A Company's Distribution And Warehouse Expenses
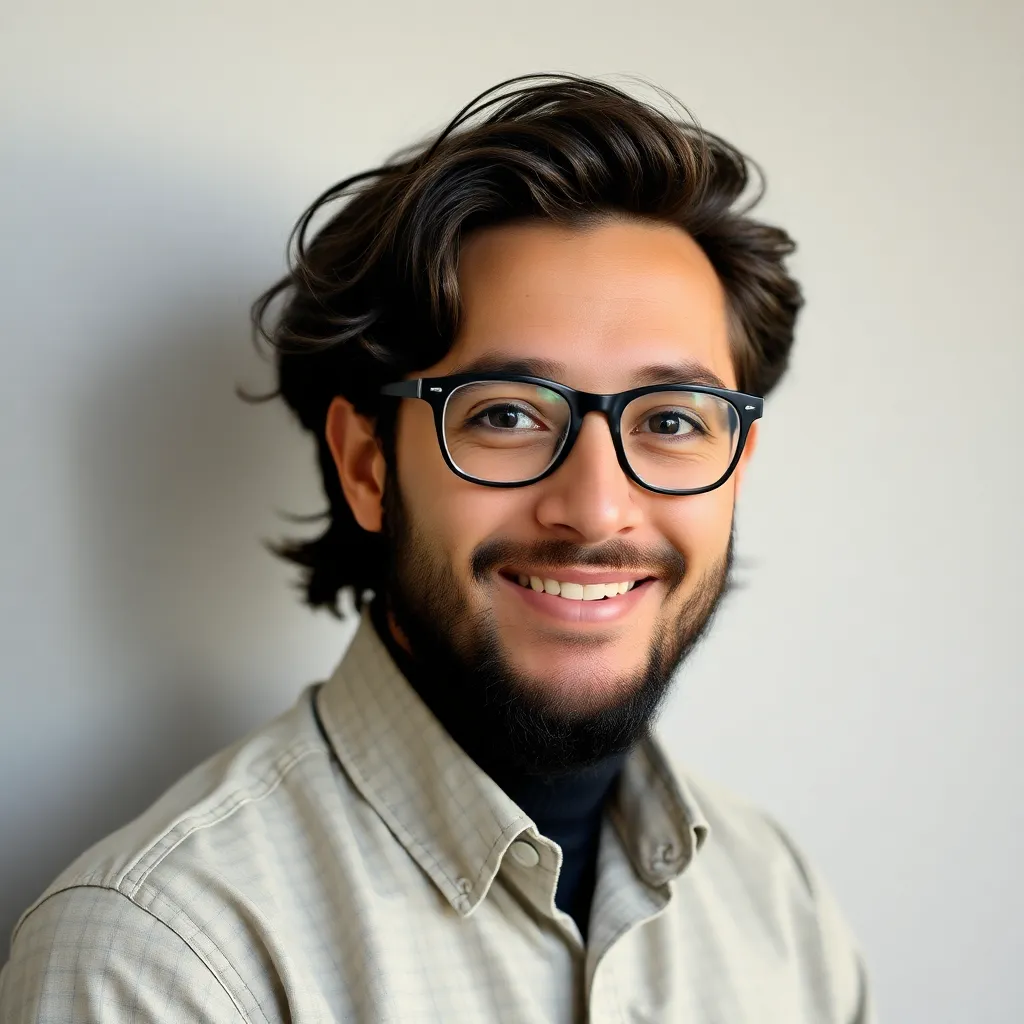
Juapaving
May 25, 2025 · 6 min read
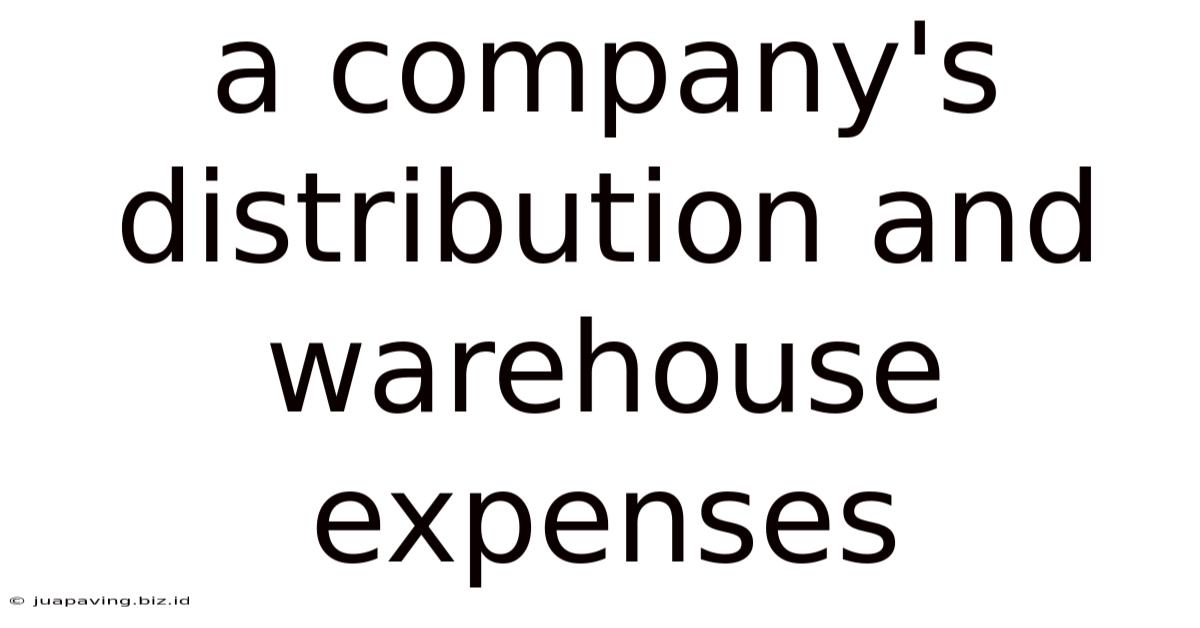
Table of Contents
Understanding and Optimizing Your Company's Distribution and Warehouse Expenses
Distribution and warehouse expenses represent a significant portion of a company's operational costs, particularly for businesses involved in manufacturing, wholesaling, or e-commerce. Effectively managing these expenses is crucial for profitability and maintaining a competitive edge. This comprehensive guide delves into the various components of distribution and warehouse expenses, strategies for optimizing them, and the importance of accurate cost accounting in this area.
Decoding Distribution and Warehouse Expenses: A Detailed Breakdown
Distribution and warehouse costs encompass a wide range of expenditures related to the storage, handling, and movement of goods from the point of production or acquisition to the end customer. Let's break down the key expense categories:
1. Warehouse Costs: The Heart of the Operation
Warehouse expenses are directly related to the physical space where inventory is stored and managed. These include:
-
Rent or Mortgage Payments: This is often the largest single expense for warehousing. Consider factors like location, accessibility, and size when evaluating warehouse space. Negotiating favorable lease terms can significantly impact your bottom line.
-
Utilities: Electricity, heating, cooling, and water consumption all contribute to operational costs. Energy-efficient practices, such as LED lighting and optimized climate control, can help reduce these expenses.
-
Property Taxes and Insurance: These are fixed costs associated with owning or leasing a warehouse. Proper insurance coverage protects against potential losses due to damage, theft, or liability.
-
Maintenance and Repairs: Regular maintenance is vital for keeping the warehouse in good working order. This includes repairs to equipment, building infrastructure, and addressing any safety concerns. A proactive approach to maintenance can prevent costly breakdowns and disruptions.
-
Security Systems: Implementing robust security measures, including surveillance cameras, alarm systems, and access control, protects inventory and prevents losses due to theft or vandalism.
-
Warehouse Management System (WMS) Software: Investing in a WMS can automate many warehouse processes, improving efficiency and reducing labor costs. The initial investment in software and training might seem high, but the long-term benefits often outweigh the costs.
-
Equipment Costs: This includes forklifts, conveyor belts, pallet jacks, and other machinery used for handling and moving inventory. Consider the cost of purchase or lease, maintenance, repairs, and fuel consumption.
-
Labor Costs: Warehouse staff, including order pickers, packers, and loaders, represent a significant expense. Optimizing staffing levels, implementing efficient work processes, and investing in training can improve productivity and reduce labor costs.
2. Distribution Costs: Getting Products to the Customer
Distribution costs encompass all expenses associated with moving goods from the warehouse to the customer. These include:
-
Transportation Costs: This is often the largest component of distribution expenses. The choice of transportation method (truck, rail, air, or sea) significantly impacts cost. Factors like distance, volume, and delivery speed need careful consideration. Negotiating favorable rates with carriers is crucial.
-
Packaging and Shipping Supplies: The cost of boxes, packing materials, labels, and other shipping supplies should be included in distribution expenses. Optimizing packaging size and material choices can lead to cost savings.
-
Fuel Costs: If you own your own fleet of vehicles, fuel costs will be a significant factor. Fuel efficiency strategies, such as route optimization and vehicle maintenance, can mitigate these expenses.
-
Insurance and Permits: Appropriate insurance coverage is essential to protect against losses or damages during transportation. Depending on your operations, you may also need various permits and licenses.
-
Handling Fees: These fees are charged by carriers or third-party logistics providers for handling and processing shipments.
-
Freight Forwarding Fees (if applicable): If you are shipping internationally, you may need to engage a freight forwarder, which will incur additional costs.
Optimizing Distribution and Warehouse Expenses: Strategic Approaches
Effectively managing distribution and warehouse expenses requires a multi-faceted approach:
1. Inventory Management Optimization
Efficient inventory management is crucial for minimizing warehousing costs. Implementing strategies such as:
-
Just-in-Time (JIT) Inventory: This method reduces inventory holding costs by receiving materials only when needed for production.
-
Demand Forecasting: Accurate demand forecasting helps optimize inventory levels and reduce the risk of stockouts or excess inventory.
-
ABC Analysis: This method categorizes inventory based on value and consumption, allowing for focused management of high-value items.
-
Inventory Tracking and Management Systems: Utilizing software to track inventory levels and movement helps identify areas for improvement and optimize storage strategies.
2. Warehouse Layout and Design
The physical layout of your warehouse significantly impacts efficiency and costs. A well-designed warehouse should:
-
Optimize workflow: Ensure smooth flow of goods from receiving to shipping.
-
Maximize space utilization: Utilize vertical space and optimize storage methods to maximize capacity.
-
Improve accessibility: Ensure easy access to frequently used items and minimize travel time for warehouse staff.
-
Implement cross-docking: This technique minimizes storage time by directly transferring goods from receiving to shipping docks.
3. Technology and Automation
Investing in technology can significantly improve efficiency and reduce costs.
-
Warehouse Management Systems (WMS): Automates many warehouse tasks, reducing labor costs and improving accuracy.
-
Automated Guided Vehicles (AGVs): Reduces manual handling and improves efficiency in large warehouses.
-
Radio Frequency Identification (RFID): Improves inventory tracking and management.
-
Robotics: Automates tasks such as picking, packing, and sorting.
4. Transportation and Logistics Optimization
Optimizing transportation and logistics can significantly reduce distribution costs:
-
Route optimization: Use software to plan efficient delivery routes, minimizing travel time and fuel consumption.
-
Carrier negotiation: Negotiate favorable rates with carriers based on volume and shipping frequency.
-
Consolidation of shipments: Combine smaller shipments into larger ones to reduce shipping costs per unit.
-
Multi-modal transportation: Explore using different modes of transportation (e.g., truck and rail) to find the most cost-effective solution.
-
Third-Party Logistics (3PL): Consider outsourcing logistics functions to a 3PL provider to leverage their expertise and infrastructure.
5. Employee Training and Motivation
Well-trained and motivated employees are essential for efficient warehouse and distribution operations.
-
Invest in training: Provide ongoing training to improve employee skills and efficiency.
-
Implement incentive programs: Reward employees for exceeding performance targets.
-
Foster a positive work environment: Create a workplace culture that values employee contributions and promotes teamwork.
6. Regular Cost Analysis and Monitoring
Continuously monitoring and analyzing distribution and warehouse expenses is critical for identifying areas for improvement.
-
Regular cost reports: Generate regular reports that track key cost metrics.
-
Benchmarking: Compare your costs to industry averages to identify areas where you can improve.
-
Cost accounting system: Implement a robust cost accounting system that tracks all aspects of distribution and warehouse costs.
The Importance of Accurate Cost Accounting
Accurate cost accounting is the cornerstone of effective expense management. A robust system should:
-
Track all expenses: Accurately track all costs associated with warehousing and distribution.
-
Allocate costs appropriately: Properly allocate costs to different products, departments, or customer segments.
-
Identify cost drivers: Determine the factors that contribute most to your costs.
-
Provide insights for decision-making: Provide data-driven insights to support informed decision-making.
By implementing these strategies and maintaining a keen focus on cost management, companies can significantly reduce their distribution and warehouse expenses, improving profitability and competitiveness. Remember that continuous improvement is key – regularly review your processes, adapt to market changes, and embrace new technologies to maintain efficiency and optimize your bottom line.
Latest Posts
Latest Posts
-
7 3 Project One Organizational Evaluation Proposal
May 25, 2025
-
To Kill A Mockingbird Part 1 Summary
May 25, 2025
-
To Kill A Mockingbird Summary Of Chapter 11
May 25, 2025
-
Sparknotes The House Of Seven Gables
May 25, 2025
-
Chapter 14 Summary Catcher In The Rye
May 25, 2025
Related Post
Thank you for visiting our website which covers about A Company's Distribution And Warehouse Expenses . We hope the information provided has been useful to you. Feel free to contact us if you have any questions or need further assistance. See you next time and don't miss to bookmark.