Difference Between Ac And Dc Motors
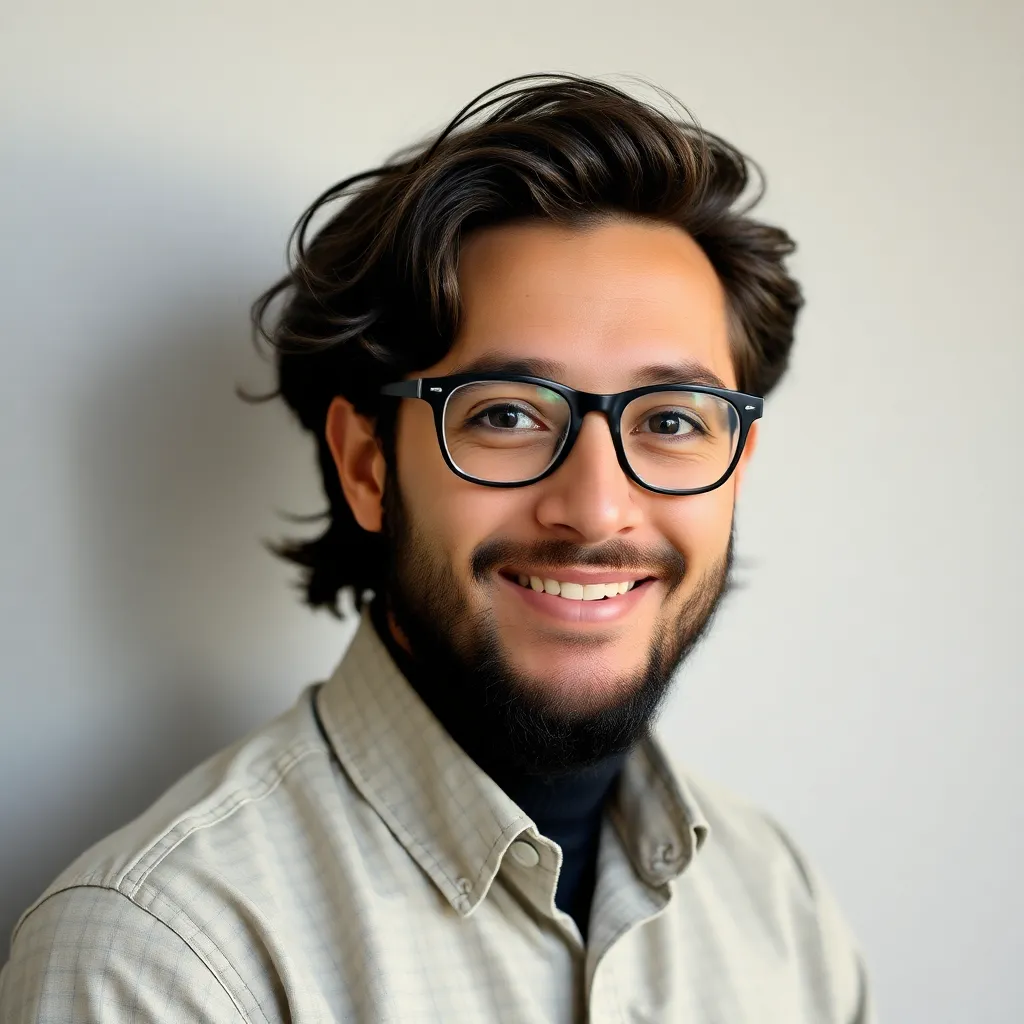
Juapaving
Mar 14, 2025 · 6 min read
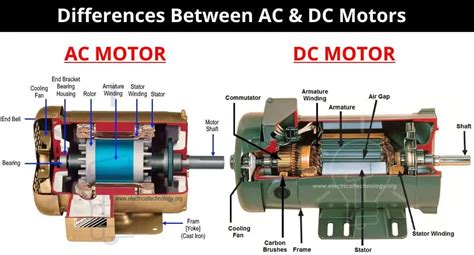
Table of Contents
- Difference Between Ac And Dc Motors
- Table of Contents
- AC vs. DC Motors: A Deep Dive into the Differences
- Understanding the Fundamentals: AC vs. DC Power
- Key Differences Between AC and DC Motors: A Comparative Analysis
- 1. Construction and Design
- 2. Starting Torque
- 3. Speed Control
- 4. Maintenance
- 5. Efficiency
- 6. Cost
- 7. Applications
- Choosing the Right Motor: A Decision Matrix
- Conclusion: The Ongoing Evolution of Motor Technology
- Latest Posts
- Latest Posts
- Related Post
AC vs. DC Motors: A Deep Dive into the Differences
The world of electric motors is vast and varied, but two fundamental types dominate the landscape: Alternating Current (AC) and Direct Current (DC) motors. While both achieve the same basic function – converting electrical energy into mechanical energy – they do so through vastly different mechanisms, leading to significant differences in their characteristics, applications, and overall suitability for specific tasks. This comprehensive guide will delve into the core distinctions between AC and DC motors, illuminating their unique strengths and weaknesses.
Understanding the Fundamentals: AC vs. DC Power
Before diving into the specifics of motor types, it's crucial to grasp the difference between AC and DC power itself. This fundamental difference underpins all the subsequent distinctions in motor operation.
-
Direct Current (DC): DC electricity flows in a single direction, maintaining a constant voltage and current. Think of a battery; it provides a steady stream of electrons from the negative to the positive terminal. This unidirectional flow simplifies the design and control of DC motors.
-
Alternating Current (AC): AC electricity, on the other hand, periodically reverses its direction. The voltage and current oscillate, typically following a sinusoidal waveform. This cyclical change in direction is a defining characteristic of AC power, which is the standard for most household and industrial power grids.
Key Differences Between AC and DC Motors: A Comparative Analysis
The fundamental difference in power source leads to significant variations in the design, operation, and performance characteristics of AC and DC motors. Let's explore these key distinctions:
1. Construction and Design
-
DC Motors: DC motors are typically characterized by their commutator and brushes. The commutator is a segmented cylindrical component that reverses the direction of current flow in the motor's rotor, ensuring continuous rotation. Brushes provide the electrical contact between the power source and the commutator. This design, however, introduces friction and wear, limiting the lifespan and speed of the motor. Furthermore, DC motors often employ permanent magnets or electromagnets for their field windings.
-
AC Motors: AC motors avoid the complexities of commutators and brushes. Instead, they rely on the alternating current itself to induce magnetic fields in the rotor, producing rotation. The most common AC motor types are induction motors (asynchronous) and synchronous motors. Induction motors utilize the principles of electromagnetic induction to create a rotating magnetic field that interacts with the rotor, inducing currents and resulting in torque. Synchronous motors, in contrast, maintain a constant speed synchronized with the frequency of the AC power supply. They often employ permanent magnets or wound rotors.
2. Starting Torque
-
DC Motors: DC motors, particularly series-wound motors, boast high starting torque. This makes them ideal for applications requiring immediate and powerful rotational force, such as electric vehicles or cranes.
-
AC Motors: The starting torque of AC motors is generally lower than that of DC motors, especially induction motors. However, modern designs and control techniques have significantly improved the starting torque capabilities of AC motors, reducing this disadvantage. Synchronous motors typically have high starting torque, but often require specialized starting mechanisms.
3. Speed Control
-
DC Motors: Speed control in DC motors is relatively simple and precise. Adjusting the voltage or current supplied to the motor directly affects its speed. This makes them highly versatile for applications needing variable speed control.
-
AC Motors: Speed control in AC motors is more complex. While it's achievable, it often necessitates sophisticated control electronics, such as Variable Frequency Drives (VFDs). VFDs modify the frequency and voltage of the AC power supply, allowing for precise speed adjustments. However, this adds to the cost and complexity of the system.
4. Maintenance
-
DC Motors: The presence of brushes and commutators in DC motors requires periodic maintenance. These components wear down over time, necessitating replacement. This increases the maintenance costs and downtime associated with DC motors.
-
AC Motors: AC motors, especially induction motors, are significantly less maintenance-intensive. The absence of brushes and commutators translates into longer operational lifespans and reduced maintenance requirements. This contributes to lower overall lifecycle costs.
5. Efficiency
-
DC Motors: The efficiency of DC motors can be high, especially in smaller sizes. However, losses due to brush friction and commutation can impact overall efficiency at higher power levels.
-
AC Motors: AC motors, particularly induction motors, generally exhibit high efficiency, especially at larger power ratings. Advances in motor design and manufacturing have significantly improved the efficiency of AC motors, making them a preferred choice for many energy-conscious applications.
6. Cost
-
DC Motors: DC motors can be relatively cost-effective, especially for lower power applications. However, the need for control electronics for variable speed operation can increase the overall system cost.
-
AC Motors: The cost of AC motors can vary depending on the type and power rating. Induction motors are generally less expensive than other AC motor types, particularly at higher power levels. However, the inclusion of VFDs for speed control increases the overall system cost.
7. Applications
The distinct characteristics of AC and DC motors lend themselves to different applications:
-
DC Motors: DC motors find extensive use in:
- Electric vehicles: Their high starting torque makes them suitable for accelerating vehicles.
- Robotics: Precision speed control is crucial for robotic movements.
- Industrial automation: Their versatility in controlling speed and torque makes them useful in various industrial processes.
- Power tools: The high power-to-weight ratio of DC motors makes them suitable for portable applications.
-
AC Motors: AC motors dominate in:
- Household appliances: Refrigerators, washing machines, and fans utilize the simplicity and cost-effectiveness of induction motors.
- Industrial machinery: Large-scale industrial processes often benefit from the efficiency and robustness of AC motors.
- HVAC systems: The consistent speed and high efficiency of AC motors are ideal for air conditioning and ventilation systems.
- Electric power generation: Synchronous motors are commonly used in power generation systems to maintain stable frequency and voltage.
Choosing the Right Motor: A Decision Matrix
Selecting the appropriate motor – AC or DC – hinges on carefully evaluating the specific requirements of the application. Here's a simplified decision matrix to guide your choice:
Feature | DC Motor | AC Motor |
---|---|---|
Starting Torque | High | Moderate to High (depends on the type) |
Speed Control | Easy and Precise | More Complex, often requires VFDs |
Maintenance | Higher (brushes and commutator) | Lower (generally maintenance-free) |
Efficiency | High (at lower powers), can be lower at higher powers | Generally High (especially induction motors) |
Cost | Can be lower (but system cost can be higher with speed controls) | Can be lower (induction motors) but higher with VFDs |
Applications | EVs, robotics, power tools | Household appliances, industrial machinery |
Conclusion: The Ongoing Evolution of Motor Technology
The choice between AC and DC motors isn't a simple "one-size-fits-all" decision. The optimal selection depends on a careful assessment of factors such as starting torque requirements, speed control needs, maintenance considerations, efficiency targets, and cost constraints. Technological advancements are continually improving both AC and DC motor technologies, leading to higher efficiency, greater controllability, and improved reliability across diverse applications. As technology evolves, the lines between AC and DC motor applications may become even more blurred, with hybrid designs and innovative control systems further refining their capabilities and expanding their potential uses. Understanding the fundamental differences detailed above provides a strong foundation for making informed decisions about motor selection for any given project.
Latest Posts
Latest Posts
-
How Many Billions Are In A Trillion
Mar 15, 2025
-
Verbs With Ing At The End
Mar 15, 2025
-
What Is 50 Pounds In Kilograms
Mar 15, 2025
-
What Is 40 Percent Of 150
Mar 15, 2025
-
What Are The Common Multiples Of 9 And 12
Mar 15, 2025
Related Post
Thank you for visiting our website which covers about Difference Between Ac And Dc Motors . We hope the information provided has been useful to you. Feel free to contact us if you have any questions or need further assistance. See you next time and don't miss to bookmark.