Capacity Cushion Can Be Determined By
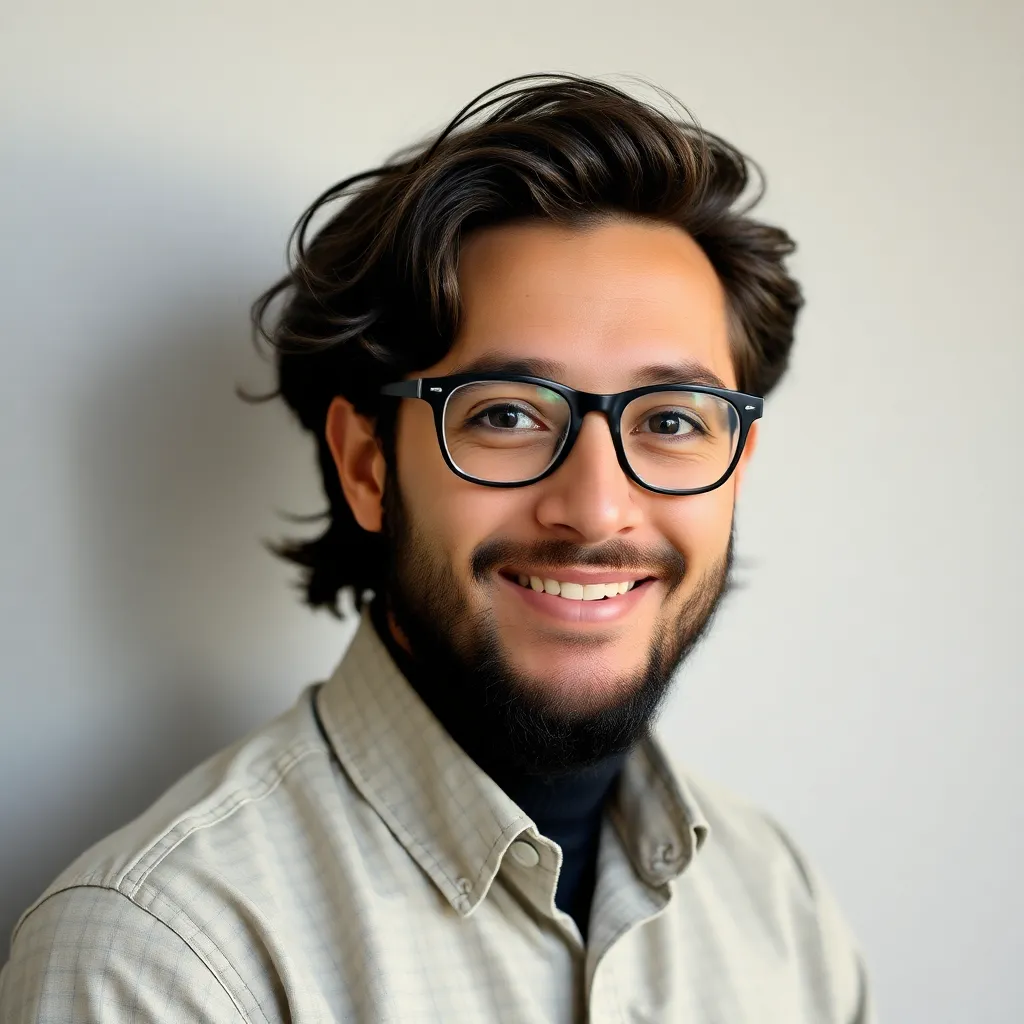
Juapaving
May 25, 2025 · 6 min read
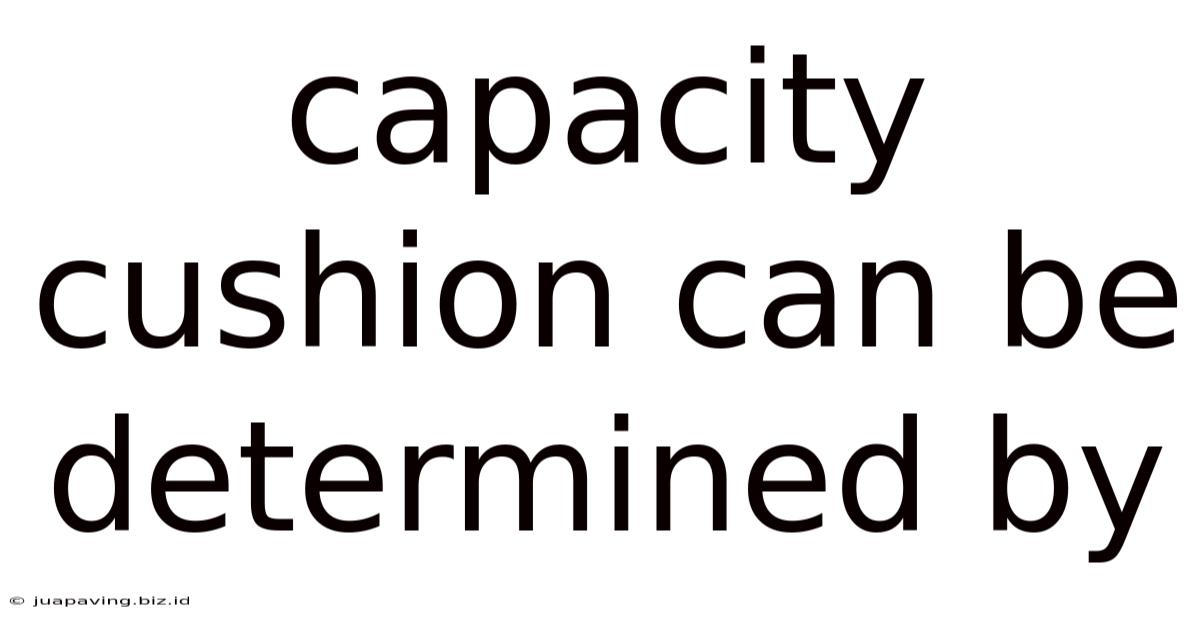
Table of Contents
How Capacity Cushion Can Be Determined: A Comprehensive Guide
Capacity cushion, also known as capacity buffer, is a crucial concept in operations management. It represents the difference between the maximum capacity of a system and the expected or planned output. This buffer acts as a safety net, protecting against unforeseen circumstances that could disrupt production and impact delivery timelines. Determining the appropriate capacity cushion is a critical decision, balancing the costs of excess capacity with the risks of insufficient capacity. This article delves into various methods for determining the optimal capacity cushion for your specific operational needs.
Understanding the Importance of Capacity Cushion
Before exploring the methods for determining capacity cushion, let's solidify the importance of this operational strategy. A well-defined capacity cushion offers numerous advantages:
Mitigating Risk:
- Unforeseen Demand Fluctuations: Market demand is rarely perfectly predictable. Seasonal peaks, unexpected surges, or sudden shifts in consumer preferences can overwhelm a system operating at maximum capacity. A cushion absorbs these fluctuations, preventing order backlogs and delays.
- Equipment Malfunctions and Maintenance: Machines break down. Planned maintenance requires downtime. A capacity cushion allows for these unavoidable events without jeopardizing production schedules.
- Supplier Issues: Delays in raw material delivery or component supply can halt production. A cushion provides a buffer against such disruptions.
- Employee Absenteeism: Illness, vacation, or unexpected absences affect workforce availability. A cushion helps maintain output levels despite temporary staff shortages.
Improving Efficiency and Responsiveness:
- Faster Lead Times: Adequate capacity enables quicker order fulfillment, enhancing customer satisfaction and potentially commanding premium pricing.
- Increased Flexibility: A cushion allows for quicker responses to unexpected opportunities, such as sudden increases in demand or new product introductions.
- Reduced Stress: Knowing that a buffer exists reduces stress on employees and management, enabling more proactive problem-solving and improved decision-making.
Balancing Costs and Risks:
The key challenge lies in finding the right balance. Too much capacity cushion leads to wasted resources (underutilized equipment, idle labor), while too little capacity exposes the business to significant risks, potentially impacting customer relationships and profitability.
Methods for Determining Capacity Cushion
Several methods can be employed to determine the optimal capacity cushion, each with its own strengths and weaknesses. The best approach depends on factors like the industry, production process, market volatility, and risk tolerance.
1. Historical Data Analysis:
This method utilizes past performance data to predict future demand and identify potential capacity needs. Analyzing historical sales figures, production output, and demand fluctuations over several periods (e.g., monthly, quarterly, annually) provides valuable insights.
- Steps:
- Collect data: Gather relevant historical data on sales, production, and demand for a sufficient period. Consider seasonal variations.
- Analyze trends: Identify patterns, seasonality, and trends in demand fluctuations. Use statistical tools like moving averages or exponential smoothing to forecast future demand.
- Calculate cushion: Based on the forecast, determine the difference between maximum capacity and expected demand. This difference represents the capacity cushion.
- Sensitivity analysis: Test the model's robustness by varying parameters (e.g., demand forecast, equipment utilization rates) to assess the impact on the cushion.
2. Simulation Modeling:
Simulation modeling employs computer software to create a virtual representation of the production system. This allows for testing different scenarios and capacity cushion levels without disrupting actual operations.
- Steps:
- Model development: Create a detailed model of the production system, incorporating relevant parameters (e.g., machine capacity, processing times, setup times, defect rates).
- Scenario testing: Simulate various scenarios with different capacity cushion levels, incorporating random variations in demand, equipment failures, and other uncertainties.
- Performance evaluation: Analyze the simulation results, evaluating key metrics like order fulfillment rates, lead times, inventory levels, and costs for each scenario.
- Optimal cushion determination: Select the cushion level that provides the best balance between cost and risk, based on the simulation results.
3. Statistical Forecasting Methods:
Statistical forecasting methods, such as ARIMA (Autoregressive Integrated Moving Average) or exponential smoothing, can provide more sophisticated demand predictions than simple historical averages. These methods consider the underlying trends and seasonality in the data to generate more accurate forecasts.
- Steps:
- Data preparation: Clean and prepare the historical data, addressing missing values and outliers.
- Model selection: Select an appropriate statistical forecasting model based on the characteristics of the data.
- Model fitting: Fit the chosen model to the historical data and generate forecasts for future periods.
- Capacity cushion calculation: Determine the capacity cushion based on the forecasted demand and the maximum capacity of the system. Consider safety factors to account for forecast errors.
4. Qualitative Methods:
In situations where historical data is limited or unreliable, qualitative methods can be valuable. These methods rely on expert judgment and intuition.
- Delphi Method: This technique involves gathering opinions from a panel of experts, iteratively refining their estimates until a consensus is reached.
- Market Research: Conducting surveys, focus groups, or interviews with customers can provide insights into future demand expectations.
- Sales Force Composite: Collecting sales forecasts from individual sales representatives can offer a bottom-up perspective on future demand.
These qualitative methods should be used in conjunction with quantitative methods whenever possible, to improve accuracy and reliability.
5. Industry Benchmarks and Best Practices:
Comparing your organization's capacity cushion to industry benchmarks and best practices can provide valuable insights. However, it's important to consider the specific characteristics of your industry and operational environment. Direct comparisons may not always be appropriate. The benchmarks should serve as a starting point for your analysis rather than a definitive answer.
Factors Influencing Capacity Cushion Determination
The optimal capacity cushion is not a fixed value; it depends on several factors:
- Demand Variability: Higher demand variability requires a larger capacity cushion.
- Lead Times: Longer lead times for procuring raw materials or manufacturing components necessitate a larger cushion.
- Production Process Complexity: More complex processes with higher defect rates or longer setup times require a larger cushion.
- Risk Tolerance: Organizations with a higher risk tolerance may choose a smaller cushion, while those with a lower risk tolerance may prefer a larger one.
- Cost of Capacity: The cost of idle capacity needs to be weighed against the cost of production disruptions.
- Product Variety: Higher product variety can lead to greater complexity and necessitate a larger cushion.
- Technology and Automation: Advanced technologies and automation can improve efficiency and reduce the required capacity cushion.
Implementing and Monitoring Capacity Cushion
Once the optimal capacity cushion is determined, it's crucial to implement and monitor it effectively.
- Clear Communication: Ensure that all relevant stakeholders understand the capacity cushion strategy and its implications.
- Regular Monitoring: Continuously monitor key performance indicators (KPIs) to ensure the effectiveness of the cushion. This involves tracking production output, order fulfillment rates, lead times, inventory levels, and overall efficiency.
- Adaptive Adjustment: Be prepared to adjust the capacity cushion based on changing market conditions and operational performance. Regular review and updates are vital for maintaining its effectiveness.
- Contingency Planning: Develop contingency plans to address potential disruptions and utilize the capacity cushion effectively during unexpected events.
Conclusion
Determining the optimal capacity cushion is a critical aspect of operations management. The choice of method depends on various factors, and often a combination of methods offers the best results. By carefully considering the factors influencing cushion determination, implementing effective monitoring mechanisms, and adapting strategies as needed, organizations can leverage capacity cushions to mitigate risks, improve efficiency, and enhance overall operational performance. The goal isn't just to determine a number, but to create a robust and responsive system that ensures sustainable growth and profitability.
Latest Posts
Latest Posts
-
Mrs Chen Will Be 65 Soon
May 25, 2025
-
Parallel Lines And Proportional Parts In Triangles
May 25, 2025
-
What Page Does Curleys Wife Talk About Her Dream
May 25, 2025
-
Religion In The Life Of Pi
May 25, 2025
-
What Is The Goldfinch Book About
May 25, 2025
Related Post
Thank you for visiting our website which covers about Capacity Cushion Can Be Determined By . We hope the information provided has been useful to you. Feel free to contact us if you have any questions or need further assistance. See you next time and don't miss to bookmark.