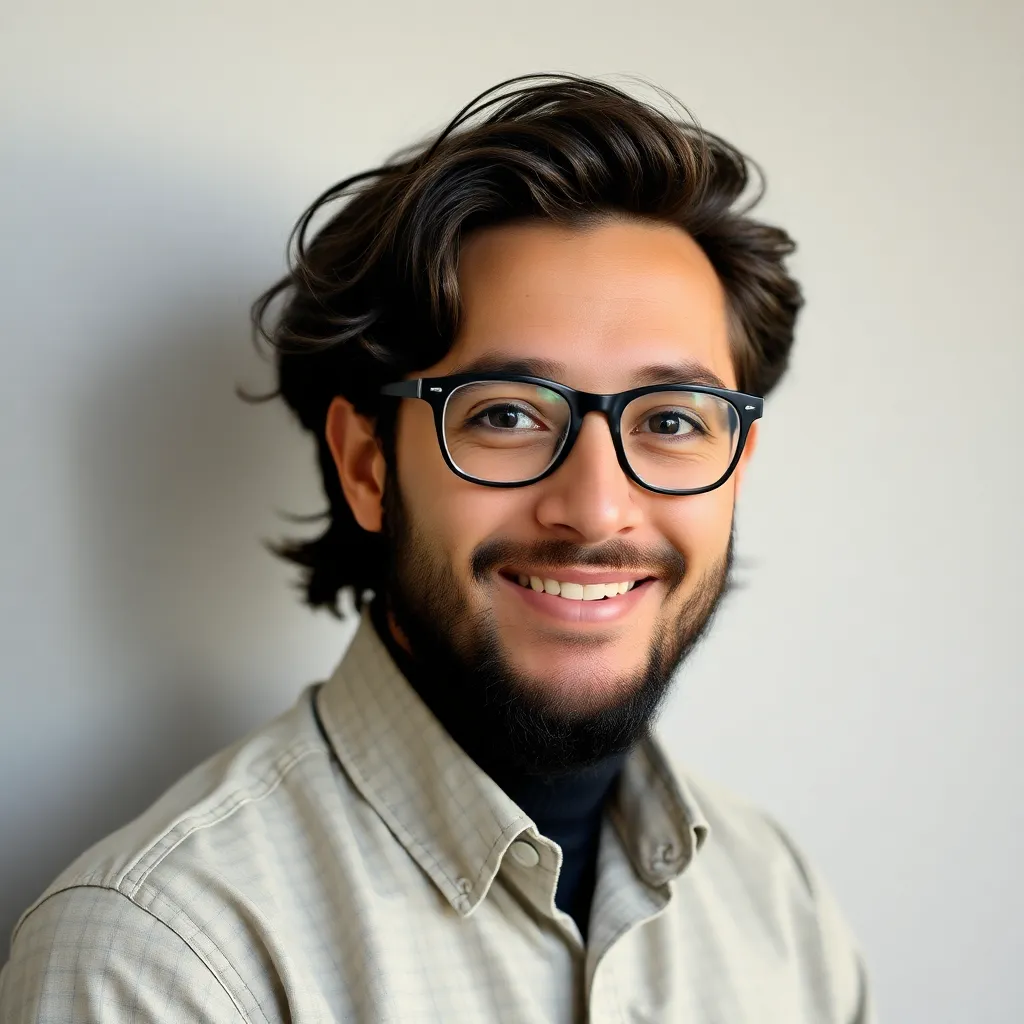
Juapaving
May 24, 2025 · 7 min read
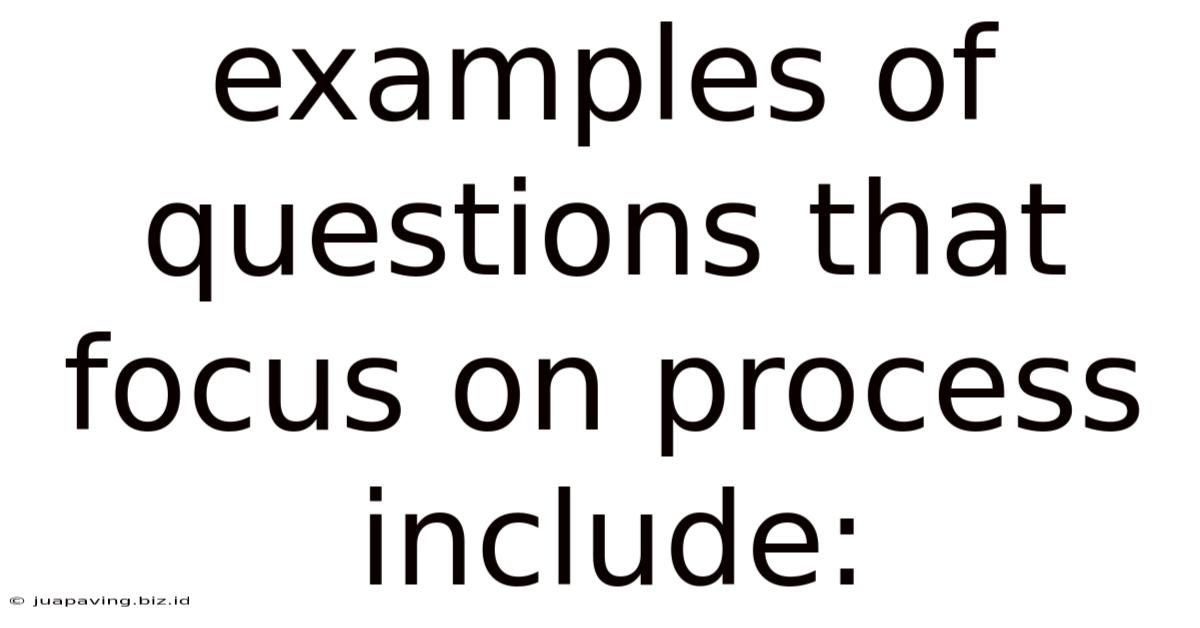
Table of Contents
Examples of Questions That Focus on Process: A Deep Dive into Process-Oriented Inquiry
Understanding processes is crucial for improvement in any field, from manufacturing to project management, customer service to software development. Asking the right questions about processes is the cornerstone of identifying bottlenecks, inefficiencies, and areas ripe for optimization. This article delves deep into the world of process-oriented questions, providing numerous examples categorized by their purpose and application. We'll explore how these questions help uncover hidden problems, streamline workflows, and ultimately, drive success.
Why Focus on Process Questions?
Before diving into specific examples, let's understand the fundamental importance of focusing on process questions. Unlike outcome-focused questions (e.g., "Did we meet the deadline?"), process questions delve into how the outcome was achieved. This granular level of inquiry reveals critical information often overlooked in a simple success/failure assessment. By understanding the process, we can:
- Identify bottlenecks: Pinpoint stages where delays or inefficiencies occur.
- Improve efficiency: Streamline workflows to reduce wasted time and resources.
- Enhance quality: Uncover sources of errors and implement preventative measures.
- Boost productivity: Optimize individual tasks and their sequencing for maximum output.
- Increase team collaboration: Identify points of friction and communication breakdowns.
- Foster innovation: Discover opportunities to improve existing processes or implement new ones.
- Reduce costs: Minimize waste and optimize resource allocation.
- Improve customer satisfaction: Identify and address pain points in customer-facing processes.
- Minimize risks: Proactively identify and mitigate potential problems before they arise.
Categorizing Process-Oriented Questions
Process questions can be broadly categorized based on their purpose:
I. Understanding the Current State: Diagnostic Questions
These questions aim to map the existing process, identify its strengths and weaknesses, and uncover areas needing improvement.
-
Step-by-Step Breakdown:
- "What are the individual steps involved in this process?"
- "Can you walk me through the process from start to finish?"
- "What are the inputs and outputs of each step?"
- "What are the decision points in the process?"
- "What triggers the transition from one step to the next?"
- "How long does each step typically take?"
- "What tools and resources are required for each step?"
-
Resource Allocation and Utilization:
- "What resources (people, materials, technology) are used in this process?"
- "Are resources being used efficiently?"
- "Are there any bottlenecks in resource allocation?"
- "Are there any underutilized resources?"
- "How is resource usage tracked and measured?"
-
Identifying Pain Points:
- "What are the biggest challenges or obstacles in this process?"
- "Where do the most frequent errors occur?"
- "What are the biggest sources of delays or inefficiencies?"
- "What are the common complaints or frustrations associated with this process?"
- "Where are the points of friction or conflict?"
-
Measurement and Metrics:
- "How is the success of this process measured?"
- "What key performance indicators (KPIs) are used to track performance?"
- "What data is collected to monitor the process?"
- "How is this data analyzed and used to improve the process?"
II. Identifying Areas for Improvement: Analytical Questions
These questions go beyond simply describing the process and delve into potential improvements.
-
Efficiency and Optimization:
- "Are there any steps that can be eliminated or combined?"
- "Can any steps be automated?"
- "Can the sequence of steps be improved?"
- "Can we improve the efficiency of any particular step?"
- "Are there any redundant steps?"
- "Can we leverage technology to streamline the process?"
-
Quality Enhancement:
- "Where are the opportunities to improve the quality of the output?"
- "How can we prevent errors or defects?"
- "What quality control measures are in place?"
- "Are these measures sufficient?"
- "How can we improve the accuracy and reliability of the process?"
-
Risk Management:
- "What are the potential risks or problems associated with this process?"
- "How can we mitigate these risks?"
- "What contingency plans are in place?"
- "How can we improve the process's resilience to unexpected events?"
-
Innovation and Creativity:
- "Are there any innovative approaches to this process that could be implemented?"
- "What best practices from other organizations could be adopted?"
- "How can we leverage new technologies or methodologies to improve this process?"
- "What are the opportunities for continuous improvement?"
III. Implementing and Monitoring Change: Action-Oriented Questions
These questions focus on putting improvements into practice and tracking their effectiveness.
-
Implementation Planning:
- "What steps are needed to implement the proposed improvements?"
- "What resources are required for implementation?"
- "What is the timeline for implementation?"
- "Who is responsible for each step of the implementation?"
-
Monitoring and Evaluation:
- "How will the effectiveness of the improvements be measured?"
- "What KPIs will be tracked?"
- "How frequently will the process be monitored?"
- "What adjustments will be made based on the monitoring results?"
-
Feedback and Iteration:
- "How will feedback be collected from stakeholders?"
- "How will this feedback be used to further improve the process?"
- "How will we ensure continuous improvement?"
- "What mechanisms are in place for ongoing process review?"
Examples Across Different Industries
The power of process-oriented questions is evident across diverse industries. Here are a few examples:
1. Manufacturing:
- Current State: "What are the bottlenecks in our assembly line?" "How much downtime do we experience due to equipment malfunctions?" "What are the defect rates for each stage of production?"
- Improvement: "Can we automate any part of the assembly process?" "How can we improve worker training to reduce errors?" "Can we implement a preventative maintenance program to reduce equipment downtime?"
- Implementation: "What is the cost-benefit analysis of implementing new automation technology?" "How will we track the effectiveness of the new training program?"
2. Software Development:
- Current State: "What are the common bugs encountered during testing?" "How long does it typically take to resolve a bug?" "What is the average time spent on code review?"
- Improvement: "Can we implement a more robust testing framework?" "Can we use automation to speed up the testing process?" "Can we improve the code review process to catch bugs earlier?"
- Implementation: "What tools can we use to automate the testing process?" "How will we measure the effectiveness of the new testing framework?"
3. Customer Service:
- Current State: "What is the average wait time for customers?" "What are the most common customer complaints?" "What is the customer satisfaction rating?"
- Improvement: "Can we improve our customer support system?" "Can we implement a knowledge base to help customers solve problems independently?" "Can we improve employee training to enhance customer interactions?"
- Implementation: "How will we track customer wait times and satisfaction ratings?" "How will we measure the effectiveness of the new knowledge base?"
4. Project Management:
- Current State: "What are the critical path activities in this project?" "What are the potential risks and issues?" "How is project progress being tracked?"
- Improvement: "Can we improve the communication between team members?" "Can we use project management software to improve task tracking and reporting?" "Can we implement a risk management plan to mitigate potential problems?"
- Implementation: "What project management software will we use?" "How will we measure project progress and success?"
5. Healthcare:
- Current State: "How long does it take to process patient records?" "What are the common errors in medication administration?" "What is the patient satisfaction score?"
- Improvement: "Can we implement electronic health records (EHR) to streamline record processing?" "Can we implement a medication reconciliation process to reduce medication errors?" "Can we improve patient communication and education?"
- Implementation: "How will we train staff on the new EHR system?" "How will we track medication errors and patient satisfaction?"
Conclusion: The Ongoing Quest for Process Improvement
Asking the right questions is fundamental to understanding, optimizing, and continuously improving processes. By using a structured approach, categorized by diagnostic, analytical, and action-oriented questions, organizations can identify bottlenecks, enhance efficiency, improve quality, and foster innovation. The examples provided across various industries illustrate the broad applicability of this process-focused inquiry. Remember, the quest for process improvement is ongoing; continuous monitoring, evaluation, and adaptation are key to sustained success. By embracing a culture of questioning and continuous improvement, organizations can unlock significant gains in productivity, efficiency, and overall performance.
Latest Posts
Latest Posts
-
What Is The Theme In The Hobbit
May 25, 2025
-
Myths Often Function As A Connection To The
May 25, 2025
-
Elie Wiesel Night Chapter 1 Summary
May 25, 2025
-
Characters In The Song Of Roland
May 25, 2025
-
How Long Must Paperwork From Residue Turn In Be Kept
May 25, 2025
Related Post
Thank you for visiting our website which covers about Examples Of Questions That Focus On Process Include: . We hope the information provided has been useful to you. Feel free to contact us if you have any questions or need further assistance. See you next time and don't miss to bookmark.