A Grooved Wheel With A Rope Running Along The Groove
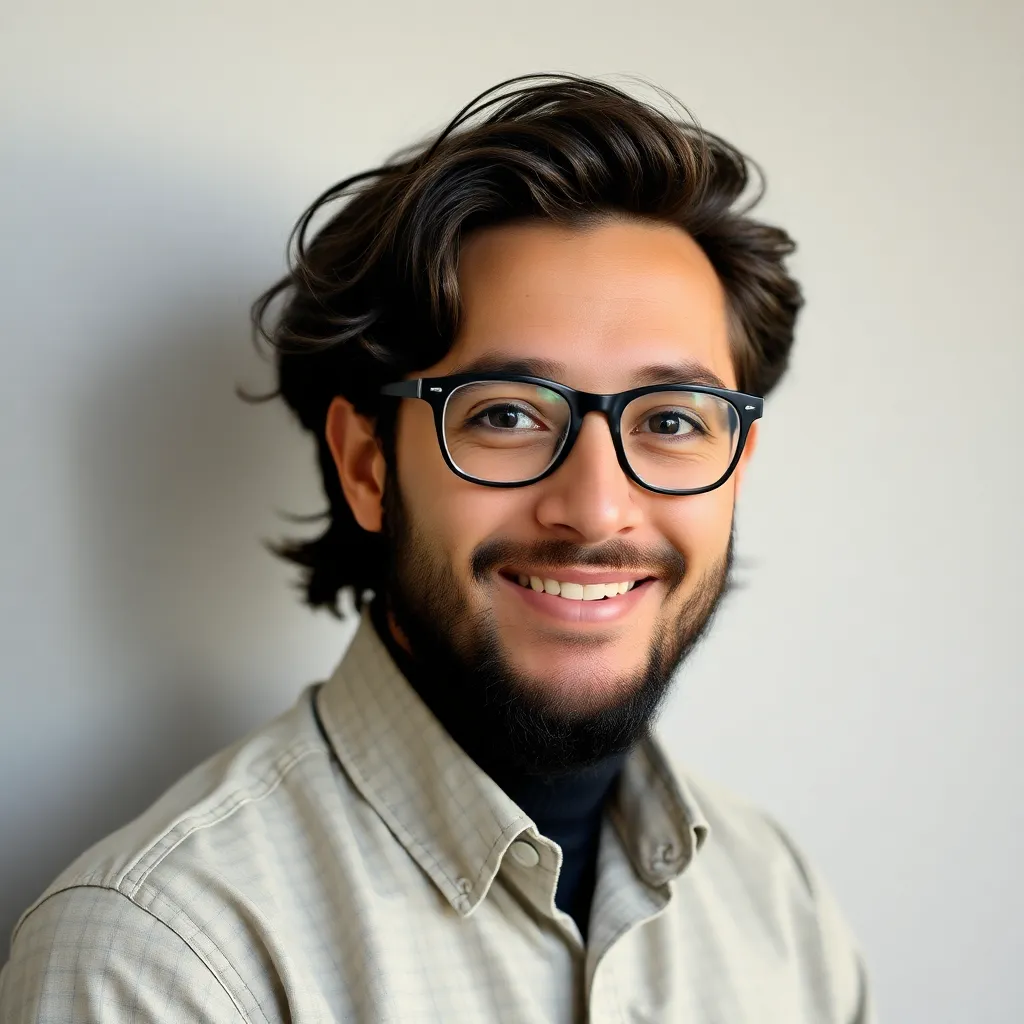
Juapaving
Mar 25, 2025 · 6 min read
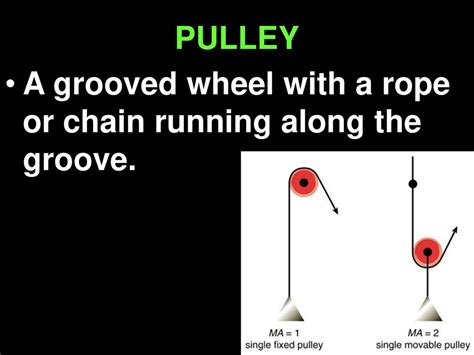
Table of Contents
Grooved Wheels and Ropes: A Deep Dive into Mechanics, Applications, and Design Considerations
A seemingly simple mechanism, a grooved wheel with a rope running along its groove, is a fundamental element in countless mechanical systems. From ancient water-lifting devices to modern industrial cranes and even intricate clockwork mechanisms, this ingenious design leverages the principles of friction and leverage to achieve a wide array of functionalities. This comprehensive guide delves into the mechanics, diverse applications, design considerations, and the ongoing evolution of grooved wheels and rope systems.
Understanding the Mechanics: Friction and Leverage
The effectiveness of a grooved wheel and rope system hinges on two key principles: friction and leverage. The groove itself is crucial in maximizing friction between the rope and the wheel's surface. This prevents the rope from slipping, ensuring efficient power transmission. The deeper and more precisely engineered the groove, the greater the friction, and thus the more reliable the system.
The Role of Friction:
- Static Friction: This prevents the rope from slipping when under load. A properly designed groove ensures sufficient static friction to hold the rope securely, even under significant tension. Material choice plays a critical role here; materials with high coefficients of friction, such as rubber or certain polymers, are often preferred for the wheel's surface.
- Kinetic Friction: While we aim to minimize kinetic friction (friction during movement), it’s still a factor. A well-lubricated system reduces kinetic friction, making the rope easier to pull and increasing efficiency. The type of rope material also significantly impacts kinetic friction.
- Coefficient of Friction: This is a dimensionless number representing the ratio of the force of friction to the normal force. A higher coefficient means more friction. Engineers carefully select materials to optimize this coefficient for specific applications.
Leveraging Leverage:
The wheel itself acts as a lever, amplifying the force applied to the rope. The mechanical advantage is determined by the wheel's radius and the radius of any other pulleys or sheaves involved in the system. A larger wheel provides a greater mechanical advantage, allowing a smaller input force to lift a heavier load. This principle is fundamental to various lifting and pulling mechanisms.
Diverse Applications Across Industries
The seemingly simple combination of a grooved wheel and rope finds applications across a stunning spectrum of industries and contexts. Here are some notable examples:
Construction and Lifting:
- Cranes: Large construction cranes rely extensively on grooved wheels and ropes to lift heavy materials. The intricate systems of pulleys and sheaves, each incorporating grooved wheels, enable precise control and significant load capacity.
- Hoists: Whether manually operated or powered, hoists use grooved wheels to lift and lower loads efficiently, often incorporating multiple pulleys for increased mechanical advantage.
- Elevators: While modern elevators incorporate more sophisticated technology, the core principle of lifting and lowering the cabin relies on a system involving grooved wheels and cables.
Transportation and Material Handling:
- Conveyors: Many conveyor systems use grooved wheels and belts to transport materials along a defined path. The grooved wheels provide the necessary traction to move the belt smoothly and reliably.
- Winches: Used for pulling and hauling heavy loads, winches employ grooved wheels to manage the rope or cable, providing a mechanical advantage for the user.
- Cable Cars and Ski Lifts: These systems utilize a series of grooved wheels and cables to transport people or goods up and down slopes, often over considerable distances.
Agriculture and Farming:
- Hay Balers: These machines utilize grooved wheels and belts to efficiently bale hay, relying on the reliable grip provided by the grooved wheel system.
- Irrigation Systems: Grooved wheels play a role in various irrigation systems, particularly those utilizing ropes or belts to guide water distribution.
- Farm Machinery: Numerous agricultural machines employ grooved wheels and belts for power transmission and material handling.
Industrial Applications:
- Power Transmission: Grooved wheels and belts are a common method for transmitting power in various industrial machinery. This system offers a flexible and efficient means of transferring rotational motion.
- Precision Engineering: In micro-mechanical and precision engineering, smaller versions of these systems are used in delicate applications, requiring highly precise grooves and high-quality materials.
Design Considerations and Material Selection
Designing an effective grooved wheel and rope system involves careful consideration of several factors:
Groove Geometry:
- Groove Depth and Width: These parameters are crucial in determining the friction and the rope's ability to stay securely within the groove. The depth should be sufficient to prevent slippage, but not so deep as to restrict rope movement or cause undue wear.
- Groove Shape: The shape of the groove—V-shaped, U-shaped, or other variations—affects the contact area between the rope and the wheel. The optimal shape depends on the rope type and the required friction.
- Groove Material: The material of the groove itself contributes significantly to friction and wear resistance. Hardened steel, polymers, or specialized composites are commonly used based on the application's requirements.
Rope Selection:
- Rope Material: Natural fibers (such as hemp or sisal), synthetic fibers (like nylon or polyester), and wire ropes each possess distinct properties affecting strength, durability, and flexibility. The choice depends on the load, environment, and required lifespan.
- Rope Diameter: The rope diameter must be compatible with the groove dimensions to ensure proper fit and prevent wear.
- Rope Strength: The rope must be strong enough to withstand the anticipated loads without breaking. Safety factors are incorporated to account for unexpected surges or variations in load.
Wheel Material and Construction:
- Wheel Material: The material chosen for the wheel must balance strength, durability, and weight. Materials range from cast iron and steel to lighter-weight alloys, depending on the application.
- Wheel Diameter: The wheel diameter significantly affects the mechanical advantage and the system's overall efficiency. A larger diameter increases the mechanical advantage but also increases the size and weight of the system.
- Bearing System: Appropriate bearings are essential to minimize friction and ensure smooth rotation. The bearing type (e.g., ball bearings, roller bearings) depends on the load, speed, and operating conditions.
Ongoing Advancements and Future Trends
While the fundamental concept of grooved wheels and ropes remains unchanged, ongoing advancements continue to refine their design and application:
- Advanced Materials: The development of new materials with enhanced properties (e.g., higher strength-to-weight ratios, improved wear resistance) leads to more efficient and durable systems.
- Precision Manufacturing: Advances in manufacturing techniques allow for the creation of more precisely engineered grooves, leading to increased efficiency and reduced wear.
- Smart Systems: Integration with sensors and control systems enables monitoring of rope tension, wheel speed, and other parameters, improving safety and optimizing system performance. These smart systems allow for predictive maintenance, minimizing downtime and ensuring optimal operation.
- Specialized Grooves: The development of specialized groove designs further optimizes the interaction between the rope and the wheel, increasing friction and durability for specific applications. This could include specialized coatings applied to the groove surface.
- Hybrid Systems: The integration of grooved wheels with other technologies, such as hydraulic or pneumatic systems, extends their capabilities, particularly in heavy-duty applications. This combines the mechanical advantage of the wheel with the power of fluid-based systems.
Conclusion
The simple elegance of a grooved wheel and rope system belies its profound significance in countless applications across diverse industries. Understanding the underlying mechanics, careful consideration of design parameters, and ongoing advancements in materials and manufacturing contribute to the continued relevance and evolution of this fundamental technology. From ancient water wells to modern construction sites, this ingenious combination of friction and leverage continues to shape our world. The future will likely see further refinements in materials, manufacturing, and integration with smart technologies, expanding the capabilities and applications of these ubiquitous systems.
Latest Posts
Latest Posts
-
What Is It Called When A Gas Turns To Liquid
Mar 26, 2025
-
How Many Feet In 58 Inches
Mar 26, 2025
-
What Is The Difference Between Sodium Bicarbonate And Sodium Carbonate
Mar 26, 2025
-
Why Is Earth Known As The Blue Planet
Mar 26, 2025
-
Melting Point Chemical Or Physical Property
Mar 26, 2025
Related Post
Thank you for visiting our website which covers about A Grooved Wheel With A Rope Running Along The Groove . We hope the information provided has been useful to you. Feel free to contact us if you have any questions or need further assistance. See you next time and don't miss to bookmark.