Based On Market Research The Contractor Identifies A Less Expensive
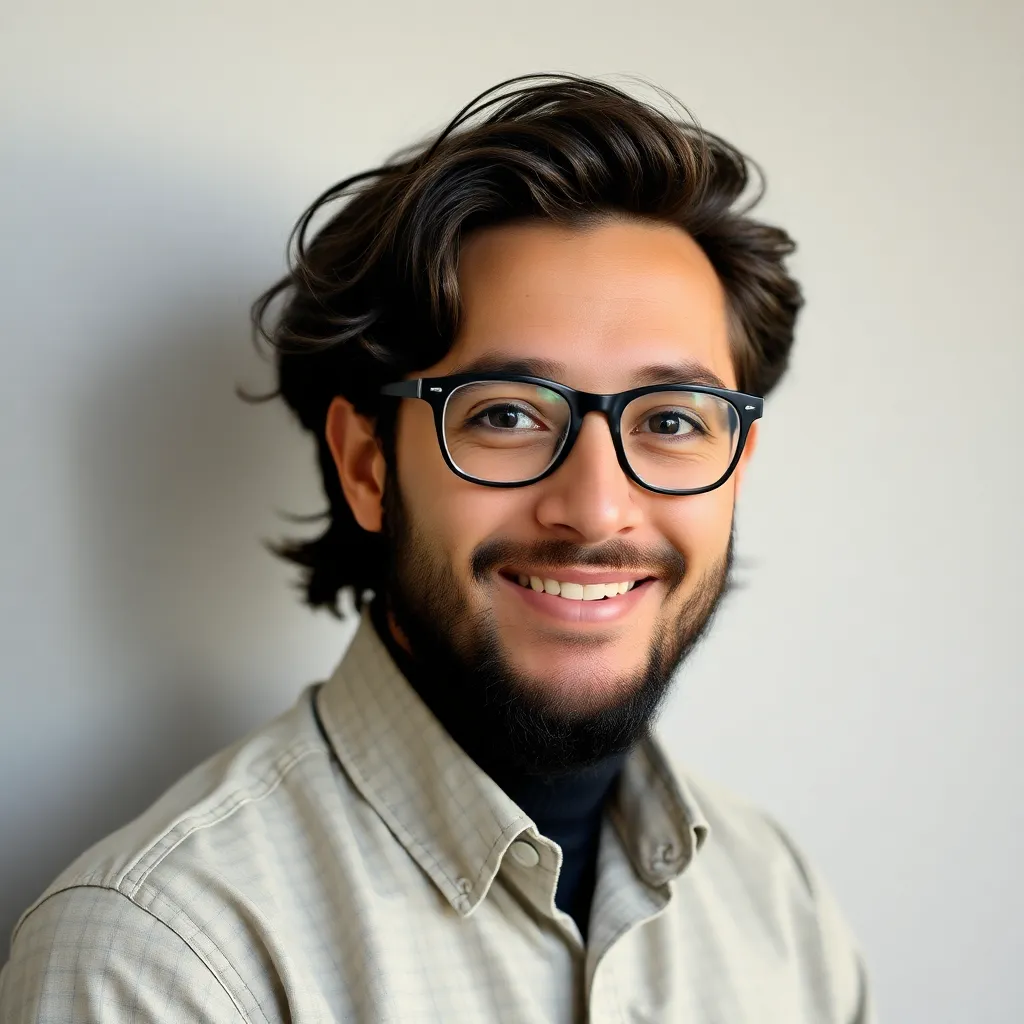
Juapaving
May 24, 2025 · 6 min read
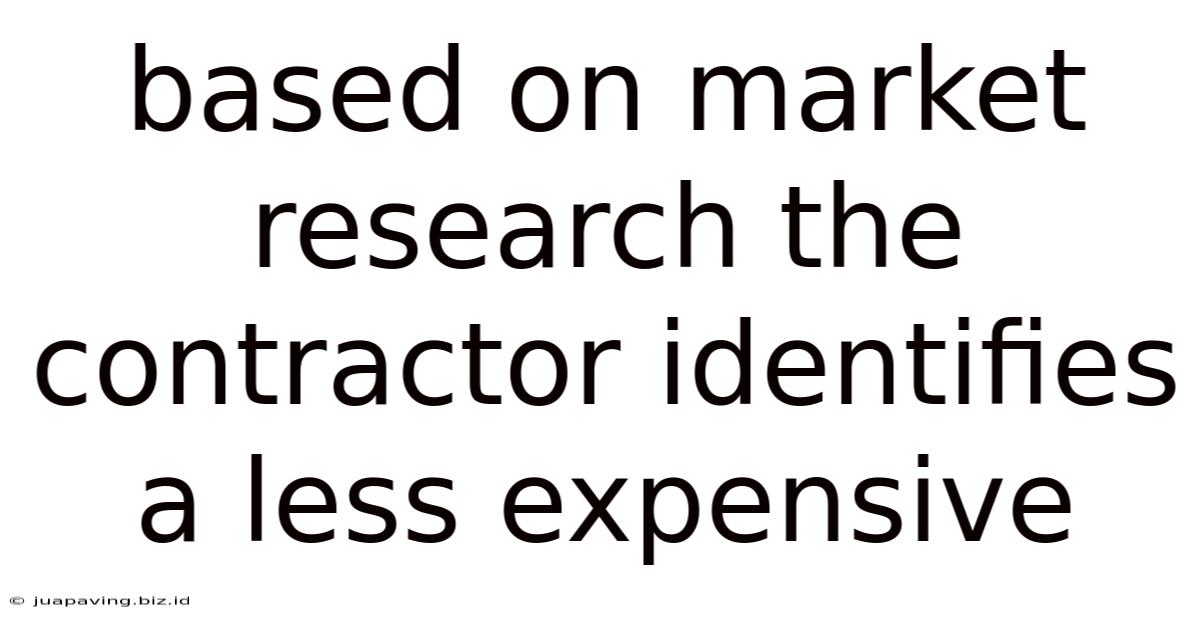
Table of Contents
Based on Market Research, the Contractor Identifies a Less Expensive Alternative: A Deep Dive into Cost Optimization in Construction
The construction industry is notoriously competitive and prone to cost overruns. Savvy contractors understand that staying profitable requires a keen eye for value engineering and a commitment to finding less expensive alternatives without sacrificing quality or project timelines. This article delves into how market research plays a crucial role in identifying cost-effective solutions, exploring strategies, case studies, and best practices for successful cost optimization in construction projects.
The Power of Market Research in Construction Cost Optimization
Market research is no longer a luxury; it's a necessity for contractors aiming for long-term success. It involves systematically gathering and analyzing information about the market to understand trends, identify opportunities, and make informed decisions. In the context of cost optimization, this means researching materials, labor, equipment, and subcontractors to find the most cost-effective options while maintaining project quality.
Key Aspects of Market Research for Cost Savings:
-
Material Sourcing: Researching different suppliers for building materials is crucial. Comparing prices, quality, lead times, and availability can significantly impact overall project costs. Consider exploring alternative materials with comparable performance at a lower price point. This could involve switching to recycled materials, exploring locally sourced products to reduce transportation costs, or investigating innovative, cost-effective substitutes.
-
Labor Market Analysis: Understanding the prevailing wage rates in your region is essential. Researching different labor unions, independent contractors, and staffing agencies helps in negotiating favorable rates and ensuring access to skilled labor within budget. Analyzing labor productivity rates and identifying potential bottlenecks can also lead to significant savings.
-
Equipment Rental vs. Purchase: A thorough cost-benefit analysis of renting versus purchasing equipment is essential. Consider the project's duration, frequency of equipment use, and maintenance costs. Rental might be more economical for short-term projects, while purchasing could be advantageous for projects requiring consistent equipment use. Market research can help you find the best rental deals or identify used equipment in good condition.
-
Subcontractor Selection: Subcontractors often account for a substantial portion of a project's budget. Thorough research, including reviewing their experience, qualifications, reputation, and pricing, is critical. Seeking multiple bids and comparing proposals are key to finding the most competitive and reliable subcontractors. Online platforms and industry directories can assist in finding potential subcontractors.
-
Technological Advancements: Keeping abreast of technological advancements in construction is vital. Innovative construction methods, software, and tools can lead to significant cost savings through increased efficiency and reduced waste. Researching and implementing these technologies, such as Building Information Modeling (BIM) or prefabrication, can improve project outcomes and reduce overall expenses.
Strategies for Identifying Less Expensive Alternatives
Beyond the foundational market research, specific strategies can enhance your ability to identify cost-effective alternatives:
1. Value Engineering:
Value engineering is a systematic approach to analyzing project design and specifications to identify cost-saving opportunities without compromising functionality or quality. This involves brainstorming alternative solutions, comparing their costs and benefits, and selecting the most economical option.
Example: Instead of using high-end imported granite for countertops, value engineering might suggest using a domestically sourced engineered stone that offers similar aesthetics at a lower cost.
2. Alternative Material Selection:
Exploring alternative materials is a powerful cost-saving strategy. This requires in-depth research to ensure that the alternatives meet the necessary performance standards and building codes.
Example: Using recycled steel instead of new steel can significantly reduce material costs. Similarly, using sustainably harvested timber can be more cost-effective and environmentally friendly than conventional lumber.
3. Lean Construction Principles:
Lean construction focuses on eliminating waste throughout the construction process. By streamlining workflows, improving communication, and reducing unnecessary steps, contractors can significantly reduce costs.
Example: Implementing a pull system instead of a push system in material delivery ensures that materials arrive only when needed, eliminating storage costs and reducing the risk of material damage or loss.
4. Negotiation and Procurement Strategies:
Effective negotiation with suppliers, subcontractors, and other stakeholders is crucial. Building strong relationships and leveraging your market research can lead to better pricing and more favorable contract terms.
Example: Negotiating bulk discounts for materials or securing long-term contracts with reliable subcontractors can significantly reduce costs over the course of a project.
5. Early Contractor Involvement (ECI):
ECI involves integrating contractors into the design process from the beginning. This allows contractors to offer valuable input on cost-effective design choices and construction methods, leading to significant savings before construction even starts.
Case Studies: Real-World Examples of Cost Optimization
Case Study 1: Sustainable Material Selection
A contractor building a multi-family residential complex used market research to identify a local supplier of recycled bricks. This not only reduced material costs compared to new bricks but also aligned with the client's sustainability goals, improving the project's image and potentially attracting environmentally conscious buyers.
Case Study 2: Lean Construction Implementation
A commercial construction firm implemented lean construction principles on a large-scale office building project. By optimizing workflows and reducing waste, they reduced labor costs by 15% and shortened the project timeline by 10%, leading to significant savings in overall project costs.
Case Study 3: Value Engineering in Design Phase
A contractor involved in the construction of a bridge used value engineering during the design phase. By suggesting a slightly modified design with less expensive materials and simpler construction methods, they were able to reduce the overall project cost by 20% without affecting the structural integrity or functionality of the bridge.
Best Practices for Successful Cost Optimization
-
Develop a comprehensive cost management plan: This plan should outline the strategies for cost optimization, the methods for tracking expenses, and the procedures for managing potential cost overruns.
-
Establish clear communication channels: Effective communication between all project stakeholders is crucial for identifying and addressing potential cost issues early on.
-
Regularly monitor and analyze costs: Tracking expenses throughout the project helps in identifying potential cost overruns and making timely adjustments.
-
Use technology to improve efficiency: Construction management software can help streamline processes, improve communication, and track expenses, leading to better cost control.
-
Continuously improve cost management processes: Regularly reviewing and evaluating your cost management processes can identify areas for improvement and further cost optimization.
Conclusion: Market Research – The Cornerstone of Cost-Effective Construction
Identifying less expensive alternatives is critical for success in the construction industry. Through comprehensive market research, strategic planning, and the implementation of effective cost optimization strategies, contractors can build profitable projects while delivering high-quality results. By embracing innovative approaches, focusing on value engineering, and leveraging technological advancements, contractors can ensure competitiveness and long-term sustainability in an ever-evolving industry. Remember, cost optimization is an ongoing process that demands vigilance, adaptability, and a proactive approach to market intelligence.
Latest Posts
Latest Posts
-
Las Llevas A La Playa Medias Sandalias Cajas
May 25, 2025
-
What Is The Theme Of Dune
May 25, 2025
-
Summary Of Macbeth Act 3 Scene 5
May 25, 2025
-
Hair Breakage May Result From Which Of The Following Actions
May 25, 2025
-
Summary Of The Tempest Act 2 Scene 1
May 25, 2025
Related Post
Thank you for visiting our website which covers about Based On Market Research The Contractor Identifies A Less Expensive . We hope the information provided has been useful to you. Feel free to contact us if you have any questions or need further assistance. See you next time and don't miss to bookmark.