An Alloy Of Copper And Tin
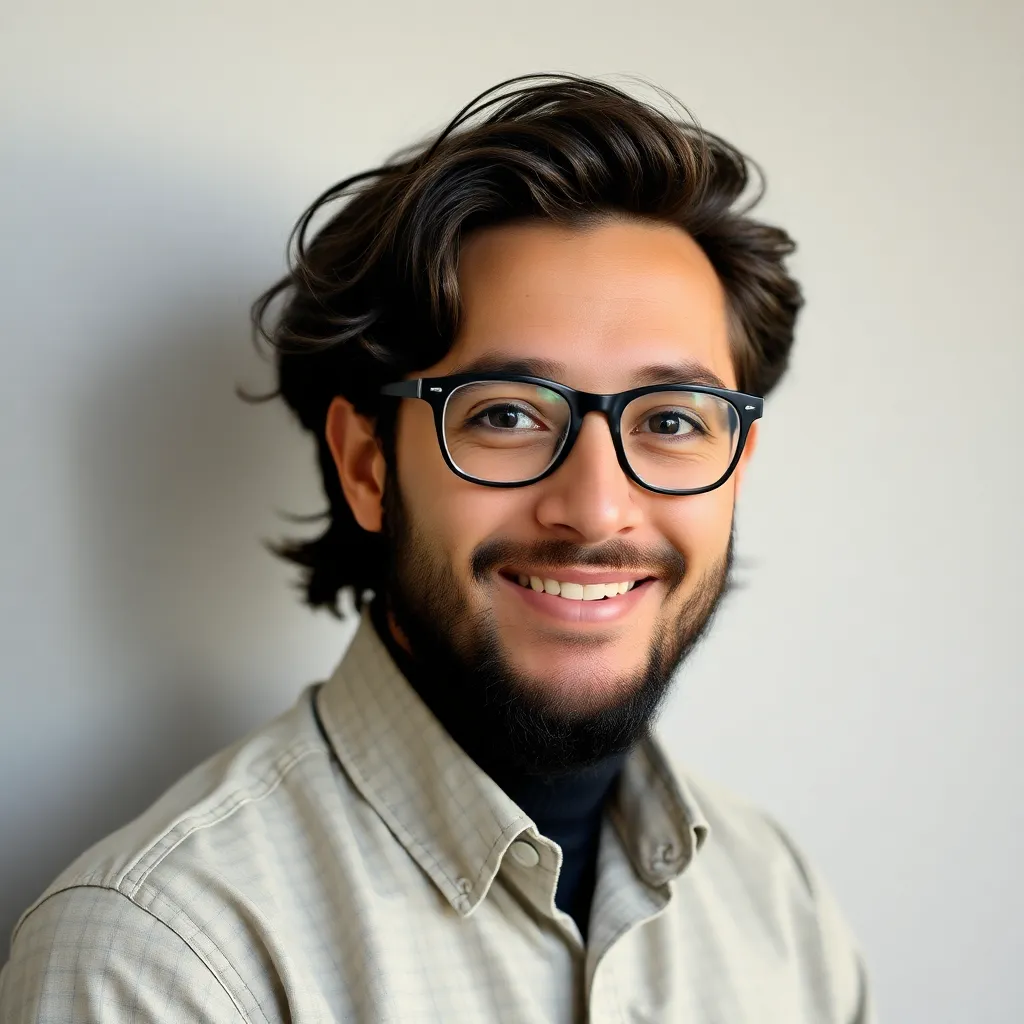
Juapaving
May 13, 2025 · 6 min read
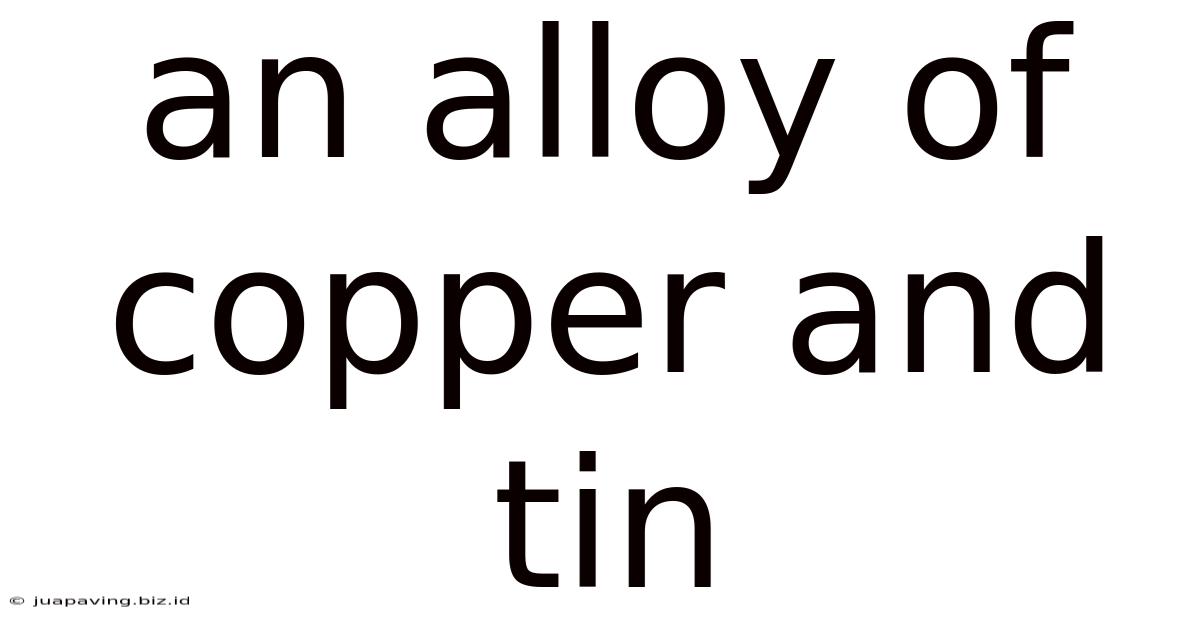
Table of Contents
An Alloy of Copper and Tin: Exploring the Properties and Applications of Bronze
Bronze, an alloy primarily composed of copper and tin, holds a significant place in human history and continues to play a vital role in modern applications. Its unique properties, stemming from the synergistic combination of its constituent metals, have shaped civilizations and continue to drive innovation across various industries. This article delves deep into the fascinating world of bronze, exploring its composition, properties, historical significance, manufacturing processes, and diverse applications.
Understanding the Composition of Bronze
Bronze isn't simply a fixed mixture of copper and tin; its precise composition varies widely depending on the desired properties. While the primary components remain copper and tin, other elements can be added to fine-tune the alloy's characteristics. This process, known as alloying, allows for the creation of bronzes with specific strengths, ductility, corrosion resistance, and aesthetic qualities.
The Role of Copper
Copper forms the base of bronze, typically constituting between 80% and 95% of the alloy's weight. Copper contributes significantly to bronze's malleability, conductivity (both thermal and electrical), and its characteristic reddish-brown hue. Its inherent resistance to corrosion also contributes to the longevity of bronze artifacts.
The Influence of Tin
Tin, the essential alloying element, plays a crucial role in determining bronze's properties. It enhances the alloy's strength, hardness, and castability while reducing its melting point compared to pure copper. The percentage of tin significantly impacts the final characteristics of the bronze. Higher tin content generally leads to a harder, more brittle bronze, while lower tin percentages result in a softer, more ductile alloy.
Other Alloying Elements: Enhancing Properties
While copper and tin are the defining elements, the addition of other metals can dramatically alter bronze's properties. Common additives include:
- Zinc: Adding zinc produces brass, sometimes considered a type of bronze, significantly altering the color and increasing ductility.
- Lead: Lead improves the alloy's machinability, making it easier to work with, but can reduce its strength.
- Aluminum: Aluminum enhances the alloy's strength and corrosion resistance, particularly in marine environments.
- Manganese: Manganese increases the alloy's hardness and tensile strength.
- Silicon: Silicon improves the alloy's fluidity during casting, leading to more intricate castings.
- Nickel: Nickel increases the alloy's corrosion resistance and strength.
The precise combination and proportion of these elements are carefully controlled to achieve the desired properties for a specific application.
The Remarkable Properties of Bronze
The unique properties of bronze are responsible for its widespread use throughout history and into the modern era. These properties include:
- High Strength and Hardness: Compared to pure copper, bronze exhibits significantly greater strength and hardness, making it suitable for tools and weapons. The level of strength and hardness is directly related to the tin content.
- Excellent Castability: Bronze's relatively low melting point and good fluidity make it exceptionally easy to cast into complex shapes, a critical factor in its historical use for sculptures and decorative items.
- Corrosion Resistance: Bronze exhibits good corrosion resistance, especially in many atmospheric and soil conditions, contributing to its longevity. However, the resistance varies depending on the alloy's composition and the specific environment.
- Good Wear Resistance: Bronze's hardness and strength translate into excellent wear resistance, making it suitable for applications involving friction and abrasion.
- Ductility and Malleability: While harder than copper, bronze retains a degree of ductility and malleability, allowing it to be shaped and worked using various techniques.
- Aesthetic Appeal: Bronze's characteristic reddish-brown color, combined with its ability to take on a beautiful patina over time, makes it highly prized for decorative and artistic purposes.
Bronze Throughout History: The Bronze Age and Beyond
The Bronze Age, spanning from approximately 3300 BCE to 1200 BCE, marks a significant turning point in human history. The discovery and widespread use of bronze revolutionized toolmaking, weaponry, and construction, leading to advancements in agriculture, warfare, and societal structures. Bronze tools were sharper, stronger, and more durable than their stone predecessors, enabling more efficient farming and construction. Bronze weapons provided a significant military advantage.
The artistic achievements of the Bronze Age are equally impressive. Sculptures, decorative objects, and tools, all meticulously crafted from bronze, remain testaments to the artistry and skill of Bronze Age civilizations. Iconic examples include the sophisticated weaponry of the Mycenaeans, intricate Chinese bronzes, and the magnificent ceremonial objects of ancient Egypt.
Even after the Iron Age, bronze remained a valuable material. Its properties made it suitable for applications requiring corrosion resistance, strength, and aesthetic appeal, leading to its continued use in various forms throughout subsequent eras.
Manufacturing Processes for Bronze
The production of bronze involves several key steps:
- Melting: Copper and tin, along with any other alloying elements, are carefully melted together in a crucible. Precise temperature control is crucial to ensure a homogeneous mixture.
- Casting: The molten bronze is poured into molds – traditionally sand molds, but now also including more sophisticated techniques like investment casting – to create the desired shape. The casting process requires careful attention to prevent defects such as porosity or shrinkage.
- Fabrication: Once solidified, the bronze casting can be further processed through various fabrication techniques, including machining, forging, rolling, and drawing. These processes are used to refine the shape and improve surface finish.
- Finishing: The final step often involves polishing, buffing, or applying a protective coating to enhance the bronze's appearance and durability. Patination, a process of controlled oxidation, can be used to create a distinctive aged look.
Modern Applications of Bronze
Despite the rise of newer materials, bronze continues to find widespread applications in modern times, owing to its unique combination of properties:
- Bearings and Bushings: Bronze's wear resistance and self-lubricating properties make it ideal for bearings and bushings, particularly in applications involving heavy loads and high speeds.
- Marine Hardware: Bronze's exceptional corrosion resistance in saltwater environments makes it a preferred material for marine hardware, such as propellers, fittings, and valves.
- Sculptures and Art: Bronze retains its artistic significance and is a popular material for sculptures and decorative objects. Its ability to withstand weathering and develop a beautiful patina enhances its artistic value.
- Electrical Connectors: Bronze's good electrical conductivity makes it suitable for various electrical components.
- Musical Instruments: The unique acoustic properties of bronze make it a favoured material for the construction of musical instruments, particularly bells and cymbals.
- Coins and Medals: Bronze's durability, aesthetic appeal, and resistance to corrosion make it an excellent choice for coins and medals.
- Industrial applications: Bronze finds uses in various industrial applications where strength, corrosion resistance, and wear resistance are crucial. This includes parts in machinery, tools, and components subjected to harsh conditions.
The Future of Bronze
The ongoing research and development in materials science are continually refining the properties and expanding the potential applications of bronze alloys. New alloy compositions are being developed to enhance specific properties, such as increased strength, superior corrosion resistance, and improved machinability. As environmental concerns rise, the use of recycled bronze is also gaining importance, contributing to sustainable manufacturing practices. The enduring legacy of this remarkable alloy ensures its continued relevance and potential for innovation in the years to come. Its versatility, combined with its historical significance, solidifies bronze's position as a material of both historical and contemporary importance. The study of bronze, therefore, offers a fascinating intersection of history, materials science, and art.
Latest Posts
Latest Posts
-
Sketch And Label A Centrosome With Two Centrioles
May 13, 2025
-
What Is The Roman Numeral Mcmxcix
May 13, 2025
-
Which Ion Has The Largest Radius
May 13, 2025
-
How To Convert Molarity Into Grams
May 13, 2025
-
Are Elephants Herbivores Carnivores Or Omnivores
May 13, 2025
Related Post
Thank you for visiting our website which covers about An Alloy Of Copper And Tin . We hope the information provided has been useful to you. Feel free to contact us if you have any questions or need further assistance. See you next time and don't miss to bookmark.