A Fully Loaded Slow Moving Freight Elevator
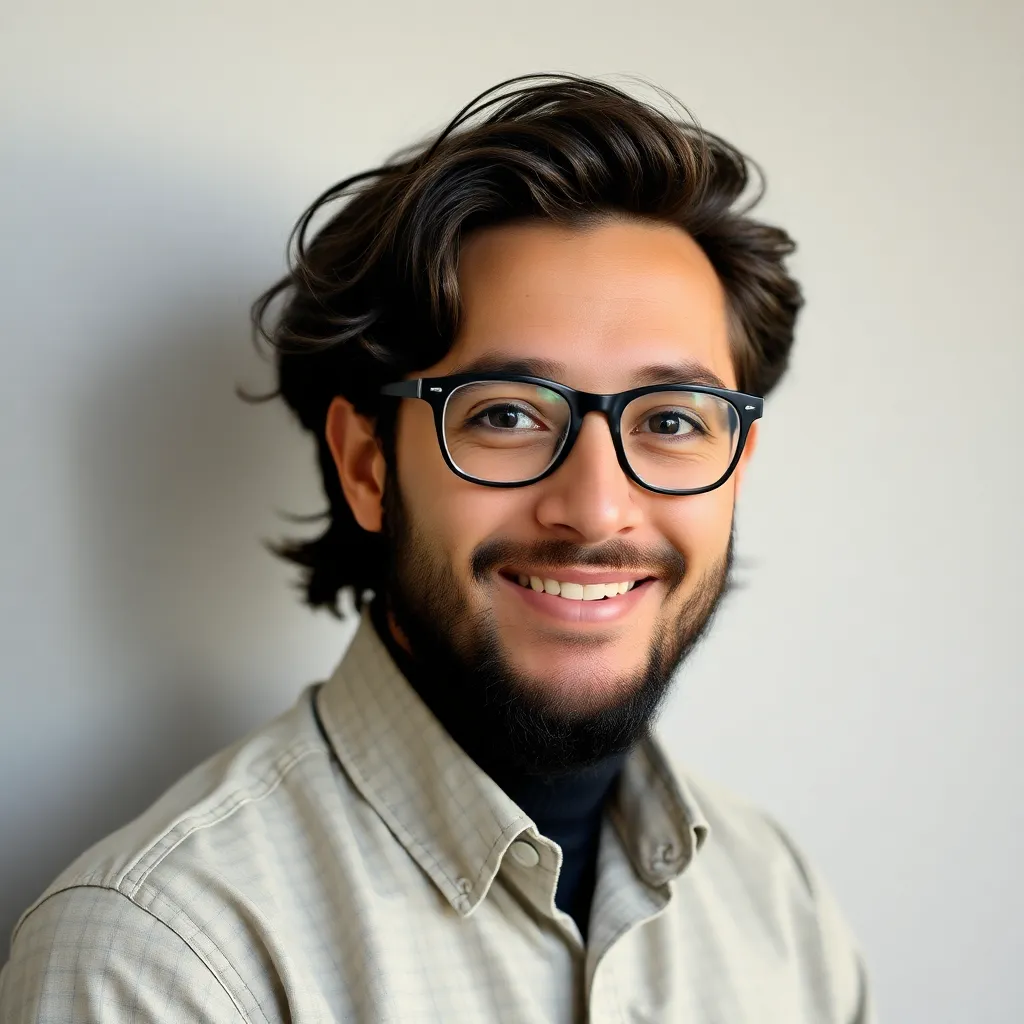
Juapaving
May 09, 2025 · 6 min read
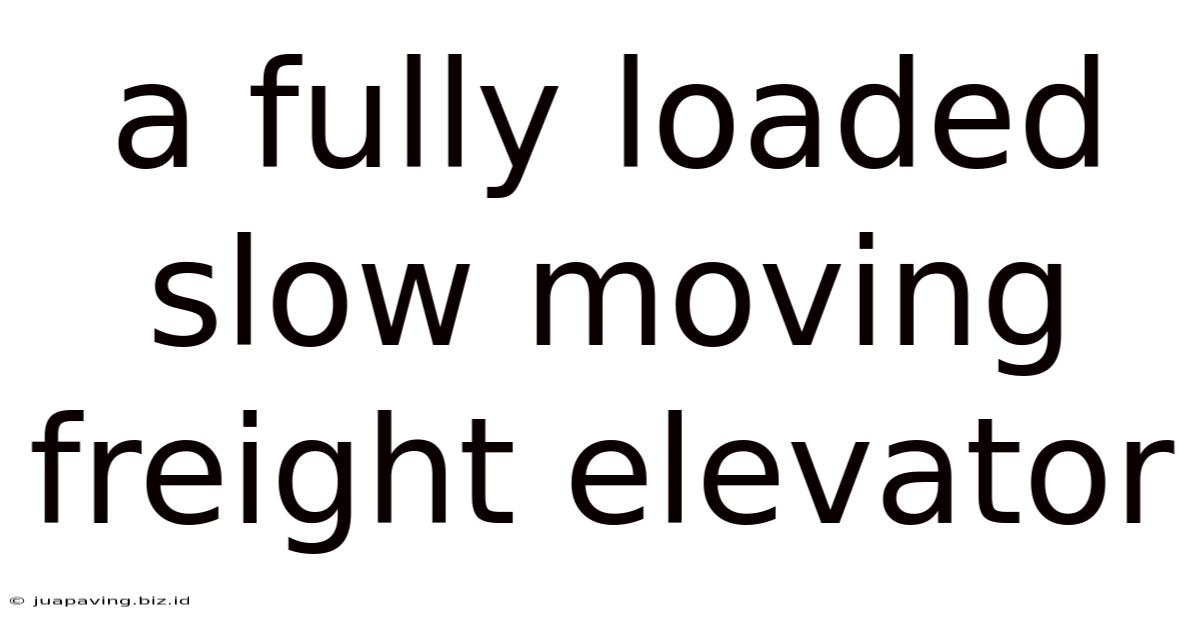
Table of Contents
A Fully Loaded Slow Moving Freight Elevator: A Deep Dive into Design, Safety, and Efficiency
Freight elevators, the unsung workhorses of industrial and commercial buildings, play a crucial role in the efficient movement of goods. While speed is a factor in passenger elevators, freight elevators prioritize capacity and safety. This article delves into the specifics of a fully loaded, slow-moving freight elevator, exploring its design, safety features, operational considerations, and the engineering challenges involved. Understanding these aspects is critical for building owners, managers, and anyone involved in the operation and maintenance of these vital systems.
The Unique Demands of a Fully Loaded Freight Elevator
A "fully loaded" freight elevator signifies the elevator operating at its maximum weight capacity. This is significantly higher than passenger elevators, often reaching several tons. This high weight capacity necessitates a robust and meticulously designed system capable of handling the stresses and strains of transporting heavy loads. The slow speed is a deliberate design choice, prioritizing safety and stability over rapid transport. This speed limitation reduces the inertial forces experienced by both the load and the elevator structure during operation, thus minimizing the risk of accidents and equipment damage.
Design Considerations for Maximum Load Capacity
Several key design elements contribute to a freight elevator's ability to handle a full load safely and efficiently:
-
Robust Construction: Freight elevators utilize stronger materials and more robust construction techniques compared to passenger elevators. This includes heavier gauge steel for the car frame, reinforced hoisting cables, and more powerful drive mechanisms. The structural integrity of the elevator shaft itself must also be carefully considered to withstand the increased load.
-
Hoisting System: The hoisting system is the heart of the freight elevator, and for a fully loaded elevator, it needs to be particularly powerful and reliable. This often involves multiple hoisting cables with high tensile strength, coupled with a robust and precisely engineered motor and gear system. The braking system is crucial, providing redundant safety mechanisms to prevent uncontrolled descent.
-
Hydraulic vs. Traction: Both hydraulic and traction systems can be used for freight elevators, each with its own advantages and disadvantages. Hydraulic systems are generally simpler and require less headroom, making them suitable for lower-rise buildings. However, they can be less efficient and more prone to leakage. Traction systems, which use cables and a motor to hoist the car, offer greater efficiency and higher speeds (though still slower than passenger elevators). They are preferred for taller buildings. For a fully loaded system, redundancy and robust design are paramount for both types.
-
Counterweight System: The counterweight system is critical for efficiency and safety. A properly balanced counterweight significantly reduces the load on the hoisting system, especially when the elevator is fully loaded. Careful calculation of the counterweight's mass is essential to optimize energy consumption and minimize wear and tear on the system.
-
Safety Features: Given the potential risks associated with handling heavy loads, multiple layers of safety features are essential. This includes overspeed governors, safety brakes, and emergency stop buttons. Regular inspections and maintenance are crucial to ensuring these features remain fully functional.
Safety Protocols for a Fully Loaded Slow-Moving Freight Elevator
Operating a fully loaded freight elevator requires strict adherence to safety protocols to prevent accidents and ensure the well-being of personnel and the integrity of the equipment.
Operational Safety Procedures:
-
Weight Limits: Clearly marked weight limits must be strictly adhered to. Operators must be trained to accurately assess the weight of the load and ensure it does not exceed the elevator's rated capacity. Overloading can cause catastrophic failure.
-
Load Distribution: Evenly distributing the load within the elevator car is critical to prevent imbalance and potential tipping. Heavy items should be positioned low and centrally to maintain stability.
-
Securement of Loads: Loose or unsecured loads pose a significant hazard. Proper load securing mechanisms, such as straps, chains, or pallets, must be used to prevent shifting during operation.
-
Operator Training: Operators of freight elevators require specific training to understand the equipment's capabilities and limitations. They must be familiar with emergency procedures and safety protocols.
-
Regular Inspections: Regular inspections and maintenance are crucial for identifying and addressing potential safety hazards before they escalate into accidents. This includes checking cables, brakes, safety devices, and the structural integrity of the elevator and its shaft.
Advanced Safety Features:
-
Load Weighing Systems: Modern freight elevators may incorporate load weighing systems that automatically prevent operation if the weight limit is exceeded.
-
Safety Interlocks: Safety interlocks prevent operation if the elevator doors are open or if other safety features are compromised.
-
Redundant Safety Systems: Multiple independent safety systems are implemented to provide redundancy in case of failure of one component.
-
Emergency Communication Systems: Effective communication systems allow trapped occupants to contact emergency services.
Efficiency and Maintenance of a Fully Loaded Slow-Moving Freight Elevator
Maintaining the efficiency of a fully loaded freight elevator is crucial for minimizing downtime and operational costs.
Energy Efficiency Considerations:
-
Regenerative Braking: Regenerative braking systems recover energy during deceleration, converting it back into electricity and reducing energy consumption.
-
Variable Frequency Drives (VFDs): VFDs optimize motor speed and torque, improving energy efficiency and reducing wear and tear on the system.
-
Optimized Counterweight System: A properly balanced counterweight minimizes the energy required to lift and lower the load.
Maintenance and Inspection:
-
Regular Lubrication: Regular lubrication of moving parts is critical for reducing friction and wear.
-
Cable Inspection: Regular visual inspection of the hoisting cables for wear and damage is crucial for preventing cable failure.
-
Brake System Inspection: The brake system must be inspected and tested regularly to ensure it functions properly.
-
Safety Device Testing: All safety devices must be tested regularly to ensure they are functioning correctly.
-
Preventative Maintenance: A proactive preventative maintenance program can significantly extend the lifespan of the elevator and minimize unexpected downtime.
The Engineering Challenges:
Designing and implementing a fully loaded, slow-moving freight elevator presents significant engineering challenges. These include:
-
Stress Analysis: The elevator system must be designed to withstand the stresses and strains imposed by the maximum load. Finite element analysis (FEA) is often used to model the stresses and ensure structural integrity.
-
Vibration Control: The slow speed helps mitigate vibration, but effective vibration damping measures may be needed to minimize wear and tear and ensure smooth operation.
-
Control Systems: Precise control of the elevator's movement, particularly with a heavy load, requires sophisticated control systems that ensure smooth starts, stops, and level positioning.
-
Material Selection: Careful selection of materials is crucial for durability, strength, and resistance to wear and tear. High-strength steel alloys are commonly used for the elevator car and other structural components.
-
Safety Factor: A significant safety factor is incorporated into the design to account for unexpected loads and potential stresses. This ensures the elevator can operate safely and reliably even under extreme conditions.
Conclusion:
A fully loaded, slow-moving freight elevator represents a complex and critical piece of infrastructure in many buildings. Its design, operation, and maintenance necessitate careful consideration of various factors, including safety, efficiency, and the engineering challenges associated with handling heavy loads. By adhering to rigorous safety protocols, implementing efficient maintenance programs, and applying advanced engineering principles, building owners and operators can ensure the reliable and safe operation of these essential systems for years to come. The focus on safety and robust design cannot be overstated, as the consequences of failure can be severe. Understanding these aspects is vital for maximizing productivity and minimizing risk in any setting where heavy goods need to be transported vertically.
Latest Posts
Latest Posts
-
The Function Of Dna Ligase In Recombinant Technology Is To
May 09, 2025
-
What Is 108 In In Feet
May 09, 2025
-
Most Reactive Metals On The Periodic Table
May 09, 2025
-
87 Cm Is How Many Inches
May 09, 2025
-
What Is The Sqaure Root Of 40
May 09, 2025
Related Post
Thank you for visiting our website which covers about A Fully Loaded Slow Moving Freight Elevator . We hope the information provided has been useful to you. Feel free to contact us if you have any questions or need further assistance. See you next time and don't miss to bookmark.