A Company Bought A Machine For Its Warehouse
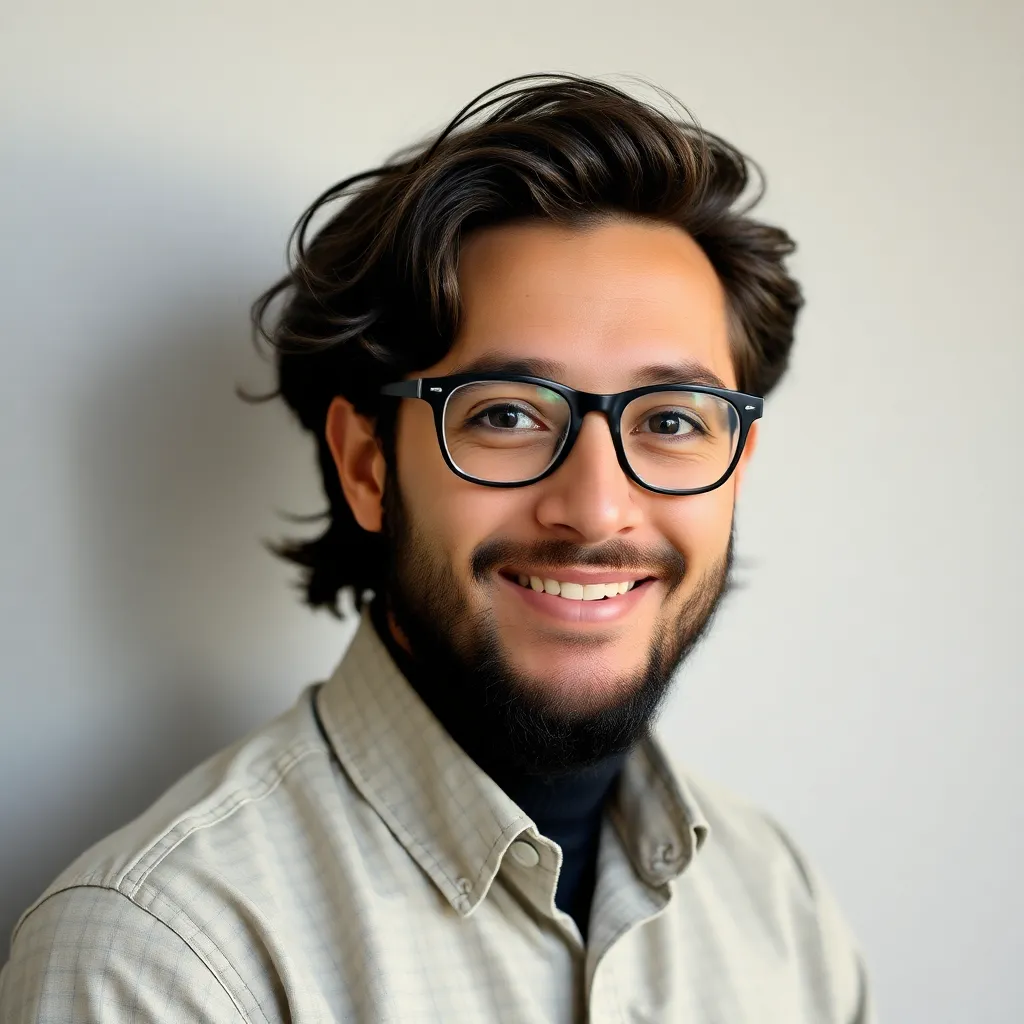
Juapaving
May 23, 2025 · 6 min read
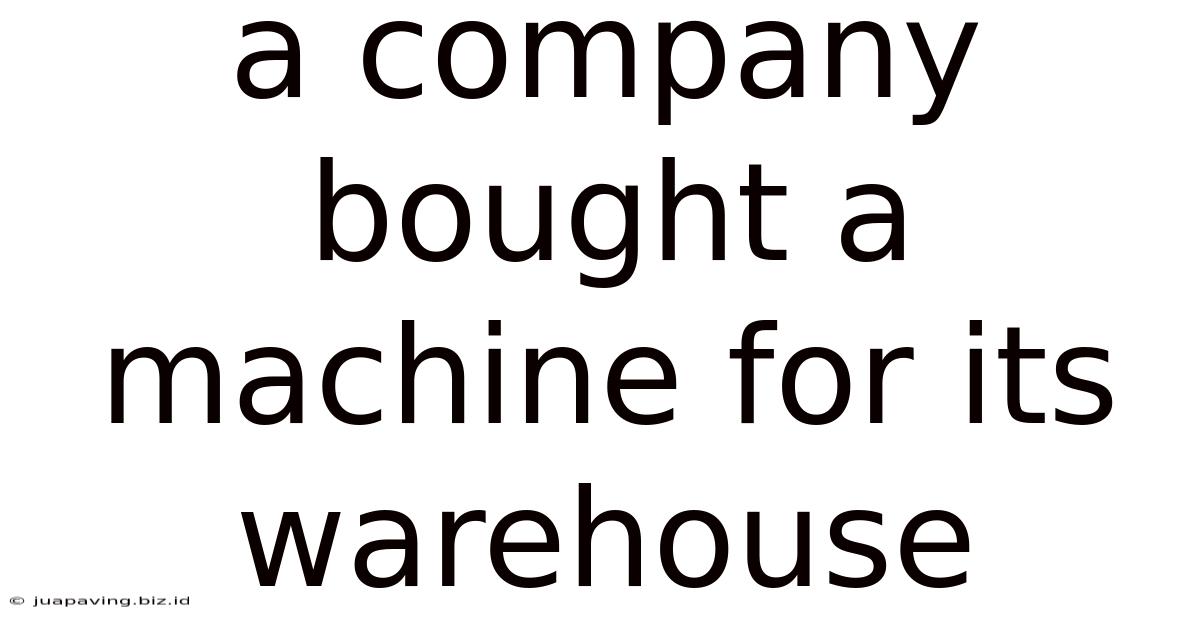
Table of Contents
Streamlining Operations: How One Company Transformed its Warehouse with a New Machine
The acquisition of new machinery is a significant event for any company, particularly for those heavily reliant on warehousing and logistics. This detailed case study explores the impact of a recent machine purchase by a fictitious company, "Acme Distribution," on its warehouse operations, highlighting the strategic decision-making process, the implementation challenges, and the overall benefits realized. We will delve into the technical specifications, operational improvements, return on investment (ROI), and the future implications of this technological upgrade.
The Need for Change: Acme Distribution's Pre-Acquisition Challenges
Before the acquisition, Acme Distribution faced several pressing challenges within its warehouse. Their existing machinery, primarily older conveyor belts and manual handling equipment, was becoming increasingly inefficient and unreliable. This resulted in:
Increased Operational Costs:
- High labor costs: Manual handling of goods was labor-intensive, requiring a large workforce to maintain throughput.
- Frequent equipment breakdowns: Older machines led to frequent downtime, causing delays in order fulfillment and increased maintenance expenses.
- High error rates: Manual processes increased the risk of human error, such as mislabeling or misplacing inventory.
Reduced Efficiency:
- Slow order processing: The inefficient workflow significantly impacted order processing times, leading to customer dissatisfaction.
- Limited storage capacity: Inefficient storage methods resulted in underutilized space and difficulties in locating inventory.
- Bottlenecks in the workflow: Various stages of the warehouse process were experiencing bottlenecks, hindering overall productivity.
Safety Concerns:
- Increased risk of workplace injuries: Manual handling tasks presented a significant risk of musculoskeletal injuries to warehouse staff.
- Lack of automation: The absence of automated safety features increased the potential for accidents.
The Solution: Selecting the Right Machine for Acme Distribution
After a thorough evaluation of its needs and a comprehensive market analysis, Acme Distribution decided to invest in a cutting-edge automated guided vehicle (AGV) system. This system comprised several key components:
Automated Guided Vehicles (AGVs):
These autonomous vehicles were designed to navigate the warehouse floor efficiently, transporting goods between different areas without human intervention. Their advanced navigation systems, utilizing laser guidance and RFID technology, ensured precise and reliable movement. The AGVs were equipped with sensors to prevent collisions and optimize their routes dynamically, avoiding congestion. Different sized AGVs were chosen to suit different warehouse tasks and load sizes, ranging from small carts ideal for individual item picking to larger platforms capable of moving entire pallets.
Warehouse Management System (WMS) Integration:
The AGV system was seamlessly integrated with Acme Distribution's existing Warehouse Management System (WMS). This integration allowed for real-time tracking of inventory, optimized routing of AGVs, and automatic task assignments. The WMS provided the AGVs with instructions on which items to pick, where to transport them, and where to deposit them, streamlining the entire process. The real-time data provided by the WMS was also invaluable in providing insights into inventory levels, helping optimize storage and order fulfillment.
Charging Infrastructure:
The AGV system included an intelligent charging infrastructure that allowed for autonomous charging of the vehicles. This meant minimal downtime and continuous operation throughout the working day. The system was designed to predict energy needs and automatically send AGVs for charging during periods of low activity, optimizing battery life and minimizing interruptions to the workflow.
Safety Features:
The AGVs were equipped with multiple safety features, including emergency stop buttons, proximity sensors, and audible alerts to ensure a safe working environment. These features significantly reduced the risk of accidents and improved workplace safety, minimizing downtime due to workplace incidents.
Implementation and Challenges: Overcoming Hurdles in the Process
Implementing the new AGV system was not without its challenges. Acme Distribution faced several hurdles:
Staff Training:
Training existing warehouse staff to operate and maintain the new system was crucial. Acme Distribution invested in comprehensive training programs, including hands-on instruction and simulations, ensuring staff proficiency and confidence. The training also focused on collaboration between human workers and the new AGV system, ensuring efficiency and preventing conflict between the two.
System Integration:
Integrating the AGV system with the existing WMS required careful planning and coordination. This process involved data migration, system testing, and adjustments to accommodate the new technology. The integration process highlighted the importance of choosing a WMS compatible with the AGV system, showcasing the value of careful pre-planning and vendor collaboration.
Initial Cost:
The initial investment in the AGV system was substantial. Acme Distribution carefully analyzed the ROI and ensured the investment aligned with the company's long-term financial goals. They carefully weighed the benefits against the initial investment cost, exploring financing options and forecasting long-term operational savings.
Space Optimization:
Implementing the AGV system required careful planning of warehouse layout to ensure efficient movement of the vehicles and avoid congestion. Acme Distribution optimized their warehouse layout to accommodate the AGV system, leading to a more efficient and organized workspace. They also re-evaluated their storage methods, optimizing their use of vertical space and improving item accessibility.
Post-Implementation Results: A Transformation in Efficiency and Productivity
The implementation of the AGV system dramatically transformed Acme Distribution's warehouse operations:
Improved Efficiency:
- Faster order processing: Order fulfillment times were significantly reduced, leading to increased customer satisfaction and quicker turnaround times.
- Increased throughput: The AGV system increased the overall throughput of the warehouse, enabling Acme Distribution to handle a larger volume of goods.
- Optimized storage: The AGV system enabled optimized storage strategies, making better use of existing warehouse space and improving inventory accessibility.
Reduced Costs:
- Lower labor costs: The automation reduced the reliance on manual labor, leading to significant cost savings on personnel.
- Reduced error rates: The automated system minimized human error, reducing the costs associated with misplaced or damaged goods.
- Lower maintenance costs: While initial investment was high, the reliable AGV system lowered the long-term costs associated with frequent repairs of older equipment.
Enhanced Safety:
- Reduced workplace injuries: The automation reduced the risk of musculoskeletal injuries associated with manual handling tasks.
- Improved safety measures: The built-in safety features of the AGV system minimized the risk of accidents.
Data-Driven Decision Making:
The integration of the AGV system with the WMS provided Acme Distribution with access to real-time data on warehouse operations. This data allowed for improved inventory management, optimized routing of AGVs, and proactive identification and mitigation of potential bottlenecks, leading to more informed decision-making.
Future Implications and Continuous Improvement
Acme Distribution plans to leverage the collected data to further optimize its warehouse operations. Future improvements might include:
- Predictive Maintenance: Utilizing data analytics to predict potential equipment failures and schedule maintenance proactively, minimizing downtime.
- Advanced Analytics: Using sophisticated data analytics to identify and resolve operational bottlenecks and inefficiencies.
- Expansion of the AGV System: As the business grows, Acme Distribution plans to expand its AGV system to accommodate increased order volumes.
- Integration with other systems: Exploring the integration of the AGV system with other enterprise systems to further streamline processes.
Conclusion: A Case Study in Successful Technological Implementation
Acme Distribution's investment in the AGV system stands as a compelling case study in the successful implementation of technology to improve warehouse operations. By carefully assessing its needs, selecting the appropriate technology, and addressing the challenges of implementation, Acme Distribution transformed its warehouse from an inefficient and costly operation into a streamlined, safe, and highly productive environment. The success of this endeavor highlights the potential for technology to drive significant improvements in efficiency, cost savings, and overall profitability within the warehousing and logistics sector. The investment in the AGV system is not just an upgrade; it’s a strategic move positioning Acme Distribution for future growth and market competitiveness. The data-driven approach ensures continuous improvement and adaptability to changing business needs, setting a new benchmark for warehouse optimization within the industry.
Latest Posts
Latest Posts
-
Characters In The Merry Wives Of Windsor
May 24, 2025
-
Chapter 3 Of Into The Wild
May 24, 2025
-
Biff And Happy Death Of A Salesman
May 24, 2025
-
Description Of Dill In To Kill A Mockingbird
May 24, 2025
-
Act 3 A Raisin In The Sun
May 24, 2025
Related Post
Thank you for visiting our website which covers about A Company Bought A Machine For Its Warehouse . We hope the information provided has been useful to you. Feel free to contact us if you have any questions or need further assistance. See you next time and don't miss to bookmark.